Introduction
In the world of electronics, safety and reliability are paramount. One critical aspect of ensuring the safety of electronic devices is the flammability rating of the materials used in their construction, particularly the Printed Circuit Boards (PCBs). The 94 V-0 circuit board rating is one of the most widely recognized standards for assessing the flammability of PCB materials. This article delves into the 94 V-0 rating, its significance, testing methods, and implications for PCB design and manufacturing.
Understanding the 94 V-0 Rating
What is the 94 V-0 Rating?
The 94 V-0 rating is a classification under the UL 94 standard, which is developed by Underwriters Laboratories (UL), a global safety certification company. The UL 94 standard evaluates the flammability of plastic materials used in devices and appliances. The “94” refers to the UL 94 standard, and “V-0” is one of the flammability classifications within this standard.
Flammability Classifications
The UL 94 standard includes several flammability classifications, with V-0 being one of the most stringent. The classifications are as follows:
- V-0: The material must stop burning within 10 seconds after two applications of a flame, with no flaming drips allowed.
- V-1: The material must stop burning within 30 seconds after two applications of a flame, with no flaming drips allowed.
- V-2: The material must stop burning within 30 seconds after two applications of a flame, but flaming drips are allowed.
- HB: The material has a horizontal burning rate and is considered less flame-retardant compared to V-0, V-1, and V-2.
Importance of the 94 V-0 Rating
The 94 V-0 rating is crucial for ensuring the safety of electronic devices, particularly in applications where fire hazards are a concern. Devices that meet the 94 V-0 standard are less likely to catch fire and spread flames, thereby reducing the risk of injury and property damage.
Testing Methods for 94 V-0 Rating
Vertical Burning Test
The 94 V-0 rating is determined through a vertical burning test, which involves the following steps:
- Sample Preparation: Specimens of the material are cut to specific dimensions and conditioned at a standard temperature and humidity.
- Mounting: The specimens are mounted vertically in a test chamber.
- Flame Application: A specified flame is applied to the bottom of the specimen for 10 seconds.
- Observation: After the flame is removed, the burning time, flaming drips, and afterglow time are recorded.
- Repeat: The flame application is repeated for a second time, and the observations are recorded again.
Criteria for 94 V-0 Rating
To achieve a 94 V-0 rating, the material must meet the following criteria:
- The material must stop burning within 10 seconds after each flame application.
- No flaming drips are allowed.
- The total afterglow time must not exceed 30 seconds after the second flame application.
Materials and Their Flammability Ratings
Common PCB Materials
PCBs are typically made from materials such as FR-4, CEM-1, and polyimide. Each of these materials has different flammability characteristics:
- FR-4: A widely used PCB material that typically meets the 94 V-0 rating. It is a composite of woven fiberglass cloth with an epoxy resin binder.
- CEM-1: A cheaper alternative to FR-4, often used in single-layer PCBs. It generally meets the 94 V-1 or 94 V-0 rating.
- Polyimide: Known for its high thermal stability and flexibility, polyimide is often used in high-temperature applications. It typically meets the 94 V-0 rating.
Additives and Flame Retardants
To achieve the 94 V-0 rating, manufacturers often add flame retardants to the base materials. Common flame retardants include:
- Halogenated Flame Retardants: These contain elements like bromine or chlorine, which are effective in reducing flammability but can release toxic gases when burned.
- Non-Halogenated Flame Retardants: These are environmentally friendly alternatives that do not release toxic gases but may be less effective in some applications.
Implications for PCB Design and Manufacturing
Design Considerations
When designing a PCB, selecting materials with the appropriate flammability rating is crucial. Here are some key considerations:
- Application Requirements: Determine the flammability requirements based on the application. For example, consumer electronics may require a 94 V-0 rating, while industrial equipment may have different standards.
- Material Selection: Choose materials that meet the required flammability rating and other performance criteria, such as thermal stability, mechanical strength, and electrical properties.
- Layer Stack-up: Ensure that all layers of the PCB, including the core and prepreg, meet the required flammability rating.
Manufacturing Considerations
Manufacturing processes can also impact the flammability rating of the final PCB. Key considerations include:
- Lamination: Proper lamination techniques ensure that the layers are bonded correctly, maintaining the integrity of the flame-retardant properties.
- Drilling and Routing: Precision in drilling and routing prevents damage to the flame-retardant layers, which could compromise the flammability rating.
- Surface Finish: The choice of surface finish can affect the flammability rating. For example, some finishes may introduce additional flammability risks.
Compliance and Certification
Achieving and maintaining the 94 V-0 rating requires compliance with UL standards and obtaining the necessary certifications. This involves:
- Testing: Conducting the vertical burning test and other relevant tests to verify the flammability rating.
- Documentation: Maintaining detailed records of material specifications, test results, and manufacturing processes.
- Audits: Undergoing periodic audits by certification bodies to ensure ongoing compliance.
