Understanding PCB Colors
PCBs come in a variety of colors, with each color serving a specific purpose or indicating a particular characteristic of the board. The most common PCB colors include:
- Green: The standard color for PCBs, offering good contrast for component placement and inspection.
- Red: Often used for high-frequency or RF applications due to its low dielectric constant.
- Blue: Sometimes used for high-speed digital applications or as a visual indicator for specific board types.
- Black: Provides a sleek appearance and is commonly used in consumer electronics.
- White: Offers high contrast for component placement and is often used in LED lighting applications.
- Yellow: Used in some high-frequency applications or as a visual indicator for warning or caution.
The Rise of Purple PCBs
In recent years, purple PCBs have gained popularity among electronics manufacturers and hobbyists alike. The distinctive color sets them apart from the more common green pcbs and offers several advantages.
Aesthetic Appeal
One of the primary reasons for the growing popularity of purple PCBs is their unique and eye-catching appearance. The vibrant purple color adds a touch of style and sophistication to electronic devices, making them stand out from the crowd. This aesthetic appeal is particularly important in consumer electronics, where product differentiation is crucial.
Improved Visibility
Purple PCBs offer excellent contrast against various components, making it easier for technicians to identify and place components accurately during the assembly process. This improved visibility can lead to fewer assembly errors and increased production efficiency.
Enhanced Inspection Capabilities
The purple color of the PCB can also enhance the effectiveness of automated optical inspection (AOI) systems. AOI systems use cameras and image processing algorithms to detect defects and ensure the quality of the assembled PCBs. The high contrast provided by purple PCBs can make it easier for these systems to identify issues such as solder bridges, missing components, or incorrect component placement.
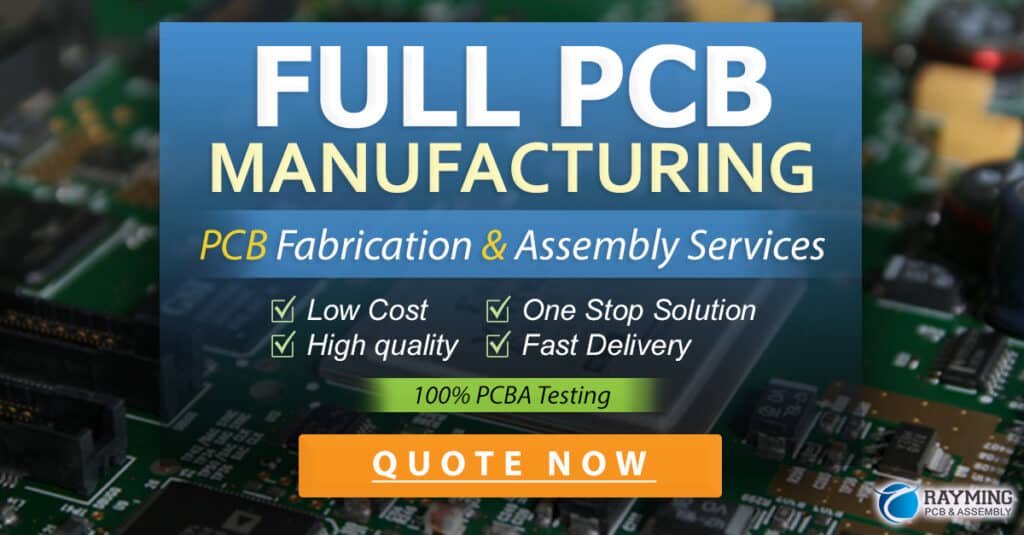
Manufacturing Process of Purple PCBs
The manufacturing process for purple PCBs is similar to that of other colored PCBs, with a few key differences in the materials and techniques used.
Substrate Material
The base material for purple PCBs is typically FR-4, a flame-retardant glass-reinforced epoxy laminate. FR-4 is the most common substrate material for PCBs due to its excellent electrical, mechanical, and thermal properties.
Copper Cladding
A thin layer of copper is laminated onto the FR-4 substrate to create the conductive pathways for the electronic components. The copper layer is typically 1 oz (35 μm) or 2 oz (70 μm) thick, depending on the specific requirements of the PCB design.
Solder Mask Application
After the copper cladding is etched to create the desired circuit pattern, a solder mask is applied to the PCB surface. The solder mask is a protective coating that insulates the copper traces and prevents short circuits. For purple PCBs, a purple-colored solder mask is used, which is typically made from a photoimageable polymer.
Silkscreen Printing
The final step in the manufacturing process is the application of silkscreen printing. This involves printing text, symbols, and component identifiers onto the PCB surface using white ink. The white silkscreen contrasts well with the purple background, making it easy to read and identify components.
