The Importance of PCB Etching
PCB etching is a fundamental step in the production of PCBs, which are the backbone of modern electronics. PCBs are used in a wide range of applications, from consumer electronics and industrial equipment to aerospace and medical devices. The accuracy and precision of the etching process directly impact the performance, reliability, and longevity of the final product.
Key Benefits of PCB Etching
- Creates precise and complex circuit patterns
- Enables high-density component placement
- Improves signal integrity and reduces electromagnetic interference
- Allows for the production of multiple identical boards
- Facilitates the miniaturization of electronic devices
The PCB Etching Process
The PCB etching process typically involves several steps, each of which is critical to achieving the desired outcome. These steps include:
1. PCB Design and Artwork Creation
The first step in the PCB etching process is to design the circuit and create the artwork. This is typically done using specialized PCB design software, such as Altium Designer or Eagle. The artwork consists of a digital representation of the copper traces, pads, and other features that will be etched onto the PCB substrate.
2. PCB Substrate Preparation
The PCB substrate, usually a copper-clad laminate, is prepared for etching by cleaning the surface to remove any contaminants or oxidation. This ensures that the photoresist adheres properly to the copper surface.
3. Photoresist Application
A light-sensitive material called photoresist is applied to the copper surface of the PCB substrate. This can be done using various methods, such as spin coating, screen printing, or dry film lamination. The photoresist acts as a protective layer, preventing the copper from being etched away in the areas where it is not wanted.
4. Exposure and Development
The PCB substrate with the applied photoresist is then exposed to light through a photomask, which contains the circuit pattern. The photomask is typically a transparent film with the circuit pattern printed in black. The exposed areas of the photoresist become soluble in a developer solution, while the unexposed areas remain intact.
After exposure, the PCB substrate is immersed in a developer solution, which removes the soluble portions of the photoresist, revealing the copper underneath. This leaves a protective photoresist layer in the areas where the copper traces and pads are desired.
5. Etching
The PCB substrate is then immersed in an etching solution, typically ferric chloride or ammonium persulfate. The etching solution chemically reacts with the exposed copper, dissolving it and leaving behind the desired circuit pattern protected by the photoresist.
6. Photoresist Removal and Cleaning
After etching, the remaining photoresist is removed using a stripping solution, revealing the final copper circuit pattern. The PCB substrate is then thoroughly cleaned to remove any residual chemicals or debris.
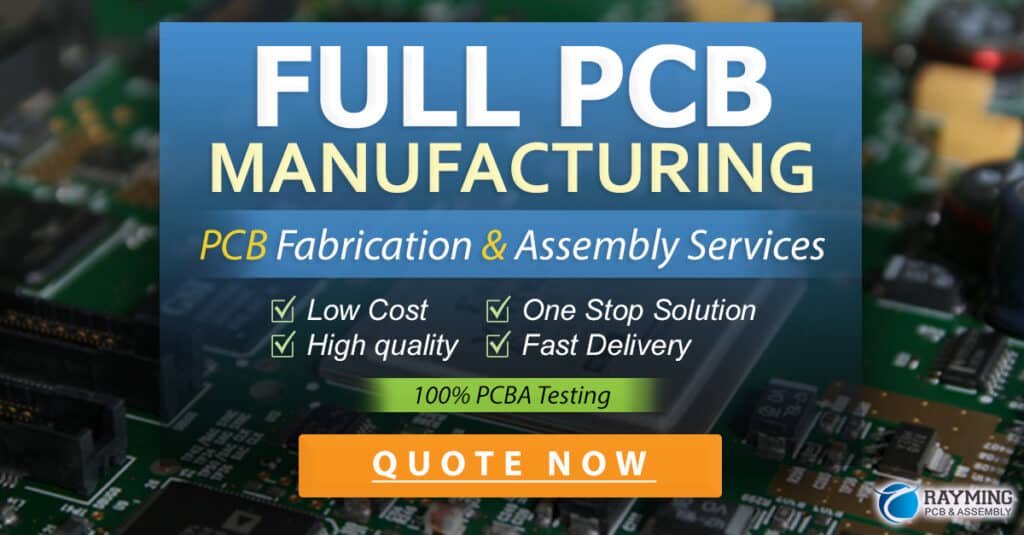
Types of PCB Etching
There are two main types of PCB etching: subtractive and additive.
