In the realm of high-speed electronics and telecommunications, signal integrity (SI) is a critical factor that determines the performance and reliability of electronic systems. As data rates continue to increase, the physical properties of materials used in printed circuit boards (PCBs) and interconnects become increasingly important. One such property that has garnered significant attention is the surface roughness of copper, which is widely used as a conductive material in PCBs and transmission lines. This article delves into the relationship between copper roughness and signal integrity, exploring the underlying mechanisms, measurement techniques, and mitigation strategies.
Introduction to Signal Integrity
Signal integrity refers to the ability of an electronic system to transmit signals without significant distortion or loss. In high-speed digital and analog circuits, maintaining signal integrity is essential to ensure accurate data transmission, minimize errors, and prevent system failures. Key factors that affect signal integrity include impedance matching, crosstalk, reflections, and losses due to conductor and dielectric materials.
As signal frequencies increase into the gigahertz range, the skin effect becomes more pronounced. The skin effect causes current to flow primarily near the surface of a conductor, making the surface properties of the conductor, such as roughness, increasingly relevant to signal integrity.
Copper in PCBs and Interconnects
Copper is the most commonly used conductive material in PCBs and interconnects due to its excellent electrical conductivity, thermal conductivity, and cost-effectiveness. However, the surface of copper is rarely perfectly smooth. During the manufacturing process, copper foils are often treated to enhance adhesion to the PCB substrate, resulting in varying degrees of surface roughness.
Copper roughness is typically characterized by parameters such as Ra (average roughness), Rz (mean roughness depth), and Rq (root mean square roughness). These parameters quantify the deviations of the surface from an ideal flat plane.
The Impact of Copper Roughness on Signal Integrity
The roughness of copper surfaces affects signal integrity through several mechanisms:
- Increased Conductor Losses: Rough surfaces increase the effective path length of current flow, leading to higher resistive losses. This is particularly significant at high frequencies, where the skin effect confines current to a thin layer near the surface.
- Skin Effect and Proximity Effect: The skin effect causes current to concentrate near the surface of the conductor, while the proximity effect causes current to redistribute due to the influence of nearby conductors. Rough surfaces exacerbate these effects, further increasing losses.
- Impedance Variations: Roughness can cause localized variations in the cross-sectional geometry of transmission lines, leading to impedance mismatches and reflections that degrade signal quality.
- Dielectric Losses: In microstrip and stripline configurations, the electric field extends into the dielectric material. Rough copper surfaces can increase the effective dielectric constant and losses in the surrounding material.
- Dispersion: Roughness can introduce frequency-dependent variations in the propagation characteristics of signals, leading to dispersion and signal distortion.
Quantifying the Effect of Roughness
To understand and mitigate the impact of copper roughness, it is essential to quantify its effect on signal integrity. Several models and techniques have been developed for this purpose:
- Huray Model: The Huray model is a widely used approach for characterizing the impact of roughness on conductor losses. It treats the rough surface as a collection of hemispherical protrusions and calculates the effective surface area and resistance.
- Hammerstad Model: This empirical model relates the roughness parameters (Ra or Rz) to the increase in conductor losses. It is commonly used in PCB design tools to account for roughness effects.
- Measurement Techniques: Techniques such as profilometry, atomic force microscopy (AFM), and scanning electron microscopy (SEM) are used to measure surface roughness. These measurements are then used as inputs for simulation and modeling.
- Simulation Tools: Electromagnetic simulation tools, such as ANSYS HFSS and CST Studio Suite, enable engineers to model the effects of roughness on signal integrity and optimize designs accordingly.
Case Studies and Experimental Results
Numerous studies have investigated the relationship between copper roughness and signal integrity. Some key findings include:
- Frequency-Dependent Losses: Experiments have shown that the impact of roughness on conductor losses increases with frequency. At frequencies above 10 GHz, roughness can account for a significant portion of total losses.
- Comparison of Roughness Types: Different types of copper foils, such as rolled annealed (RA) and electrodeposited (ED) foils, exhibit varying degrees of roughness. ED foils, which are commonly used in PCBs, tend to have higher roughness and greater losses compared to RA foils.
- Effect on Eye Diagrams: In high-speed digital systems, roughness can degrade eye diagrams by reducing eye height and increasing jitter. This can lead to higher bit error rates (BER) and reduced system performance.
- Impact on Differential Signals: Differential signaling, which is widely used in high-speed interfaces such as USB and PCIe, is also affected by roughness. Asymmetric roughness on paired traces can lead to mode conversion and common-mode noise.
