What is a PCB manufacturer?
A PCB manufacturer is a company that specializes in the production of printed circuit boards. These manufacturers take electronic designs and translate them into physical boards, which are then populated with components and integrated into various electronic devices. PCB manufacturers play a critical role in the electronics industry, as they provide the foundation upon which modern technology is built.
PCB manufacturers offer a range of services, including:
- PCB design and layout
- Prototype fabrication
- High-volume production
- Assembly and testing
- Quality control and inspection
Types of PCB manufacturers
There are several types of PCB manufacturers, each catering to different market segments and offering specialized services:
Type | Description |
---|---|
Bare board manufacturers | These companies focus on producing unpopulated PCBs, which are then sold to electronics assembly companies or OEMs for component placement and final assembly. |
turnkey pcb assembly providers | Turnkey manufacturers offer a complete range of services, from pcb fabrication to component sourcing, assembly, and testing. This one-stop-shop approach is ideal for companies that want to streamline their supply chain and reduce time-to-market. |
High-mix, low-volume (HMLV) manufacturers | HMLV manufacturers specialize in producing a wide variety of PCBs in small quantities, often for prototyping, testing, or niche applications. These manufacturers are known for their flexibility and quick turnaround times. |
High-volume manufacturers | High-volume PCB manufacturers focus on producing large quantities of boards for mass-market applications, such as consumer electronics. These companies often have highly automated production lines and can offer competitive pricing due to economies of scale. |
The PCB manufacturing process
The PCB manufacturing process involves several key steps, each of which is critical to ensuring the quality and reliability of the final product.
1. PCB design and layout
The first step in PCB manufacturing is the creation of the electronic design and layout. This involves using specialized software to create a schematic diagram of the circuit and then translating that diagram into a physical layout that specifies the location of components, traces, and vias on the board.
2. PCB fabrication
Once the design is finalized, the PCB fabrication process begins. This involves several sub-steps:
- Substrate preparation: The base material, typically a laminate such as FR-4, is cut to size and cleaned.
- Copper cladding: A thin layer of copper is bonded to the substrate using heat and pressure.
- Patterning: The copper layer is selectively removed to create the desired circuit pattern, using a process called etching.
- Drilling: Holes are drilled through the board to accommodate through-hole components and vias.
- Plating: The holes are plated with copper to create electrical connections between layers.
- Solder mask application: A protective layer of solder mask is applied to the board, leaving only the exposed pads and contacts.
- Silkscreen printing: Text and symbols are printed on the board for component identification and assembly guidance.
3. PCB assembly
After the bare board is fabricated, it is ready for component assembly. This process can be done manually for low-volume or prototype boards, but high-volume production typically relies on automated assembly lines.
The assembly process involves several steps:
- Solder paste application: A thin layer of solder paste is applied to the pads on the board using a stencil or screen printing process.
- Component placement: Surface mount components are placed on the board using pick-and-place machines, while through-hole components are inserted manually or with automated insertion equipment.
- Reflow soldering: The board is heated in a reflow oven, causing the solder paste to melt and form electrical connections between the components and the board.
- Inspection and testing: The assembled board is inspected visually and tested electrically to ensure proper functionality and adherence to specifications.
4. Quality control and testing
Throughout the manufacturing process, PCB manufacturers employ strict quality control measures to ensure the consistency and reliability of their products. This includes:
- Incoming material inspection: Raw materials and components are inspected to ensure they meet specifications and are free from defects.
- In-process inspection: Boards are inspected at various stages of production to identify and correct any issues before they propagate further down the line.
- Final inspection and testing: Completed boards are subject to a thorough visual inspection and electrical testing to verify functionality and conformance to customer requirements.
