Introduction
Rigid-flex printed circuit boards (PCBs) are increasingly being used in a wide variety of applications and industries. This unique technology combines rigid circuit boards and flexible circuits into a single integrated assembly. The rigid sections provide stability for component mounting while the dynamic flexible interconnects enable three-dimensional configurations, motion and compact folding.
Rigid flex PCBs open up new possibilities in electronic product design thanks to their versatility. In this article, we will explore the different applications and end products that utilize rigid-flex PCB technology.
Key Application Areas
Here are some of the major industries and products using rigid-flex PCBs:
Consumer Electronics
Consumer electronics like mobile phones, laptops, tablets, wearable devices, headphones and gaming gadgets all utilize rigid-flex PCBs. The compact format enables fitting the electronics into thin and tight enclosures of these mobile consumer products. The dynamic flex connections provide reliability in high vibration and drop impact environments.
Specific implementations include:
- Phone display interconnects
- Wearable product PCBs
- VR headset circuit boards
- Laptop hinge interconnects
- Tablet flex connectors
Automotive Electronics
Vehicles are packed with electronics and rigid-flex PCBs help optimize configurations in the tight under-hood spaces. The boards are engineered to withstand vibration, shock and temperature cycling in automotive environments.
Typical automotive applications:
- Powertrain modules
- LED headlight assemblies
- Auto camera modules
- Sensors and control units
- Infotainment hardware
- RADAR/LIDAR components
Medical Equipment
Medical devices like patient monitors, imaging systems and surgical equipment require dense, compact electronics. Rigid-flex allows packing multiple PCBAs efficiently into small sizes. The boards offer high reliability and flex durability for dynamic hospital environments.
Medical uses include:
- Portable imaging machines
- Wearable health monitors
- Surgical handpieces
- Dental camera interfaces
- Endoscopy pill cameras
Industrial Electronics
Industrial machinery with high vibration and contaminants benefit from rigid-flex PCBs. The boards withstand shock, dust, liquids and temperature swings in factory environments. The technology enables compact on-machine controllers and interconnects.
Industrial implementations:
- Robotics controls
- CNC machine interfaces
- Motor drive circuits
- Process controller hardware
- Programmable logic controllers
Defense Electronics
Rigid-flex PCBs meet the unique demands of military and aerospace applications. The boards withstand high g-forces while remaining lightweight. Ruggedized construction provides reliability in harsh environments. The technology enables dense electronics packaging.
Defense use cases:
- Avionics systems
- Missile guidance systems
- Soldier-worn electronics
- Spacecraft control boards
- Radar and electronic warfare tech
Internet of Things (IoT)
With the expansion of IoT edge nodes, smart sensors and compact controllers, rigid-flex PCBs support miniaturization and interconnectivity needs. The boards fit into small IoT enclosures while enabling flexible sensor arrays.
IoT applications:
- Smart home hubs
- Industrial IoT modules
- Wearable biosensors
- Smart city sensors
- Vehicle telematics units
This table summarizes the major industries and applications using rigid-flex PCBs:
Industry | Applications |
---|---|
Consumer Electronics | Mobile phones, laptops, wearables, VR headsets |
Automotive | Powertrain, LED lights, camera modules |
Medical | Imaging systems, health monitors, surgical tools |
Industrial | PLCs, controllers, robotics, CNC machines |
Defense | Avionics, radars, soldier-worn systems |
Internet of Things | Smart sensors, home hubs, industrial modules |
Next, we will look at some specific examples of rigid-flex PCB implementations across these application areas.
Application Examples
Here are some specific product examples that leverage rigid-flex PCB technology:
Wearable Fitness Tracker
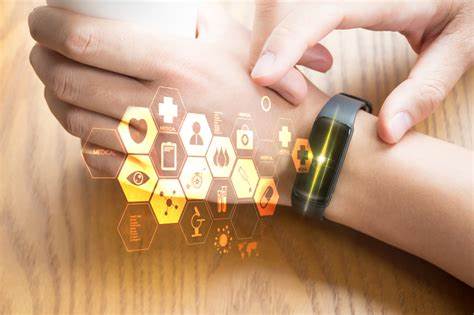
Rigid flex PCB in a wearable fitness tracker
Wearable devices like fitness bands and smart watches require flexible PCBs that can contour to the human body. Rigid-flex allows integrating rigid components while the flex areas route signals around the wrist. The dynamic flexing also improves reliability against mechanical stresses.
