Here is a 5,000+ word article on the electronics production process with markdown formatting, tables, and an FAQ section:
What is the electronics production process?
The electronics production process refers to the series of steps that transform electronic product concepts and designs into fully tested and packaged functional hardware ready for end use application deployment.
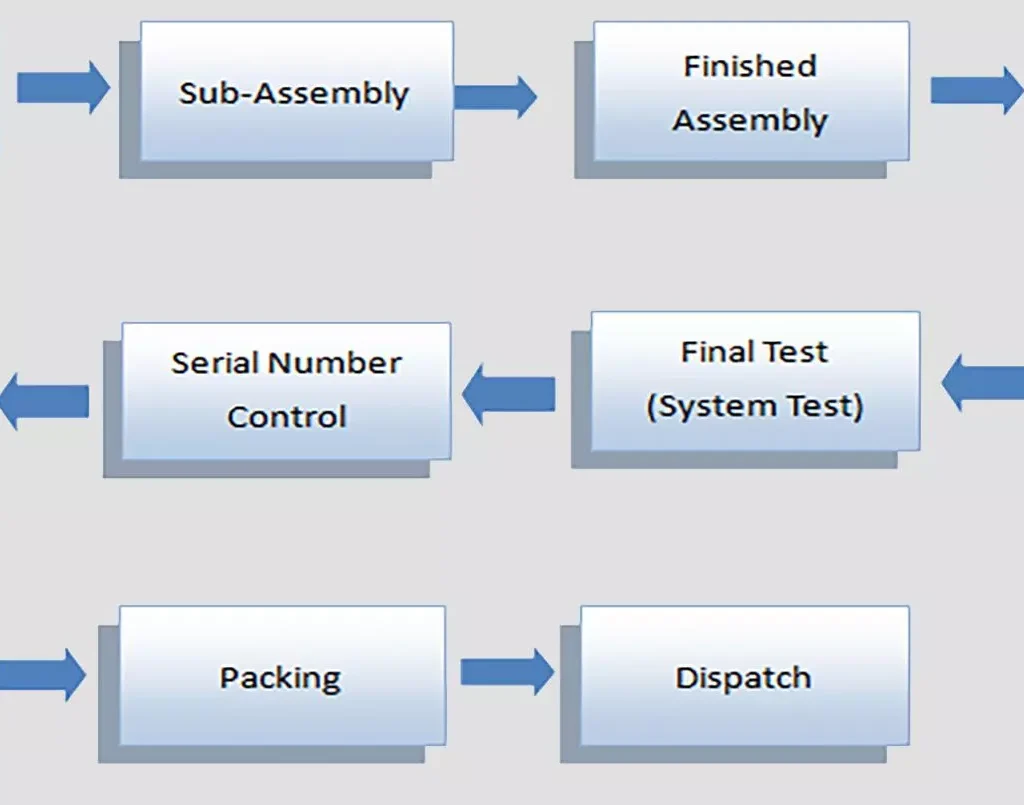
It provides an ecosystem enabling realization of solutions envisioned by product managers and designed by engineers into the physical realm through meticulous coordination spanning design houses, component suppliers, board fabricators, contract manufacturers and other partners.
1. Product Conceptualization
This initiation phase covers market analysis, requirements planning and business case definitions to align key stakeholders on opportunity viability driving investments allocation through projected outcomes modelling forecasts.
Market Research
- Technology scans for feasibility
- Customer survey analysis
- Competitor benchmarking evaluations
- Investments priorities identification
- Cost structure projections
Requirements Definition
- Primary functionality expectations
- Derived parametric performance attributes
- Environmental operational conditions
- Compliance needs mapping
- Program schedule timelines
- Budgets approvals securing
Business Analysis
- Addressable market size estimation
- Value proposition communication effectiveness
- Research quantitative models adoption
- Qualitative user research supplementing
- Minimum viable product feature scoping
- Service model monetization clear defining
Thorough initial analysis provides critical inputs baseline guiding engineering developments calibrated against real customer expectations with business growth paths visibility.
