Overview of PCB Fabrication
Printed circuit board (PCB) fabrication is the process of manufacturing PCBs for use in electronic devices. A PCB fab, short for PCB fabrication facility or factory, is where the complex process of making PCBs takes place. PCB fabs range from small specialized shops to large factories producing thousands of boards per day.
The PCB fabrication process involves several key steps:
1. PCB design and engineering
2. Inner layer printing
3. Etching
4. Lamination
5. Drilling
6. Plating
7. Outer layer printing
8. Surface finish
9. Silkscreen
10. Electrical test
11. Quality control
PCB Design and Engineering
PCB fabrication starts with the customer’s PCB design files, usually in Gerber format. PCB design engineers at the fab review the design for manufacturability, make any necessary modifications, and generate tooling and stencil files to guide the fabrication process. This upfront engineering is critical to ensure high yields and reliability in volume production.
Inner Layer Printing
For multi-layer PCBs, the inner layer circuitry is printed onto large thin sheets of laminated copper clad material. The copper is coated with a light-sensitive resist. Then the resist is exposed to light through a high-precision photomask or LDI (Laser Direct Imaging) system to transfer the circuit pattern. The unexposed resist is chemically removed, leaving the copper circuitry protected.
Etching
The sheets go through a chemical etching process which removes the unprotected copper, leaving only the circuit traces behind. The remaining resist is then stripped off, leaving the bare copper circuits. The sheets are then optically inspected for any defects.
Lamination
The inner layer sheets, prepreg (pre-impregnated bonding material), and copper foil for the outer layers are stacked in proper order and bonded together under high temperature and pressure in a laminating press. This forms a solid multi-layer board.
Drilling
High-speed CNC drilling machines drill all the holes in the board – holes for plated through-holes, component leads, and mounting. More advanced fabs use laser drills for ultra-small microvias. Proper drill bit management is key for quality and cost control.
Plating
The drilled boards are plated with copper to form the plated through-holes, which electrically connect the layers. This is done through an electroless copper process followed by electroplating. The holes are then filled or partially filled with a special epoxy if required by the design.
Outer Layer Printing
Similar to inner layer printing, the outer layer circuitry is printed and etched. The outer layer resist is stripped off. A protective plating of tin or gold preserves the exposed copper circuits.
Surface Finish
A PCB’s surface finish protects the outer copper layer and facilitates soldering. Common finishes are:
Finish | Composition | Pros | Cons |
---|---|---|---|
HASL | Tin-lead | Low cost, easy to solder | Not flat, contains lead |
ENIG | Nickel-gold | Flat, lead-free, easy to solder | Expensive |
OSP | Organic film | Low cost, flat, lead-free | Harder to solder, short shelf life |
Immersion Tin | Tin | Lead-free, flat, low cost | Can form whiskers |
Immersion Silver | Silver | Lead-free, flat, easy to solder | Tarnishes over time |
The choice of surface finish depends on the application, cost, and lead-free requirements.
Silkscreen
The top silkscreen legend is applied, usually by screen printing white epoxy ink. This layer labels components, test points, part numbers, logos, etc. for ease of assembly and identification.
Electrical Test
The fab tests the finished board to check for any shorts or open circuits in the connections. A “bed of nails” fixture or a flying probe tester rapidly checks the continuity and isolation of every net in the board against the PCB netlist file. Any defective boards are repaired or scrapped.
Quality Control
The boards go through a final visual inspection, and a sample set is microsectioned and inspected to verify the plating thickness, hole wall quality, and lamination integrity meet IPC standards. Ionic contamination testing checks the cleanliness of the board. A certificate of conformance is issued with the order.
Types of PCB Fabs
PCB fabs can be categorized by their capabilities:
Prototype vs Production
Prototype fabs specialize in quick-turn fabrication of one-off boards or small batches for prototyping and testing purposes. They are generally more expensive but offer faster turnaround times.
Production fabs focus on larger volume orders and offer better pricing, but have longer lead times due to batching and queuing of orders. Some fabs offer both prototyping and production services.
Domestic vs Offshore
Domestic fabs are located in the same country as the customer. They offer faster delivery times, easier communication, and better IP protection, but are usually more expensive.
Offshore fabs, mainly in China and Taiwan, offer significantly lower pricing and have evolved to provide good quality and service, but have longer shipping times, potential communication barriers, and higher risk of IP theft. Many companies prototype domestically but volume produce offshore.
Technology Capabilities
Fabs are also differentiated by the complexity of designs they can handle, as defined by:
- Minimum trace width and spacing
- Minimum hole size
- Maximum layer count
- Material types (FR-4, Rogers, flex, etc)
- Special processes (HDI, embedded passives, metal core, etc)
High-tech fabs can fabricate dense designs with trace widths under 3 mil (75 micron), microvias, and high layer counts over 40 layers. Low-tech fabs are limited to larger features, fewer layers, and standard materials.