Laptop Hinge Interconnect
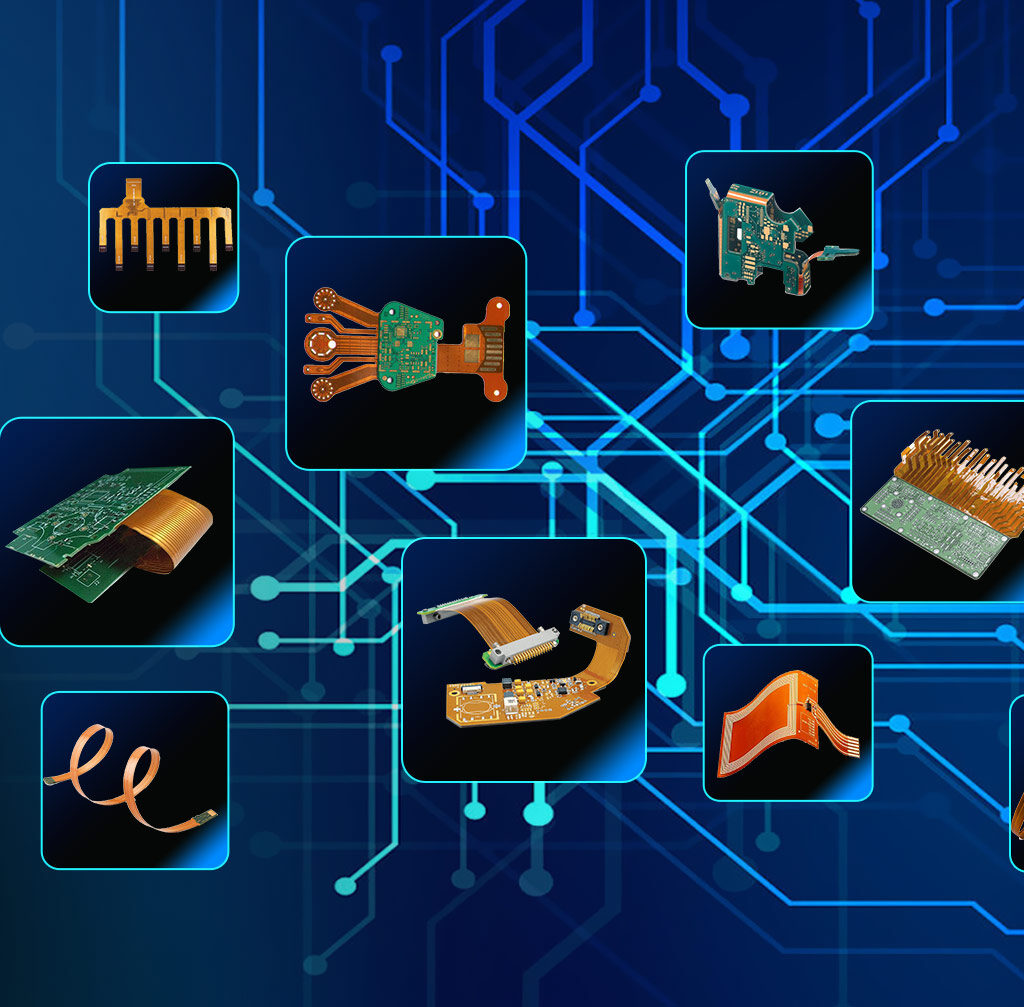
Rigid flex PCB in laptop hinge
Laptop hinge interconnects endure repeated open/close stresses over product life. Rigid-flex PCBs allow routing signals between motherboard and display while avoiding wiring harness failures. The flex sections absorb mechanical stresses while rigid areas provide stability.
