Step 1: Concept and Schematic Design
The first step in PCB designing is to develop a concept and create a schematic design. This involves:
- Defining the purpose and functionality of the PCB
- Identifying the components required to achieve the desired functionality
- Creating a schematic diagram that shows the interconnections between the components
The schematic design is a crucial step as it serves as the blueprint for the entire PCB design process. It is essential to ensure that the schematic is accurate and complete before moving on to the next step.
Tools used in Schematic Design
Tool | Description |
---|---|
OrCAD Capture | A schematic capture tool used to create and edit schematic diagrams |
KiCad | An open-source schematic capture and PCB design tool |
Eagle | A popular schematic capture and PCB design tool used by hobbyists and professionals |
Altium Designer | A comprehensive PCB design software suite used by professional pcb designers |
Step 2: Component Placement
Once the schematic design is complete, the next step is to place the components on the PCB layout. This involves:
- Determining the size and shape of the PCB
- Placing the components on the PCB layout in a logical and efficient manner
- Ensuring that the components are spaced appropriately to avoid interference and signal integrity issues
Component placement is a critical step in PCB designing as it directly affects the performance and reliability of the final product. It is essential to consider factors such as signal integrity, thermal management, and manufacturability when placing components on the PCB layout.
Factors to Consider in Component Placement
Factor | Description |
---|---|
Signal Integrity | Ensuring that the signals are routed correctly and do not interfere with each other |
Thermal Management | Placing components in a way that allows for proper heat dissipation |
Manufacturability | Ensuring that the PCB layout is compatible with the manufacturing process |
Mechanical Constraints | Considering the mechanical requirements of the final product, such as size and shape |
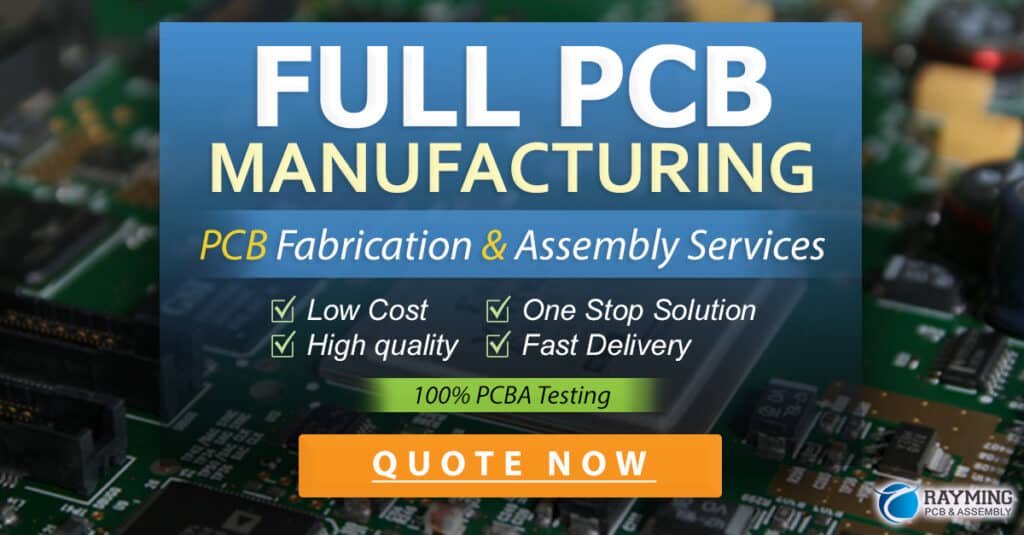
Step 3: Routing
After the components are placed on the PCB layout, the next step is to route the connections between the components. This involves:
- Defining the width and spacing of the traces
- Routing the traces between the components in a way that minimizes signal interference and crosstalk
- Adding vias to connect traces on different layers of the PCB
Routing is a complex process that requires careful consideration of signal integrity, impedance matching, and EMI/EMC compliance. It is essential to follow best practices and guidelines when routing the PCB to ensure optimal performance and reliability.
pcb routing Guidelines
Guideline | Description |
---|---|
Trace Width | The width of the traces should be appropriate for the current carrying capacity and signal integrity requirements |
Trace Spacing | The spacing between traces should be sufficient to avoid signal interference and crosstalk |
Via Sizing | The size and spacing of vias should be appropriate for the current carrying capacity and manufacturing process |
Length Matching | Critical signals should be length-matched to ensure signal integrity and timing requirements are met |
Step 4: pcb stackup Design
PCB stackup design involves determining the number of layers in the PCB and the arrangement of those layers. This involves:
- Determining the number of layers required based on the complexity of the design and the signal integrity requirements
- Arranging the layers in a way that minimizes signal interference and crosstalk
- Specifying the material and thickness of each layer in the stackup
PCB stackup design is a critical step in PCB designing as it directly affects the performance, reliability, and manufacturability of the final product. It is essential to consider factors such as signal integrity, impedance control, and manufacturability when designing the PCB stackup.
