Introduction to PCB Stiffeners
A printed circuit board (PCB) stiffener, also known as a PCB stiffening bracket or PCB support, is a mechanical component used to provide additional rigidity and support to a PCB. PCB stiffeners are commonly used in applications where the PCB is subjected to vibration, shock, or other mechanical stresses that could cause the board to flex or bend, potentially leading to component damage or failure.
PCB stiffeners are typically made from materials such as aluminum, steel, or plastic, and are designed to be attached to the PCB using screws, rivets, or adhesives. They come in various shapes and sizes to accommodate different PCB designs and can be customized to meet specific requirements.
Why Use PCB Stiffeners?
There are several reasons why PCB stiffeners are used in electronic assemblies:
-
Preventing PCB Flexing: PCBs can flex or bend due to various factors, such as vibration, shock, or thermal expansion. This flexing can cause components to become damaged or dislodged, leading to circuit failures. PCB stiffeners help prevent this flexing by providing additional support and rigidity to the board.
-
Improving Reliability: By reducing the risk of component damage or failure due to PCB flexing, stiffeners help improve the overall reliability of the electronic assembly. This is particularly important in applications where reliability is critical, such as in aerospace, military, or medical devices.
-
Enhancing Mechanical Strength: PCB stiffeners can also enhance the mechanical strength of the PCB, making it more resistant to physical damage. This is especially useful in applications where the PCB may be subjected to rough handling or extreme environmental conditions.
-
Enabling Larger PCBs: As PCB designs become more complex and feature-rich, they often require larger board sizes. However, larger PCBs are more susceptible to flexing and warping. PCB stiffeners enable the use of larger PCBs by providing the necessary support to maintain the board’s structural integrity.
-
Facilitating Mounting: In some cases, PCB stiffeners can also serve as mounting points for the PCB, allowing it to be securely attached to the enclosure or chassis. This can simplify the overall assembly process and improve the mechanical stability of the final product.
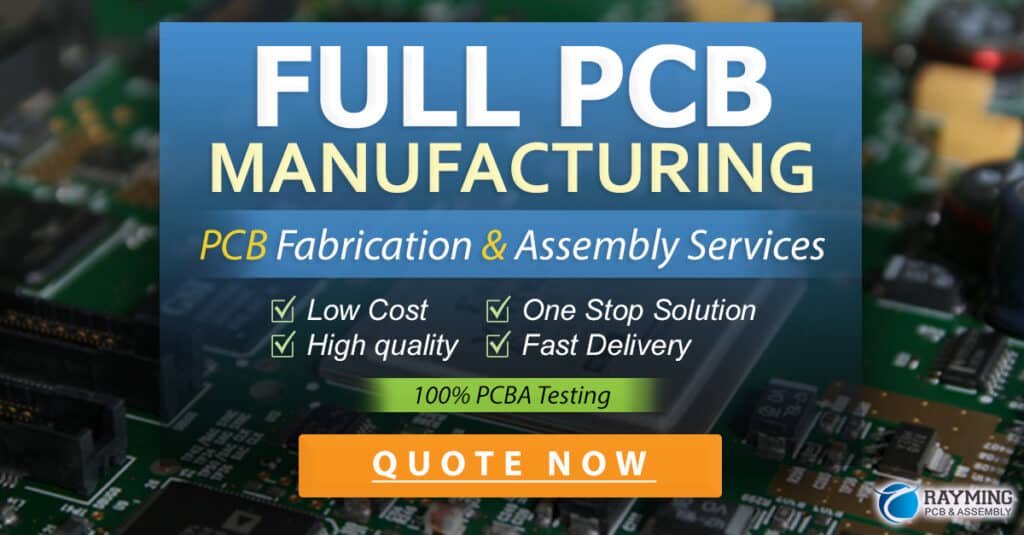
Types of PCB Stiffeners
PCB stiffeners come in various types, each with its own advantages and applications. Some common types include:
-
Flat Bar Stiffeners: These are simple, flat pieces of metal or plastic that are attached to the PCB to provide additional rigidity. They are often used in applications where the PCB is subjected to moderate levels of stress.
-
L-Shaped Stiffeners: L-shaped stiffeners are designed to provide support along two edges of the PCB, forming an “L” shape. They are commonly used in applications where the PCB is mounted vertically and requires support along both the top and bottom edges.
-
U-Shaped Stiffeners: U-shaped stiffeners, also known as channel stiffeners, are designed to provide support along three edges of the PCB, forming a “U” shape. They offer a higher level of rigidity compared to flat bar or L-shaped stiffeners and are often used in applications where the PCB is subjected to high levels of stress.
-
Custom Stiffeners: In some cases, custom stiffeners may be designed to meet specific requirements or to fit unique PCB shapes. These stiffeners can be manufactured using various materials and fabrication techniques, such as machining, stamping, or 3D printing.