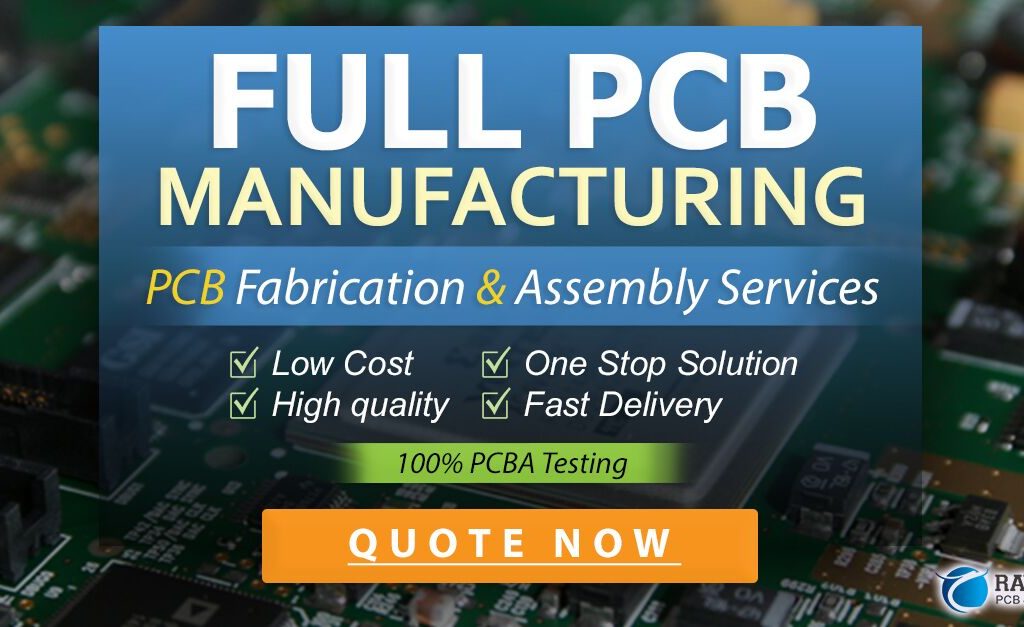
Advantages of 94 V-0 Rated PCBs
Enhanced Safety
The primary advantage of 94 V-0 rated PCBs is enhanced safety. These PCBs are less likely to catch fire and spread flames, reducing the risk of injury and property damage.
Regulatory Compliance
Many industries and regions have stringent regulations regarding the flammability of electronic devices. Using 94 V-0 rated materials ensures compliance with these regulations, facilitating market access and reducing legal risks.
Consumer Confidence
Devices that meet high safety standards, such as the 94 V-0 rating, can enhance consumer confidence and brand reputation. Consumers are more likely to trust and purchase products that prioritize safety.
Challenges and Limitations
Cost
Materials that meet the 94 V-0 rating, especially those with non-halogenated flame retardants, can be more expensive than standard materials. This can increase the overall cost of the PCB.
Environmental Concerns
Halogenated flame retardants, while effective, can release toxic gases when burned, posing environmental and health risks. Non-halogenated alternatives are available but may have limitations in terms of effectiveness and cost.
Performance Trade-offs
Some flame-retardant additives can affect the mechanical and electrical properties of the PCB material. Designers must balance flammability requirements with other performance criteria.
Case Studies
Case Study 1: Consumer Electronics
Application: Smartphone PCB
Requirements:
- High safety standards
- Compact design
- Cost-effectiveness
Solution:
The smartphone PCB uses FR-4 material with a 94 V-0 rating. The material provides the necessary flame retardancy while meeting the compact design and cost requirements.
Case Study 2: Industrial Control Systems
Application: Industrial Control Unit PCB
Requirements:
- High reliability
- Compliance with industrial safety standards
- Thermal stability
Solution:
The industrial control unit PCB uses polyimide material with a 94 V-0 rating. The material offers high thermal stability and meets the stringent safety requirements of industrial applications.
Case Study 3: Automotive Electronics
Application: Automotive Control Module PCB
Requirements:
- High safety standards
- Resistance to harsh environments
- Long-term reliability
Solution:
The automotive control module PCB uses FR-4 material with a 94 V-0 rating and additional environmental protection coatings. The material ensures safety and reliability in the demanding automotive environment.
Conclusion
The 94 V-0 circuit board rating is a critical standard for ensuring the safety and reliability of electronic devices. By understanding the significance of this rating, the testing methods involved, and the implications for PCB design and manufacturing, engineers and designers can make informed decisions that enhance the safety and performance of their products. While there are challenges and limitations associated with achieving the 94 V-0 rating, the benefits in terms of safety, regulatory compliance, and consumer confidence make it a worthwhile investment for many applications. Whether designing consumer electronics, industrial control systems, or automotive electronics, selecting materials with the appropriate flammability rating is essential for creating robust and reliable PCBs