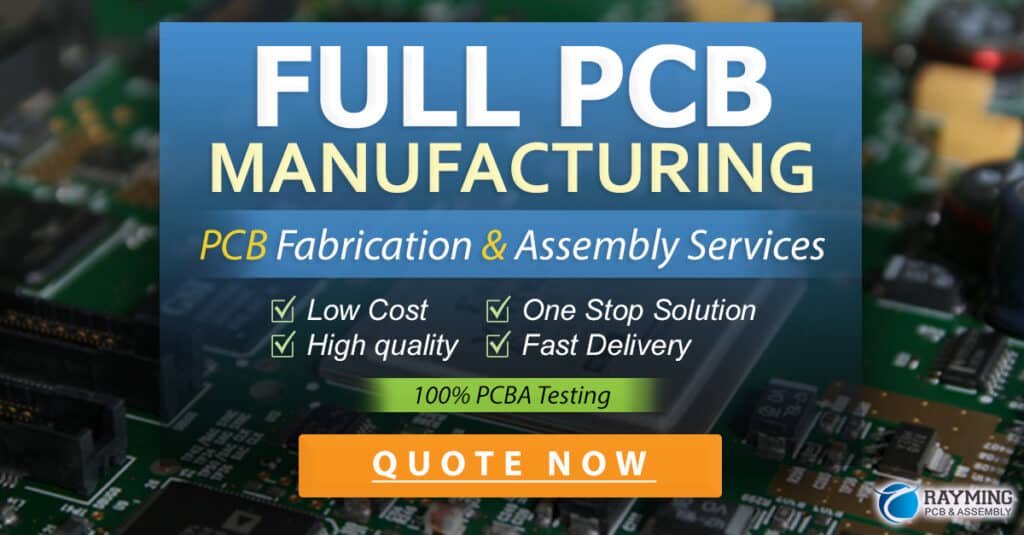
Key players in the PCB manufacturing industry
The PCB manufacturing industry is highly competitive and globalized, with players ranging from small, specialized shops to large, multinational corporations. Some of the key players in the industry include:
Company | Headquarters | Description |
---|---|---|
Jabil | USA | A global manufacturing services company that offers PCB design, fabrication, and assembly services for a wide range of industries. |
Foxconn | Taiwan | The world’s largest contract electronics manufacturer, with a significant presence in the PCB market. |
Nippon Mektron | Japan | A leading manufacturer of flexible printed circuits (FPCs) and rigid-flex PCBs, serving the automotive, consumer electronics, and healthcare industries. |
Zhen Ding Tech | Taiwan | A major supplier of HDI (high-density interconnect) PCBs for smartphones, tablets, and other consumer electronics. |
TTM Technologies | USA | A top-tier PCB manufacturer offering a full range of services, from quick-turn prototypes to high-volume production. |
These companies, along with many others, form a complex and interconnected ecosystem that drives innovation and growth in the electronics industry.
Trends and innovations in PCB manufacturing
As the demand for smaller, faster, and more powerful electronic devices continues to grow, PCB manufacturers are constantly pushing the boundaries of what is possible. Some of the key trends and innovations shaping the industry include:
Advanced materials
New substrate materials, such as high-frequency laminates and thermally conductive materials, are enabling the creation of PCBs that can operate in challenging environments and support the latest wireless technologies.
Miniaturization
The trend towards miniaturization is driving the adoption of advanced packaging technologies, such as chip-on-board (COB) and system-in-package (SiP), which allow for greater integration and higher component density on PCBs.
Flexible and stretchable electronics
The development of flexible and stretchable PCBs is opening up new possibilities for wearable devices, medical implants, and other applications where conformability and durability are essential.
Additive manufacturing
3D printing technologies, such as conductive ink printing and stereolithography, are being explored as potential alternatives to traditional subtractive PCB manufacturing methods, offering greater design freedom and faster prototyping.
Sustainability
As environmental concerns continue to grow, PCB manufacturers are increasingly focusing on sustainable practices, such as the use of lead-free solders, halogen-free materials, and recyclable packaging.
Frequently Asked Questions (FAQ)
-
What is the difference between a bare board and an assembled pcb?
A bare board is a PCB that has been fabricated but does not have any components installed. An assembled PCB, on the other hand, is a board that has been populated with components and is ready for integration into an electronic device. -
What are the different types of PCBs?
There are several types of PCBs, including: - Single-sided PCBs: These have components and traces on only one side of the board.
- Double-sided PCBs: These have components and traces on both sides of the board.
- Multi-layer PCBs: These have multiple layers of conductive material, separated by insulating layers, allowing for more complex circuits and higher component density.
- flexible pcbs: These are made from flexible materials, such as polyimide, and can bend and flex to fit into tight spaces or conform to curved surfaces.
-
Rigid-flex PCBs: These combine rigid and flexible sections, providing the benefits of both types of boards in a single unit.
-
What is the typical turnaround time for PCB manufacturing?
Turnaround times can vary widely depending on the complexity of the board, the volume of the order, and the manufacturer’s capacity. For simple, prototype boards, turnaround times can be as short as 24-48 hours. For high-volume, complex boards, lead times can extend to several weeks or even months. -
How do I choose the right PCB manufacturer for my project?
When selecting a PCB manufacturer, consider factors such as: - Experience and expertise in your specific industry or application
- Range of services offered (e.g., design, fabrication, assembly)
- Quality control and certification (e.g., ISO 9001, UL, RoHS)
- Pricing and lead times
-
Customer support and communication
It’s also a good idea to request quotes from multiple manufacturers and review their references and customer testimonials before making a decision. -
What is the future outlook for the PCB manufacturing industry?
The PCB manufacturing industry is expected to continue growing in the coming years, driven by the increasing demand for electronic devices across various sectors, such as automotive, healthcare, aerospace, and consumer electronics. However, the industry also faces challenges, such as supply chain disruptions, rising material costs, and skilled labor shortages. To remain competitive, PCB manufacturers will need to invest in advanced technologies, streamline their operations, and foster close collaborations with their customers and suppliers.
In conclusion, PCB manufacturing is a vital and dynamic industry that plays a crucial role in enabling the development and production of modern electronic devices. From design and fabrication to assembly and testing, PCB manufacturers offer a wide range of services to meet the diverse needs of their customers. As the industry continues to evolve, driven by technological advancements and changing market demands, PCB manufacturers will need to remain agile, innovative, and customer-focused to succeed in an increasingly competitive global marketplace.