What are Custom PCBs?
Custom PCBs are printed circuit boards that are designed and manufactured to meet specific requirements and specifications. Unlike standard PCBs, which are mass-produced and available off-the-shelf, custom PCBs are tailored to the unique needs of a particular application or device. This means that the layout, components, and features of a custom PCB are carefully selected and optimized to achieve the desired performance and functionality.
Custom PCBs can be designed using various software tools, such as Eagle, KiCad, or Altium Designer. These tools allow designers to create schematic diagrams, select components, and layout the PCB. Once the design is finalized, the PCB can be manufactured using a variety of techniques, such as photolithography, etching, drilling, and plating.
Advantages of Custom PCBs
1. Tailored to Specific Requirements
One of the main advantages of custom PCBs is that they can be tailored to meet specific requirements and specifications. This means that designers can optimize the PCB layout, select the appropriate components, and add features that are not available in standard PCBs. For example, a custom PCB can be designed with a specific shape or size to fit into a particular enclosure or device. It can also be designed with special features, such as high-speed interfaces, wireless connectivity, or sensors.
2. Improved Performance and Reliability
Custom PCBs can be designed to achieve optimal performance and reliability. By carefully selecting the components and optimizing the layout, designers can minimize signal interference, reduce power consumption, and improve thermal management. This can result in better signal integrity, higher efficiency, and longer product life. Custom PCBs can also be designed with redundancy and fail-safe mechanisms to ensure reliable operation in critical applications.
3. Cost-Effective for Large Volumes
While custom PCBs may have higher upfront costs compared to standard PCBs, they can be cost-effective for large volume production. This is because custom PCBs can be optimized for manufacturing, reducing the amount of material, labor, and time required to produce each board. In addition, custom PCBs can be designed with fewer components and simpler layouts, which can further reduce manufacturing costs.
4. Intellectual Property Protection
Custom PCBs can provide a level of intellectual property protection that standard PCBs cannot. By designing a custom PCB, manufacturers can keep their proprietary technology and designs confidential. This can be especially important for companies that develop unique or innovative products that they want to protect from competitors.
5. Faster Time-to-Market
Custom PCBs can enable faster time-to-market for new products. By designing a PCB specifically for a particular application, manufacturers can avoid the need to modify or adapt standard PCBs to fit their needs. This can save time and reduce the risk of errors or compatibility issues. In addition, custom PCBs can be designed with future upgrades or modifications in mind, allowing for faster and more efficient product iterations.
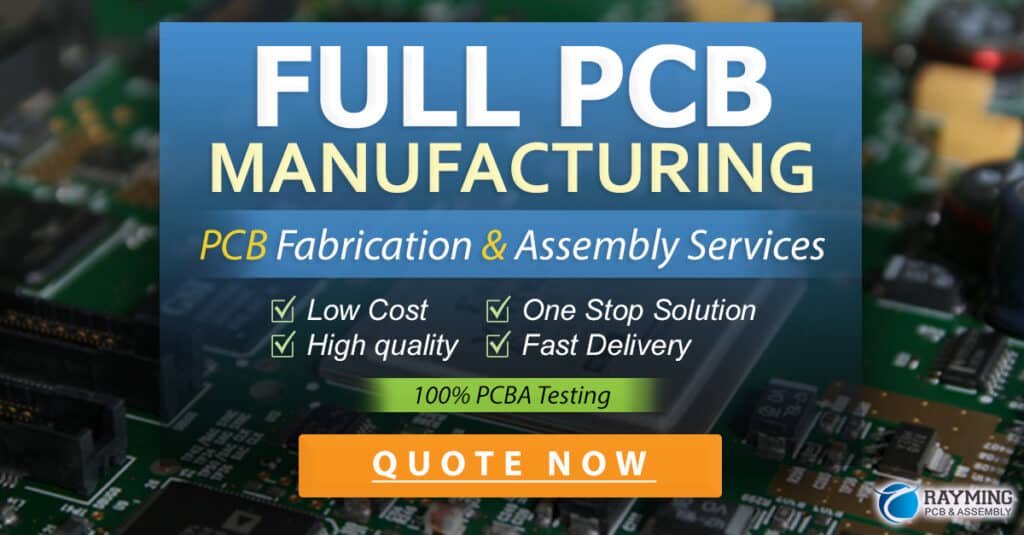
Disadvantages of Custom PCBs
1. Higher Upfront Costs
One of the main disadvantages of custom PCBs is that they have higher upfront costs compared to standard PCBs. This is because custom PCBs require more design and engineering work, as well as specialized manufacturing processes. The cost of designing and prototyping a custom PCB can be significant, especially for complex or high-density designs. In addition, the cost of tooling and setup for manufacturing can also be higher for custom PCBs.
