What is a PCB substrate?
A PCB substrate is the insulating material that forms the base of a printed circuit board. It is typically made of a dielectric material, which is a poor conductor of electricity. The substrate provides a stable platform for the copper traces and components to be mounted on, while also insulating them from each other to prevent short circuits.
The substrate also plays a role in the PCB’s thermal management, as it helps to dissipate heat generated by the components. The choice of substrate material can significantly impact the PCB’s ability to withstand high temperatures and maintain its structural integrity.
Types of PCB substrates
There are several types of PCB substrates available, each with its own unique properties and advantages. The most common types include:
FR-4
FR-4 is the most widely used PCB substrate material. It is a composite material made of woven fiberglass cloth impregnated with an epoxy resin binder. FR-4 offers good mechanical strength, electrical insulation, and thermal stability. It is suitable for a wide range of applications, from simple single-layer boards to complex multi-layer designs.
High-Tg FR-4
High-Tg FR-4 is a variant of standard FR-4 that offers improved thermal performance. It has a higher glass transition temperature (Tg), which is the point at which the material begins to soften and lose its mechanical properties. High-Tg FR-4 is ideal for applications that require higher operating temperatures or increased reliability.
Polyimide
Polyimide is a high-performance substrate material that offers excellent thermal stability, chemical resistance, and mechanical strength. It can withstand temperatures up to 260°C and is often used in aerospace, military, and medical applications. Polyimide is more expensive than FR-4 and can be more challenging to process.
PTFE
PTFE (polytetrafluoroethylene), also known as Teflon, is a substrate material with outstanding dielectric properties and low loss at high frequencies. It is often used in high-frequency applications, such as radar systems and microwave circuits. PTFE has a low dielectric constant and dissipation factor, which helps to minimize signal loss and distortion.
Ceramic
Ceramic substrates are made from materials such as alumina (Al2O3) or aluminum nitride (AlN). They offer excellent thermal conductivity, high mechanical strength, and good electrical insulation. Ceramic substrates are often used in high-power applications, such as LED lighting and power electronics.
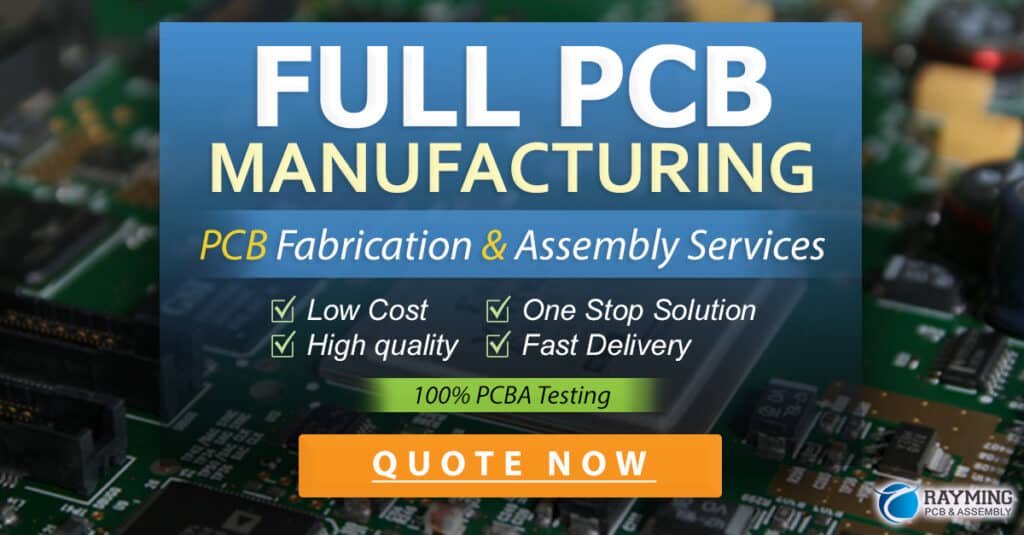
Properties of PCB substrates
When selecting a PCB substrate, several key properties must be considered to ensure the board’s performance and reliability. These properties include:
Dielectric constant (Dk)
The dielectric constant is a measure of a material’s ability to store electrical energy. A lower Dk value indicates that the material has a lower capacitance, which is desirable for high-frequency applications. FR-4 has a Dk value of around 4.5, while PTFE can have a Dk as low as 2.1.
Dissipation factor (Df)
The dissipation factor, also known as loss tangent, is a measure of a material’s ability to dissipate electrical energy as heat. A lower Df value indicates lower signal loss and better high-frequency performance. FR-4 has a Df value of around 0.02, while PTFE can have a Df as low as 0.0004.
Thermal conductivity
Thermal conductivity is a measure of a material’s ability to conduct heat. A higher thermal conductivity allows the substrate to dissipate heat more effectively, which is essential for high-power applications. FR-4 has a thermal conductivity of around 0.3 W/mK, while ceramic substrates can have values as high as 170 W/mK.
Coefficient of thermal expansion (CTE)
The coefficient of thermal expansion is a measure of how much a material expands or contracts with changes in temperature. A substrate with a CTE that closely matches that of the copper traces and components can help to reduce stress and improve reliability. FR-4 has a CTE of around 14 ppm/°C, while polyimide can have a CTE as low as 4 ppm/°C.
