Introduction
The field of electronics design and manufacturing has undergone significant transformations over the past few decades. One of the most groundbreaking advancements in recent years is the ability to 3D print circuit boards for fast prototyping. This technology is revolutionizing the way engineers, designers, and hobbyists approach the development of electronic devices. By enabling rapid iteration, reducing costs, and offering unparalleled design flexibility, 3D printing is poised to become a cornerstone of modern electronics prototyping.
This article delves into the intricacies of 3D printing circuit boards, exploring the technology behind it, its advantages, challenges, and future potential. We will also examine real-world applications and provide insights into how this innovative approach is shaping the future of electronics design.
Understanding 3D Printing in Electronics
What is 3D Printing?
3D printing, also known as additive manufacturing, is a process of creating three-dimensional objects by depositing material layer by layer based on a digital model. Unlike traditional manufacturing methods that involve cutting, drilling, or molding, 3D printing builds objects from the ground up, allowing for complex geometries and intricate designs that would be difficult or impossible to achieve otherwise.
The Evolution of 3D Printing in Electronics
While 3D printing has been widely adopted in industries such as aerospace, automotive, and healthcare, its application in electronics is relatively recent. The ability to print conductive materials alongside insulating substrates has opened up new possibilities for creating functional electronic components, including circuit boards.
Traditional circuit board manufacturing involves multiple steps, including designing the board, etching copper layers, drilling holes, and soldering components. This process can be time-consuming and expensive, especially for small-scale production or prototyping. 3D printing offers a more streamlined alternative, allowing for the direct fabrication of circuit boards with embedded components in a single process.
How 3D Printing Circuit Boards Works
Materials Used in 3D Printing Circuit Boards
The success of 3D printing circuit boards hinges on the availability of suitable materials. Key materials include:
- Conductive Inks and Filaments: These materials contain conductive particles, such as silver, copper, or graphene, which allow for the creation of conductive traces on the circuit board. Conductive inks are typically used in inkjet-based 3D printers, while conductive filaments are used in fused deposition modeling (FDM) printers.
- Insulating Substrates: The base material of the circuit board must be non-conductive to prevent short circuits. Common insulating materials include polylactic acid (PLA), acrylonitrile butadiene styrene (ABS), and polyamide (nylon).
- Dielectric Materials: These materials are used to separate different layers of conductive traces in multi-layer circuit boards. Dielectric inks or filaments are deposited between conductive layers to ensure proper insulation.
3D Printing Technologies for Circuit Boards
Several 3D printing technologies are being adapted for circuit board fabrication:
- Fused Deposition Modeling (FDM): FDM is one of the most common 3D printing methods, where a thermoplastic filament is extruded through a heated nozzle to create the object layer by layer. For circuit boards, FDM printers can use conductive filaments to print conductive traces directly onto an insulating substrate.
- Inkjet Printing: Inkjet-based 3D printers use conductive inks to deposit conductive traces onto a substrate. This method offers high precision and is suitable for creating fine-pitch traces and complex geometries.
- Aerosol Jet Printing: This advanced 3D printing technique uses a focused aerosol stream to deposit conductive and dielectric materials with high precision. Aerosol jet printing is capable of creating multi-layer circuit boards with embedded components.
- Stereolithography (SLA): SLA uses a laser to cure liquid resin into solid layers. While traditionally used for creating high-resolution prototypes, SLA can also be adapted for circuit board fabrication by incorporating conductive resins.
The 3D Printing Process for Circuit Boards
The process of 3D printing a circuit board typically involves the following steps:
- Design: The circuit board design is created using computer-aided design (CAD) software. The design includes the layout of conductive traces, vias, and component placements.
- Material Selection: Appropriate conductive and insulating materials are selected based on the design requirements.
- Printing: The 3D printer deposits the conductive and insulating materials layer by layer to build the circuit board. In some cases, components can be embedded directly into the board during the printing process.
- Curing/Post-Processing: After printing, the circuit board may require curing or post-processing to ensure the conductive traces are fully functional and the board is structurally sound.
- Component Assembly: If components were not embedded during printing, they are soldered onto the board using traditional methods or conductive adhesives.