Common PCB Stackups
Stackup | Description |
---|---|
2-Layer | A simple stackup consisting of a top and bottom layer, suitable for low-complexity designs |
4-Layer | A common stackup consisting of top, bottom, and two internal layers, suitable for most designs |
6-Layer | A stackup with six layers, suitable for high-speed and high-density designs |
8-Layer and Above | Complex stackups with eight or more layers, suitable for very high-speed and high-density designs |
Step 5: Design Rule Check (DRC)
After completing the PCB layout and routing, the next step is to perform a Design Rule Check (DRC). This involves:
- Checking the PCB layout and routing against a set of predefined design rules
- Identifying and correcting any errors or violations of the design rules
- Ensuring that the PCB layout and routing are compatible with the manufacturing process
DRC is an essential step in PCB designing as it helps to identify and correct any errors or issues before the PCB goes into manufacturing. It is important to perform a thorough DRC and address any issues before proceeding to the next step.
Common DRC Checks
Check | Description |
---|---|
Clearance | Checking the spacing between components, traces, and vias to ensure they meet the minimum requirements |
Trace Width | Checking the width of traces to ensure they meet the minimum requirements for current carrying capacity |
Annular Ring | Checking the size of the annular ring around vias and pads to ensure they meet the minimum requirements |
Copper Pour | Checking the copper pour for any isolated islands or disconnected areas |
Step 6: Gerber File Generation
Once the PCB layout and routing are complete and have passed the DRC, the next step is to generate the Gerber files. Gerber files are the industry-standard format for PCB manufacturing and contain all the necessary information for fabricating the PCB. This involves:
- Exporting the PCB layout and routing information in Gerber format
- Generating separate Gerber files for each layer of the PCB
- Including additional files such as the drill file and silkscreen layers
It is essential to ensure that the Gerber files are accurate and complete before sending them to the manufacturer. Any errors or omissions in the Gerber files can result in manufacturing defects or delays.
Common Gerber File Formats
Format | Description |
---|---|
RS-274X | The most common Gerber file format, used for defining the copper layers, solder mask, and silkscreen |
Excellon | The standard format for defining the drill holes and their locations |
ODB++ | A more advanced format that includes additional information such as netlist and component data |
Step 7: pcb fabrication
The final step in PCB designing is to send the Gerber files to a pcb manufacturer for fabrication. This involves:
- Choosing a reputable PCB manufacturer with experience in fabricating the type of PCB you have designed
- Providing the manufacturer with the Gerber files and any additional instructions or requirements
- Reviewing and approving the manufacturer’s quote and timeline for fabrication
PCB fabrication typically takes several days to several weeks, depending on the complexity of the design and the manufacturing process used. It is essential to choose a reputable manufacturer and communicate clearly to ensure that the final product meets your specifications and requirements.
PCB Manufacturing Processes
Process | Description |
---|---|
Etching | The process of removing unwanted copper from the PCB to create the desired circuit pattern |
Drilling | The process of drilling holes in the PCB for component leads and vias |
Plating | The process of applying a thin layer of metal, such as gold or nickel, to the PCB to improve conductivity and prevent oxidation |
Solder Mask | The process of applying a protective coating to the PCB to prevent solder bridging and improve the appearance |
Silkscreen | The process of printing text and symbols on the PCB for component identification and assembly instructions |
Frequently Asked Questions (FAQ)
What software is used for PCB designing?
There are several software tools used for PCB designing, including:
- Altium Designer
- OrCAD
- Eagle
- KiCad
Each software has its own strengths and weaknesses, and the choice of software depends on the specific requirements of the project and the designer’s preferences.
What are the different types of PCBs?
There are several types of PCBs, including:
- Single-sided PCBs: PCBs with components and traces on only one side of the board
- Double-sided PCBs: PCBs with components and traces on both sides of the board
- Multi-layer PCBs: PCBs with multiple layers of traces and insulation, allowing for more complex designs and higher component density
The choice of PCB type depends on the complexity of the design, the signal integrity requirements, and the manufacturing process used.
What are some common PCB design mistakes to avoid?
Some common PCB design mistakes to avoid include:
- Incorrectly sized or spaced traces and vias
- Insufficient clearance between components and traces
- Incorrect component placement or orientation
- Lack of proper grounding and shielding
- Inconsistent or incorrect labeling and silkscreen
These mistakes can lead to manufacturing defects, signal integrity issues, and reduced reliability of the final product. It is essential to follow best practices and guidelines when designing PCBs to avoid these mistakes.
How long does PCB fabrication typically take?
PCB fabrication typically takes several days to several weeks, depending on the complexity of the design and the manufacturing process used. Some factors that can affect the fabrication time include:
- The number of layers in the PCB
- The size and shape of the PCB
- The type of materials used
- The quantity of PCBs being manufactured
It is important to communicate clearly with the PCB manufacturer and provide them with accurate and complete information to ensure that the fabrication process goes smoothly and on schedule.
What are some factors to consider when choosing a PCB manufacturer?
When choosing a PCB manufacturer, some factors to consider include:
- Experience and reputation in the industry
- Quality control processes and certifications
- Capabilities and expertise in fabricating the specific type of PCB being designed
- Pricing and lead times
- Customer support and communication
It is essential to choose a reputable and experienced PCB manufacturer to ensure that the final product meets the required specifications and quality standards.
Conclusion
PCB designing is a complex and multi-step process that requires technical knowledge, creativity, and attention to detail. From concept and schematic design to component placement, routing, and fabrication, each step plays a critical role in the overall success of the project.
By following best practices and guidelines, using appropriate tools and software, and working with reputable manufacturers, PCB designers can create high-quality and reliable electronic products that meet the needs of their customers and end-users.