Here is a table comparing the different types of PCB stiffeners:
Type | Description | Advantages | Applications |
---|---|---|---|
Flat Bar | Simple, flat piece of metal or plastic | Low cost, easy to install | Moderate stress levels |
L-Shaped | Provides support along two edges of the PCB | Suitable for vertically mounted PCBs | Moderate to high stress levels |
U-Shaped | Provides support along three edges of the PCB | High level of rigidity | High stress levels |
Custom | Designed to meet specific requirements or fit unique PCB shapes | Tailored to specific needs | Unique or demanding applications |
Materials Used for PCB Stiffeners
PCB stiffeners can be manufactured from a variety of materials, each with its own properties and advantages. The choice of material depends on factors such as the application, environmental conditions, and cost. Some common materials used for PCB stiffeners include:
-
Aluminum: Aluminum is a popular choice for PCB stiffeners due to its low cost, lightweight, and good thermal conductivity. It is easy to machine and can be anodized for improved corrosion resistance.
-
Stainless Steel: Stainless steel stiffeners offer high strength and excellent corrosion resistance. They are often used in applications where the PCB is subjected to harsh environmental conditions or high levels of stress.
-
Cold Rolled Steel: Cold rolled steel is another cost-effective option for PCB stiffeners. It offers good strength and can be easily machined or stamped into various shapes.
-
Plastic: Plastic stiffeners, such as those made from polyethylene terephthalate (PET) or polycarbonate (PC), are lightweight and provide good electrical insulation. They are often used in applications where electrical isolation is required between the PCB and the stiffener.
-
Fiberglass: Fiberglass stiffeners, also known as FR-4 stiffeners, are made from the same material as the PCB substrate. They offer excellent dimensional stability and a coefficient of thermal expansion (CTE) that closely matches that of the PCB, minimizing stress due to thermal changes.
Here is a table comparing the properties of different materials used for PCB stiffeners:
Material | Strength | Weight | Thermal Conductivity | Corrosion Resistance | Cost |
---|---|---|---|---|---|
Aluminum | Medium | Low | High | Medium | Low |
Stainless Steel | High | High | Low | High | High |
Cold Rolled Steel | Medium | High | Medium | Low | Low |
Plastic | Low | Low | Low | High | Medium |
Fiberglass | Medium | Medium | Low | High | Medium |
Designing with PCB Stiffeners
When designing a PCB assembly that includes stiffeners, there are several factors to consider to ensure optimal performance and reliability:
-
Stiffener Placement: The placement of the stiffener on the PCB is crucial for effectively reducing flexing and improving mechanical stability. Stiffeners should be positioned in areas where the PCB is most susceptible to bending, such as near connectors, heavy components, or unsupported edges.
-
Attachment Methods: PCB stiffeners can be attached to the board using various methods, such as screws, rivets, or adhesives. The choice of attachment method depends on factors such as the size and weight of the stiffener, the available space on the PCB, and the required level of mechanical strength.
-
Thermal Considerations: When using metal stiffeners, it is important to consider the thermal impact on the PCB. Metal stiffeners can act as heat sinks, drawing heat away from the PCB and potentially affecting the temperature distribution across the board. In some cases, thermal interface materials may be used to improve heat transfer between the PCB and the stiffener.
-
Electrical Isolation: If electrical isolation is required between the PCB and the stiffener, designers must ensure that appropriate insulation materials or coatings are used. This is particularly important when using metal stiffeners, as they can create unwanted electrical paths if not properly isolated.
-
Manufacturing Considerations: The design of the PCB stiffener should also take into account manufacturing considerations, such as the ease of assembly, the required tolerances, and the compatibility with the chosen fabrication processes. Designers should work closely with the manufacturing team to ensure that the stiffener design can be efficiently and reliably produced.
Installing PCB Stiffeners
The installation process for PCB stiffeners varies depending on the type of stiffener and the chosen attachment method. However, there are some general steps that are common to most installations:
-
Preparing the PCB: Before installing the stiffener, the PCB should be cleaned and any necessary markings or alignment features should be added. This may include drilling holes for screws or rivets, or applying adhesive to the designated mounting areas.
-
Aligning the Stiffener: The stiffener should be carefully aligned with the PCB, ensuring that it is positioned correctly and that any mounting holes or features are properly aligned. This step is critical for ensuring a secure and stable attachment.
-
Securing the Stiffener: Once the stiffener is aligned, it can be secured to the PCB using the chosen attachment method. For screw or rivet attachments, the fasteners should be tightened to the appropriate torque to ensure a strong and reliable connection. If using adhesives, the adhesive should be applied evenly and allowed to cure according to the manufacturer’s instructions.
-
Inspecting the Installation: After the stiffener is installed, the assembly should be inspected to ensure that the stiffener is securely attached and that there are no signs of damage or misalignment. Any issues should be addressed before the assembly is put into service.