Mechanical strength
The mechanical strength of a substrate determines its ability to withstand physical stress and maintain its structural integrity. Factors such as flexural strength, tensile strength, and impact resistance are important considerations. FR-4 has good mechanical strength, while ceramic substrates offer even higher strength and stiffness.
Choosing the right PCB substrate
Selecting the appropriate PCB substrate involves careful consideration of the application’s requirements and constraints. Some key factors to consider include:
-
Frequency: For high-frequency applications, substrates with low Dk and Df values, such as PTFE, are preferred to minimize signal loss and distortion.
-
Temperature: Applications that involve high operating temperatures or thermal cycling require substrates with good thermal stability and high Tg values, such as high-Tg FR-4 or polyimide.
-
Power: High-power applications benefit from substrates with high thermal conductivity, such as ceramic, to efficiently dissipate heat and prevent component failure.
-
Environment: Applications exposed to harsh environments, such as chemicals or moisture, may require substrates with high chemical resistance and low moisture absorption, such as polyimide.
-
Cost: The choice of substrate material can significantly impact the overall cost of the PCB. FR-4 is the most cost-effective option for general-purpose applications, while high-performance materials like polyimide and ceramic are more expensive.
Substrate thickness and layer count
The thickness and number of layers in a PCB substrate also play a crucial role in the board’s performance and manufacturability. Thinner substrates allow for smaller vias and finer trace widths, enabling higher component density and more compact designs. However, thinner substrates are also more prone to warping and mechanical stress.
Multi-layer PCBs, which consist of multiple substrates bonded together with insulating layers in between, offer several advantages over single-layer boards. They allow for more complex routing, better signal integrity, and improved EMI/RFI shielding. The number of layers in a PCB can range from two to over 30, depending on the application’s complexity and requirements.
Advanced substrate technologies
As electronic devices continue to push the boundaries of performance and miniaturization, advanced substrate technologies have emerged to meet these challenges. Some examples include:
High-Density Interconnect (HDI)
HDI PCBs feature fine pitch traces, small vias, and buried or blind vias to achieve higher component density and improved signal integrity. HDI substrates often use materials with lower Dk and Df values, such as modified FR-4 or polyphenylene oxide (PPO), to minimize signal loss and distortion.
Embedded components
Embedded component PCBs have passive components, such as resistors and capacitors, buried within the substrate layers. This technology allows for shorter signal paths, reduced parasitic effects, and improved reliability. Embedded components can be created using materials such as ceramic, tantalum, or polymer thick film.
Flexible and rigid-flex PCBs
Flexible PCBs use thin, flexible substrates, such as polyimide or polyester, to create circuits that can bend and fold. Rigid-flex PCBs combine flexible and rigid substrates, allowing for three-dimensional designs and improved mechanical reliability. These substrates are often used in wearable electronics, medical devices, and aerospace applications.
FAQ
-
Q: What is the most common PCB substrate material?
A: FR-4 is the most widely used PCB substrate material due to its good balance of mechanical, electrical, and thermal properties, as well as its cost-effectiveness. -
Q: What are the advantages of using a ceramic PCB substrate?
A: Ceramic PCB substrates offer excellent thermal conductivity, high mechanical strength, and good electrical insulation. They are ideal for high-power applications that require efficient heat dissipation. -
Q: How does the dielectric constant of a substrate affect PCB performance?
A: A lower dielectric constant indicates that the substrate has a lower capacitance, which is desirable for high-frequency applications. Substrates with low dielectric constants help to minimize signal loss and distortion. -
Q: What is the difference between a single-layer and a multi-layer PCB?
A: A single-layer PCB has only one substrate layer, while a multi-layer PCB consists of multiple substrates bonded together with insulating layers in between. Multi-layer PCBs offer more complex routing, better signal integrity, and improved EMI/RFI shielding compared to single-layer boards. -
Q: What factors should be considered when selecting a PCB substrate for a specific application?
A: When choosing a PCB substrate, consider factors such as the application’s frequency, operating temperature, power requirements, environmental conditions, and cost constraints. These factors will help determine the most suitable substrate material and properties for the specific application.
Conclusion
The substrate is a critical component of a printed circuit board, providing the foundation for the copper traces, components, and other elements. Understanding the various types of PCB substrates, their properties, and selection criteria is essential for designing and manufacturing reliable and high-performance electronic devices.
From the widely used FR-4 to high-performance materials like polyimide and ceramic, each substrate offers unique advantages and trade-offs. By carefully considering the application’s requirements and constraints, designers can select the most appropriate substrate material and properties to ensure optimal performance, reliability, and cost-effectiveness.
As electronic devices continue to evolve and push the boundaries of performance and miniaturization, advanced substrate technologies like HDI, embedded components, and flexible/rigid-flex PCBs will play an increasingly important role in enabling the next generation of innovative products.
Substrate Material | Key Properties | Typical Applications |
---|---|---|
FR-4 | Good mechanical strength, electrical insulation, and thermal stability | General-purpose electronics, consumer devices, industrial controls |
High-Tg FR-4 | Improved thermal performance, higher glass transition temperature | Automotive electronics, aerospace, high-reliability applications |
Polyimide | Excellent thermal stability, chemical resistance, and mechanical strength | Aerospace, military, medical devices, high-temperature applications |
PTFE | Outstanding dielectric properties, low loss at high frequencies | High-frequency applications, radar systems, microwave circuits |
Ceramic | Excellent thermal conductivity, high mechanical strength, good electrical insulation | High-power applications, LED lighting, power electronics |