What is HASL?
HASL is a process that involves immersing the PCB in a molten solder bath, typically consisting of a tin-lead alloy (SnPb). The excess solder is then blown off the surface of the PCB using hot air knives, leaving behind a thin, uniform layer of solder on the exposed copper pads and through-holes. This process helps to protect the copper from oxidation and enhances the solderability of the PCB.
The HASL Process
The HASL process consists of several steps:
-
Cleaning: The PCB is thoroughly cleaned to remove any dirt, debris, or contaminants that may affect the solder adhesion.
-
Fluxing: A thin layer of flux is applied to the PCB to help the molten solder adhere to the copper surfaces and prevent oxidation during the process.
-
Solder Dipping: The PCB is immersed in a molten solder bath, typically maintained at a temperature between 240°C and 260°C (464°F to 500°F). The solder alloy used in HASL is usually a eutectic composition of 63% tin and 37% lead (Sn63Pb37).
-
Hot Air Leveling: Immediately after the PCB is removed from the solder bath, hot air knives blow excess solder off the surface, leaving a thin, uniform layer of solder on the exposed copper areas.
-
Cooling: The PCB is then cooled to room temperature, allowing the solder to solidify.
-
Cleaning: Any remaining flux residue is removed from the PCB using a cleaning agent.
Advantages of HASL
HASL offers several advantages that make it a popular choice for PCB surface finishing:
-
Cost-effectiveness: HASL is one of the most economical surface finishing options, making it suitable for high-volume production.
-
Excellent solderability: The uniform solder layer provided by HASL ensures good solderability and facilitates the assembly process.
-
Compatibility: HASL is compatible with a wide range of soldering processes, including wave soldering, reflow soldering, and hand soldering.
-
Durability: The solder layer protects the copper from oxidation and provides a durable surface that can withstand multiple thermal cycles.
Disadvantages of HASL
Despite its many advantages, HASL also has some drawbacks:
-
Uneven surface: The hot air leveling process can sometimes result in an uneven surface, with variations in solder thickness across the PCB. This can lead to issues with component placement and soldering.
-
Thermal shock: The rapid temperature changes during the HASL process can cause thermal shock to the PCB, potentially leading to warpage or delamination.
-
Environmental concerns: The use of lead in the solder alloy poses environmental and health hazards, leading to the development of lead-free alternatives (e.g., lead-free HASL, SN100C).
-
Fine-pitch limitations: HASL may not be suitable for PCBs with very fine-pitch components or high-density designs due to the risk of bridging between closely spaced pads.
HASL vs. Other Surface Finishes
There are several other surface finishing options available for PCBs, each with its own advantages and disadvantages. Let’s compare HASL with some of the most common alternatives:
HASL vs. ENIG (Electroless Nickel Immersion Gold)
ENIG is a surface finish that consists of a layer of electroless nickel followed by a thin layer of immersion gold. Compared to HASL, ENIG offers several advantages:
- Flat, uniform surface: ENIG provides a flat, even surface that is ideal for fine-pitch components and high-density designs.
- Excellent oxidation resistance: The gold layer protects the underlying nickel from oxidation, ensuring long-term solderability.
- Lead-free: ENIG is a lead-free surface finish, making it more environmentally friendly than HASL.
However, ENIG is more expensive than HASL and can be prone to issues such as “black pad” (a defect caused by the corrosion of the nickel layer) if not properly controlled during the manufacturing process.
HASL vs. OSP (Organic Solderability Preservative)
OSP is a surface finish that involves applying a thin, organic coating to the exposed copper surfaces of the PCB. OSP offers several advantages over HASL:
- Flat surface: OSP provides a flat, uniform surface that is suitable for fine-pitch components.
- Lower cost: OSP is generally less expensive than HASL, making it an attractive option for cost-sensitive applications.
- Lead-free: OSP is a lead-free surface finish, making it more environmentally friendly than HASL.
However, OSP has a limited shelf life (typically 6-12 months) and may require special handling and storage conditions to maintain its solderability. Additionally, OSP may not be suitable for multiple thermal cycles or high-temperature applications.
HASL vs. Immersion Tin
Immersion tin is a surface finish that involves depositing a thin layer of pure tin on the exposed copper surfaces of the PCB. Compared to HASL, immersion tin offers several advantages:
- Flat surface: Immersion tin provides a flat, uniform surface that is suitable for fine-pitch components.
- Lead-free: Immersion tin is a lead-free surface finish, making it more environmentally friendly than HASL.
- Compatibility: Immersion tin is compatible with a wide range of soldering processes and can withstand multiple thermal cycles.
However, immersion tin is more expensive than HASL and may be prone to tin whiskers (thin, conductive filaments that can grow from the tin surface) if not properly controlled during the manufacturing process.
