Introduction to Tombstoning in PCB Assembly
Tombstoning, also known as the “Manhattan effect” or “Stonehenge effect,” is a common defect that occurs during the surface mount technology (SMT) assembly process of printed circuit boards (PCBs). This defect is characterized by the vertical standing of chip components, such as resistors or capacitors, on one end, resembling a tombstone or a miniature version of the famous Stonehenge monument.
Tombstoning can lead to various issues, including poor electrical connections, reduced mechanical strength, and potential short circuits. Understanding the causes and prevention techniques for tombstoning is crucial for ensuring high-quality PCB assembly and minimizing production delays and costs.
Causes of Tombstoning in PCB Assembly
Several factors can contribute to the occurrence of tombstoning during the SMT assembly process. Some of the main causes include:
Uneven Heating
One of the primary reasons for tombstoning is uneven heating of the component during the reflow soldering process. If one end of the component heats up faster than the other, it can cause the molten solder to pull the component upright, resulting in tombstoning.
Component Size and Geometry
Smaller chip components, such as 0402 or 0201 sized resistors and capacitors, are more prone to tombstoning due to their lightweight and compact size. Additionally, components with a rectangular geometry or unequal terminal sizes can be more susceptible to tombstoning.
Solder Paste Volume and Composition
Inconsistent or excessive solder paste application can lead to tombstoning. If one end of the component has more solder paste than the other, it can create an imbalance during the reflow process, causing the component to stand up. The composition of the solder paste, including its flux activity and metal content, can also influence the likelihood of tombstoning.
PCB Design and Pad Geometry
The design of the PCB and the geometry of the component pads can play a significant role in tombstoning. Unequal pad sizes, incorrect pad spacing, or misaligned pads can contribute to uneven heating and solder flow, increasing the risk of tombstoning.
Reflow Profile and Temperature Gradients
An improper reflow profile, with excessive temperature ramp rates or peak temperatures, can exacerbate tombstoning. Temperature gradients across the PCB or within the reflow oven can also lead to uneven heating and tombstoning of components.
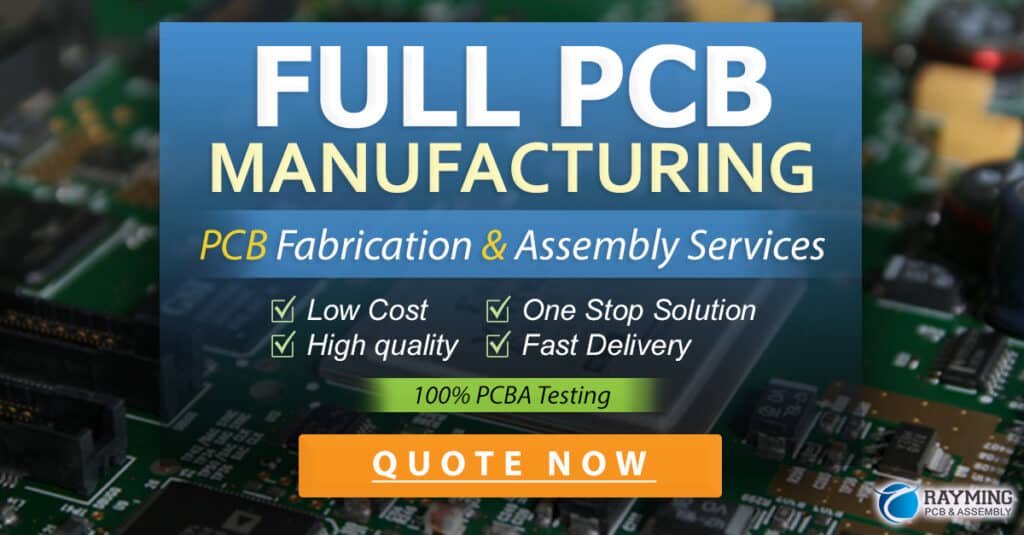
Prevention Techniques for Tombstoning
To minimize the occurrence of tombstoning in PCB assembly, several prevention techniques can be employed:
Component Selection and Placement
Choosing components with balanced terminal sizes and avoiding excessively small chip components can help reduce the risk of tombstoning. Proper component placement, with adequate spacing and alignment, can also minimize the potential for uneven heating.