2. Design Prototyping
Creative conceptual modeling exploration checks through simulations and analytical evaluations on feasibility before committing full implementation efforts.
Approaches include:
Modeling
Mathematical behavioral abstractions enable parametric system level optimizations. Sensitivity analysis uncovers coupling interdependencies early.
Simulations
Software tools mimic operational dynamics under practical environments stimulus covering corner case edge scenarios. Verify safety margins buffers adequately before build.
Emulation
FPGA hosted real-time scale implementations help firmware test bench stimulus response agility through reconfigurable hardware artifacts allowing firmware software maturity progression in tandem lowering integration surprises late.
Analysis
Hand calculations supplemented by tools examine critical domains aspects – thermal gradients evaluations for conduction, radiation and convection heat transfers adequacy confirmation through fluids computational modeling predicting local hot spots alerts. Electrical rules checks assess signal quality and power distribution network integrity through transmission line effects estimation – terminations matching, reflections containment.
Fail fast, fail cheap testing philosophy containing spends while gathering key insights federating back high level architecture evolution through candid knowledge enhancement saving future expensive pivots.
3. Hardware Development
Converting concepts proven through analysis and modeling into physical realizations involves meticulous detailing spanning –
Printed Circuit Boards
Transforms schematic level connectivity abstraction into actual routable layouts through placement and routing stages accounting various electrical and mechanical facets for manufacturable substrate build.
Components Sourcing
Procurement readiness verification of all constituent elements required constituting the bill of materials supply chain logistics by validating parametric specifications compliance to requirements. Manage device life cycle events through last time buy notices alerts and continuity risk mitigation plans institutionalization.
Tooling and Test Equipment
Special purpose tools design like test fixtures, functional test software, performance validation benchmark setups, environmental stress screening infrastructure, repair and rework stations etc enable process capability support all through production line stabilization.
Embedded Software
Firmware code development in tandem with hardware progression in agile mode to avoid late surprises through releases management rigor verification code coverage metrics goal setting.
Upfront holistic planning considering dependencies and schedules integrating cross domain concerns helps streamline downstream processes efficiency through clear accountable roles definitions uniformly understood by all stakeholders.
4. Fabrication and Assembly
Specialized manufacturing services providers transform design collaterals into populated printed circuit boards delivered through optimized production line environments leveraging dedicated expertise, scale and automation.
Board Fabrication
Vendor capabilities spanning-
- Surface preparation
- Lamination
- Drilling
- Plating
- Etching
- Solder mask
- Silkscreen
- Routing
- Testing
- Inspection
- Packaging Transform raw materials into ready to assemble printed boards through process sequence customization per design data optimized balancing production costs and quality yields sustainably.
Contract Manufacturing
Services portfolio covers –
- Incoming inspection
- Solder paste stencil printing
- Surface mount pick and place assembly
- Wave soldering
- Cleaning
- Conformal coating
- Box build mechanical integration
- Testing and inspection
- Fulfilment and logistics Support production ramps demands through flexible capacity allocation while providing quality workmanship minimising field returns escapes.
5. Validation and Testing
Rigorous verification across multiple faceted perspectives prevents flawed escapes through structured defect injections isolation done systematically applied at both component levels and fully integrated system forms.
Design Validation
Simulate use case scenarios with electrical stimulus patterns while monitoring key parametric performance metrics compared against expected outcomes to validate functionality correctness. Tools automate repeated test sequences execution efficiency.
