The Importance of PCB Engineering
PCB engineering is essential for several reasons:
-
Functionality: A well-designed PCB ensures that the electronic components are connected correctly and can perform their intended functions.
-
Reliability: Proper PCB design and manufacturing techniques help create robust and reliable electronic devices that can withstand various environmental factors and operate for an extended period.
-
Performance: Optimized PCB layouts and material choices contribute to better signal integrity, reduced electromagnetic interference (EMI), and improved overall system performance.
-
Cost-effectiveness: Efficient PCB design and manufacturing processes help minimize production costs while maintaining high quality standards.
The PCB Engineering Process
The PCB engineering process typically involves the following stages:
1. Schematic Design
The first step in PCB engineering is creating a schematic diagram that represents the electrical connections between various components. This diagram serves as a blueprint for the PCB layout and helps engineers understand the circuit’s functionality.
2. Component Selection
Engineers select the appropriate electronic components based on the circuit’s requirements, such as power consumption, operating frequency, and environmental factors. They also consider factors like package size, cost, and availability.
3. PCB Layout
Once the schematic is finalized and components are selected, engineers proceed with the PCB layout. This involves arranging the components on the board and routing the electrical connections between them. The layout process considers various factors, such as:
- Signal integrity
- Power distribution
- Thermal management
- EMI reduction
- Manufacturing constraints
4. Design Rule Check (DRC) and Verification
After completing the PCB layout, engineers perform a Design Rule Check (DRC) to ensure that the design adheres to the manufacturing guidelines and constraints. They also verify the design using simulation tools to check for signal integrity issues, power distribution problems, and potential EMI concerns.
5. Prototyping and Testing
Once the PCB design is verified, a prototype is manufactured for testing and validation. Engineers perform various tests to ensure that the PCB functions as intended and meets the required specifications. This stage may involve several iterations of design modifications and re-testing until the desired performance is achieved.
6. Manufacturing and Assembly
After the prototype is validated, the PCB design is sent for mass production. The manufacturing process involves the following steps:
- PCB fabrication: The PCB is manufactured using a combination of chemical etching, drilling, and plating processes.
- PCB assembly: Electronic components are soldered onto the PCB using either through-hole or surface-mount technology (SMT).
- Quality control: The assembled PCBs undergo various inspections and tests to ensure they meet the required quality standards.
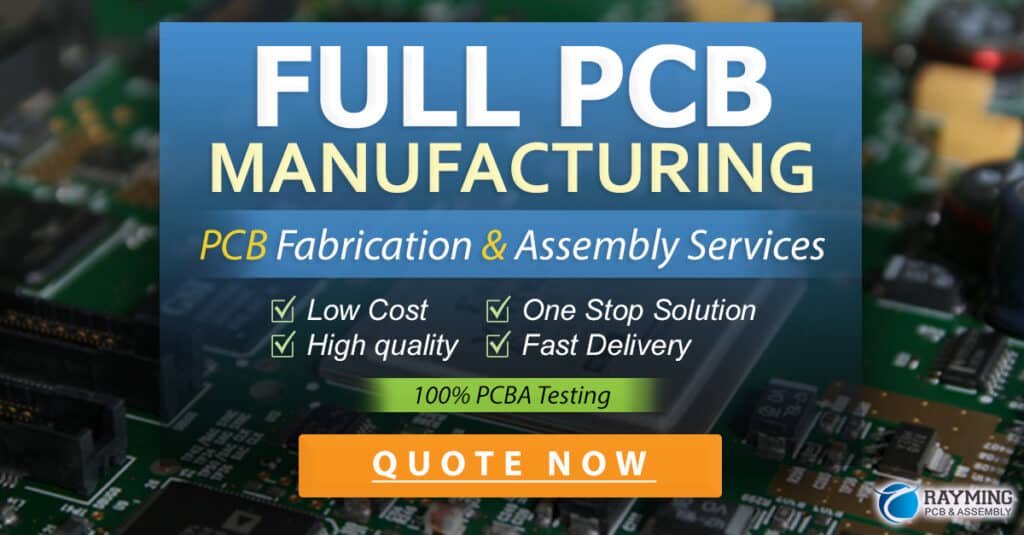
PCB Design Considerations
To create a successful PCB design, engineers must consider several key factors:
1. Material Selection
The choice of PCB material depends on the application’s requirements, such as operating temperature, frequency, and environmental conditions. Common PCB materials include:
- FR-4: A widely used, cost-effective material suitable for most general-purpose applications.
- High-frequency laminates: Materials like Rogers or Isola are used for high-frequency applications, such as RF and microwave circuits.
- Metal core PCBs: Used for applications that require efficient heat dissipation, such as high-power LED lighting or power electronics.
2. Layer Stack-up
The number of layers and their arrangement in a PCB, known as the layer stack-up, plays a crucial role in signal integrity, power distribution, and EMI performance. Engineers must carefully design the layer stack-up based on the circuit’s requirements and the chosen manufacturing process.
3. Signal Integrity
Maintaining signal integrity is essential for ensuring reliable communication between components on a PCB. Engineers must consider factors such as trace width, spacing, impedance matching, and termination to minimize signal distortion, crosstalk, and reflections.
4. Power Distribution
Proper power distribution is critical for maintaining stable voltage levels and minimizing noise in a PCB. Engineers must design appropriate power planes, decoupling capacitors, and voltage regulators to ensure clean and stable power supply to all components.
