Why is PCB Layout Important?
A well-designed PCB layout is essential for several reasons:
-
Functionality: The primary goal of PCB layout is to ensure that the circuit functions as intended. Proper component placement and routing are necessary to minimize signal integrity issues, EMI/EMC problems, and thermal challenges.
-
Manufacturability: A PCB layout must adhere to manufacturing constraints and design rules to ensure that it can be fabricated reliably and cost-effectively. This includes considerations such as minimum trace width, clearance, and hole size.
-
Reliability: A good PCB layout contributes to the long-term reliability of the circuit. Proper grounding, power distribution, and thermal management techniques can prevent issues like ground loops, voltage drops, and overheating.
-
Cost: An optimized PCB layout can help minimize manufacturing costs by reducing the board size, layer count, and complexity. It also helps avoid costly design revisions and production delays.
PCB Layout Process
The PCB layout process typically involves the following steps:
-
Schematic Review: Before starting the layout, it’s crucial to review the schematic for completeness, accuracy, and adherence to design guidelines.
-
Component Placement: Components are placed on the board based on their functional relationships, signal flow, and mechanical constraints. Critical components like connectors, power regulators, and sensitive analog parts are placed first.
-
Routing: The connections between components are established using copper traces. The routing process follows a hierarchy, with critical signals like power, ground, and high-speed lines routed first.
-
Design Rule Check (DRC): The layout is checked against a set of design rules to ensure that it meets manufacturing constraints and electrical requirements. This includes checks for minimum trace width, spacing, and hole size.
-
Output Generation: Once the layout is finalized and verified, output files like Gerber, drill, and assembly files are generated for manufacturing.
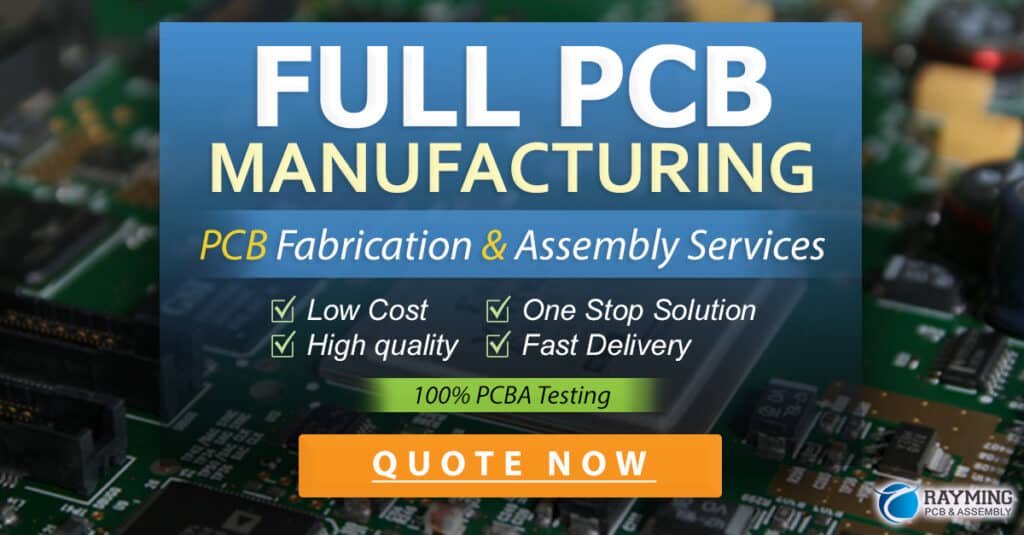
PCB Layout Considerations
Several factors must be considered during PCB layout to ensure a robust and manufacturable design:
Signal Integrity
Signal integrity refers to the ability of a signal to maintain its intended characteristics as it propagates through the circuit. Key signal integrity considerations in PCB layout include:
-
Impedance Control: Maintaining consistent impedance along a trace is crucial for high-speed signals. This is achieved through proper trace width and spacing.
-
Crosstalk: Crosstalk occurs when signals from one trace interfere with another. It can be minimized by adequate spacing between traces and the use of guard traces.
-
Reflections: Signal reflections occur when there are impedance mismatches along a trace. They can be minimized by proper termination and avoiding sharp bends in traces.
