Introduction
Printed circuit boards (PCBs) are essential components in nearly all modern electronic devices. They provide the physical structure and electrical connections between electronic components. While the most common type of PCB uses rigid FR-4 fiberglass as the substrate material, polyimide PCBs offer superior thermal and mechanical performance for demanding applications.
Polyimide is a high-performance polymer material known for its excellent thermal stability, chemical resistance, and mechanical properties. Rigid polyimide PCBs leverage these material advantages to enable smaller, lighter, and more reliable electronic circuits. This article provides a comprehensive overview of rigid polyimide PCB technology, manufacturing processes, applications, pros and cons, and future trends.
What is Rigid Polyimide PCB?
A rigid polyimide PCB uses polyimide as the dielectric insulating material or substrate instead of traditional FR-4 fiberglass. The substrate gives the PCB its mechanical structure while also electrically isolating the layered copper traces. Polyimide has superior thermal performance with a glass transition temperature around 400°C compared to only 150°C for standard FR-4.
Rigid means the PCB is self-supporting and does not flex like a flex PCB. The rigid structure allows intricate routing and stacking of multiple circuit layers. Rigid polyimide PCBs typically have between 2 and 30 layers of copper interconnects. They can also incorporate blind and buried vias for vertical connections between layers.
Here are some key properties and characteristics of rigid polyimide PCBs:
- Excellent thermal performance up to 300°C
- Low thermal expansion coefficient similar to copper
- High tensile strength and modulus
- Excellent chemical resistance
- Low moisture absorption
- Good dielectric properties
- High frequency capability
- Can be made very thin (<100 um) but structurally rigid
Manufacturing Process
Rigid polyimide PCBs follow a similar fabrication process to conventional FR-4 PCBs. The major difference is in the substrate material layer.
Substrate Preparation
The process starts with liquid polyimide precursor being cast or coated onto a metal drum or belt. The polyimide film is cured at high temperature into a solid sheet form. The fully cured polyimide film is cut into sheets for lamination.
Lamination
Layers of polyimide dielectric film are stacked alternating with copper foil layers. The stack is laminated under heat and pressure to form a solid bonded multilayer board. The bonding occurs as the partially cured polyimide layers fuse together.
Drilling
The laminated board then undergoes drilling to create holes for electrical vias. High precision laser or mechanical drilling forms thousands of via holes precisely positioned for the circuit layout.
Metallization
The walls of the via holes are plated with copper using electroless and electrolytic plating processes. This electrically connects the copper layers vertically through the board.
Photolithography
Next, photoresist is coated on the outer copper layers and imaged using photolithography techniques. The photoresist acts as a mask to selectively etch away unwanted copper, leaving behind the desired circuit trace pattern.
Testing and Finishing
The completed boards undergo electrical testing before final finishing steps such as solder mask coating, silkscreen printing, edge connectors, and surface finishes.
Applications and Benefits
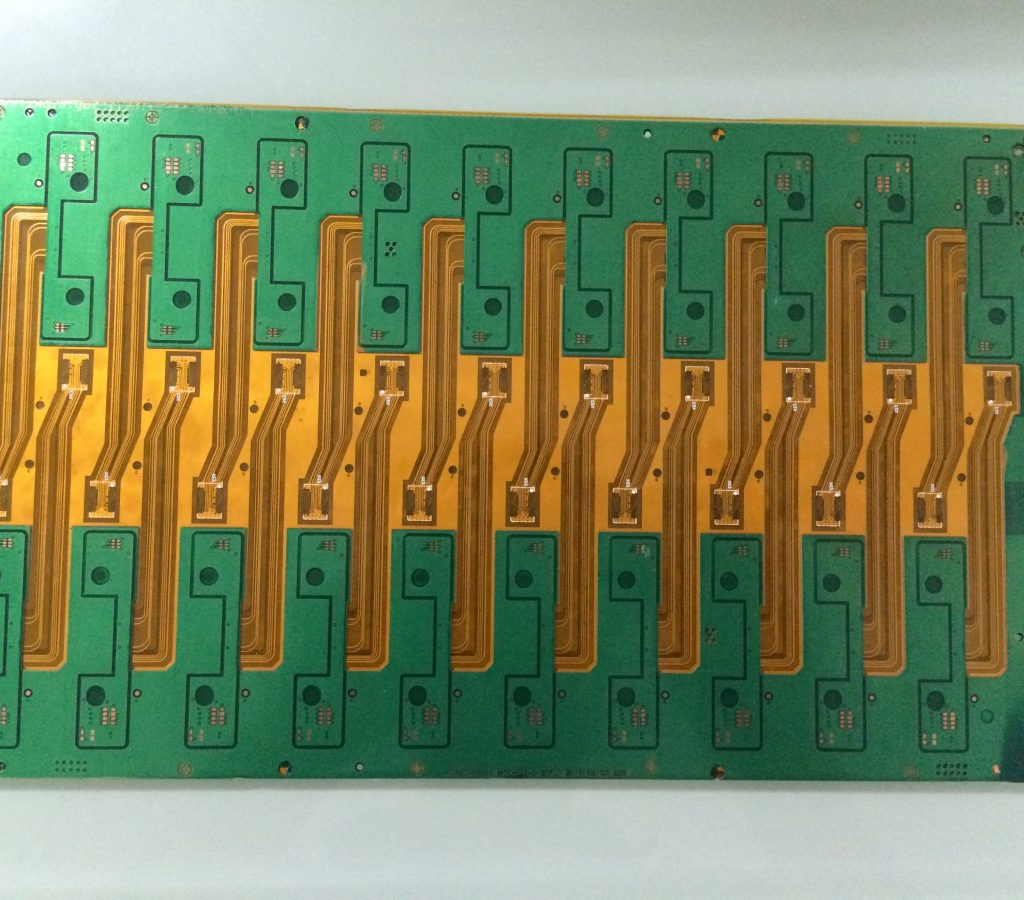
The unique properties of polyimide make rigid polyimide PCBs ideal for many demanding applications:
- Aerospace and aviation electronics
- High-temperature electronics
- Military and defense electronics
- Downhole drilling and exploration
- Medical electronics and implants
- Automotive engine control units
Here are some of the major benefits provided by rigid polyimide PCBs:
Thermal Performance – The excellent heat resistance allows electronics to operate at very high temperatures exceeding 200°C. Polyimide has lower thermal expansion to match copper interconnects.
