Overview of the PCB industry in the USA
The printed circuit board industry in the United States has evolved significantly over the past few decades. While some manufacturing has shifted overseas, particularly to Asia, the US still has a robust PCB manufacturing sector. US-based PCB manufacturers are known for their advanced capabilities, strict quality standards, and ability to handle complex, high-reliability applications.
Market size and trends
According to a report by Grand View Research, the global PCB market size was valued at USD 60.2 billion in 2020 and is expected to grow at a compound annual growth rate (CAGR) of 4.3% from 2021 to 2028. The North American PCB market, which includes the United States, is a significant contributor to this growth.
The US PCB industry has seen a shift towards more advanced technologies, such as high-density interconnect (HDI) PCBs, flexible and rigid-flex PCBs, and specialized substrates. There is also a growing demand for quick-turn prototyping services and low-volume, high-mix production.
Advantages of US-based PCB manufacturing
There are several reasons why companies choose to work with US-based PCB manufacturers:
-
Quality: US pcb fabricators are known for their strict quality standards and adherence to industry certifications such as ISO 9001, ITAR, and AS9100.
-
Technology: Many US PCB manufacturers have invested in advanced manufacturing equipment and processes, enabling them to produce complex, high-performance boards.
-
Proximity: For companies based in the United States, working with a domestic PCB manufacturer can simplify logistics, reduce shipping times, and facilitate communication.
-
Intellectual property protection: US-based manufacturers are subject to strict intellectual property laws, providing peace of mind for companies with sensitive designs.
Top PCB manufacturers in the USA
There are numerous PCB manufacturers located throughout the United States, each with its own specialties and capabilities. Here are some of the top PCB manufacturers in the USA:
1. TTM Technologies
TTM Technologies is one of the largest PCB manufacturers in the United States, with facilities located across the country. They offer a wide range of PCB technologies, including HDI, flexible, and rigid-flex PCBs, as well as advanced packaging solutions.
2. Summit Interconnect
Summit Interconnect is a leading provider of advanced technology PCBs, with a focus on aerospace, defense, and medical applications. They have multiple facilities in California and Illinois, offering HDI, rigid-flex, and rf pcbs, among other specialties.
3. Printed Circuits
Printed Circuits is a Minnesota-based PCB manufacturer with over 40 years of experience. They specialize in quick-turn prototyping and low-volume production, with capabilities including HDI, flexible, and rigid-flex PCBs.
4. Royal Circuit Solutions
Royal Circuit Solutions is a California-based PCB manufacturer offering a range of services, from prototyping to volume production. They have expertise in HDI, flexible, and rigid-flex PCBs, as well as advanced materials and finishes.
5. Imagineering
Imagineering is a PCB manufacturer located in Illinois, with a focus on quick-turn prototyping and low-volume production. They offer a variety of PCB technologies, including HDI, flexible, and metal-backed PCBs.
Manufacturer | Location(s) | Specialties |
---|---|---|
TTM Technologies | Multiple US locations | HDI, flexible, rigid-flex, advanced packaging |
Summit Interconnect | California, Illinois | HDI, rigid-flex, RF PCBs, aerospace, defense, medical |
Printed Circuits | Minnesota | Quick-turn prototyping, low-volume production, HDI, flexible, rigid-flex |
Royal Circuit Solutions | California | HDI, flexible, rigid-flex, advanced materials and finishes |
Imagineering | Illinois | Quick-turn prototyping, low-volume production, HDI, flexible, metal-backed PCBs |
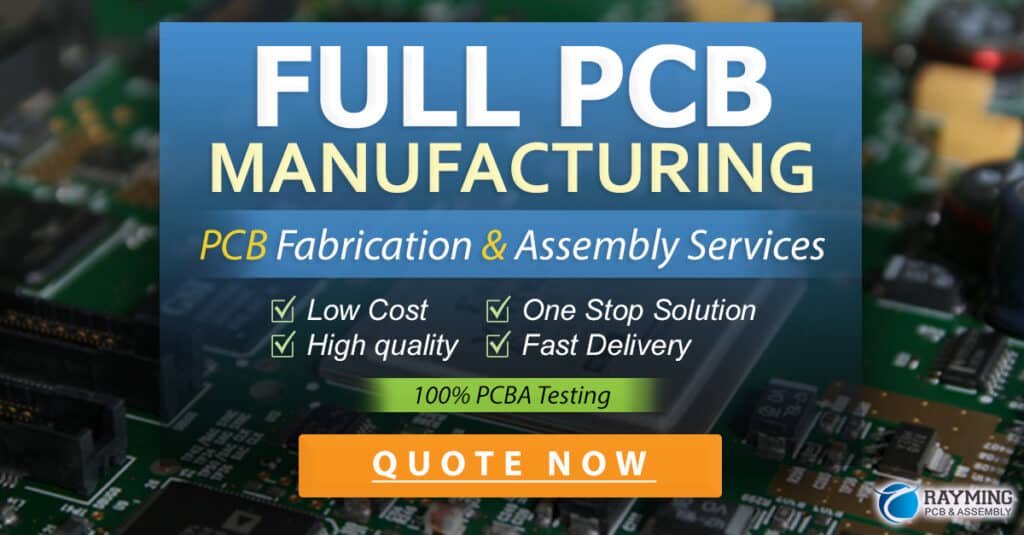
Choosing a US-based PCB manufacturer
When selecting a PCB manufacturer in the United States, there are several factors to consider:
1. Technical capabilities
Ensure that the manufacturer has experience with the specific PCB technologies and materials required for your project. Consider factors such as layer count, line width and spacing, hole size, and surface finishes.
