Introduction to PCB Design
Printed Circuit Board (PCB) design is the process of creating a layout for the electronic components and their interconnections on a PCB. Designing your own PCB can be a rewarding experience, allowing you to create custom electronic devices tailored to your specific needs. In this article, we will guide you through the steps involved in designing your own PCB, from concept to fabrication.
Understanding the Basics of PCB Design
Before diving into the PCB design process, it’s essential to understand the basics of PCB design. A PCB consists of several layers of conductive and insulating materials, with electronic components mounted on the surface and interconnected through conductive traces.
PCB Layers
A typical PCB can have multiple layers, each serving a specific purpose:
- Copper Layers: These are the conductive layers that carry electrical signals between components. A PCB can have one or more copper layers, depending on the complexity of the design.
- Substrate Layer: This is the insulating layer that separates the copper layers and provides mechanical support to the PCB.
- Solder Mask Layer: This layer covers the copper traces, protecting them from oxidation and preventing short circuits during soldering.
- Silkscreen Layer: This layer contains text and symbols that help identify components and provide assembly instructions.
pcb components
PCBs can accommodate a wide range of electronic components, including:
- Resistors
- Capacitors
- Inductors
- Diodes
- Transistors
- Integrated Circuits (ICs)
- Connectors
- Switches
- LEDs
Each component has specific requirements for placement, orientation, and interconnection, which must be considered during the PCB design process.
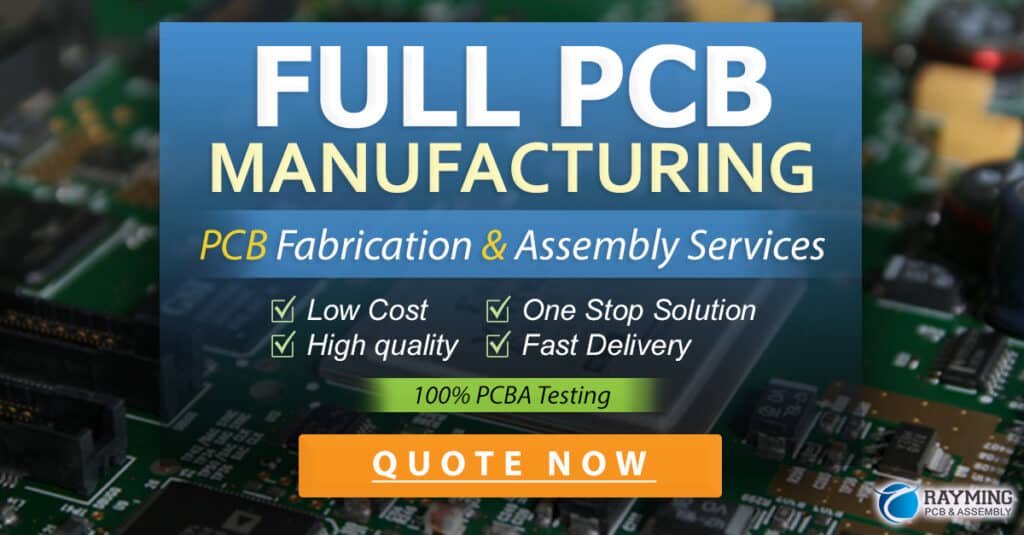
PCB Design Workflow
The PCB design workflow typically involves the following steps:
- Schematic Design: Create a schematic diagram that represents the electrical connections between components.
- Component Selection: Choose the appropriate components based on the schematic design and the desired functionality of the PCB.
- pcb layout: Arrange the components on the PCB and route the interconnections between them.
- Design Rule Check (DRC): Verify that the PCB layout meets the manufacturing constraints and design rules.
- Gerber File Generation: Generate the Gerber files, which are the industry-standard format for pcb fabrication.
- Fabrication: Send the Gerber files to a pcb manufacturer for fabrication.
Let’s explore each step in more detail.
Schematic Design
The schematic design is the first step in the PCB design process. It involves creating a diagram that represents the electrical connections between components using schematic capture software. Popular schematic capture tools include:
- KiCad
- Eagle
- Altium Designer
- OrCAD
When creating the schematic, consider the following:
- Use schematic symbols that accurately represent the components.
- Assign unique reference designators to each component (e.g., R1 for resistor 1, C1 for capacitor 1).
- Specify the component values and tolerances.
- Define the power and ground connections.
- Use net labels to identify signal connections between components.
Component Selection
Once the schematic design is complete, the next step is to select the appropriate components for the PCB. Consider the following factors when choosing components:
- Electrical specifications (e.g., voltage rating, current rating, power dissipation)
- Package type and size (e.g., through-hole, surface-mount, SMD package dimensions)
- Availability and cost
- Manufacturer reputation and quality
It’s important to choose components that meet the electrical requirements of the circuit and are compatible with the PCB manufacturing process.
PCB Layout
The PCB layout is the process of arranging the components on the PCB and routing the interconnections between them. This step is critical to ensure proper functionality, manufacturability, and reliability of the PCB.
When creating the PCB layout, consider the following:
- Component placement: Arrange the components in a logical and efficient manner, minimizing the distance between interconnected components and avoiding physical interference.
- Routing: Route the interconnections between components using copper traces. Consider factors such as trace width, spacing, and length to minimize signal integrity issues and ensure manufacturability.
- Power and ground planes: Use copper planes to distribute power and ground connections efficiently across the PCB.
- Thermal considerations: Ensure adequate thermal dissipation for power-hungry components by providing sufficient copper area and thermal vias.