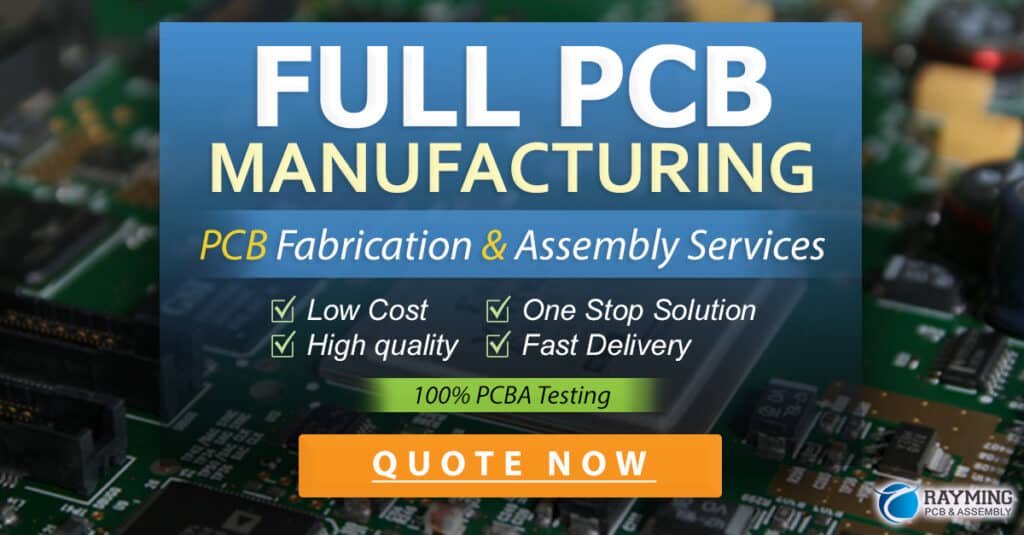
Choosing the Right Surface Finish
When selecting a surface finish for your PCB, consider the following factors:
-
Application requirements: Consider the specific requirements of your application, such as the need for fine-pitch components, high-density designs, or multiple thermal cycles.
-
Cost: Evaluate the cost of each surface finish option and balance it against your budget and production volume.
-
Environmental considerations: If environmental friendliness is a priority, consider lead-free surface finishes such as ENIG, OSP, or immersion tin.
-
Shelf life: If your PCBs will be stored for an extended period before assembly, consider surface finishes with longer shelf lives, such as ENIG or immersion tin.
-
Soldering process: Ensure that the chosen surface finish is compatible with your intended soldering process (e.g., wave soldering, reflow soldering, hand soldering).
FAQ
-
Q: Is HASL a lead-free surface finish?
A: Traditional HASL uses a tin-lead solder alloy, which contains lead. However, there are lead-free alternatives available, such as lead-free HASL (LF-HASL) and SN100C. -
Q: Can HASL be used for fine-pitch components?
A: HASL may not be the best choice for fine-pitch components or high-density designs due to the risk of solder bridging between closely spaced pads. In these cases, surface finishes like ENIG, OSP, or immersion tin may be more suitable. -
Q: What is the typical shelf life of a HASL-finished PCB?
A: HASL-finished PCBs generally have a shelf life of 12-18 months, depending on storage conditions and the specific solder alloy used. -
Q: Can HASL-finished PCBs be reworked?
A: Yes, HASL-finished PCBs can be reworked using standard soldering techniques. However, the rework process may be more challenging compared to other surface finishes due to the uneven surface and the potential for solder bridging. -
Q: Is HASL suitable for high-temperature applications?
A: HASL is generally suitable for high-temperature applications, as the solder layer can withstand multiple thermal cycles. However, the specific temperature limits will depend on the solder alloy used and the PCB materials.
Surface Finish | Advantages | Disadvantages |
---|---|---|
HASL | – Cost-effective – Excellent solderability – Compatible with various soldering processes – Durable |
– Uneven surface – Thermal shock risk – Environmental concerns (lead) – Limited fine-pitch capability |
ENIG | – Flat, uniform surface – Excellent oxidation resistance – Lead-free |
– Higher cost – Potential for “black pad” defect |
OSP | – Flat surface – Lower cost – Lead-free |
– Limited shelf life – May require special handling and storage – Not suitable for multiple thermal cycles or high-temperature applications |
Immersion Tin | – Flat surface – Lead-free – Compatible with various soldering processes – Withstands multiple thermal cycles |
– Higher cost – Potential for tin whiskers |
In conclusion, HASL is a widely used and cost-effective surface finishing option for PCBs, offering excellent solderability and compatibility with various soldering processes. However, it has limitations in terms of uneven surface, thermal shock risk, and environmental concerns due to the use of lead. When choosing a surface finish for your PCB, consider your application requirements, cost, environmental considerations, shelf life, and soldering process compatibility. Alternative surface finishes like ENIG, OSP, and immersion tin offer their own unique advantages and disadvantages, making them suitable for specific applications and requirements.