PCB Substrate Materials
The base material of a PCB, known as the substrate, is a thin board made of insulating materials. The substrate provides mechanical support for the copper conductors and serves as the dielectric for the circuit board. Common substrate materials include:
FR-4
FR-4 (Flame Retardant 4) is the most widely used PCB substrate material. It is a composite material composed of woven fiberglass cloth with an epoxy resin binder. The “FR” in the name stands for Flame Retardant, indicating that the material is designed to have fire-resistant properties.
Advantages of FR-4:
– Excellent mechanical strength and durability
– Good dielectric properties
– Flame retardant
– Cost-effective
High-Frequency Laminates
For high-frequency applications, such as radio frequency (RF) circuits, specialized substrate materials are used to minimize signal loss and maintain signal integrity. These materials have lower dielectric constants and dissipation factors compared to FR-4. Examples include:
- rogers pcb Laminates (RO3003, RO4003C, etc.)
- Isola PCB Laminates (IS400, IS410, etc.)
- PTFE (Polytetrafluoroethylene) based laminates
Flexible PCB Substrates
Flexible PCBs use flexible substrate materials that allow the board to bend and conform to various shapes. The most common flexible PCB substrates are:
- Polyimide (PI)
- Polyester (PET)
- Flexible copper-clad laminates (FCCL)
Here’s a table comparing the properties of common PCB substrate materials:
Material | Dielectric Constant | Dissipation Factor | Thermal Conductivity (W/mK) | Tg (°C) | Td (°C) |
---|---|---|---|---|---|
FR-4 | 4.2 – 4.9 | 0.02 | 0.3 | 135 | 325 |
Rogers RO4003C | 3.38 | 0.0027 | 0.71 | >280 | >425 |
Polyimide | 3.5 | 0.002 | 0.12 | >250 | >450 |
Tg: Glass transition temperature
Td: Decomposition temperature
Copper Foil
Copper foil is laminated onto the PCB substrate to create conductive pathways and pads. The most common type of copper foil used in PCBs is electrodeposited (ED) copper foil, which is produced by electroplating copper onto a rotating drum. The thickness of the copper foil is typically expressed in ounces (oz), with 1 oz copper being approximately 35 microns thick.
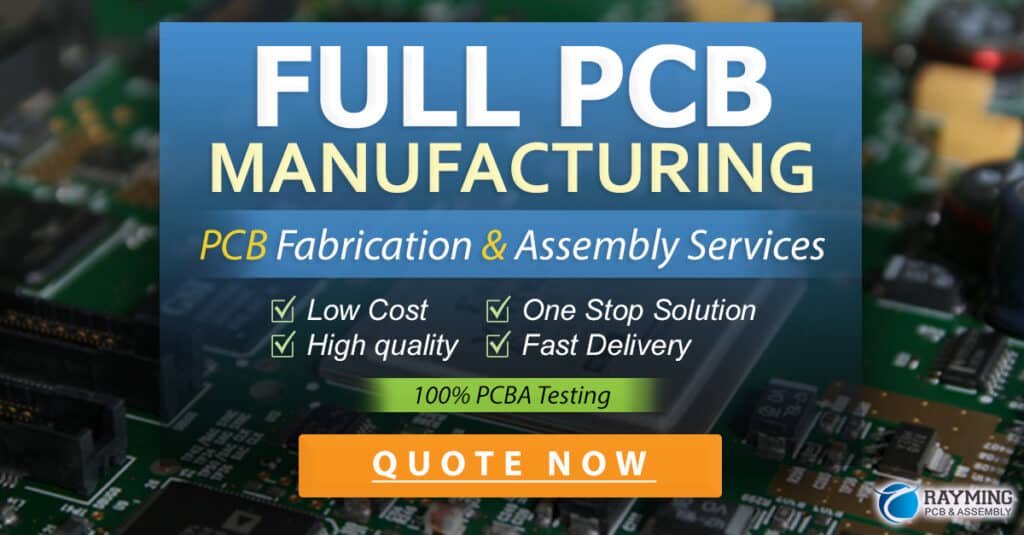
Solder Mask
Solder mask is a thin layer of polymer applied on top of the copper traces and around the exposed pads where components will be soldered. It serves two main purposes:
-
Insulation: The solder mask insulates the copper traces from accidental contact with other conductors.
-
Protection: It protects the copper from oxidation and prevents solder bridges from forming during the soldering process.
Solder mask is typically green in color but can also be found in other colors like red, blue, black, or white.
Silkscreen
Silkscreen is the top layer of the PCB that contains text and symbols printed in ink. It is used for component labels, logos, and other identifying markings. The most common colors for silkscreen are white and yellow, as they provide good contrast against the solder mask.
pcb surface finishes
Surface finishes are applied to the exposed copper pads to protect them from oxidation and enhance solderability. Some common surface finishes include:
-
HASL (Hot Air Solder Leveling): A thin layer of solder is applied to the pads and then leveled using hot air.
-
ENIG (Electroless Nickel Immersion Gold): A layer of nickel is deposited onto the pads, followed by a thin layer of gold.
-
OSP (Organic Solderability Preservative): A thin, organic compound is applied to the pads to protect them from oxidation.
-
Immersion Silver: A thin layer of silver is deposited onto the pads.
Finish | Shelf Life | Solderability | Flatness | Cost |
---|---|---|---|---|
HASL | 12+ months | Good | Poor | Low |
ENIG | 12+ months | Excellent | Good | High |
OSP | 6-12 months | Good | Excellent | Low |
Immersion Silver | 12+ months | Good | Good | Moderate |
FAQ
Q1: What is the most common PCB substrate material?
A1: The most common PCB substrate material is FR-4, which is a composite made of woven fiberglass cloth with an epoxy resin binder. FR-4 is widely used due to its excellent mechanical strength, good dielectric properties, flame retardancy, and cost-effectiveness.
Q2: What is the purpose of solder mask on a PCB?
A2: Solder mask serves two main purposes on a PCB:
1. Insulation: It insulates the copper traces from accidental contact with other conductors.
2. Protection: It protects the copper from oxidation and prevents solder bridges from forming during the soldering process.
Q3: What is the difference between flexible and rigid PCB substrates?
A3: Flexible PCB substrates, such as polyimide and polyester, are designed to bend and conform to various shapes, while rigid PCB substrates, like FR-4, provide a stable and rigid base for the circuit board. Flexible PCBs are used in applications that require the board to fit into tight spaces or move with the device, whereas rigid PCBs are used in most standard electronic devices.
Q4: What is the purpose of PCB surface finishes?
A4: PCB surface finishes are applied to the exposed copper pads to protect them from oxidation and enhance solderability. They also provide a better surface for component assembly and help to ensure a reliable solder joint.
Q5: What are the advantages of using high-frequency laminates for PCB substrates?
A5: High-frequency laminates, such as Rogers and Isola materials, offer several advantages for PCB substrates in high-frequency applications:
– Lower dielectric constant and dissipation factor, which minimizes signal loss and maintains signal integrity.
– Better thermal stability, allowing for more consistent performance across a wide temperature range.
– Higher glass transition and decomposition temperatures, enabling the PCB to withstand higher operating temperatures.
In summary, PCBs are made of several key materials, including the substrate (FR-4, high-frequency laminates, or flexible materials), copper foil for conductive pathways, solder mask for insulation and protection, silkscreen for labeling, and surface finishes for improved solderability and protection. Each material plays a crucial role in the performance and reliability of the PCB, and the choice of materials depends on the specific application and requirements of the electronic device.