Introduction to PCB Heatsinks
In the world of electronics, printed circuit boards (PCBs) play a crucial role in connecting and supporting various components. As electronic devices become more powerful and compact, managing heat dissipation becomes a critical concern. This is where PCB heatsinks come into play. In this comprehensive article, we will explore the concept of heatsinks in PCBs, their importance, types, selection criteria, and best practices for effective thermal management.
Understanding the Need for PCB Heatsinks
Electronic components generate heat during operation, and if this heat is not effectively dissipated, it can lead to performance degradation, reduced reliability, and even device failure. PCB heatsinks are designed to absorb and dissipate excess heat from heat-generating components, such as power transistors, voltage regulators, and microprocessors.
Heat Generation in Electronic Components
Electronic components, especially those handling high power or operating at high frequencies, generate significant amounts of heat. This heat is a byproduct of the electrical resistance within the components and the power dissipation resulting from their operation. The amount of heat generated depends on factors such as:
- Power consumption of the component
- Operating voltage and current
- Efficiency of the component
- Ambient temperature
Consequences of Insufficient Heat Dissipation
If the generated heat is not efficiently removed from the components, it can lead to various issues:
- Performance degradation: Excessive heat can cause components to operate outside their optimal temperature range, leading to reduced performance and efficiency.
- Reduced reliability: Prolonged exposure to high temperatures can accelerate the aging process of components, leading to premature failure and reduced reliability.
- Device failure: In extreme cases, overheating can cause permanent damage to components, resulting in complete device failure.
Therefore, implementing effective thermal management solutions, such as PCB heatsinks, is crucial to ensure the proper functioning and longevity of electronic devices.
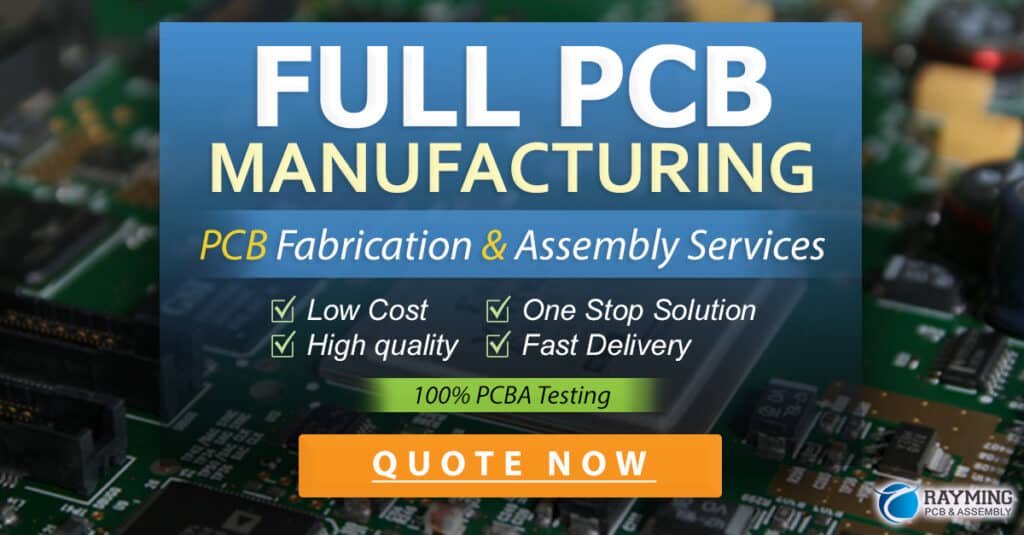
Types of PCB Heatsinks
PCB heatsinks come in various forms and materials, each with its own advantages and suitability for different applications. Let’s explore some common types of PCB heatsinks:
Passive Heatsinks
Passive heatsinks rely on natural convection and radiation to dissipate heat. They are typically made of materials with high thermal conductivity, such as aluminum or copper. Passive heatsinks come in different shapes and sizes, including:
- Extruded heatsinks: These heatsinks are manufactured through an extrusion process, resulting in a uniform cross-section along their length. They often have fins or channels to increase the surface area for heat dissipation.
- Stamped heatsinks: Stamped heatsinks are created by stamping or pressing metal sheets into the desired shape. They are cost-effective and suitable for low-power applications.
- Bonded fin heatsinks: These heatsinks consist of a base plate with fins bonded to it. The fins are typically made of aluminum, while the base plate can be made of copper or other materials.
Active Heatsinks
Active heatsinks incorporate a fan or other active cooling mechanisms to enhance heat dissipation. They are suitable for high-power applications where passive heatsinks alone may not provide sufficient cooling. Active heatsinks can be further classified into:
- Fan-assisted heatsinks: These heatsinks have a fan attached to the heatsink to force air over the fins, improving convective heat transfer.
- Peltier-based heatsinks: Peltier-based heatsinks utilize thermoelectric cooling (TEC) modules to actively pump heat away from the component. They can provide precise temperature control but require additional power and control circuitry.
Material Considerations
The choice of material for PCB heatsinks depends on various factors, including thermal conductivity, weight, cost, and compatibility with the PCB and components. Common materials used for PCB heatsinks include:
- Aluminum: Aluminum is widely used due to its good thermal conductivity, low cost, and lightweight nature. It is suitable for most general-purpose applications.
- Copper: Copper has higher thermal conductivity than aluminum but is heavier and more expensive. It is often used in high-performance applications where superior heat dissipation is required.
