Introduction to Rogers Flex Circuit Materials
Rogers Corporation is a leading manufacturer of high frequency circuit substrate materials used for making flexible printed circuits (FPC) and rigid flex PCBs. Rogers offers a range of low-loss flexible circuit materials under its RO4000 and RO3000 series laminates and bonding films. These materials are designed to enable reliable performance in high frequency, high speed circuits and applications where flexibility is required.
One of Rogers’ most popular flex circuit materials is Rogers RO4000 series high frequency circuit materials, which includes the widely used RO4350B laminate and adhesive. RO4000 series materials are reinforced woven glass reinforced hydrocarbon thermoset laminates and bonding films designed for performance demanding flexible printed circuit applications.
Key Benefits of Rogers Fr4 Flexible Circuit Materials
- Excellent dimensional stability for reliable plated through holes (PTHs)
- Low dielectric loss for improved high frequency signal integrity
- Tight dielectric constant (Dk) control for consistent electrical performance
- High peel and tensile strength for robust multilayer bonding
- Excellent flexural endurance and crack resistance
Rogers RO4350B Laminate Overview
The Rogers RO4350B laminate is a glass reinforced, ceramic-filled fluoropolymer composite circuit material designed for performance demanding rigid and multilayer flex PCB applications. With a dielectric constant of 3.48 at 10 GHz, RO4350B delivers excellent electrical performance for RF circuits and controlled impedance transmission lines.
Here are some key properties and characteristics of Rogers RO4350B laminate:
- Dielectric constant: 3.48 at 10 GHz
- Low loss tangent: 0.0037 at 10 GHz
- Glass transition temperature: >280°C
- Decomposition temperature: >425°C
- Z-axis coefficient of thermal expansion (CTE): 30 ppm/°C
- X and Y-axis CTE: 17 ppm/°C
- Flexural rigidity: 475,000 psi (3,276 MPa)
- Peel strength: 4.5 lbs/in (0.79 kg/cm)
- Water absorption: 0.03% after 48 hours at 23°C
With its stable dielectric constant vs. frequency, low loss, and tight impedance control, RO4350B is an excellent choice for RF/microwave circuits and controlled impedance lines up to 77 GHz. The ceramic filler allows it to be precisely punched or mechanically drilled, while the glass reinforcement provides excellent dimensional stability for reliable PTH interconnects.
Benefits of Rogers RO4350B Rigid Flex PCBs
The properties of Rogers RO4350B make it ideal for creating high performance rigid flex PCBs and flex circuits. Here are some of the benefits of using RO4350B rigid flex PCBs:
- Stable electrical performance – Consistent dielectric constant and low loss tangent across a wide frequency range ensures stable impedance control and signal integrity.
- Fine line trace capabilities – RO4350B allows the design of finer line width/space traces for increased circuit density.
- Excellent passive integration – Low loss and tight Dk tolerance supports embedded passives for space and weight savings.
- Reliable multilayer bonding – Robust adhesive and laminate bond strength prevents delamination.
- High temperature durability – With glass transition temperature above 280°C, RO4350B maintains mechanical and electrical integrity at lead-free soldering temperatures.
- Good flex life – Provides over 25,000 flexural cycles in rigid flex applications.
- Design flexibility – Compatible with a range of laminate and adhesive options to optimize rigid and flex sections.
Popular Configurations of Rogers Flex PCBs
Rogers flex materials allow a range of constructions to meet specific rigid-flex design requirements:
Single Layer Flexible Circuits
Consist of a single Rogers laminate layer with conductive traces on one or both sides. Provide basic flexibility for dynamic or high density interconnections.
Double Layer Flex Circuits
Use Rogers flexible bonding films to bond two circuitized laminate layers together. Allow traces on both outer surfaces. Better suited for controlled impedance lines.
Multilayer Rigid Flex
Alternate layers of Rogers laminates and adhesives to create multilayer circuits with sections of rigid boards and flexible interconnects between boards. Complex rigid flex configuration for advanced designs.
Rigidized Flexible Circuits
Add additional Rogers laminate layers in just the rigid sections for increased thickness and rigidity while keeping high flexibility in interconnect areas. Saves weight and space versus all rigid boards.
