Introduction
Printed circuit boards (PCBs) are essential components in almost all modern electronic devices. As products get smaller and more complex, flex PCBs have become increasingly common. Flex PCBs offer a durable yet flexible platform for routing traces between components.
For prototypes and new product development, being able to quickly iterate on flex PCB designs is critical. Long lead times from fabrication shops can slow down development and delay time-to-market. This is where quick turn flex PCB fabrication services come in.
In this comprehensive guide, we’ll cover everything you need to know about quick turn flex PCBs including:
- What are flex PCBs and why use them?
- Benefits of quick turn flex PCB fabrication
- How the quick turn process works
- Design considerations and guidelines
- How to choose a quick turn flex PCB manufacturer
- Costs and lead times to expect
- QA, testing, and qualifications for flex PCBs
- Applications and examples
Let’s get started!
What are Flex PCBs and Why Use Them?
A flex PCB uses a flexible polyimide substrate to mount components and route traces between them. The circuits can flex and bend while still maintaining electrical connectivity. Common flex PCB materials include polyimide (Kapton), polyester (PET), and PEN.
Compared to rigid PCBs, flex PCBs provide:
- Increased shock/vibration resistance – flex circuits can withstand repeated bending
- Tighter bend radii – can fold into tight spaces
- Weight reduction – very thin and lightweight
- 3D assembly – can conform to various form factors
- Improved aesthetics – no visible PCB edges
These characteristics make flex PCBs well-suited for:
- Consumer electronics – cell phones, wearables, VR/AR
- Automotive – sensors, engine/transmission control
- Medical – hearing aids, patient monitoring
- Industrial – robotics, aviation and aerospace
Flex PCBs allow designers to fit more features into less space while maintaining reliability. The circuits can dynamically flex and move in harmony with the product itself.
Benefits of Quick Turn Flex PCB Fabrication
For prototypes and short-run manufacturing, producing flex PCBs with a quick turn service offers important advantages:
Faster Iteration: Making design tweaks and adjustments is much easier with 1-5 day turnaround. No need to wait weeks for a revised PCB.
Accelerate Development: Getting boards in hand faster lets you validate concepts and conduct testing sooner.
Lower Costs: Shorter runs with quick turn shops costs less per board. Avoid expenses of long fabrication cycles.
On-Demand Flexibility: Get your flex PCBs produced when you need them with flexible ordering. No need to order large inventories upfront.
Higher Mix: Support high mix production with fast changeovers between different designs.
Bridge Prototyping: Easily transition from prototyping to pre-production using the same fabrication process.
For products with short life cycles, like consumer electronics, quick turn PCB production improves the ability to respond to market needs.
How Quick Turn Flex PCB Fabrication Works
Specialized manufacturers offer rapid fabrication of flex PCBs with very short lead times. Here is an overview of the quick turn process:
1. Design File Submission
After designing the flex PCB, the Gerber and drill files are uploaded to the quick turn company’s website. Include any special notes or requirements.
2. Engineering Review
Experienced engineers will review the design files for manufacturability and potential issues. Feedback is provided if any design changes are necessary.
3. Fabrication and Materials
Once approved, fabrication begins with automated production lines. Polyimide flex materials come in sheets or rolls with copper laminated on one or both sides.
4. Imaging and Etching
Using photolithography, the circuit layout is imaged onto the copper layers. Chemical etching then removes unwanted copper to leave the desired traces and pads.
5. Automated Assembly
Surface mount and through hole components can be assembled using pick and place and solder reflow. Automation enables high mix production.
6. Testing and QA
Finished boards undergo comprehensive testing and inspection checking for continuity, functionality, and defects.
7. Shipping
The flex PCBs ship out in 1-5 days for worldwide delivery. For prototyping, boards can ship next day.
This streamlined and automated process minimizes lead time to enable ultra fast delivery of flex circuits, even for small batches.
Design Guidelines for Quick Turn Flex PCBs
To ensure your flex PCB design files can be quickly fabricated follow these guidelines:
- Use 1 oz (35 μm) copper or thicker to allow for PCB bending. Thinner copper may crack.