5. Thermal Management
Managing heat dissipation is crucial for maintaining the reliability and performance of electronic components. Engineers must consider factors such as component placement, copper pour, and thermal vias to effectively transfer heat away from components and prevent overheating.
6. EMI Reduction
Electromagnetic interference (EMI) can cause undesired signal distortion and affect the performance of nearby electronic devices. To reduce EMI, engineers employ various techniques, such as proper grounding, shielding, filtering, and strategic component placement.
Advanced PCB Technologies
As electronic devices become more complex and demanding, PCB engineering has evolved to incorporate advanced technologies and techniques:
1. High-Density Interconnect (HDI)
HDI PCBs feature finer trace widths, smaller vias, and higher component density compared to traditional PCBs. This technology enables the design of compact, high-performance electronic devices, such as smartphones and wearables.
2. Flexible and Rigid-Flex PCBs
Flexible PCBs are made from thin, flexible materials that allow the board to bend and conform to various shapes. Rigid-flex PCBs combine both rigid and flexible sections, offering the benefits of both technologies in a single board. These PCBs are ideal for applications that require compact packaging or movable parts.
3. Embedded Components
Embedded component technology involves placing passive components, such as resistors and capacitors, inside the PCB substrate. This technique saves space on the board surface, reduces parasitic effects, and improves overall system performance.
4. 3D PCBs
3D PCBs, also known as multi-board modules, consist of multiple PCBs stacked and interconnected vertically. This technology enables the creation of highly compact and complex electronic systems, such as system-in-package (SiP) solutions.
PCB Manufacturing Processes
There are two primary PCB manufacturing processes:
1. Through-hole Technology (THT)
THT involves drilling holes in the PCB and inserting component leads through the holes, which are then soldered on the opposite side of the board. THT is suitable for larger components and applications that require higher mechanical strength.
2. Surface-Mount Technology (SMT)
SMT involves placing components directly on the surface of the PCB and soldering them using a reflow or wave soldering process. SMT allows for higher component density, smaller board sizes, and faster assembly compared to THT.
The Future of PCB Engineering
As technology continues to advance, PCB engineering will face new challenges and opportunities:
1. Miniaturization
The demand for smaller, more compact electronic devices will drive the need for even higher-density PCBs and advanced packaging techniques.
2. High-Speed and High-Frequency Applications
As data rates and operating frequencies increase, PCB engineers will need to develop new strategies for managing signal integrity, power integrity, and EMI in high-speed and high-frequency applications.
3. Sustainable and Eco-Friendly Practices
There will be a growing emphasis on sustainable PCB materials and manufacturing processes to reduce the environmental impact of electronic waste and comply with evolving regulations.
4. Integration with Additive Manufacturing
The integration of additive manufacturing techniques, such as 3D printing, with PCB fabrication processes will enable the creation of novel PCB structures and more efficient prototyping.
Frequently Asked Questions (FAQ)
-
What is the difference between a schematic and a PCB layout?
A schematic is a diagram that represents the electrical connections between components, while a PCB layout is the physical arrangement of those components and their interconnections on a printed circuit board. -
What is the purpose of a Design Rule Check (DRC)?
A Design Rule Check (DRC) is performed to ensure that a PCB design adheres to the manufacturing guidelines and constraints, such as minimum trace widths, clearances, and hole sizes. It helps identify and resolve potential issues before the PCB is sent for manufacturing. -
What is the difference between through-hole and surface-mount technology?
Through-hole technology (THT) involves inserting component leads through drilled holes in the PCB and soldering them on the opposite side. Surface-mount technology (SMT) involves placing components directly on the surface of the PCB and soldering them using a reflow or wave soldering process. SMT allows for higher component density and smaller board sizes compared to THT. -
What is signal integrity, and why is it important in PCB design?
Signal integrity refers to the ability of a PCB to maintain the quality and accuracy of electrical signals as they travel through the board. It is important because poor signal integrity can lead to signal distortion, crosstalk, and reflections, which can negatively affect the performance and reliability of the electronic device. -
What are the benefits of using flexible or rigid-flex PCBs?
Flexible PCBs offer several benefits, such as the ability to conform to various shapes, reduced weight, and improved resistance to vibration and shock. Rigid-flex PCBs combine the benefits of both rigid and flexible sections, allowing for more complex designs and improved reliability in applications that require movement or compact packaging.
PCB Manufacturing Process | Characteristics | Suitable Applications |
---|---|---|
Through-hole Technology (THT) | – Components inserted through drilled holes – Soldered on the opposite side of the board – Suitable for larger components and higher mechanical strength |
– High-power electronics – Aerospace and defense systems – Industrial control systems |
Surface-Mount Technology (SMT) | – Components placed directly on the PCB surface – Soldered using reflow or wave soldering process – Higher component density and smaller board sizes compared to THT |
– Consumer electronics – Smartphones and wearables – Medical devices |
In conclusion, PCB engineering is a critical aspect of modern electronics design and manufacturing. It involves the design, layout, and production of printed circuit boards that form the backbone of nearly all electronic devices we use today. By considering key factors such as material selection, layer stack-up, signal integrity, power distribution, thermal management, and EMI reduction, PCB engineers create functional, reliable, and high-performance electronic systems. As technology advances, PCB engineering will continue to evolve, incorporating new technologies and techniques to meet the ever-increasing demands of the electronics industry.