Subtractive Etching
Subtractive etching is the most common method used in PCB manufacturing. It involves starting with a copper-clad PCB substrate and selectively removing the unwanted copper to create the desired circuit pattern. This is the process described in the previous section.
Additive Etching
Additive etching, also known as pattern plating, is a less common method that involves selectively adding copper to a bare PCB substrate to create the desired circuit pattern. This method is typically used for high-density PCBs or those with very fine features.
Factors Affecting PCB Etching Quality
Several factors can impact the quality of the PCB etching process, including:
- Photoresist quality and application
- Exposure and development conditions
- Etching solution composition and temperature
- Etching time and agitation
- PCB substrate material and thickness
To ensure high-quality PCB etching, it is essential to carefully control these factors and follow established best practices and industry standards.
Advancements in PCB Etching Technology
As the demand for smaller, more complex, and higher-performance electronic devices continues to grow, PCB etching technology has evolved to meet these challenges. Some of the latest advancements in PCB etching include:
Direct Imaging (DI)
Direct imaging is a process that uses a high-resolution digital imaging system to directly expose the photoresist on the PCB substrate, eliminating the need for a physical photomask. This allows for faster and more accurate circuit pattern transfer, particularly for high-density designs.
Laser Direct Imaging (LDI)
Laser direct imaging is a variation of DI that uses a high-powered laser to expose the photoresist. This enables even higher resolution and precision, making it suitable for the most demanding PCB applications.
Plasma Etching
Plasma etching is a dry etching process that uses a plasma (ionized gas) to remove the unwanted copper from the PCB substrate. This method offers several advantages over traditional wet etching, including higher resolution, better uniformity, and reduced environmental impact.
Environmental Considerations in PCB Etching
PCB etching involves the use of chemicals that can be hazardous to human health and the environment if not handled and disposed of properly. To minimize the environmental impact of PCB etching, many manufacturers are adopting more sustainable practices, such as:
- Using less hazardous etching solutions
- Implementing closed-loop systems to recycle and reuse chemicals
- Investing in wastewater treatment and proper disposal methods
- Adhering to environmental regulations and industry standards
The Future of PCB Etching
As the electronics industry continues to evolve, PCB etching technology will need to keep pace with the increasing demands for performance, reliability, and sustainability. Some of the trends and challenges that are likely to shape the future of PCB etching include:
- Continued miniaturization and increased circuit complexity
- Growing demand for high-frequency and high-speed applications
- Adoption of advanced materials, such as high-performance polymers and ceramics
- Emphasis on environmental sustainability and regulatory compliance
- Integration of AI and machine learning for process optimization and quality control
By embracing these challenges and investing in innovative solutions, the PCB manufacturing industry can ensure that PCB etching remains a critical and enabling technology for the electronics of tomorrow.
Frequently Asked Questions (FAQ)
1. What is the purpose of PCB etching?
PCB etching is used to selectively remove unwanted copper from a PCB substrate to create the desired circuit pattern. This process creates the conductive pathways that allow electronic components to be connected and function as intended.
2. What are the main types of PCB etching?
The two main types of PCB etching are subtractive etching and additive etching. Subtractive etching involves removing unwanted copper from a copper-clad PCB substrate, while additive etching involves selectively adding copper to a bare PCB substrate to create the desired circuit pattern.
3. What factors can affect the quality of PCB etching?
Several factors can impact the quality of PCB etching, including photoresist quality and application, exposure and development conditions, etching solution composition and temperature, etching time and agitation, and PCB substrate material and thickness.
4. What are some of the latest advancements in PCB etching technology?
Some of the latest advancements in PCB etching technology include direct imaging (DI), laser direct imaging (LDI), and plasma etching. These methods offer higher resolution, precision, and efficiency compared to traditional etching techniques.
5. How can the environmental impact of PCB etching be minimized?
To minimize the environmental impact of PCB etching, manufacturers can adopt sustainable practices such as using less hazardous etching solutions, implementing closed-loop systems to recycle and reuse chemicals, investing in wastewater treatment and proper disposal methods, and adhering to environmental regulations and industry standards.