Miniaturization – Thin polyimide substrates down to 25 um enable denser circuits and component packaging. Complex multilayer boards are possible.
Light Weight – Polyimide has a lower density than FR-4 allowing thinner, lighter weight PCBs ideal for aerospace applications.
Reliability – The outstanding mechanical and chemical properties improve reliability and lifetime in demanding environments.
High Frequency – Low dielectric loss allows polyimide PCBs to support high frequency microwave and mmWave applications.
Pros and Cons
Here is a summary of the key pros and cons to consider when using rigid polyimide PCBs:
Pros:
- High thermal performance
- Excellent mechanical properties
- Low moisture absorption
- Good high frequency properties
- High reliability in harsh environments
Cons:
- More expensive than FR-4 PCBs
- Exotic material requires special handling
- Limited size availability
- Advanced processes often required
- Not easy to rework or modify
Design Considerations
Rigid polyimide PCBs enable new design possibilities, but also have some unique design restrictions to consider:
- The high Young’s modulus requires managing board warpage and stress
- Matching coefficients of thermal expansion (CTE) is critical
- Maximum process temperature often 350°C or higher
- Allowable glass transition temperature may limit some component mounting
- Effects of moisture absorption on electrical performance
- High frequency behaviour influenced by anisotropy
- Limited substrate thickness availability (25-250 um typical)
Careful thermal and mechanical analysis is recommended when designing rigid polyimide PCBs.
Future Trends
Rigid polyimide PCBs currently fill niche applications, but continued material and process improvements may expand their broader adoption:
- Lower cost manufacturing as volumes increase
- Improved high temperature component integration
- Hybrid boards with high density interconnects
- Advanced cooling integration within boards
- Embedded passives and sensors using printed polymer thick films
- 5G communications infrastructure applications
- Leveraging high strength-to-weight for UAVs and satellites
- Optoelectronics integration with polyimide waveguides
With expanded capabilities, rigid polyimide PCBs could displace standard FR-4 PCBs in many applications that value the superior thermal and mechanical performance.
Conclusion
Rigid polyimide PCB technology enables lightweight, high-performance, and reliable electronics for extreme environment applications. Polyimide’s outstanding thermal stability and mechanical properties help satisfy the increasing demands of next-generation electronic devices. With continued innovation in materials, design, and manufacturing, rigid polyimide PCBs have a bright future in high-speed communications, aerospace, automotive, and other challenging applications.
FAQs
What is polyimide?
Polyimide is a high-performance polymer material renowned for its excellent thermal, mechanical, and chemical properties. The fully cured polyimide polymer exhibits high heat and chemical resistance.
What are some examples of polyimide trade names?
Some common polyimide trade names include Kapton (DuPont), Apical (Kaneka), UPILEX (Ube), and Upilex-S (ISE Electronics).
How are polyimide PCBs different from FR-4 PCBs?
Polyimide PCBs can operate at much higher temperatures (>300°C) compared to FR-4 PCBs (~150°C max). Polyimide also has greater mechanical strength, chemical inertness, and high frequency capabilities.
What are some typical applications for rigid polyimide PCBs?
Common applications include aerospace, military, automotive, oil/gas drilling, medical implants, and high-speed communications. Polyimide properties help meet demands of high-temperature, lightweight, and reliable electronics.
What are some challenges when working with polyimide PCBs?
Polyimide PCBs have more limited size availability, higher cost, and often require advanced manufacturing processes. The material is also difficult to rework or modify after fabrication. Careful design is needed to manage thermal expansion stresses.