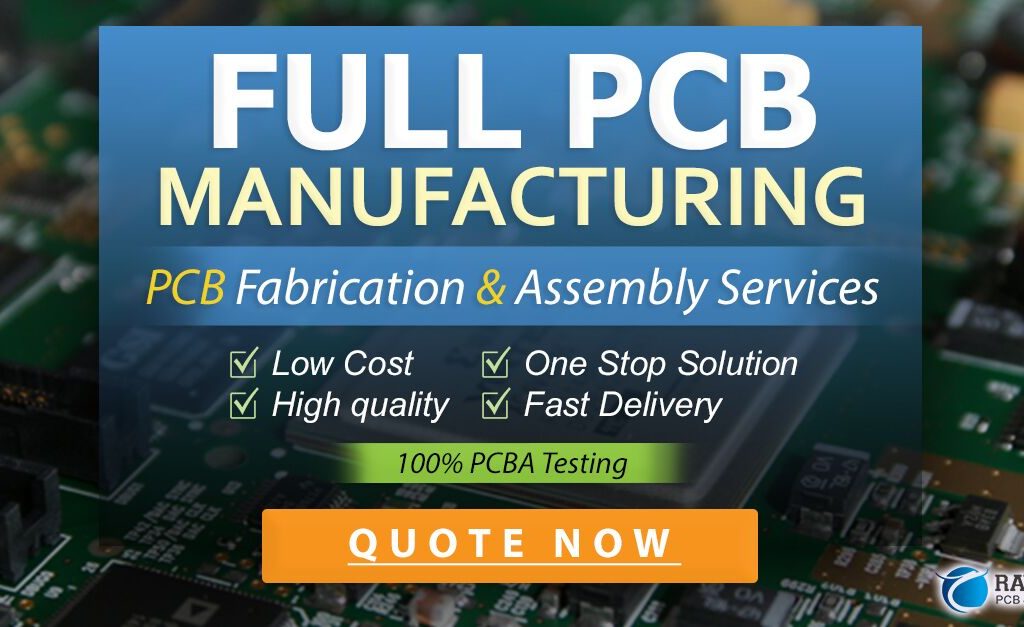
Advantages of 3D Printing Circuit Boards for Fast Prototyping
Rapid Iteration and Design Flexibility
One of the most significant advantages of 3D printing circuit boards is the ability to rapidly iterate designs. Traditional circuit board manufacturing can take days or even weeks, depending on the complexity and the manufacturer’s lead time. With 3D printing, designers can produce a prototype in a matter of hours, allowing for quick testing and refinement.
Moreover, 3D printing offers unparalleled design flexibility. Designers are no longer constrained by the limitations of traditional manufacturing processes, such as the need for flat, rigid boards. 3D printing enables the creation of curved, flexible, and even three-dimensional circuit boards, opening up new possibilities for innovative product designs.
Cost-Effectiveness for Prototyping
Traditional circuit board manufacturing often involves high setup costs, especially for small production runs or custom designs. 3D printing eliminates many of these costs by allowing for on-demand production without the need for expensive tooling or molds. This makes it an ideal solution for prototyping, where the cost per unit is less critical than the ability to quickly and affordably test new ideas.
Reduced Waste and Environmental Impact
3D printing is an additive manufacturing process, meaning material is only deposited where it is needed. This contrasts with traditional subtractive methods, where excess material is removed and often discarded. As a result, 3D printing generates less waste, making it a more environmentally friendly option for circuit board production.
Customization and Complexity
3D printing allows for the creation of highly customized and complex circuit boards that would be difficult or impossible to produce using traditional methods. For example, multi-layer boards with intricate interconnects, embedded components, and non-standard shapes can be easily fabricated with 3D printing. This capability is particularly valuable for specialized applications, such as medical devices, aerospace systems, and wearable electronics.
Challenges and Limitations of 3D Printing Circuit Boards
Material Limitations
While significant progress has been made in developing conductive materials for 3D printing, there are still limitations in terms of conductivity, durability, and compatibility with standard electronic components. Conductive inks and filaments often have higher resistivity compared to traditional copper traces, which can impact the performance of high-frequency or high-power circuits.
Additionally, the range of available materials for 3D printing circuit boards is still relatively limited compared to traditional manufacturing. This can restrict the types of circuits that can be effectively printed and may require designers to compromise on certain aspects of their designs.