Advantages of Purple PCBs
Purple PCBs offer several advantages over traditional green PCBs, making them an attractive choice for various applications.
Improved Durability
The purple solder mask used on these PCBs is typically more resistant to UV light, making them less prone to fading or discoloration over time. This improved durability is particularly important for devices that are exposed to direct sunlight or harsh environmental conditions.
Better Heat Dissipation
Some manufacturers claim that purple PCBs offer better heat dissipation compared to green PCBs. The theory is that the purple color allows for better absorption and distribution of heat, which can help prevent component overheating and extend the lifespan of the device. However, more research is needed to confirm this claim.
Reduced Eye Strain
For technicians and engineers who work with PCBs on a daily basis, the high contrast and improved visibility of purple PCBs can help reduce eye strain and fatigue. This can lead to increased productivity and fewer errors in the long run.
Applications of Purple PCBs
Purple PCBs are used in a wide range of applications, from consumer electronics to industrial control systems. Some specific examples include:
- Smartphones and tablets
- Wearable devices
- Internet of Things (IoT) devices
- Automotive electronics
- Medical devices
- Industrial control systems
- High-frequency and RF applications
Choosing the Right PCB Color
When selecting the color for your PCB, consider the following factors:
- Application requirements
- Manufacturing constraints
- Aesthetic preferences
- Cost implications
While purple PCBs offer several advantages, they may not be the best choice for every application. It’s essential to consult with your PCB manufacturer to determine the most suitable color for your specific needs.
Frequently Asked Questions (FAQ)
1. Are purple PCBs more expensive than green PCBs?
In general, purple PCBs may be slightly more expensive than green PCBs due to the specialized solder mask and the lower volume of production compared to the more common green PCBs. However, the price difference is usually minimal and can be offset by the benefits of using purple PCBs.
2. Can purple PCBs be used for high-frequency applications?
Yes, purple PCBs can be used for high-frequency applications. The color of the PCB does not directly affect its electrical properties. However, it’s essential to choose a substrate material and copper thickness that is suitable for the specific frequency range and signal integrity requirements of your application.
3. Are there any disadvantages to using purple PCBs?
One potential disadvantage of using purple PCBs is the limited availability compared to green PCBs. Not all PCB manufacturers offer purple as a standard color option, which may lead to longer lead times or higher minimum order quantities. Additionally, some people may find the purple color less aesthetically pleasing than the traditional green.
4. Can purple PCBs be used in military or aerospace applications?
Yes, purple PCBs can be used in military and aerospace applications as long as they meet the required specifications and standards for those industries. These applications often have strict requirements for durability, reliability, and performance, so it’s essential to work with a PCB manufacturer that has experience in these sectors.
5. How can I ensure the quality of my purple PCBs?
To ensure the quality of your purple PCBs, work with a reputable PCB manufacturer that has experience in producing high-quality boards. Look for certifications such as ISO 9001, UL, or IPC to verify the manufacturer’s commitment to quality standards. Additionally, consider using automated optical inspection (AOI) and other quality control measures to detect and correct any defects in the manufacturing process.
Conclusion
Purple PCBs are a growing trend in the electronics industry, offering several advantages over traditional green PCBs. With their unique aesthetic appeal, improved visibility, and enhanced durability, purple PCBs are finding applications in a wide range of sectors, from consumer electronics to industrial control systems.
When considering purple PCBs for your next project, it’s essential to weigh the benefits against any potential drawbacks, such as limited availability or higher costs. By working with an experienced PCB manufacturer and carefully considering your specific application requirements, you can leverage the advantages of purple PCBs to create high-quality, visually appealing electronic devices.
As the electronics industry continues to evolve, it’s likely that we will see more innovations in PCB colors and materials. By staying up-to-date with these trends and understanding the characteristics of different PCB colors, you can make informed decisions and create products that stand out in an increasingly competitive market.
PCB Color | Typical Applications | Advantages | Disadvantages |
---|---|---|---|
Green | General-purpose, standard applications | Wide availability, lower cost | Limited visual appeal |
Red | High-frequency, RF applications | Low dielectric constant, improved signal integrity | Higher cost, limited availability |
Blue | High-speed digital, specific board types | Visual differentiation, improved contrast | Limited availability, higher cost |
Black | Consumer electronics, aesthetics | Sleek appearance, high visual appeal | Reduced visibility for component placement |
White | LED lighting, high-contrast applications | Excellent contrast for component placement | Potential for discoloration over time |
Yellow | High-frequency, warning indicators | Visual indication for specific applications | Limited availability, potential for color fading |
Purple | Consumer electronics, improved durability | Unique aesthetic appeal, improved visibility and durability | Slightly higher cost, limited availability |