2. Longer Lead Times
Custom PCBs also have longer lead times compared to standard PCBs. This is because the design and manufacturing process is more complex and requires more time to complete. The lead time for a custom PCB can vary depending on the complexity of the design, the availability of components, and the manufacturing capacity of the supplier. In some cases, lead times can be several weeks or even months, which can be a significant challenge for companies with tight deadlines or fast-moving markets.
3. Limited Flexibility for Changes
Another disadvantage of custom PCBs is that they have limited flexibility for changes or modifications once the design is finalized. Unlike standard PCBs, which can be easily modified or adapted to new requirements, custom PCBs are designed for a specific application and may not be compatible with other devices or systems. This means that any changes or updates to the design may require a new round of prototyping and manufacturing, which can be time-consuming and expensive.
4. Dependence on Supplier Expertise
Custom PCBs also require a higher level of expertise and experience from the supplier. Designing and manufacturing a custom PCB requires specialized knowledge and skills in areas such as signal integrity, thermal management, and manufacturing processes. This means that companies may need to work with experienced and reputable suppliers who have the necessary expertise and capabilities to deliver high-quality custom PCBs. Choosing the wrong supplier can result in delays, quality issues, or even project failures.
5. Potential for Overdesign
Finally, custom PCBs can also be prone to overdesign, which can lead to unnecessary complexity and higher costs. Overdesign occurs when designers add features or components that are not essential to the functionality or performance of the PCB. This can be due to a lack of understanding of the requirements, a desire to future-proof the design, or simply a lack of discipline in the design process. Overdesign can result in higher manufacturing costs, longer lead times, and reduced reliability.
FAQ
1. What is the difference between a custom PCB and a standard PCB?
A custom PCB is designed and manufactured to meet specific requirements and specifications, while a standard PCB is mass-produced and available off-the-shelf. Custom PCBs are tailored to the unique needs of a particular application or device, while standard PCBs are designed for general-purpose use.
2. How much does it cost to design and manufacture a custom PCB?
The cost of designing and manufacturing a custom PCB can vary widely depending on factors such as the complexity of the design, the number of layers, the type of components, and the volume of production. In general, the upfront costs for custom PCBs are higher than for standard PCBs, but they can be cost-effective for large volume production.
3. How long does it take to design and manufacture a custom PCB?
The lead time for designing and manufacturing a custom PCB can vary depending on the complexity of the design, the availability of components, and the manufacturing capacity of the supplier. In general, custom PCBs have longer lead times than standard PCBs, and can take several weeks or even months to complete.
4. What are the benefits of using a custom PCB?
The benefits of using a custom PCB include:
- Tailored to specific requirements and specifications
- Improved performance and reliability
- Cost-effective for large volume production
- Intellectual property protection
- Faster time-to-market
5. What are the challenges of using a custom PCB?
The challenges of using a custom PCB include:
- Higher upfront costs
- Longer lead times
- Limited flexibility for changes or modifications
- Dependence on supplier expertise
- Potential for overdesign
Conclusion
Custom PCBs offer many advantages over standard PCBs, including the ability to tailor the design to specific requirements, improve performance and reliability, and protect intellectual property. However, they also come with higher upfront costs, longer lead times, and limited flexibility for changes. Companies considering custom PCBs should carefully weigh the pros and cons and choose a reputable and experienced supplier to ensure success.
Advantages of Custom PCBs | Disadvantages of Custom PCBs |
---|---|
Tailored to specific requirements | Higher upfront costs |
Improved performance and reliability | Longer lead times |
Cost-effective for large volumes | Limited flexibility for changes |
Intellectual property protection | Dependence on supplier expertise |
Faster time-to-market | Potential for overdesign |
Ultimately, the decision to use a custom PCB or a standard PCB will depend on the specific needs and constraints of the application. By understanding the advantages and disadvantages of custom PCBs, companies can make informed decisions and choose the best option for their needs.