Key Features of HDI PCBs
HDI PCBs have several distinct features that set them apart from traditional PCBs:
- Smaller vias and pads
- Finer trace widths and spacings
- Multiple layers (typically 8 or more)
- Blind and buried vias
- Microvias (vias with a diameter less than 150 microns)
These features enable HDI PCBs to pack more functionality into a smaller space, making them essential for modern electronic devices.
Advantages of HDI PCBs
HDI PCBs offer several advantages over traditional PCBs:
- Reduced size and weight: The higher wiring density allows for smaller PCB sizes, which translates to smaller and lighter end products.
- Improved signal integrity: Shorter traces and smaller vias reduce signal loss and distortion, leading to better signal integrity.
- Increased reliability: The use of blind and buried vias reduces the number of through-holes, which minimizes the risk of defects and improves reliability.
- Enhanced thermal management: The compact design of HDI PCBs allows for better heat dissipation, which is crucial for high-performance electronic devices.
- Lower power consumption: Shorter traces and smaller components lead to lower power consumption, extending battery life in portable devices.
HDI PCB Manufacturing Process
The manufacturing process for HDI PCBs is more complex than that of traditional PCBs due to the smaller features and higher precision required. The process typically involves the following steps:
- Design and layout: The PCB design is created using computer-aided design (CAD) software, taking into account the specific requirements of HDI PCBs.
- Material selection: High-quality, high-performance materials are chosen for the PCB substrate, copper foil, and solder mask.
- Drilling: Microvias and blind vias are drilled using laser or mechanical drilling techniques.
- Plating: The vias are plated with copper to establish electrical connections between layers.
- Patterning: The copper layers are patterned using photolithography and etching processes to create the desired traces and pads.
- Lamination: The pcb layers are laminated together under high pressure and temperature.
- Surface finishing: The PCB surface is finished with a protective coating, such as ENIG (Electroless Nickel Immersion Gold) or HASL (Hot Air Solder Leveling).
- Electrical testing: The completed PCB undergoes rigorous electrical testing to ensure functionality and reliability.
HDI PCB Design Considerations
When designing an HDI PCB, several factors must be considered to ensure optimal performance and manufacturability:
- Via types and sizes: Careful selection of via types (through, blind, or buried) and sizes is crucial for achieving the desired wiring density and signal integrity.
- Trace width and spacing: Trace widths and spacings must be optimized to balance wiring density, signal integrity, and manufacturability.
- Layer stackup: The number and arrangement of layers in the pcb stackup must be carefully planned to accommodate the required interconnections and minimize signal interference.
- Impedance control: Proper impedance control is essential for maintaining signal integrity, especially in high-speed applications.
- Thermal management: Adequate thermal management strategies, such as the use of thermal vias and heat sinks, must be incorporated to prevent overheating and ensure reliable operation.
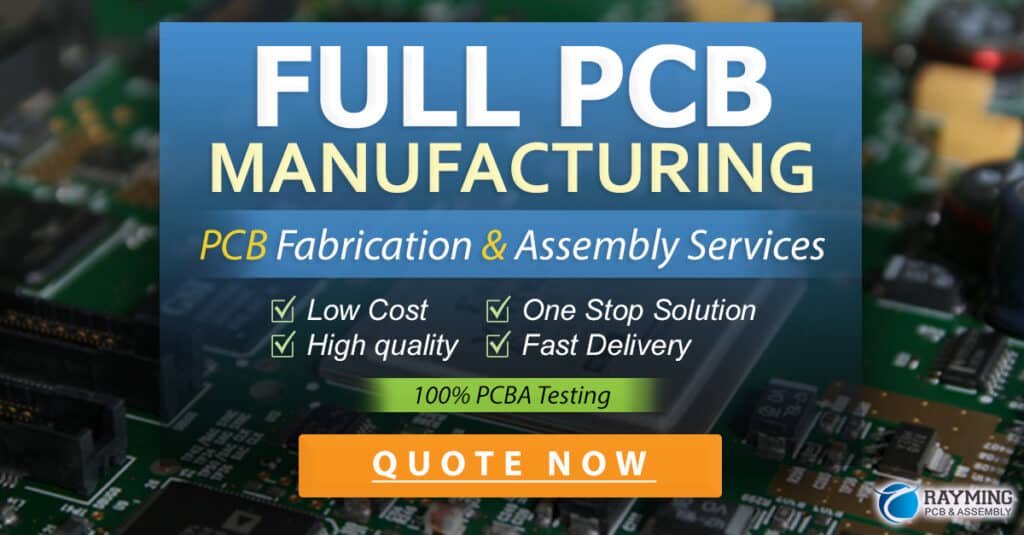
HDI PCB Applications
HDI PCBs find applications in a wide range of industries and products, including:
- Consumer electronics: Smartphones, tablets, laptops, smartwatches, and other portable devices heavily rely on HDI PCBs for their compact size and high performance.