Resolution and Precision
The resolution and precision of 3D printing technologies are improving, but they still lag behind traditional circuit board manufacturing methods, especially for fine-pitch traces and small components. Achieving the level of detail required for complex circuits can be challenging, particularly with FDM and inkjet printing.
Post-Processing Requirements
While 3D printing can streamline the fabrication process, some post-processing steps may still be necessary, such as curing conductive inks, removing support structures, or soldering components. These additional steps can add time and complexity to the overall process, reducing some of the speed advantages of 3D printing.
Scalability
3D printing is well-suited for prototyping and small-scale production, but it may not be as cost-effective or efficient for large-scale manufacturing. The speed of 3D printing is generally slower than traditional methods, and the cost per unit may not scale as favorably for high-volume production.
Real-World Applications of 3D Printed Circuit Boards
Rapid Prototyping in Research and Development
3D printing circuit boards is particularly valuable in research and development (R&D) settings, where rapid prototyping is essential for testing new ideas and concepts. Engineers and researchers can quickly produce and test multiple iterations of a design, accelerating the development process and reducing time-to-market.
Custom and Low-Volume Production
For custom or low-volume production runs, 3D printing offers a cost-effective alternative to traditional manufacturing. This is especially useful for niche markets, specialized equipment, or bespoke electronic devices where the demand may not justify the high setup costs of traditional methods.
Wearable Electronics
The flexibility and customization capabilities of 3D printing make it an ideal solution for wearable electronics, where circuit boards often need to conform to the shape of the human body. 3D printing allows for the creation of flexible, lightweight, and ergonomic circuit boards that can be seamlessly integrated into clothing, accessories, or medical devices.
Aerospace and Defense
In the aerospace and defense industries, where weight, space, and performance are critical factors, 3D printing offers the ability to create highly optimized and customized circuit boards. These boards can be designed to fit specific form factors, reduce weight, and improve performance, making them ideal for use in satellites, drones, and other advanced systems.
Education and Hobbyist Projects
3D printing circuit boards is also gaining traction in educational settings and among hobbyists. The ability to quickly and affordably produce custom circuit boards allows students and enthusiasts to experiment with electronics design, learn new skills, and bring their creative ideas to life.
The Future of 3D Printing Circuit Boards
Advancements in Materials
As research into conductive materials continues, we can expect to see significant advancements in the performance and versatility of 3D printed circuit boards. New materials with higher conductivity, improved durability, and better compatibility with standard components will expand the range of applications for 3D printing in electronics.
Integration with Other Technologies
The integration of 3D printing with other emerging technologies, such as artificial intelligence (AI) and the Internet of Things (IoT), holds great promise for the future of electronics design. AI-driven design tools could optimize circuit layouts for 3D printing, while IoT devices could benefit from the customization and rapid prototyping capabilities of 3D printed circuit boards.
Multi-Material and Multi-Functional Printing
Future developments in 3D printing technology may enable the simultaneous printing of multiple materials, including conductive, insulating, and even semiconducting materials. This could lead to the creation of fully functional electronic devices in a single printing process, further streamlining the production of complex electronics.
Scalability and Industrial Adoption
As 3D printing technology continues to mature, we may see increased adoption in industrial settings for large-scale production. Advances in printing speed, material handling, and post-processing automation could make 3D printing a viable option for high-volume manufacturing, particularly for specialized or customized products.
Conclusion
3D printing circuit boards for fast prototyping represents a significant leap forward in the field of electronics design and manufacturing. By offering rapid iteration, cost-effectiveness, and unparalleled design flexibility, this technology is empowering engineers, designers, and hobbyists to push the boundaries of what is possible in electronics.
While there are still challenges to overcome, the ongoing advancements in materials, printing technologies, and integration with other emerging fields are paving the way for a future where 3D printed circuit boards are commonplace. As this technology continues to evolve, it will undoubtedly play a crucial role in shaping the next generation of electronic devices, from wearable gadgets to advanced aerospace systems.
In a world where speed, customization, and innovation are paramount, 3D printing circuit boards is not just a tool for fast prototyping—it is a catalyst for the future of electronics.