PCB Stiffener Materials
As previously mentioned, PCB stiffeners can be made from various materials, each with its own advantages and disadvantages. Here, we will take a closer look at some of the most common materials used for PCB stiffeners:
Aluminum
Aluminum is one of the most popular materials for PCB stiffeners due to its combination of low cost, lightweight, and good thermal conductivity. Some key advantages of aluminum stiffeners include:
- Excellent thermal dissipation properties, helping to distribute heat evenly across the PCB
- Easy to machine and fabricate into various shapes and sizes
- Can be anodized for improved corrosion resistance and electrical insulation
- Readily available and cost-effective compared to other materials
However, aluminum stiffeners also have some limitations:
- Lower strength compared to materials like stainless steel, which may be a concern in high-stress applications
- Can be prone to oxidation and corrosion if not properly protected
- May require additional insulation or coatings for electrical isolation
Stainless Steel
Stainless steel is another common material for PCB stiffeners, particularly in applications where high strength and corrosion resistance are required. Some advantages of stainless steel stiffeners include:
- Excellent mechanical strength and rigidity, making them suitable for high-stress environments
- High corrosion resistance, even in harsh conditions
- Can be fabricated into various shapes and sizes
- Provides good EMI/RFI shielding properties
However, stainless steel stiffeners also have some drawbacks:
- Higher cost compared to aluminum or cold rolled steel
- Higher weight, which may be a concern in weight-sensitive applications
- Lower thermal conductivity compared to aluminum, which may impact heat dissipation
Cold Rolled Steel
Cold rolled steel is a cost-effective alternative to stainless steel for PCB stiffeners. It offers a good balance of strength and affordability, making it a popular choice in many applications. Some advantages of cold rolled steel stiffeners include:
- Good mechanical strength and rigidity
- Easy to machine and fabricate into various shapes and sizes
- Lower cost compared to stainless steel
- Can be plated or coated for improved corrosion resistance
However, cold rolled steel stiffeners also have some limitations:
- Lower corrosion resistance compared to stainless steel, particularly in harsh environments
- May require additional coatings or treatments for electrical isolation
- Higher weight compared to aluminum
Plastic
Plastic stiffeners, such as those made from PET or PC, offer a lightweight and electrically insulating alternative to metal stiffeners. Some advantages of plastic stiffeners include:
- Excellent electrical insulation properties
- Lightweight and easy to handle
- Good chemical resistance and durability
- Can be molded into various shapes and sizes
However, plastic stiffeners also have some drawbacks:
- Lower mechanical strength and rigidity compared to metal stiffeners
- May be susceptible to creep and deformation under high stress or temperature
- Limited thermal conductivity, which may impact heat dissipation
Fiberglass
Fiberglass, or FR-4, stiffeners are made from the same material as the PCB substrate, offering a unique set of advantages. Some benefits of fiberglass stiffeners include:
- Excellent dimensional stability and CTE matching with the PCB
- Good electrical insulation properties
- Lightweight and easy to fabricate
- Good mechanical strength and rigidity
However, fiberglass stiffeners also have some limitations:
- Higher cost compared to some metal stiffeners
- Limited thermal conductivity, which may impact heat dissipation
- May be more brittle than metal stiffeners, requiring careful handling
Conclusion
PCB stiffeners play a crucial role in ensuring the mechanical stability, reliability, and longevity of electronic assemblies. By providing additional support and rigidity to the PCB, stiffeners help prevent flexing, warping, and component damage, ultimately improving the overall performance of the device.
When designing with PCB stiffeners, it is important to consider factors such as the type of stiffener, the material, the attachment method, and the specific requirements of the application. By carefully selecting the appropriate stiffener and properly integrating it into the PCB design, engineers can create robust and reliable electronic assemblies that can withstand the rigors of various operating environments.
As electronic devices continue to become more complex and compact, the use of PCB stiffeners will likely remain an essential aspect of PCB design and manufacturing. By staying up-to-date with the latest developments in stiffener materials, design techniques, and manufacturing processes, engineers can ensure that their products are well-equipped to meet the evolving demands of the electronics industry.
Frequently Asked Questions (FAQ)
-
What is the primary purpose of a PCB stiffener?
The primary purpose of a PCB stiffener is to provide additional mechanical support and rigidity to a printed circuit board, preventing it from flexing or bending due to vibration, shock, or other mechanical stresses. -
What are some common materials used for PCB stiffeners?
Common materials used for PCB stiffeners include aluminum, stainless steel, cold rolled steel, plastic (such as PET or PC), and fiberglass (FR-4). -
How are PCB stiffeners typically attached to the board?
PCB stiffeners can be attached to the board using various methods, such as screws, rivets, or adhesives, depending on the specific requirements of the application and the chosen stiffener material. -
What factors should be considered when selecting a PCB stiffener material?
When selecting a PCB stiffener material, engineers should consider factors such as the required mechanical strength, thermal conductivity, electrical insulation properties, corrosion resistance, weight, and cost. -
Can PCB stiffeners be customized to fit specific design requirements?
Yes, PCB stiffeners can be customized to meet specific design requirements, such as unique shapes or sizes, by using various manufacturing processes like machining, stamping, or 3D printing.