Solder Paste Application
Ensuring consistent and appropriate solder paste volume is crucial for preventing tombstoning. The use of solder paste inspection (SPI) systems can help monitor and control the solder paste deposition process, ensuring even distribution across the component pads.
PCB Design Optimization
Designing PCBs with balanced pad sizes, appropriate pad spacing, and proper thermal management can minimize the occurrence of tombstoning. Implementing thermal relief patterns or using via-in-pad designs can help evenly distribute heat during the reflow process.
Reflow Profile Optimization
Developing and optimizing the reflow profile is essential for preventing tombstoning. A well-designed reflow profile should have controlled ramp rates, adequate soak times, and appropriate peak temperatures to ensure even heating and solder flow across the PCB.
Process Control and Monitoring
Implementing process control measures, such as regular maintenance and calibration of the reflow oven, can help maintain consistent temperature profiles and minimize temperature gradients. Monitoring the assembly process using automated optical inspection (AOI) or X-ray inspection can help detect and address tombstoning issues early in the production cycle.
Impact of Tombstoning on PCB Performance and Reliability
Tombstoning can have significant consequences for the performance and reliability of PCBs. Some of the potential impacts include:
Electrical Connectivity Issues
When a component tombstones, it can result in poor or incomplete electrical connections between the component and the PCB pads. This can lead to intermittent or complete loss of functionality, depending on the severity of the tombstoning and the specific circuit affected.
Mechanical Instability
Tombstoned components are less mechanically stable compared to properly soldered components. The vertical standing of the component can make it more susceptible to mechanical stress, vibration, or shock, potentially leading to component detachment or damage.
Short Circuits and Signal Integrity
In some cases, tombstoning can cause the component terminals to come into contact with adjacent components or traces, resulting in short circuits or signal integrity issues. This can lead to malfunctions, reduced performance, or even complete failure of the PCB.
Rework and Repair Challenges
Tombstoned components often require manual rework or repair, which can be time-consuming and costly. The process of correcting tombstoning may involve manually resoldering the component or, in severe cases, replacing the affected component entirely. This can impact production throughput and increase the overall manufacturing costs.
Reduced Reliability and Product Lifetime
PCBs with tombstoned components may have reduced overall reliability and shorter product lifetimes. The compromised electrical and mechanical connections can make the PCB more susceptible to failures, especially when exposed to environmental stresses such as temperature fluctuations, humidity, or vibration.
Best Practices for Tombstone-Free PCB Assembly
To achieve tombstone-free PCB assembly, consider the following best practices:
-
Design for Manufacturing (DFM): Incorporate DFM principles into the PCB design process, ensuring balanced pad sizes, appropriate component spacing, and optimal thermal management.
-
Component Selection: Choose components with balanced terminal sizes and avoid excessively small chip components whenever possible. Consider using larger component packages or alternative component types if tombstoning is a recurring issue.
-
Solder Paste Optimization: Use high-quality solder paste with appropriate flux activity and metal content. Implement solder paste inspection (SPI) to ensure consistent and even solder paste deposition.
-
Reflow Profile Development: Develop and optimize the reflow profile for each PCB design, considering factors such as component thermal mass, PCB thickness, and solder paste characteristics. Use controlled ramp rates, adequate soak times, and appropriate peak temperatures.
-
Process Control and Monitoring: Regularly maintain and calibrate the reflow oven to ensure consistent temperature profiles. Implement automated optical inspection (AOI) or X-ray inspection to detect and address tombstoning issues early in the production process.