Typical Applications of Rogers Flexible PCBs
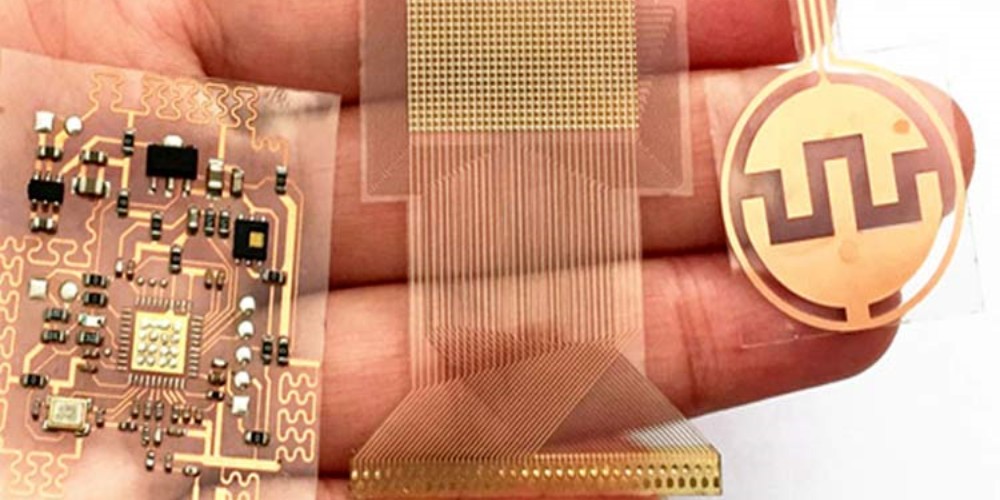
The high frequency capabilities, dimensional stability, and flexibility make Rogers circuits well suited for:
- Aerospace and defense electronics – Radar systems, avionics, missiles
- Satellite communications – Antennas, waveguides, transceivers
- Automotive electronics – Collision avoidance radar, powertrain modules
- Medical electronics – Patient monitoring systems, imaging equipment
- Consumer wearable devices – Smart watches, fitness trackers
- IoT devices – Sensors, actuators, antennas
For these applications, Rogers flex materials provide excellent electrical, mechanical and thermal properties to ensure reliable performance under demanding operating conditions.
Rogers RO4350B Processing Guidelines
To fabricate high quality PCBs using Rogers RO4350B, here are some key processing guidelines:
Inner layer preparation
- Ensure dielectric materials are fully cured prior to circuitization
- Use photoimageable or electrodeposited resists for fine line resolution
- Avoid glass styles that may puncture resist coatings
Oxide treatment
- Use chemical oxide or plasma etch to improve adhesion
- Adjust treatment levels to avoid over-etching laminates
Lamination
- Use Rogers approved lamination cycles with slow heat rise and pressure ramps
- Allow sufficient resin flow time for filling plated through holes
- Employ vacuum assist lamination processes whenever possible
Drilling
- Maintain sharp drill bits and proper clearance angles
- Low cutting speeds and feeds are recommended
- Avoid excessive heat buildup during drilling
Hole Wall Preparation
- Swell removal and desmear with gentle permanganate etch
- Plasma etching optimizes adhesion while minimizing material loss
Metallization
- Direct metallization processes work best
- Allow sufficient dwell time for completeness of coverage
- 50-80 microinches of copper in holes balances thickness and conductivity
Solder mask
- Liquid photoimageable solder mask preferred for adhesion and resolution
- Ensure solder mask process is compatible with Rogers materials
Legend printing
- Use reverse printed and cured legend whenever possible
- Allow inks to fully cure to avoid smearing or contamination
Careful process control at each fabrication step helps maximize the electrical and mechanical capabilities of Rogers rigid flex materials.
Rogers RO4350B Rigid Flex PCBs – FAQs
Here are answers to some frequently asked questions about Rogers RO4350B rigid flex PCBs:
What are the key benefits of Rogers RO4350B rigid flex circuits?
The consistent electrical properties, excellent passive integration, robust adhesion, and high temperature durability of RO4350B make it an ideal choice for high frequency rigid flex PCBs where reliability is critical.
What types of constructions can be created with RO4350B?
Rogers RO4350B supports single layer flex circuits, multilayer rigid-flex with rigid and flex sections, and rigidized flex where rigid laminates are added to flexible circuits.
What thickness of RO4350B laminate is typically used?
Common RO4350B rigid flex laminate thicknesses range from 25 μm (1 mil) for the thinnest flex sections up to 200 μm (8 mils) for the rigid boards. Thicker rigid sections are possible too.
What are some key lamination guidelines for RO4350B?
Use slow heat ramp rates of 3-5°C/min with at least 180°C (360°F) temperature and adequate pressure. Allow sufficient resin flow time for filling plated through holes.
How are circuits protected during legend printing and soldering?
Use liquid photoimageable solder mask and cured legend ink for protection. Avoid smearing inks during assembly. Use recommended soldering profiles.
What applications are Rogers RO4350B rigid flex PCBs well suited for?
Aerospace, defense, communications, automotive, medical, and consumer electronics leverage the high frequency capabilities, flexibility, and ruggedness of RO4350B.