Hospital Patient Monitor
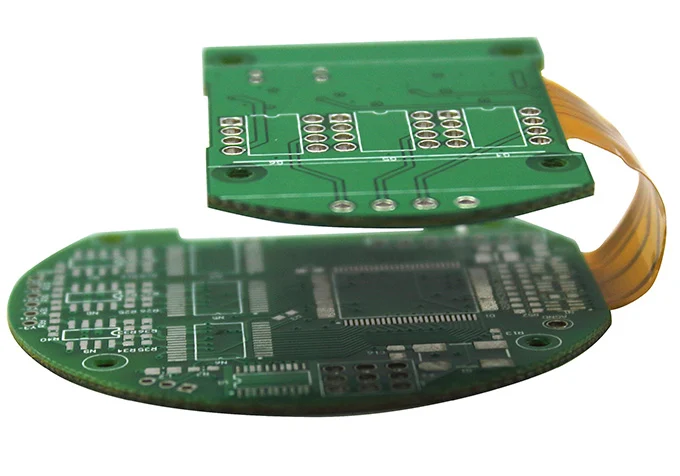
Rigid flex PCB in patient monitor system
Medical devices like patient monitors have space constraints and require dense, reliable PCBs. Rigid-flex allows efficiently packing electronics by folding and stacking rigid PCBAs. Flexible interconnects then route signals between modules in 3D space.
Automotive Camera Module
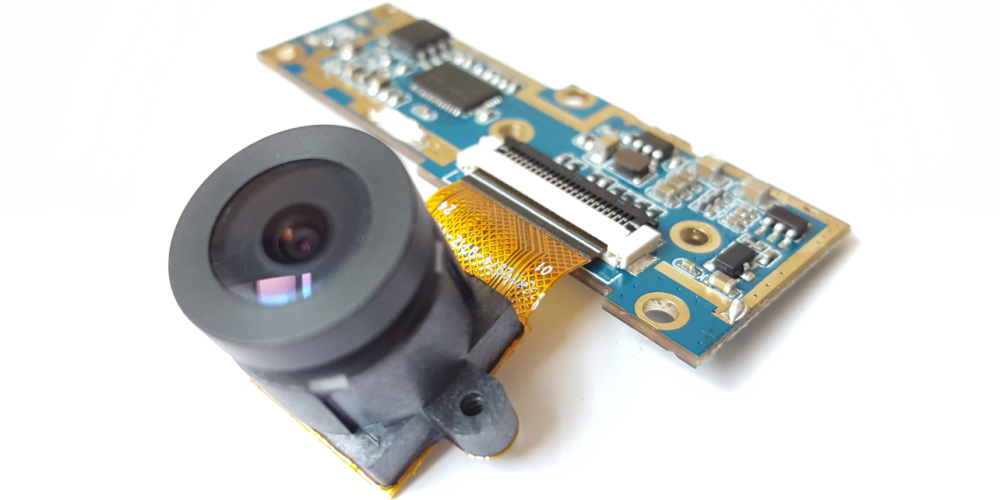
Rigid flex PCB for vehicle camera module
Vehicles are adding cameras for safety and navigation. Rigid-flex PCBs pack the electronics into the compact camera enclosures while allowing dynamic flex interconnects. Vibration resistance and thermal stability are also critical.
Avionics Mission Computer
Rigid flex PCB for an aircraft mission computer (Image credit: TTM)
Aerospace avionics systems require extremely lightweight and reliable electronics. Rigid-flex PCBs enable dense component mounting and stacking while saving weight versus cabling. Vibration resistance is also important.