- Manufacturability: Adhere to the manufacturing constraints and design rules provided by the PCB fabrication house, such as minimum trace width, spacing, and drill sizes.
Popular PCB layout software tools include:
- KiCad
- Eagle
- Altium Designer
- OrCAD
Design Rule Check (DRC)
After completing the PCB layout, it’s essential to perform a Design Rule Check (DRC) to verify that the design meets the manufacturing constraints and design rules. The DRC checks for issues such as:
- Minimum trace width and spacing violations
- Minimum drill size violations
- Copper clearance violations
- Silk screen clearance violations
- Solder mask clearance violations
Most PCB layout software tools have built-in DRC functionality that can automatically detect and highlight violations, allowing you to make necessary corrections before proceeding to the next step.
Gerber File Generation
Once the PCB layout passes the DRC, the next step is to generate the Gerber files. Gerber files are the industry-standard format for PCB fabrication and contain all the necessary information for manufacturing the PCB.
Gerber files typically include:
- Copper layer files (e.g., top layer, bottom layer, inner layers)
- Solder mask files
- Silkscreen files
- Drill files
Most PCB layout software tools have built-in Gerber file generation functionality, allowing you to export the necessary files for fabrication.
Fabrication
The final step in the PCB design process is fabrication. Send the Gerber files to a reputable PCB manufacturer, who will use them to create the physical PCB.
When choosing a PCB manufacturer, consider the following:
- Manufacturing capabilities (e.g., number of layers, minimum trace width and spacing, hole sizes)
- Turnaround time
- Cost
- Quality and reliability
- Customer support
It’s important to communicate clearly with the PCB manufacturer and provide all the necessary files and specifications to ensure a smooth fabrication process.
PCB Design Best Practices
To ensure a successful PCB design, consider the following best practices:
- Keep it simple: Avoid unnecessary complexity in your design. Keep the layout clean and organized, and use standard component packages whenever possible.
- Plan for manufacturability: Adhere to the manufacturing constraints and design rules provided by the PCB fabrication house. This will help ensure that your design can be manufactured reliably and cost-effectively.
- Consider signal integrity: Minimize the length of high-speed signal traces and use appropriate termination techniques to reduce signal reflections and crosstalk.
- Provide adequate power distribution: Use copper planes and wide traces to distribute power efficiently across the PCB. Consider the current requirements of each component and ensure that the power traces can handle the necessary current.
- Use a consistent naming convention: Assign meaningful and consistent names to components, nets, and layers. This will make it easier to navigate and understand the design.
- Document your design: Create a clear and concise documentation package that includes the schematic, PCB layout, bill of materials (BOM), and assembly instructions. This will help ensure that the PCB can be manufactured and assembled correctly.
PCB Design Tools
There are several PCB design tools available, ranging from free and open-source to commercial and enterprise-level solutions. Some popular PCB design tools include:
KiCad
KiCad is a free and open-source PCB design tool that offers a complete suite of applications for schematic capture, PCB layout, and Gerber file generation. It supports a wide range of PCB design features and has an active user community.
Autodesk Eagle
Autodesk Eagle is a popular PCB design tool that offers a streamlined and intuitive interface for schematic capture and PCB layout. It has a extensive library of components and supports a wide range of PCB manufacturing capabilities.
Altium Designer
Altium Designer is a professional-grade PCB design tool that offers advanced features for schematic capture, PCB layout, and 3D visualization. It has a comprehensive library of components and supports high-speed PCB design techniques.
OrCAD
OrCAD is an enterprise-level PCB design tool that offers a complete suite of applications for schematic capture, PCB layout, and simulation. It has a extensive library of components and supports a wide range of PCB manufacturing capabilities.
Frequently Asked Questions (FAQ)
-
What is the minimum number of layers required for a PCB?
A PCB can have as few as one layer (single-sided) or as many as required by the complexity of the design. Simple designs can often be implemented on single-sided or double-sided PCBs, while more complex designs may require four or more layers. -
What is the difference between through-hole and surface-mount components?
Through-hole components have leads that are inserted into holes drilled in the PCB and soldered on the opposite side. Surface-mount components are mounted directly on the surface of the PCB and soldered in place. Surface-mount components are generally smaller and more suitable for high-density designs. -
What is the purpose of a solder mask?
A solder mask is a layer of polymer material applied to the copper traces on a PCB. It protects the copper from oxidation and prevents short circuits during the soldering process. The solder mask also provides electrical insulation between adjacent traces. -
What are the advantages of using a four-layer PCB compared to a two-layer PCB?
A four-layer PCB offers several advantages over a two-layer PCB, including: - Improved signal integrity due to the use of dedicated power and ground planes
- Reduced electromagnetic interference (EMI) and crosstalk
- Higher component density and more routing options
-
Better thermal management due to the additional copper layers
-
What is the typical turnaround time for PCB fabrication?
The turnaround time for PCB fabrication varies depending on the complexity of the design, the chosen fabrication house, and the manufacturing options selected. Typical turnaround times range from a few days to several weeks. Rush services may be available for an additional cost.
Conclusion
Designing your own PCB can be a challenging but rewarding experience. By understanding the basics of PCB design, following a structured workflow, and adhering to best practices, you can create custom electronic devices that meet your specific requirements.
Remember to choose the appropriate components, create a clear and organized schematic, and carefully plan your PCB layout. Use PCB design tools that suit your needs and budget, and always perform a thorough Design Rule Check before sending your files for fabrication.
With patience, practice, and attention to detail, you can become proficient in PCB design and bring your electronic projects to life.