How PCB Milling Works
The PCB milling process involves several steps:
-
Design: The PCB design is created using electronic design automation (EDA) software, such as KiCad or Eagle. The design includes the circuit schematic, component placement, and routing of the copper traces.
-
Substrate Preparation: A substrate, typically a copper-clad fiberglass board (FR-4), is cut to the desired size and cleaned to remove any debris or contaminants.
-
Milling Machine Setup: The substrate is secured to the bed of the PCB milling machine, and the cutting tools are installed and calibrated.
-
Milling Process: The milling machine follows the PCB design file and removes unwanted copper from the substrate using the rotating cutting tools. The tools can include end mills, drill bits, and engraving bits, depending on the specific requirements of the design.
-
Cleaning and Inspection: After milling, the PCB is cleaned to remove any debris and inspected for defects or errors. If necessary, manual touch-ups can be made using a razor blade or other tools.
-
Component Placement and Soldering: The electronic components are placed on the PCB and soldered in place, either manually or using a pick-and-place machine and a reflow oven.
Advantages of PCB Milling
PCB milling offers several advantages over traditional PCB fabrication methods:
-
Rapid Prototyping: PCB milling allows for quick and easy creation of prototype boards, enabling faster iteration and testing of designs.
-
Customization: Milling machines can easily accommodate custom PCB shapes and sizes, as well as unique features like slots or cutouts.
-
In-house Fabrication: With a PCB milling machine, designers and engineers can fabricate boards in-house, reducing lead times and costs associated with outsourcing to external manufacturers.
-
Small-scale Production: PCB milling is well-suited for small-scale production runs, as it eliminates the need for expensive setup costs associated with traditional PCB fabrication methods.
-
Environmental Benefits: PCB milling does not require the use of harsh chemicals, such as those used in the etching process, making it a more environmentally friendly option.
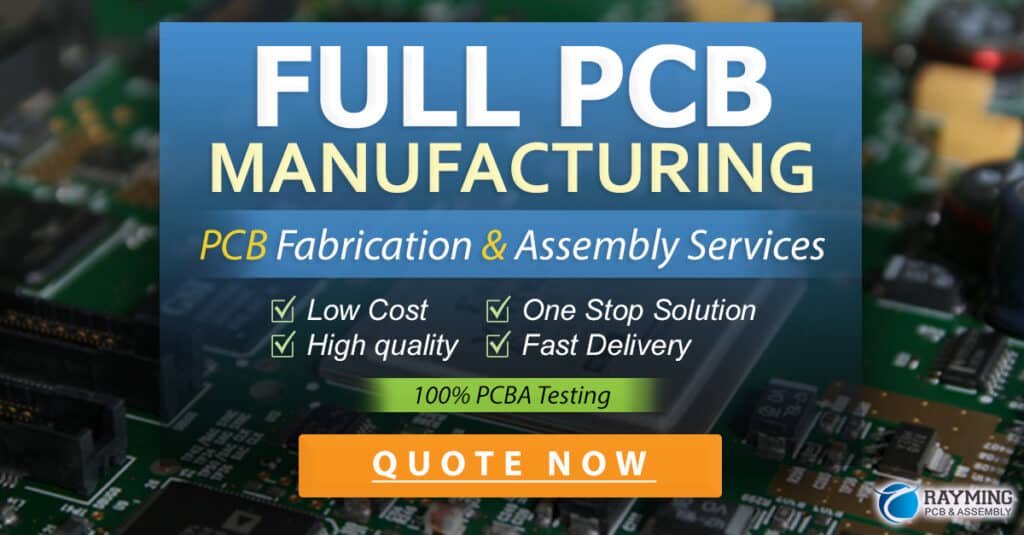
Disadvantages of PCB Milling
Despite its advantages, PCB milling also has some limitations:
-
Limited Trace Width and Spacing: Milling machines are limited by the size of the cutting tools, which can restrict the minimum trace width and spacing achievable compared to other fabrication methods.
-
Slower for Large-scale Production: While ideal for prototyping and small-scale production, PCB milling is slower than traditional methods for large-scale manufacturing.
-
Tool Wear: The cutting tools used in PCB milling are subject to wear and tear, which can affect the quality and precision of the milled traces over time.
-
Material Limitations: Some substrate materials, such as ceramic or metal-core PCBs, may be more difficult or impossible to mill due to their hardness or other properties.
