1. Overview of PCB Design
Printed Circuit Board (PCB) design is a critical aspect of modern electronics engineering. It involves the creation of a layout that connects various electronic components to form a functional circuit. PCBs are used in almost all electronic devices, from simple gadgets like calculators to complex systems like computers and smartphones. The design process requires a combination of technical knowledge, creativity, and precision to ensure that the final product meets the desired specifications and functions reliably.
1.1 What is a PCB?
A PCB is a flat board made of insulating material, typically fiberglass, with conductive pathways etched or printed onto its surface. These pathways, known as traces, connect different components such as resistors, capacitors, integrated circuits (ICs), and connectors. The primary purpose of a PCB is to provide a stable and organized platform for mounting and interconnecting electronic components.
1.2 Importance of PCB Design
The design of a PCB is crucial because it directly impacts the performance, reliability, and manufacturability of the electronic device. A well-designed PCB ensures that the circuit functions as intended, minimizes signal interference, and can be efficiently manufactured. Poor PCB design, on the other hand, can lead to issues such as signal degradation, overheating, and manufacturing defects, which can compromise the functionality and longevity of the device.
1.3 Evolution of PCB Design
PCB design has evolved significantly since its inception in the early 20th century. Early PCBs were simple, single-layer boards with limited functionality. As electronic devices became more complex, the need for multi-layer PCBs with higher component density arose. Today, PCB design involves advanced techniques such as high-speed signal routing, impedance matching, and thermal management, driven by the demands of modern electronics.
2. Key Components of a PCB
Understanding the key components of a PCB is essential for effective design. These components include:
2.1 Substrate
The substrate is the base material of the PCB, typically made of fiberglass (FR4), which provides mechanical support and electrical insulation. The choice of substrate material depends on factors such as the operating environment, thermal requirements, and electrical properties.
2.2 Copper Layers
Copper layers are laminated onto the substrate to form the conductive pathways or traces. The number of copper layers varies depending on the complexity of the circuit. Single-layer PCBs have one copper layer, while multi-layer PCBs can have several layers, each separated by insulating material.
2.3 Solder Mask
The solder mask is a protective layer applied over the copper traces to prevent oxidation and short circuits. It also provides insulation and defines the areas where solder can be applied during component assembly. The solder mask is typically green, but other colors are also used for aesthetic or functional purposes.
2.4 Silkscreen
The silkscreen is a layer of text and symbols printed on the PCB to indicate component placement, reference designators, and other important information. It aids in the assembly and debugging process by providing visual guidance.
2.5 Vias
Vias are small holes drilled through the PCB to connect traces on different layers. They can be through-hole vias, which go through the entire board, or blind and buried vias, which connect specific layers without penetrating the entire board.
2.6 Pads
Pads are the exposed areas of copper where components are soldered to the PCB. They come in various shapes and sizes, depending on the type of component and the soldering method used.
- PCB Design Process
The PCB design process involves several stages, each requiring careful planning and execution. The main stages are:
3.1 Schematic Design
The schematic design is the first step in the PCB design process. It involves creating a graphical representation of the circuit using symbols for components and lines to represent connections. The schematic serves as a blueprint for the PCB layout and is used to verify the circuit’s functionality before proceeding to the physical design.
3.1.1 Component Selection
Selecting the right components is crucial for the success of the PCB design. Factors to consider include the electrical characteristics, size, cost, and availability of the components. The chosen components must meet the circuit’s requirements and be compatible with the PCB layout.
3.1.2 Schematic Capture
Schematic capture is the process of entering the circuit design into a computer-aided design (CAD) tool. The CAD tool allows the designer to place components, draw connections, and annotate the schematic with reference designators and other information.
3.2 PCB Layout
The PCB layout is the physical representation of the circuit, where components are placed on the board, and traces are routed to connect them. The layout must consider factors such as signal integrity, thermal management, and manufacturability.
3.2.1 Component Placement
Component placement is a critical aspect of PCB layout. The goal is to arrange components in a way that minimizes trace lengths, reduces signal interference, and ensures efficient heat dissipation. Components should be placed according to their functional relationships, with high-speed components located close to each other to minimize signal delay.
3.2.2 Routing
Routing involves drawing the traces that connect the components on the PCB. The routing process must consider factors such as signal integrity, impedance matching, and electromagnetic compatibility (EMC). High-speed signals require careful routing to avoid issues such as crosstalk and signal reflection.
3.2.3 Design Rules Check (DRC)
A Design Rules Check (DRC) is performed to ensure that the PCB layout complies with the design rules and constraints. The DRC checks for issues such as minimum trace width, clearance between traces, and proper via placement. Any violations must be corrected before proceeding to the next stage.
3.3 Simulation and Verification
Simulation and verification are essential steps to ensure that the PCB design meets the required performance criteria. Various types of simulations can be performed, including signal integrity analysis, power integrity analysis, and thermal analysis.