-
Operator Training and Awareness: Provide comprehensive training to assembly operators, emphasizing the importance of proper component placement, solder paste application, and process control. Foster a culture of quality and continuous improvement to minimize the occurrence of tombstoning and other assembly defects.
Troubleshooting Tombstoning Issues
When tombstoning issues arise during PCB assembly, follow these troubleshooting steps:
-
Identify the Affected Components: Determine which components are consistently experiencing tombstoning and analyze their characteristics, such as size, geometry, and terminal configuration.
-
Review the PCB Design: Examine the PCB design, focusing on the pad sizes, spacing, and thermal relief patterns for the affected components. Identify any potential design-related factors contributing to tombstoning.
-
Analyze the Solder Paste Application: Assess the solder paste deposition process, including the solder paste volume, consistency, and placement accuracy. Use SPI data to identify any inconsistencies or excessive solder paste application.
-
Evaluate the Reflow Profile: Review the reflow profile used for the affected PCBs, paying attention to the temperature ramp rates, soak times, and peak temperatures. Compare the profile against the recommended guidelines for the specific solder paste and components used.
-
Inspect the Reflow Oven: Check the reflow oven for any temperature gradients, uneven heating zones, or airflow issues that could contribute to tombstoning. Perform regular maintenance and calibration to ensure optimal performance.
-
Conduct Root Cause Analysis: Analyze the collected data and observations to identify the root cause of the tombstoning issue. Consider factors such as component selection, PCB design, solder paste application, reflow profile, and process control.
-
Implement Corrective Actions: Based on the root cause analysis, implement appropriate corrective actions, such as redesigning the PCB, adjusting the solder paste application, optimizing the reflow profile, or improving process control measures.
-
Monitor and Validate: After implementing the corrective actions, monitor the assembly process closely to ensure the effectiveness of the changes. Validate the results through inspection and testing to confirm the elimination or reduction of tombstoning occurrences.
FAQ
-
What is tombstoning in PCB assembly?
Tombstoning is a defect that occurs during the surface mount technology (SMT) assembly process, where a chip component, such as a resistor or capacitor, stands vertically on one end, resembling a tombstone. -
What causes tombstoning in PCB assembly?
Tombstoning can be caused by various factors, including uneven heating of the component, component size and geometry, inconsistent solder paste application, improper PCB design, and suboptimal reflow profile. -
How can tombstoning be prevented in PCB assembly?
Tombstoning can be prevented by selecting appropriate components, ensuring consistent solder paste application, optimizing PCB design, developing proper reflow profiles, and implementing process control and monitoring measures. -
What are the consequences of tombstoning in PCBs?
Tombstoning can lead to poor electrical connections, mechanical instability, short circuits, signal integrity issues, and reduced overall reliability and product lifetime of the PCB. -
How can tombstoning issues be troubleshot in PCB assembly?
Troubleshooting tombstoning issues involves identifying the affected components, reviewing the PCB design, analyzing the solder paste application, evaluating the reflow profile, inspecting the reflow oven, conducting root cause analysis, implementing corrective actions, and monitoring and validating the results.
Conclusion
Tombstoning is a common defect in PCB assembly that can have significant implications for the performance, reliability, and manufacturing efficiency of electronic products. By understanding the causes and implementing appropriate prevention techniques, manufacturers can minimize the occurrence of tombstoning and ensure high-quality PCB assembly.
Effective tombstone prevention relies on a combination of factors, including component selection, PCB design optimization, solder paste application control, reflow profile development, and process monitoring. By adopting best practices and continuously improving the assembly process, manufacturers can achieve tombstone-free PCB production, reducing rework, minimizing costs, and enhancing overall product quality.
When tombstoning issues do arise, a systematic troubleshooting approach, involving root cause analysis and corrective action implementation, is essential for resolving the problem and preventing future occurrences. By staying vigilant and proactively addressing tombstoning challenges, manufacturers can maintain a competitive edge in the fast-paced and demanding world of electronics manufacturing.