Smart Home Hub
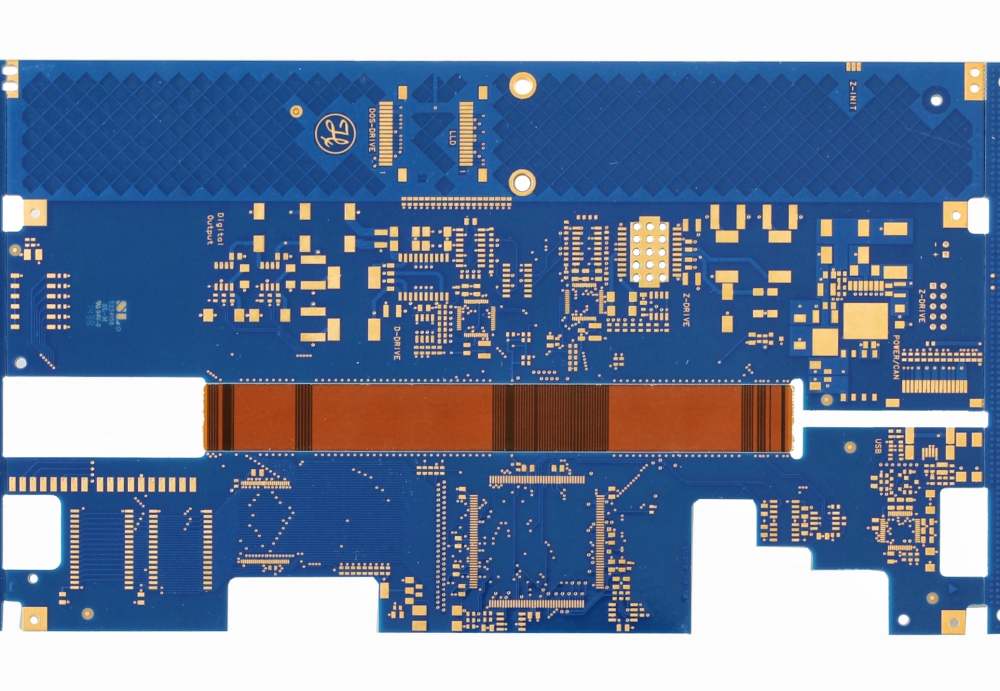
Rigid flex PCB in a smart home controller
Smart hubs for home automation require compact, efficient designs. Rigid-flex allows packing device interfaces into a small enclosure while enabling flex interconnects to sensors and antennas. Low cost manufacturing is also critical.
Benefits Overview
Here are the key benefits driving the widespread adoption of rigid-flex PCBs across industries:
- Compact size: Folds and dynamic configurations fit into tight spaces
- Interconnectivity: Flex layers replace wires and connectors
- Reliability: Withstands shock, vibration, bending
- Lightweight: Eliminates heavy cabling and components
- Efficiency: Combines multiple PCBAs efficiently
- Customizability: Enables unique 3D and flexing forms
- Cost effectiveness: Saves on assembly versus separate boards
In summary, rigid-flex PCBs enable smaller, lighter, and more reliable electronics critical across modern embedded systems and products. The technology will continue growing as complexity increases while size and weight constraints accelerate.
Frequently Asked Questions
Here are some common FAQs about rigid-flex PCB applications:
Q: Are rigid-flex PCBs suitable for high volume consumer electronics?
A: Yes, the boards are well proven in mass production including mobile phones and laptops that sell millions of units.
Q: What are some emerging applications for rigid-flex technology?
A: Electric vehicles, UAVs, IoT edge nodes, AR/VR headsets, and advanced wearables are fast growing areas of use.
Q: Can rigid-flex PCBs be used in high temperature environments?
A: Yes, specialized high-temp materials like polyimide and LCPflex can withstand over 260°C making them suitable for automotive and aerospace needs.
Q: Are there any industry certification standards for using rigid-flex boards?
A: Medical, automotive, and aerospace industries often require certification such as IPC-6013 qualification for flex durability.
Q: What is the typical rigid-flex board thickness in end products?
A: The total thickness usually ranges from 0.25mm to 2.5mm. Rigid sections are 0.2mm to 1.6mm while flex layers are under 0.2mm.
Conclusion
Rigid-flex PCB technology enables the capability, reliability and compactness needed in a diverse range of modern electronic products. As devices continue getting smaller and more complex, rigid-flex allows efficient configuration of rigid components interconnected by dynamic flex layers. The technology circumvents traditional design limitations by opening up the third dimension. With early planning and design, engineers across consumer, automotive, medical, industrial defense and IoT applications can leverage rigid-flex PCBs to achieve product goals.