What are Flexible Rigid PCBs?
A flexible rigid PCB (also known as flex-rigid PCB) combines rigid and flexible PCB technologies into a single circuit board. As the name suggests, flex-rigid PCBs have both rigid and flexible sections on the same board. The rigid parts of the PCB provide mechanical support and mounting stability, while the flexible sections allow dynamic flexing and bending.
Flexible rigid PCBs provide the best of both worlds – the precision and reliability of rigid PCBs combined with the dynamic flexing abilities of flex PCBs. This makes them suitable for many applications where complex and compact electronic designs are required.
Construction of Flex-Rigid PCBs
A flex-rigid PCB consists of flexible copper layers bonded together with rigid copper clad laminates. The flex layers provide flexibility while the rigid sections offer mechanical support.
Here are some key construction elements of a typical flex-rigid PCB:
- Flex layer – Made of a flexible polyimide film substrate clad with copper on one or both sides. Allows dynamic bending and flexing.
- Rigid layer – Made of rigid FR-4 glass epoxy substrate clad with copper. Provides mechanical support.
- Adhesive layers – Bond the flex and rigid layers together. Popular adhesive include acrylic, epoxy, and thermoplastic.
- Cover layer – A protective solder mask layer covering the outer surfaces.
- Silkscreen layer – Used for markings and component legends.
The rigid and flex layers are strategically arranged and interconnected to form a complete flex-rigid board optimized for the target application.
Benefits of Flex-Rigid PCBs
Flex-rigid PCBs offer several benefits over regular rigid PCBs:
- Flexible bending – The flex sections allow the PCB to bend and flex dynamically. This enables shaping the PCB to fit product enclosures and move dynamically.
- Space savings – By folding and bending, flex-rigid PCBs can fit into tight spaces where rigid PCBs won’t. This allows for smaller product sizes.
- Reliability – The rigid sections provide stability and prevent flexing failures in high stress areas. This improves reliability.
- Layer stacking – Rigid layers provide more layers for routing complex designs. Flex-rigid PCBs can have 10 layers or more.
- Reduced wiring – Integrating multiple PCB assemblies onto a single flex-rigid PCB simplifies interconnections and reduces wiring.
- Design freedom – Flex-rigid PCBs allow partitioning of circuits across rigid and flex areas for optimal performance, space savings, and reliability.
In summary, flex-rigid PCBs provide an ideal combination of flexibility, reliability, miniaturization and performance. Let’s look at some of the common applications that benefit from flex-rigid PCB technology.
Applications of Flex-Rigid PCBs
Here are some typical applications that utilize flexible rigid PCB technology:
1. Consumer Electronics
Consumer electronics like smartphones, tablets and wearables require compact and dynamic PCB solutions. Here are some examples:
- Foldable displays – The flex sections allow displays to fold/bend while interconnects maintain electrical connections.
- Hinges – Flex-rigid PCBs act as a hinge to enable flip phones and laptop lids to open/close smoothly.
- Buttons – Domed mechanical buttons with flex tails allow reliable connections to the main PCB.
- Space savings – Folding flex-rigid PCBs in half allows fitting them into tight enclosures.
2. Medical Electronics
Medical devices impose stringent reliability requirements where flex-rigid PCBs deliver:
- Imaging – Flexible PCB sections allow convenient shaping inside diagnostic imaging equipment like CT and MRI scanners.
- Wearables – Skin-worn health monitoring devices are designed with flex-rigid PCBs that dynamically bend and flex with body movements.
- Implants – Miniature flex-rigid PCBs withstand repeated flexing after being implanted inside the human body.
- Instruments – Laparoscopic surgery tools and endoscopes use flex-rigid PCBs that can snake through the patient’s body.
3. Automotive Electronics
Vehicles utilize flex-rigid PCBs in areas like:
- Dashboards – To conform to curved surfaces and fold into tight spaces behind the dashboard.
- Moving parts – Headlamps, doors, steering systems use flex-rigid PCBs to interconnect across moving joints.
- Sensors – Flexible tails connect rigid sensor PCBs installed in various parts of the vehicle body.
- High temp – Withstand under-the-hood high temperature environments.
4. Aerospace and Defense
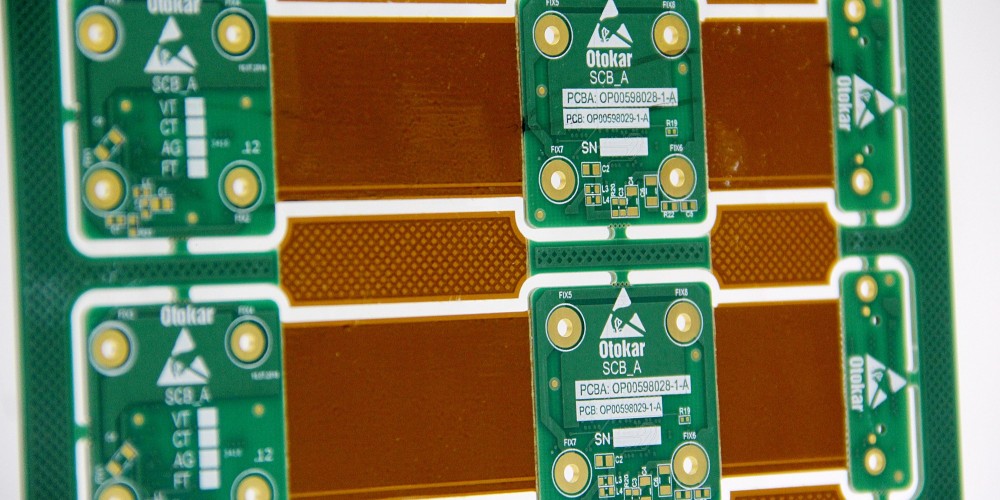
Military systems commonly use rigid-flex PCBs for:
- Missiles – Interconnect electronics across the flexing missile airframe.