PCB Milling Machines
There are several types of PCB milling machines available, ranging from desktop models for hobbyists and small businesses to large-scale industrial machines for high-volume production.
Machine Type | Typical Working Area | Spindle Speed (RPM) | Tool Change | Automatic Tool Calibration | Price Range |
---|---|---|---|---|---|
Desktop | 200 x 150 mm | 10,000 – 50,000 | Manual | No | $500 – $5,000 |
Benchtop | 500 x 400 mm | 20,000 – 60,000 | Automatic | Some models | $5,000 – $20,000 |
Industrial | 800 x 600 mm or larger | 50,000 – 100,000 | Automatic | Yes | $20,000 – $100,000+ |
Some popular PCB milling machines include:
- Bantam Tools Desktop PCB Milling Machine
- Othermill Pro
- Carbide 3D Nomad
- LPKF ProtoMat S series
- CNC Piranha FX
When choosing a PCB milling machine, consider factors such as working area, spindle speed, tool change capabilities, and automatic tool calibration, as well as your budget and the intended use of the machine.
Software for PCB Milling
To create PCB designs and generate the necessary files for milling, designers use electronic design automation (EDA) software. Some popular EDA software packages that support PCB milling include:
-
KiCad: A free and open-source EDA software suite that supports schematic capture, PCB layout, and generation of files for PCB milling.
-
Autodesk Eagle: A powerful EDA software package that offers schematic capture, PCB layout, and support for generating milling files. It is available in both free and paid versions.
-
Altium Designer: A high-end EDA software package used by professional PCB designers. It offers advanced features and supports the generation of files for PCB milling.
-
FlatCAM: An open-source software package specifically designed for generating PCB milling and drilling files from Gerber and Excellon files.
In addition to EDA software, some PCB milling machines come with their own proprietary software for importing designs and controlling the milling process.
Applications of PCB Milling
PCB milling is used in a variety of applications, including:
-
Prototyping: Milling is an ideal method for quickly creating prototype PCBs for testing and validation of new designs.
-
Education: Many educational institutions use PCB milling machines to teach students about PCB design and fabrication.
-
Hobby and DIY Projects: Hobbyists and makers use desktop PCB milling machines to create custom PCBs for their projects.
-
Small-scale Production: PCB milling is well-suited for small-scale production runs, particularly for custom or niche products.
-
Research and Development: R&D departments use PCB milling to quickly iterate and test new PCB designs before committing to large-scale production.
Conclusion
PCB milling is a versatile and accessible method for creating custom printed circuit boards. By removing unwanted copper from a substrate using a rotating cutting tool, PCB milling enables rapid prototyping, small-scale production, and in-house fabrication of PCBs. While it has some limitations compared to traditional PCB fabrication methods, the advantages of PCB milling make it an attractive option for many applications, from education and hobby projects to professional prototyping and small-scale manufacturing.
Frequently Asked Questions (FAQ)
-
What is the difference between PCB milling and PCB etching?
PCB milling removes unwanted copper from a substrate using a rotating cutting tool, while PCB etching uses chemical processes to remove the unwanted copper. Milling is better suited for rapid prototyping and small-scale production, while etching is more commonly used for large-scale manufacturing. -
Can I use any material for the substrate in PCB milling?
The most common substrate material for PCB milling is copper-clad fiberglass (FR-4). However, other materials like aluminum, brass, or polycarbonate can also be used, depending on the specific requirements of the project and the capabilities of the milling machine. -
How small can the traces be when using PCB milling?
The minimum trace width and spacing achievable with PCB milling depends on the specific milling machine and the cutting tools used. Generally, desktop milling machines can achieve trace widths and spacing down to around 0.1 mm (4 mil), while high-end industrial machines can produce even smaller features. -
What is the typical cost of a PCB milling machine?
The cost of a PCB milling machine varies depending on the type and capabilities of the machine. Desktop models for hobbyists and small businesses can range from $500 to $5,000, while industrial machines for high-volume production can cost $20,000 to $100,000 or more. -
Do I need special skills or training to operate a PCB milling machine?
Operating a PCB milling machine requires some basic knowledge of PCB design, milling processes, and the specific software and hardware used. Most manufacturers provide user manuals, tutorials, and support to help users get started. However, for more advanced applications or high-volume production, specialized training or experience may be necessary to ensure optimal results and maintain the machine.