2. Quality certifications
Look for manufacturers with relevant quality certifications, such as ISO 9001, AS9100, or ITAR registration, depending on your industry and application.
3. Lead times and pricing
Compare lead times and pricing among different manufacturers, keeping in mind that the lowest price may not always be the best value. Consider the manufacturer’s reputation for on-time delivery and their ability to accommodate your specific needs.
4. Customer support and communication
Choose a manufacturer that is responsive and easy to communicate with. Good customer support can make a significant difference in the success of your project, particularly for complex or time-sensitive orders.
PCB manufacturing process
The PCB manufacturing process typically involves several key steps:
1. Design and layout
The PCB design is created using specialized software, such as Altium Designer or Eagle. The layout includes the placement of components, routing of traces, and the creation of solder mask and silkscreen layers.
2. Fabrication
The PCB fabrication process begins with the creation of a copper-clad laminate, which is then etched to create the desired circuit pattern. Multiple layers are aligned and bonded together, and holes are drilled for through-hole components.
3. Solder mask and silkscreen application
A solder mask is applied to protect the copper traces from oxidation and prevent solder bridges. A silkscreen layer is then added to provide labels and other identifying marks on the PCB.
4. Surface finish
The exposed copper is coated with a surface finish, such as HASL (hot air solder leveling), ENIG (electroless nickel immersion gold), or OSP (organic solderability preservative), to enhance solderability and protect the copper from oxidation.
5. Electrical testing
The completed PCB undergoes electrical testing to ensure that all connections are correct and that there are no short circuits or open connections.
Benefits of US-based PCB manufacturing
Working with a US-based PCB manufacturer offers several advantages, including:
1. Faster turnaround times
By eliminating the need for international shipping, US-based manufacturers can often provide faster turnaround times, particularly for quick-turn prototypes and low-volume orders.
2. Improved communication
Collaborating with a domestic manufacturer can simplify communication, as there are no language barriers or significant time zone differences to contend with.
3. Enhanced quality control
US PCB manufacturers are subject to strict quality standards and regulations, providing a higher level of quality assurance for critical applications.
4. Support for the domestic economy
Choosing a US-based manufacturer supports the domestic economy and helps maintain a strong PCB manufacturing industry within the country.
Future of PCB manufacturing in the USA
The US PCB industry is poised for continued growth and innovation in the coming years. Some key trends and developments to watch include:
1. Advancement of 5G technology
The rollout of 5G networks is driving demand for high-frequency, low-loss PCBs, presenting new opportunities for US manufacturers with advanced capabilities.
2. Expansion of aerospace and defense applications
The aerospace and defense sectors are significant consumers of high-reliability PCBs, and US manufacturers are well-positioned to serve these industries due to their strict quality standards and ITAR compliance.
3. Growth of IoT and wearables
The proliferation of Internet of Things (IoT) devices and wearable technology is creating demand for smaller, more complex PCBs, including flexible and rigid-flex designs.
4. Reshoring initiatives
Geopolitical factors and supply chain disruptions have led some companies to consider reshoring their PCB manufacturing to the United States, presenting new opportunities for domestic fabricators.
Frequently Asked Questions (FAQ)
1. Are PCBs made in the USA more expensive than those made overseas?
While PCBs manufactured in the USA may sometimes have a higher initial cost compared to those made in countries with lower labor costs, the total cost of ownership can be lower when considering factors such as shipping, tariffs, and potential quality issues.
2. What certifications should I look for when choosing a US PCB manufacturer?
The certifications you should look for depend on your specific industry and application. Some common certifications include ISO 9001 for quality management, AS9100 for aerospace applications, and ITAR registration for defense-related projects.
3. Can US PCB manufacturers handle high-volume orders?
Yes, many US PCB manufacturers have the capacity to handle high-volume orders. However, it’s important to discuss your specific volume requirements with potential manufacturers to ensure they can meet your needs.
4. How long does it typically take to receive a prototype PCB from a US manufacturer?
Lead times for prototype PCBs can vary depending on the manufacturer and the complexity of the design. Many US manufacturers offer quick-turn prototyping services, with lead times ranging from 24 hours to several days.
5. What should I provide to a PCB manufacturer when requesting a quote?
When requesting a quote from a PCB manufacturer, you should provide as much detail as possible about your project, including the PCB design files (Gerber files), material specifications, quantities needed, and any special requirements or certifications. The more information you can provide upfront, the more accurate the quote will be.
In conclusion, the United States has a robust and innovative PCB manufacturing industry, with numerous manufacturers offering a wide range of capabilities and specialties. By working with a US-based PCB manufacturer, companies can benefit from advanced technology, strict quality standards, faster turnaround times, and improved communication. As the demand for complex, high-reliability PCBs continues to grow across various industries, the US PCB manufacturing sector is well-positioned to meet these challenges and drive the future of electronic device production.