- Avionics – Ruggedized electronics for aircraft flight and control systems.
- Spacecraft – Flex-rigid PCBs withstand the rigors of space travel and landing shocks.
- Wearables – Helmet mounted displays, electronics, and communications.
Flex-Rigid PCB Design Considerations
Designing an optimal flex-rigid PCB requires paying attention to the following factors:
- Layer stackup – Optimal arrangement of flex and rigid layers to meet flexibility, rigidity, and interconnect requirements. Rigid layers on outside provide protection.
- Flex-rigid interfaces – Careful design of intersections between rigid and flex to avoid stresses. Strategic placement and number of layers.
- Conductor width – Wide copper tracks on flex layers for reliability. Narrow conductors prone to cracking.
- Bending radius – Allow sufficient bend radius for flex areas based on minimum specifications.
- Reliability – Validate the design to withstand target minimum bend cycles and vibration levels.
- Adhesives – Use high performance adhesives like acrylic or epoxy to strongly bond flex and rigid sections.
- Stiffeners – Additional reinforcement around cutouts and at critical stress points.
With careful design considerations and validation, flex-rigid PCBs can withstand millions of bend cycles and provide long service life.
Flex-Rigid PCB Manufacturing
Manufacturing flexible rigid PCBs requires specialized processes and equipment. Here is a brief overview:
- Materials for rigid and flex layers are prepared based on design needs.
- Rigid layers are fabricated using conventional PCB processes.
- Thin flexible layers are produced by laminating copper to polyimide films.
- Rigid and flex layers are bonded together using adhesive sheets.
- Registration is critical to align layers and interconnects.
- Etching and component assembly follows regular PCB production process.
- Final testing validates bending performance and electrical functionality.
Rigid-flex PCB production requires expertise across both rigid and flex PCB domains. Working with a manufacturer experienced in both technologies is highly recommended.
Flex-Rigid PCB vs Rigid PCBs
Here is a comparison between flex-rigid PCBs and their regular rigid PCB counterparts:
Parameter | Flex-Rigid PCB | Rigid PCB |
---|---|---|
Flexibility | Has flexible sections for bending/folding | Completely rigid with no flexibility |
Layers | Can have 10 or more layers by combining rigid and flex | Typically 2 to 8 layers |
Miniaturization | Folds into small spaces. Enables smaller product sizes. | Larger overall footprint |
Reliability | Rigid sections provide stability and prevent flexing failures | Susceptible to vibrations and drops |
Design | Partitions circuits across rigid and flex areas. Allows optimized performance. | Constrained to a completely rigid board |
Cost | Higher than rigid PCBs due to specialized materials and processes | Lower cost due to standard materials and high volumes |
In summary, flex-rigid PCBs provide an ideal combination of flexibility, reliability, miniaturization and performance compared to regular rigid PCBs. The additional costs are justified for many applications.
Flexible Rigid PCBs – Frequently Asked Questions
Here are some common questions about flexible rigid PCB technology:
Q1. How many bend cycles can a flex-rigid PCB withstand?
This depends on the materials and construction. Typical flex-rigid PCBs can withstand 50,000 to 100,000 dynamic bend cycles before failure. With robust design, special materials, and rigorous testing, several million bend cycles can be achieved.
Q2. Can components be assembled on the flex area of the PCB?
Yes, but components in the flex area need to be small and lightweight. Typical components include chip resistors and capacitors, LEDs and small connectors. Heavier components can cause stresses and cracks.
Q3. What are some typical layer counts for flex-rigid PCBs?
Simple designs may have 1-2 flex layers combined with 2-4 rigid layers. Complex designs can have 5-8 rigid layers integrated 2-3 flex layers. Totals of 8 to 12 layers are typical for most applications.
Q4. How small can the bend radius be designed?
The bend radius is generally determined by the flex layer material. Typical polyimide film can be bent to 0.5mm radius. Special flex materials like polyester allow even tighter 0.05mm bend radii.
Q5. Can flex-rigid PCBs be double sided?
Yes, flex-rigid PCBs can have circuit layers on both sides of the board. Components can also be assembled on both sides. Vias and plated through holes interconnect the layers.
Conclusion
Flexible rigid PCB technology combines the best of rigid and flex PCBs – providing dynamical flexing ability along with mechanical stability and reliability. The folding and 3D shaping abilities of flex-rigid PCBs allow innovative and compact product designs across many industries from consumer electronics to automotive and aerospace applications. With a sound understanding of the design and manufacturing considerations, engineers can harness the benefits of flex-rigid PCB technology for their electronic products.