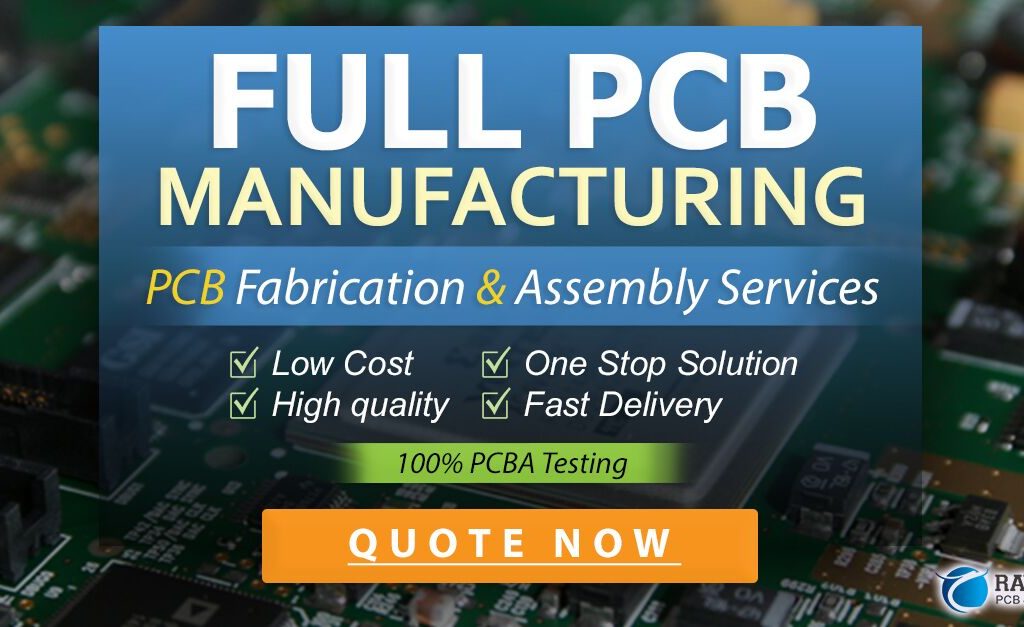
Mitigation Strategies
To minimize the impact of copper roughness on signal integrity, several strategies can be employed:
- Smoother Copper Foils: Using copper foils with lower roughness, such as RA foils or advanced low-profile foils, can reduce conductor losses and improve signal integrity.
- Surface Treatments: Chemical and mechanical treatments can be used to reduce surface roughness. For example, planarization processes can smooth the copper surface before applying the dielectric layer.
- Design Optimization: Careful design of transmission lines, including trace geometry, spacing, and impedance matching, can help mitigate the effects of roughness.
- Advanced Materials: Using low-loss dielectric materials with stable properties over a wide frequency range can reduce the overall impact of roughness on signal integrity.
- Simulation and Modeling: Incorporating roughness models into simulation tools allows engineers to predict and optimize the performance of high-speed interconnects.
Future Trends and Challenges
As data rates continue to increase, the impact of copper roughness on signal integrity will become even more significant. Emerging technologies, such as 5G, automotive radar, and high-performance computing, demand ever-higher frequencies and tighter tolerances. Addressing the challenges posed by roughness will require ongoing research and innovation in materials, manufacturing processes, and design methodologies.
Some key areas of focus include:
- Advanced Roughness Models: Developing more accurate and comprehensive models to predict the impact of roughness on signal integrity.
- Novel Materials: Exploring alternative conductive materials with lower roughness and better high-frequency performance.
- Manufacturing Innovations: Improving manufacturing processes to produce smoother copper surfaces and more consistent dielectric properties.
- Integration with Other Effects: Considering the interplay between roughness and other factors, such as temperature, humidity, and mechanical stress, in the design and analysis of high-speed interconnects.
Conclusion
The roughness of copper surfaces plays a critical role in determining the signal integrity of high-speed electronic systems. As data rates continue to rise, understanding and mitigating the effects of roughness will be essential to ensure the performance and reliability of modern electronics. Through a combination of advanced modeling, innovative materials, and optimized design practices, engineers can overcome the challenges posed by copper roughness and pave the way for the next generation of high-speed technologies.
By addressing this often-overlooked aspect of PCB and interconnect design, the industry can achieve significant improvements in signal integrity, enabling faster, more efficient, and more reliable electronic systems. The study of copper roughness and its impact on signal integrity is not just a technical challenge but also an opportunity to push the boundaries of what is possible in the world of high-speed electronics.