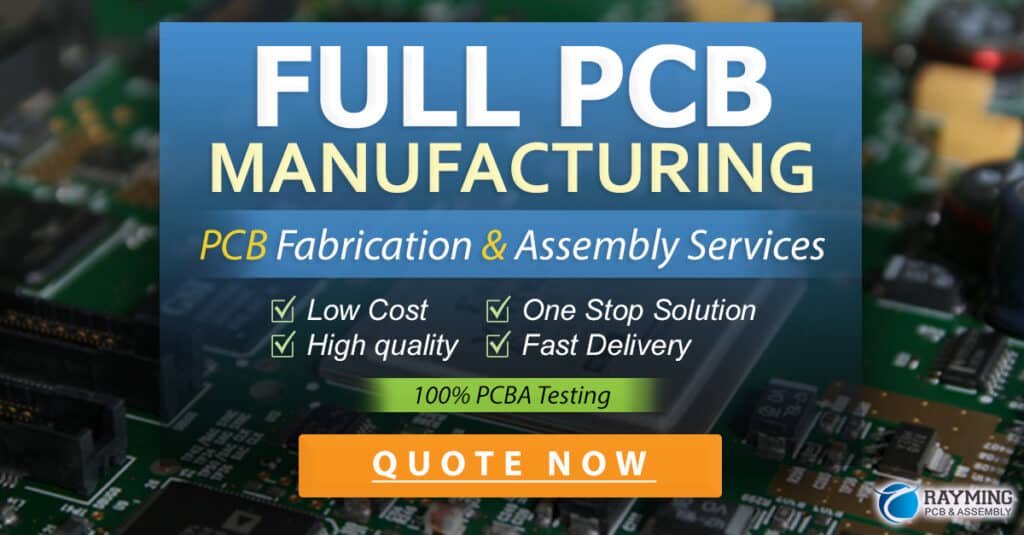
Choosing a PCB Fab
When selecting a PCB fab, consider the following:
- Technology capabilities – can they handle your most complex designs?
- Quality certifications – ISO 9001, IATF 16949, AS9100, IPC, UL, etc.
- Industry focus – some fabs specialize in certain industries like automotive, aerospace, or medical that have specific requirements
- Volume capabilities – what is their typical lot size and capacity?
- Lead times – how fast can they deliver?
- Pricing – get quotes from multiple fabs
- Customer service – how responsive and easy are they to work with?
- Location – domestic or offshore?
Get referrals from colleagues, check online reviews, and audit potential fabs in person if possible. Building a good relationship with your fab is key to successful production.
PCB Fab Industry Trends
The PCB fabrication industry is constantly evolving to support advances in electronics:
Miniaturization
As devices shrink, PCBs are getting denser with finer traces and smaller vias. HDI (High Density Interconnect) techniques like microvias, blind and buried vias, and via-in-pad are becoming more common. Fabs are investing in advanced equipment to etch smaller features accurately.
High Speed
Faster signaling rates in applications like 5G, automotive radar, and high-performance computing require PCBs with tighter impedance control, lower loss materials, and smoother copper. High-frequency materials like Rogers and PTFE are being used more. Fabs are improving their processes to meet these needs.
Packaging Substrates
The growth of advanced IC packaging technologies like 2.5D and 3D integration is driving demand for packaging substrates – high-density PCBs that interconnect chips. Fabs are developing modified semi-additive processes (mSAP) and other techniques to fabricate substrates with trace widths as small as 2 microns.
Automation
PCB fabs are automating more of their processes to improve quality, repeatability, and efficiency. Examples include:
– Automated optical inspection (AOI) systems for catching defects
– Robotic material handling systems
– Data-driven process optimization using machine learning
Environmental Regulations
Environmental concerns continue to shape the PCB industry. More fabs are going green to reduce their environmental impact and comply with regulations like RoHS. This includes using lead-free processes, recycling water, and proper disposal of chemicals. Some fabs are also exploring additive manufacturing techniques that are less wasteful.
FAQ
What is the typical turnaround time for PCB fabrication?
Turnaround times vary depending on the complexity of the design and the fab’s workload. Simple 2-layer boards can be fabricated in 1-2 days at a prototype shop, while complex multi-layer boards can take 2-3 weeks or more. Most fabs offer expedite options for a higher price.
How much does PCB fabrication cost?
PCB fabrication costs depend on the number of layers, size of the board, minimum feature sizes, material type, surface finish, and quantity. A small 2-layer board might cost $10-$50 each in low volumes, while a large multi-layer board can cost hundreds of dollars each. Get quotes from several fabs for your specific design.
What files do I need to provide to a PCB fab?
PCB fabs typically require Gerber files for each layer of the board, drill files, and a pick-and-place file for assembly. Gerber files are a standard format that defines the copper patterns, soldermask, silkscreen, and other features. Drill files specify the location and size of all the holes. Pick-and-place files define the location and rotation of each component for assembly. Some fabs also accept ODB++ files which include all this information in one intelligent format.
What certifications should a PCB fab have?
At a minimum, a reputable PCB fab should be ISO 9001 certified, which indicates they have a robust quality management system. For automotive, medical, aerospace, and defense applications, look for industry-specific certifications like IATF 16949, ISO 13485, AS9100, and NADCAP. IPC-A-600 and IPC-6012 certifications demonstrate the fab’s ability to meet IPC workmanship and performance standards.
How do I ensure my intellectual property is protected when using an offshore fab?
Protecting IP is a valid concern when using offshore fabs. Some steps to mitigate risk include:
– Have the fab sign a non-disclosure agreement (NDA)
– Don’t send them the complete design – use a service like Seeed Studio’s Fusion PCB service that only requires uploading Gerber files
– Break the design into modules and have them fabricated by different fabs
– Encrypt or obfuscate any sensitive design files
– Work with a domestic broker that has vetted offshore fabs and manages the fabrication process securely
Ultimately, there is always some risk in sending designs offshore, so it’s important to weigh the cost savings against the potential impact of IP theft for your business.
Conclusion
PCB fabrication is a complex multi-step process carried out at specialized PCB fabs. Choosing the right fab involves considering their capabilities, quality, service, location, and cost. As electronics continue to evolve, PCB fabs are advancing their processes to enable denser, faster, and more environmentally friendly designs. Building a strong relationship with a reliable fab partner is critical for bringing new electronic products to market successfully.