- Automotive electronics: Advanced driver assistance systems (ADAS), infotainment systems, and other automotive electronics use HDI PCBs for their reliability and space-saving properties.
- Medical devices: Implantable devices, wearable health monitors, and other medical electronics benefit from the miniaturization and reliability offered by HDI PCBs.
- Aerospace and defense: Avionics, satellite systems, and military equipment employ HDI PCBs for their high performance, reliability, and resistance to harsh environments.
- Industrial automation: Sensors, controllers, and other industrial electronics use HDI PCBs for their compact size and robustness.
HDI PCB Market and Future Trends
The global HDI PCB market is expected to grow significantly in the coming years, driven by the increasing demand for compact and high-performance electronic devices. According to a report by Grand View Research, the global HDI PCB market size was valued at USD 10.69 billion in 2020 and is expected to expand at a compound annual growth rate (CAGR) of 11.2% from 2021 to 2028.
Several trends are shaping the future of HDI PCBs:
- Miniaturization: As electronic devices continue to shrink in size, the demand for even smaller and denser HDI PCBs will increase.
- 5G and IoT: The proliferation of 5G networks and the Internet of Things (IoT) will drive the need for HDI PCBs in connected devices and infrastructure.
- Advanced materials: The development of new, high-performance materials, such as low-loss dielectrics and ultra-low-profile copper foils, will enable even higher wiring densities and better signal integrity.
- Embedded components: The integration of passive components, such as resistors and capacitors, directly into the PCB substrate will further enhance miniaturization and performance.
- Sustainable manufacturing: The increasing focus on environmental sustainability will drive the adoption of eco-friendly materials and manufacturing processes in HDI pcb production.
Frequently Asked Questions (FAQ)
-
What is the difference between HDI PCBs and traditional PCBs?
HDI PCBs have a higher wiring density per unit area compared to traditional PCBs. They feature smaller vias, finer trace widths and spacings, and often incorporate blind and buried vias, enabling denser component placement and improved performance. -
What are the benefits of using HDI PCBs?
HDI PCBs offer several benefits, including reduced size and weight, improved signal integrity, increased reliability, enhanced thermal management, and lower power consumption. These advantages make HDI PCBs ideal for compact, high-performance electronic devices. -
What industries commonly use HDI PCBs?
HDI PCBs are used in a wide range of industries, including consumer electronics, automotive electronics, medical devices, aerospace and defense, and industrial automation. They are particularly prevalent in applications that require miniaturization, high performance, and reliability. -
How do HDI PCBs handle thermal management?
HDI PCBs employ various thermal management strategies, such as the use of thermal vias and heat sinks, to dissipate heat effectively. The compact design of HDI PCBs also allows for better heat distribution, reducing the risk of hotspots and ensuring reliable operation. -
What is the future outlook for the HDI PCB market?
The global HDI PCB market is expected to grow significantly in the coming years, driven by the increasing demand for compact and high-performance electronic devices. Trends such as miniaturization, 5G and IoT adoption, advanced materials, embedded components, and sustainable manufacturing are expected to shape the future of HDI PCBs.
In conclusion, HDI PCBs are a critical component in modern electronic devices, enabling miniaturization, high performance, and reliability. As the demand for smaller and more powerful devices continues to grow, the importance of HDI PCBs in the electronics industry will only increase. By understanding the key features, manufacturing processes, design considerations, and applications of HDI PCBs, engineers and manufacturers can create innovative products that meet the evolving needs of consumers and businesses alike.