Power Integrity
Power integrity ensures that all components receive a clean and stable power supply. Key power integrity considerations include:
-
Power Distribution Network (PDN): A well-designed PDN is crucial for maintaining a low-impedance power supply. It includes proper placement of power and ground planes, decoupling capacitors, and power regulators.
-
Decoupling: Decoupling capacitors are placed close to ICs to provide a local, low-impedance power source and filter out high-frequency noise.
-
Ground Planes: Ground planes provide a low-impedance return path for signals and help minimize ground loops and EMI.
Thermal Management
Thermal management ensures that components operate within their specified temperature range. Key thermal considerations include:
-
Component Placement: Heat-generating components like power regulators and high-speed ICs should be placed away from temperature-sensitive components.
-
Copper Pours: Copper pours on the top and bottom layers can help dissipate heat from components.
-
Thermal Vias: Thermal vias are used to transfer heat from components to the inner layers or the opposite side of the board.
EMI/EMC
Electromagnetic compatibility (EMC) ensures that the PCB does not interfere with other electronic devices and is not susceptible to interference. Key EMI/EMC considerations include:
-
Grounding: Proper grounding techniques like star grounding and the use of ground planes can help minimize EMI.
-
Shielding: Sensitive components can be shielded using metal cans or conductive coatings to reduce EMI.
-
Filtering: Input/output filtering can be used to suppress high-frequency noise and prevent EMI.
PCB Layout Tools
There are several software tools available for PCB layout, ranging from simple 2D drafting programs to advanced 3D CAD systems. Some popular PCB layout tools include:
Tool | Vendor | Description |
---|---|---|
Altium Designer | Altium | A comprehensive PCB design platform with advanced routing and simulation capabilities |
OrCAD pcb designer | Cadence | A powerful PCB layout tool with tight integration with OrCAD Capture |
PADS | Mentor | A full-featured PCB layout solution with advanced constraint management |
Eagle | Autodesk | A popular PCB design tool for hobbyists and small businesses |
KiCad EDA | KiCad | A free and open-source PCB design suite with schematic capture and layout |
PCB Layout File Formats
PCB layouts are typically exchanged using standard file formats to ensure compatibility between different tools and manufacturers. Some common PCB layout file formats include:
-
Gerber: Gerber files are the industry standard for pcb fabrication. They contain information about the copper layers, solder mask, and silkscreen.
-
Drill: Drill files specify the location, size, and type of holes on the PCB.
-
ODB++: The ODB++ format is a comprehensive PCB manufacturing format that includes design, bill of materials, and manufacturing information.
-
IPC-2581: IPC-2581 is an emerging standard for PCB design data exchange that aims to replace Gerber and drill files.
FAQ
What is the difference between schematic capture and PCB layout?
Schematic capture is the process of creating a symbolic representation of a circuit, showing the components and their connections. PCB layout, on the other hand, is the process of physically arranging the components on a board and routing the connections between them.
What is the importance of design for manufacturing (DFM) in PCB layout?
DFM ensures that a PCB can be manufactured reliably and cost-effectively. It involves adhering to manufacturing constraints and design rules, such as minimum trace width and spacing, hole size, and clearance. DFM helps avoid manufacturing issues and costly design revisions.
What is the role of design rule check (DRC) in PCB layout?
DRC is an automated process that checks a PCB layout against a set of predefined design rules. These rules ensure that the layout meets manufacturing constraints and electrical requirements, such as minimum trace width, spacing, and hole size. DRC helps identify and correct layout errors before the board is sent for fabrication.
What are the common challenges in PCB layout?
Some common challenges in PCB layout include:
- Maintaining signal integrity for high-speed designs
- Managing power distribution and decoupling
- Dealing with limited board space and component placement constraints
- Ensuring proper grounding and minimizing EMI
- Meeting manufacturing constraints while optimizing performance and cost
How do I choose the right PCB layout tool for my project?
Choosing the right PCB layout tool depends on factors such as the complexity of your design, the features you need, and your budget. Consider the following when selecting a PCB layout tool:
- Ease of use and learning curve
- Integration with schematic capture and simulation tools
- Support for advanced features like 3D modeling and signal integrity analysis
- Cost and licensing options
- Compatibility with your design workflow and manufacturing partners
By understanding the importance of PCB layout, following best practices, and using the right tools, you can create reliable, high-performance circuit boards that meet your design goals and manufacturing requirements.