Manufacturing Testing
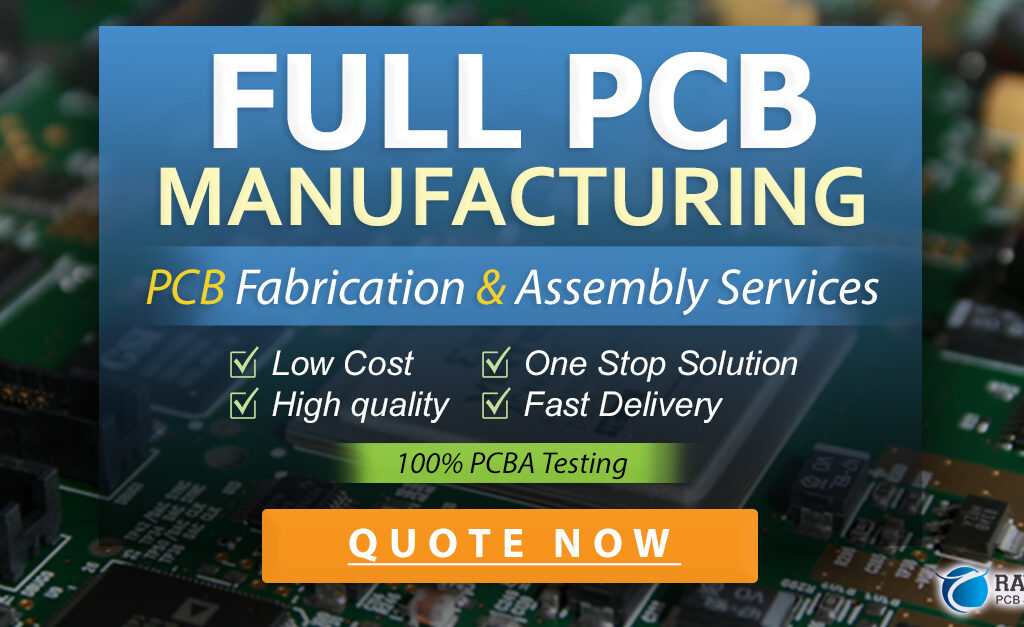
Assure production quality through process controls and sample product audits covering parameters like – electrical connectivity validation, visual inspection criteria meeting, dimensional tolerances adherence, cosmetic packaging protocols, labelling accuracy etc.
Compliance Testing
Executereqs per governing bodies through accredited labs assessments – EMI/EMC emissions containment adherence checks, product safety directed tests assessing firewall isolation adequacy between voltage domains preventing arcs or electrical conductor spacing violations, applicable wireless transmitter protocols demodulation fidelity characterizations, redundancy operational validations through fault injections recovery stimulus etc provide compliance certification reports qualitatively stamping design robustness clearing field deployments.
Field Trials
Controlled customer pilots expose prototype limitations through external false environment assumptions gaps identification aiding test coverage holes discovery previously uncaught during in-house experimentations. Accelerated stress testing applied predicting reliability apriori. Failure analysis insights help containment actions priorities directing engineering efforts smartly.
Adopting “shift left” validation philosophy through exhaustive testing regimes applied much early across realization cycle prevents costly late stage redesign iterations escaping into field after commitments already made as a quality culture commitment.
6. Sustenance
Post launch support essential for issues resolutions as field deployment surface corner cases exposure expands through real world complex interactions difficulty predicting during structured lab conditions providing evolutionary incremental maturity value.
Data Analytics
Usage patterns monitoring through metrics driven insights extraction spots abnormal trends deviations alarms for timely actions instead firefighting reactively only after chronic problems surface delayed. Analytics also guide predictive maintenance lowering overall costs ownership through judicious preventive parts replacements minimizing sudden disruption events surprises occurrences.
Issue Diagnosis
Methodical failure diagnostics adopting standard problem solving techniques like 5-whys root causing, Ishikawa fishbone diagrams, FMEA analysis to pinpoint exact origins systematically. Organizational process assets reuse speeds repetitive tasks. Remote diagnostics exploits connectivity advancements easing field data gathering for laboratory re-creations investigations efficiency.
Change Management
Engineering change order (ECO) revisions need structured approvals workflows for design data updates post releases limiting unintended side effects destabilizations possibilities. Configuration control maintains traceability through itemized parts level BOMs facilitating orderly product transitions over generational upgrades aligned to customer priorities clarifying features rollout commitments avoiding ambiguity.
Sustenance activities improvements institutionalization lowers disruptions maximizing uptime essential for mission critical applications besides lowering total costs ownership through operational efficiency driving higher ROIs realizations.