3.3.1 Signal Integrity Analysis
Signal integrity analysis evaluates the quality of electrical signals as they travel through the PCB. It helps identify issues such as signal reflection, crosstalk, and timing errors, which can affect the circuit’s performance.
3.3.2 Power Integrity Analysis
Power integrity analysis ensures that the power distribution network (PDN) provides stable and sufficient power to all components. It involves analyzing voltage drops, current density, and decoupling capacitor placement to minimize noise and ensure reliable operation.
3.3.3 Thermal Analysis
Thermal analysis assesses the heat dissipation and temperature distribution on the PCB. It helps identify hotspots and ensures that the PCB can operate within the specified temperature range without overheating.
3.4 Manufacturing Preparation
Once the PCB design is finalized, it must be prepared for manufacturing. This involves generating the necessary files and documentation for the PCB fabrication and assembly process.
3.4.1 Gerber Files
Gerber files are the standard format used to communicate PCB design information to manufacturers. They contain data about the copper layers, solder mask, silkscreen, and drill holes. The Gerber files are used to create the photomasks for the PCB fabrication process.
3.4.2 Bill of Materials (BOM)
The Bill of Materials (BOM) is a list of all components required for the PCB assembly. It includes information such as part numbers, quantities, and reference designators. The BOM is used by the manufacturer to source and place the components on the PCB.
3.4.3 Assembly Drawings
Assembly drawings provide visual instructions for the placement and orientation of components on the PCB. They include details such as component outlines, reference designators, and polarity markings. Assembly drawings are used by the manufacturer to ensure accurate and consistent assembly.
4. PCB Design Considerations
Several factors must be considered during the PCB design process to ensure a successful outcome. These considerations include:
4.1 Signal Integrity
Signal integrity is the quality of the electrical signals as they travel through the PCB. Poor signal integrity can lead to issues such as signal distortion, timing errors, and data corruption. To maintain signal integrity, designers must consider factors such as trace impedance, routing topology, and termination techniques.
4.2 Power Integrity
Power integrity refers to the stability and efficiency of the power distribution network (PDN). A well-designed PDN ensures that all components receive the required voltage and current without excessive noise or voltage drops. Designers must consider factors such as decoupling capacitor placement, power plane design, and current density.
4.3 Thermal Management
Thermal management is the process of controlling the temperature of the PCB to prevent overheating and ensure reliable operation. Designers must consider factors such as component placement, heat sink design, and thermal vias to dissipate heat effectively.
4.4 Electromagnetic Compatibility (EMC)
Electromagnetic compatibility (EMC) is the ability of the PCB to operate without causing or being affected by electromagnetic interference (EMI). Designers must consider factors such as grounding, shielding, and trace routing to minimize EMI and ensure compliance with EMC regulations.
4.5 Manufacturability
Manufacturability refers to the ease with which the PCB can be fabricated and assembled. Designers must consider factors such as component placement, trace width, and clearance to ensure that the PCB can be manufactured efficiently and cost-effectively.
4.6 Testability
Testability is the ease with which the PCB can be tested for functionality and defects. Designers must consider factors such as test point placement, accessibility, and test coverage to ensure that the PCB can be thoroughly tested during and after assembly.
- Advanced PCB Design Techniques
As electronic devices become more complex, advanced PCB design techniques are required to meet the demands of modern electronics. Some of these techniques include:
5.1 High-Speed Design
High-speed design involves the routing of signals with fast rise times and high frequencies. Designers must consider factors such as impedance matching, signal reflection, and crosstalk to ensure reliable signal transmission. Techniques such as differential pair routing, length matching, and controlled impedance routing are commonly used in high-speed design.
5.2 Flexible and Rigid-Flex PCBs
Flexible and rigid-flex PCBs are used in applications where space and weight are critical, such as wearable devices and aerospace systems. Flexible PCBs are made of flexible substrate materials, while rigid-flex PCBs combine rigid and flexible sections. Designers must consider factors such as bend radius, material selection, and layer stackup when designing flexible and rigid-flex PCBs.
5.3 High-Density Interconnect (HDI)
High-Density Interconnect (HDI) PCBs are used in applications with high component density and complex routing requirements. HDI PCBs feature microvias, fine pitch traces, and multiple layers to achieve high interconnect density. Designers must consider factors such as via-in-pad, blind and buried vias, and layer stackup when designing HDI PCBs.
5.4 Embedded Components
Embedded components are integrated directly into the PCB substrate, reducing the need for surface-mounted components. This technique is used to save space, improve performance, and enhance reliability. Designers must consider factors such as component placement, thermal management, and signal integrity when designing PCBs with embedded components.
5.5 3D PCB Design
3D PCB design involves the use of three-dimensional modeling to visualize and optimize the PCB layout. This technique is particularly useful for complex designs with multiple layers and components. Designers can use 3D modeling to check for mechanical interference, optimize component placement, and ensure proper clearance and alignment.