- Minimum trace/space is 0.003″ (0.076 mm) but 0.005″ (0.127 mm) is preferred.
- Minimum hole size is 0.012″ (0.30 mm)
- Avoid acute angles (<90°) between traces and pads which can crack during flexing. Round traces and use tear drops.
- Include cross-hatched copper fills for stiffening and heat dissipation in areas without traces.
- Remove all silkscreen and outline layers to eliminate additional processing steps.
- No more than one connector edge per side to allow panelization of circuits.
- Add radius corners on board outlines to reduce points of stress.
- Eliminate internal cutouts and slots if possible. Use routing paths instead.
While advanced HDI technology enables very dense flex PCBs, avoid untested layouts and stick with minimum spacing and dimensions at first. Work with your flex PCB manufacturer early in the design process to ensure your board can be fabricated with quick turn.
Choosing A Quick Turn Flex PCB Manufacturer
Choosing the right quick turn partner ensures you get high quality flex PCBs when you need them. Here are important factors to consider:
Speed and Lead Times: Look for guaranteed lead times of 5 days or less, with 1-2 day rush services. Manufacturers with local facilities can often deliver fastest.
Quality Processes: Seek ISO certified fabricators with well controlled processes. They should inspect 100% of boards and provide detailed test reports.
Flex Circuit Experience: Choose a shop with several years of experience and expertise in flexible PCBs specifically. They should provide helpful design reviews.
Production Scale: Ensure they can handle prototype quantities of just a few boards as well as mid-volume production up to ~10,000 boards.
Design File Support: Check that they accept multiple CAD formats like Altium, Cadence, and Eagle. Gerber import capability is also critical.
Assembly Services: Many will provide part sourcing, soldering, and full turnkey assembly for faster completion of prototypes.
Customer Service: Look for great communication during the design, quoting, and production process. It shows they focus on customer satisfaction.
By partnering with the right quick turn manufacturer you gain access to their specialized expertise and resources for delivering flex PCBs fast.
Costs and Lead Times for Quick Turn Flex PCBs
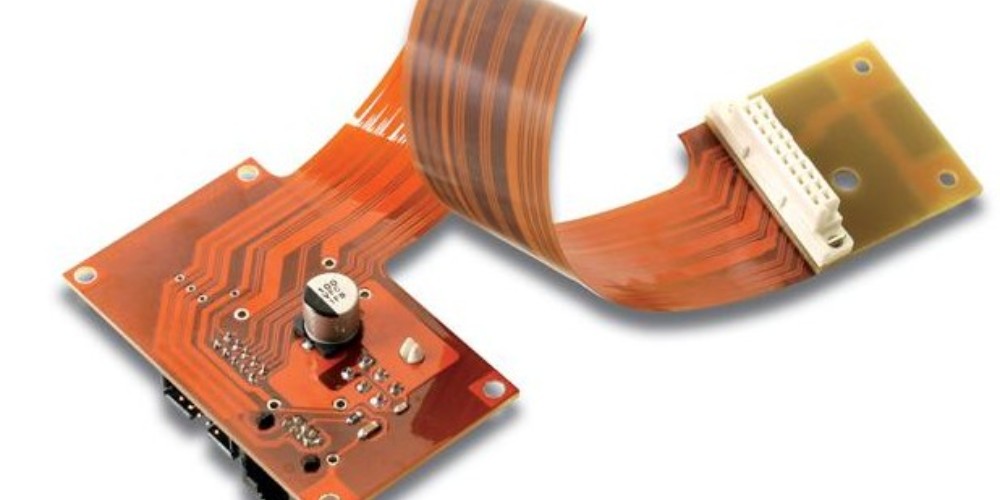
Here are typical costs and lead times when ordering flex PCB prototypes or small batches from a quick turn service:
Quantity | Lead Time | Price Per Board |
---|---|---|
1-10 boards | 24-48 hrs | $200 – $500 |
10-25 boards | 2-5 days | $100 – $300 |
25-100 boards | 5 days | $75 – $250 |
100-500 boards | 5-10 days | $50 – $150 |
500-1,000 boards | 10-15 days | $30 – $100 |
1,000-10,000 boards | 15-20 days | $15 – $50 |
- NRE and tooling charges are usually waived for orders under 100 boards.