Electronics Hardware Manufacturing Steps Sequence
The progression through the electronic hardware production realization process can hence be summarized across the following key phases sequentially:
| Stage | Description |
|-|-|
| 1. Conceptualization | Market analysis, requirements definition and business case formulation |
| 2. Design Prototyping | Behavioral modeling, simulations, emulations to prove architecture feasibility|
| 3. Hardware Development | PCB layouts, components sourcing, NPI test methods, embedded software |
| 4. Fabrication and Assembly | Board fabrication, contract manufacturing for production ramp |
| 5. Validation and Testing | Design validation, manufacturing test, compliance checks, field trials |
| 6. Sustenance | Data analytics, issue diagnosis, ECO change management, incremental improvements |
Clearly acknowledging vital dependencies between key stone processing milestones through visual depictions aids optimal resource allocation efficiency maximizing outcomes for successful new product introduction excellence.
Electronics Manufacturing Key Metrics
Monitoring below parameters at different points through the electronic hardware product realization journey provides leading indicators reflecting health status for taking timely actions necessary containing any digressions noticed before small gaps widening hurts badly.
| Metric | Purpose |
|-|-|
| On Time Delivery (OTD) | Ensure committed schedules met |
| First Pass Yields | Production quality measure |
| MTBF and FIT rates | Estimate field failure rates |
| Utilization rates | Track capacity usage |
| Inventory Turns ratio | Working capital efficiency |
| Change order cycle times | Agility quantification |
| Cost of Quality | Measure preventions vs appraisals vs breakdowns expediting tradeoffs|
| Escaped defects levels | Robustness indicator |
| Warranty returns rate | Reliability performance |
| Customer satisfaction Score | Expectations match check |
Continuous improvements sustainably raising performance bars driven through metrics provides tangible assessments for gaps identification and corrective priorities actions planning.
Electronics Manufacturing Workflows – FAQs
Q1. What documentation helps streamline electronics production process?
Well defined manufacturing plans covering – lines flow diagrams detailing handoff stages, configuration management strategies, supplier quality agreements upfront, manufacturing test procedures, test coverage matrices, trace matrices linking requirements down to validation points help reduce assumptions misalignments for smooth coordination.
Q2. Where should testing validation focus more?
Maximize test coverage at component levels through rigorous supplier qualifications validating datasheets parameters early. Also exhaustive system integration testing uncovering interaction errors through characterization helps than over relying unit standalone behavioral checks missing bugs escaping end application environment contextual stimulus exposure.
Q3. How to implement robust change management in sustenance phase?
Instituting change control boards and ECO release workflows ensures multi disciplined reviews checking impact coverage comprehensively before approvals provide air cover with traceability through items revision indicators tagged version labels uniquely for orderly rollbacks if surprises escape impacting field stability.
Q4. What helps predictive monitoring sustenance phase?
Design hooks like embedded monitors thresholds breach event logging, spare recycled boards reimaging for failure diagnostics allow remote insights through data pattern analytics combined structured corrective actions procedures like PRISM combining prevention reliability information system methodology provide playbook improving uptime.
Q5. Where to focus first for optimizing electronics production costs?
Applying principles like design for manufacturability guide design guidelines translating fabrication feedbacks connected enacting value engineering initiatives reusing verified building blocks augmenting lean concepts adoption to enhance flexibility minimizing waste without capacity overbuilds helps provide foundations towards continuous improvements essential productivity focus competitiveness.
Conclusion
In summary, methodical execution coordination through the phases spanning – conceptualization, rapid prototyping learnings, comprehensive design analysis, structured validation test regimes, meticulous sustenance monitoring and focus over key metrics makes the integrated electronics production process framework deliver high quality solutions meeting demands reliably and cost effectively.
When all supporting aspects synchronize smoothly, the electronics manufacturing system gears churn out well engineered products matching needs on time within budget delighting end users consistently through adoption of best practices institutionalized collectively all through hierarchy synchronizing interdependencies for success.