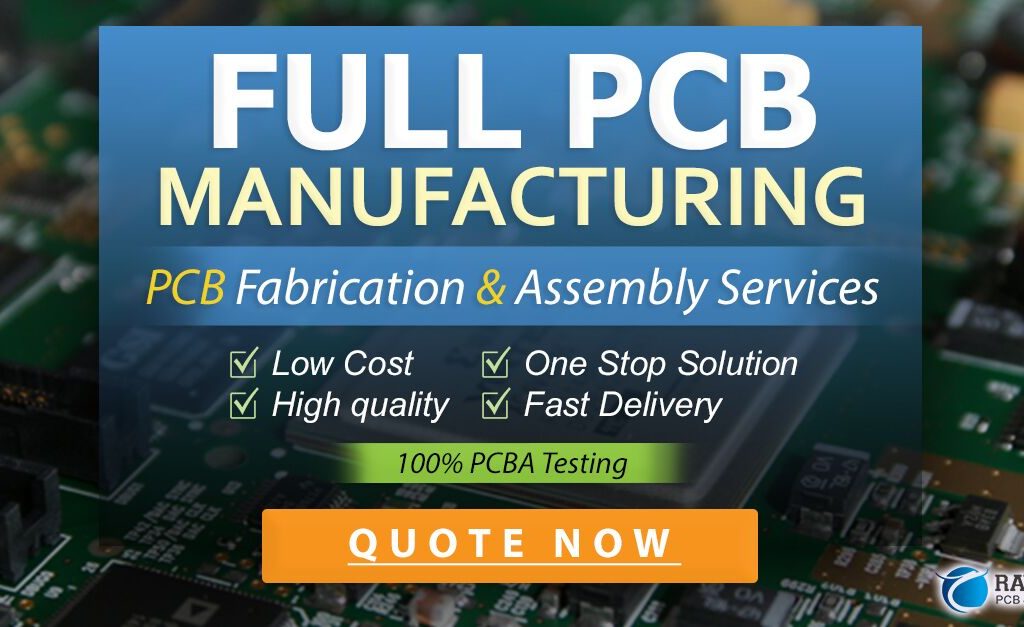
6. PCB Design Tools and Software
PCB design tools and software are essential for creating and optimizing PCB layouts. These tools provide a range of features and capabilities to assist designers in every stage of the design process.
6.1 Schematic Capture Tools
Schematic capture tools are used to create and edit the circuit schematic. These tools provide libraries of component symbols, allow for easy connection of components, and generate netlists for PCB layout.
6.2 PCB Layout Tools
PCB layout tools are used to create the physical layout of the PCB. These tools provide features such as component placement, trace routing, and design rule checking. Advanced tools also offer simulation and analysis capabilities for signal integrity, power integrity, and thermal management.
6.3 Simulation and Analysis Tools
Simulation and analysis tools are used to evaluate the performance of the PCB design before manufacturing. These tools can simulate signal behavior, power distribution, and thermal characteristics to identify and resolve potential issues.
6.4 Manufacturing Preparation Tools
Manufacturing preparation tools are used to generate the necessary files and documentation for PCB fabrication and assembly. These tools can create Gerber files, BOMs, assembly drawings, and other manufacturing outputs.
- Future Trends in PCB Design
The field of PCB design is continuously evolving, driven by advancements in technology and the demands of modern electronics. Some of the future trends in PCB design include:
7.1 Miniaturization
As electronic devices become smaller and more compact, PCB designers must find ways to reduce the size of PCBs while maintaining or improving performance. This trend is driving the development of advanced techniques such as HDI, embedded components, and flexible PCBs.
7.2 High-Speed and High-Frequency Design
The increasing demand for high-speed data transmission and high-frequency communication is driving the need for advanced PCB design techniques. Designers must consider factors such as signal integrity, impedance matching, and EMI to ensure reliable performance in high-speed and high-frequency applications.
7.3 Integration of Advanced Materials
The integration of advanced materials, such as high-performance substrates and conductive inks, is enabling new possibilities in PCB design. These materials offer improved electrical, thermal, and mechanical properties, allowing for more efficient and reliable PCB designs.
7.4 Automation and AI in PCB Design
Automation and artificial intelligence (AI) are increasingly being used in PCB design to streamline the design process and improve efficiency. AI-powered tools can assist with tasks such as component placement, routing, and optimization, reducing the time and effort required for PCB design.
7.5 Sustainability in PCB Design
Sustainability is becoming an important consideration in PCB design, with a focus on reducing environmental impact and improving recyclability. Designers are exploring ways to use eco-friendly materials, reduce waste, and design for disassembly and recycling.
8. Conclusion
PCB design is a complex and multifaceted process that plays a critical role in the development of modern electronic devices. From the initial schematic design to the final manufacturing preparation, each stage requires careful consideration of factors such as signal integrity, power integrity, thermal management, and manufacturability. As technology continues to advance, PCB designers must stay abreast of new techniques, tools, and trends to create innovative and reliable designs that meet the demands of the ever-evolving electronics industry. By mastering the principles and practices of PCB design, engineers can contribute to the development of cutting-edge technologies that shape the future of electronics.