- Lead times are after design files are approved and ready for manufacturing.
- Prices vary based on size, layer count, and other requirements like stiffeners or coverlay.
While per board pricing is higher for low volumes, for prototyping the total cost is affordable. Compared to waiting weeks, quick turn shops offer huge time savings.
Turnaround gets quicker the more the manufacturer understands your design requirements upfront. Work closely with engineering staff during the design stage to maximize speed.
QA and Qualification Testing
Ensuring quality requires robust testing and inspection at multiple stages of the quick turn flex PCB fabrication process:
Pre-Production Qualification: Prior to full production, initial boards undergo qualification testing like:
- Netlist testing – validates PCB connectivity matches schematics
- Visual inspection – checks for material/fabrication defects
- AOI (Automated Optical Inspection) – detects faults in trace widths, registration, etc
- Flying probe – verifies electrical connectivity on bare boards
- ICT (In Circuit Test) – tests analog/digital circuitry function
- Burn-in testing – screens for early life failures by stressing components
In-Process Quality: During PCB production, quality checkpoints include:
- Incoming material inspection – verifies flex substrate quality
- AOI after etching, legend printing, solder mask steps
- 100% netlist verification ensures accuracy
Outgoing Quality Control: Every shipped board goes through:
- Final visual inspection of solder joints, board defects
- ICT tests based on test coverage determined by engineering
- AOI and x-ray inspection for hidden layer faults
- Dimensional checks using automated optical measuring systems
Test Documentation: Extensive reports detailing test results should be provided. Used for evaluating and improving processes.
Following established qualification and quality procedures is critical even during quick turn fabrication to achieve high yields and reliability.
Flex PCB Applications Showcasing Quick Turn Benefits
Here are some examples of products using quick turn flex PCB prototyping and pre-production:
Wearable Devices: Using 1-2 day turnaround allows wearable tech companies to quickly test different flex circuit sizes, shapes, and layouts. Finding the optimal mechanical fit faster.
Consumer Electronics: For handheld consumer products, flex circuitry integrates tightly around inside the enclosure. Engineers can iterate on positioning of components and connectors.
Automotive Sensors: Auto suppliers use rapid flex PCB turns to adjust position and shape of sensor boards for prototyping placement.
Medical Electronics: Short turnaround allows designers of patient monitoring devices or implants to evaluate and optimize different flex circuit materials and constructions.
Industrial Hardware: Equipment makers produce customized control boards unique to each machine configuration by uploading new designs daily for quick shipping.
IoT Devices: For streamlined IoT devices, quick turn services help identify the optimal combination of thinness, flexibility, and sensor inputs needed during development.
The ability to quickly get flex PCB prototypes and small batches accelerates innovation for new products in many markets.
Frequently Asked Questions
Here are answers to some common questions about quick turn flex PCB fabrication:
How many flex layer can you get with quick turn?
Typically 1-6 layers are possible, though over 4 layer will have longer lead times. Keep layer counts minimal during early prototyping.
What are the minimum and maximum quantity I can order?
Any quantity from 1 board up is possible. 10-25 boards is ideal for prototyping before moving to ~100 boards for field testing and pre-production.
What are the typical substrate thicknesses and sizes?
Polyimide thickness from 25 to 125 micron are common. Maximum panel sizes are usually 9 x 12 inches but some shops can go bigger.
Can I include stiffeners and coverlay materials?
Yes, but that may add 1-2 days. Keep construction simple during early iteration. These can be added later as the design is finalized.
Can you do assembled boards with components?
Many quick turn shops offer assembly of both SMT and through hole parts. Preferential pricing on components helps with prototyping cost.
Conclusion
Quick turn flex PCB fabrication enables the rapid design iteration critical for new product development. Fast prototype turns and small batch circuit production accelerate time-to-market while reducing development expenses. By partnering with a specialist manufacturer, innovators can have high quality flex PCBs in their hands in just 1-5 days.