- Ceramic: Ceramic heatsinks offer excellent electrical insulation properties and can be used in applications where electrical isolation is crucial.
Heatsink Selection Criteria
Selecting the appropriate heatsink for a specific application involves considering several key factors:
Thermal Resistance
Thermal resistance is a measure of a heatsink’s ability to dissipate heat. It is expressed in units of °C/W (degrees Celsius per watt) and represents the temperature rise of the component per unit of power dissipated. A lower thermal resistance indicates better heat dissipation performance. When selecting a heatsink, it is essential to choose one with a thermal resistance that meets the cooling requirements of the specific component.
Surface Area and Fin Design
The surface area and fin design of a heatsink play a crucial role in its heat dissipation capabilities. A larger surface area allows for more heat to be dissipated through convection and radiation. Heatsinks with well-designed fins or channels maximize the surface area while maintaining efficient airflow. The fin spacing, thickness, and orientation should be optimized to achieve the desired cooling performance.
Compatibility with PCB and Components
Heatsinks must be compatible with the PCB and the components they are intended to cool. Factors to consider include:
- Size and form factor: The heatsink should fit within the available space on the PCB and not interfere with other components or connectors.
- Mounting options: The heatsink should have appropriate mounting provisions, such as through-holes or tabs, to securely attach it to the PCB or component.
- Thermal interface material (TIM): A suitable TIM, such as thermal paste or thermal pads, should be used between the component and the heatsink to ensure efficient heat transfer.
Cost and Manufacturability
Cost and manufacturability are important considerations when selecting heatsinks for mass production. Factors to consider include:
- Material cost: The cost of the heatsink material should be balanced against the required thermal performance and budget constraints.
- Manufacturing process: The chosen heatsink should be compatible with the manufacturing processes used for the PCB assembly, such as reflow soldering or wave soldering.
- Availability and lead time: The availability and lead time of the heatsink should be considered to ensure timely production and avoid supply chain disruptions.
Best Practices for PCB Heatsink Implementation
To ensure effective thermal management using PCB heatsinks, follow these best practices:
Proper Heatsink Sizing
Properly sizing the heatsink is crucial to achieve the desired cooling performance. Use thermal simulation tools or consult with heatsink manufacturers to determine the appropriate heatsink size based on the component’s power dissipation, ambient temperature, and desired operating temperature.
Efficient Heatsink Mounting
Ensure proper mounting of the heatsink to the PCB or component. Use appropriate mounting hardware, such as screws or clips, to achieve a secure and thermally efficient connection. Apply the recommended amount of thermal interface material between the component and the heatsink to minimize thermal resistance.
Optimize Airflow
Consider the airflow around the heatsink when designing the PCB layout. Ensure that the heatsink fins are oriented in the direction of natural or forced airflow to maximize convective heat transfer. Avoid obstructing the airflow with other components or structures.
Thermal Interface Material Selection
Select an appropriate thermal interface material (TIM) based on the specific application requirements. Thermal paste or grease provides excellent thermal conductivity but requires careful application. Thermal pads or adhesive tapes offer ease of assembly but may have slightly higher thermal resistance compared to paste.
Testing and Validation
Conduct thorough testing and validation of the PCB with the heatsink installed to ensure that the thermal management solution meets the desired performance criteria. Use thermal imaging cameras or temperature sensors to monitor the component temperatures under various operating conditions. Make adjustments to the heatsink design or mounting if necessary.
Frequently Asked Questions (FAQ)
-
What is the purpose of a heatsink in a PCB?
A heatsink in a PCB is used to dissipate excess heat generated by electronic components, ensuring proper functioning and preventing overheating. -
How do I select the right heatsink for my PCB?
When selecting a heatsink, consider factors such as the component’s power dissipation, desired operating temperature, available space on the PCB, compatibility with the component and PCB, and cost considerations. -
Can I use a heatsink without a fan?
Yes, passive heatsinks can be used without a fan in applications where the heat generation is relatively low or when natural convection is sufficient for cooling. However, for high-power applications, active heatsinks with fans may be necessary. -
What materials are commonly used for PCB heatsinks?
Common materials used for PCB heatsinks include aluminum, copper, and ceramic. Aluminum is lightweight and cost-effective, copper offers superior thermal conductivity, and ceramic provides excellent electrical insulation properties. -
How do I ensure proper mounting of the heatsink on the PCB?
To ensure proper mounting, use appropriate mounting hardware, such as screws or clips, to securely attach the heatsink to the PCB or component. Apply the recommended amount of thermal interface material between the component and the heatsink to minimize thermal resistance.
Conclusion
PCB heatsinks play a vital role in managing heat dissipation in electronic devices, ensuring reliable performance and longevity. Understanding the types of heatsinks, selection criteria, and best practices for implementation is crucial for effective thermal management. By carefully considering factors such as thermal resistance, surface area, compatibility, and cost, designers can select the most suitable heatsink for their specific application. Proper sizing, mounting, and testing are essential to validate the thermal management solution and ensure optimal performance. As electronic devices continue to evolve, the importance of efficient heat dissipation through PCB heatsinks will only grow, driving innovation in heatsink design and materials. By staying informed about the latest advancements in thermal management, engineers can develop robust and reliable electronic products that meet the ever-increasing demands of the industry.