What are Flexible PCBs?
Flexible PCBs, also known as flex circuits or FPCBs, are a type of printed circuit board that consists of a thin, flexible substrate with conductive traces and components attached to it. Unlike traditional rigid PCBs, flexible PCBs can bend and conform to various shapes, allowing for more compact and space-saving designs. They are typically made from materials such as polyimide, polyester, or PEEK (polyetheretherketone), which provide excellent thermal stability, chemical resistance, and mechanical strength.
Advantages of Flexible PCBs
Flexible PCBs offer several advantages over their rigid counterparts, including:
- Flexibility and durability: Flexible PCBs can withstand repeated bending and flexing without breaking or losing their electrical properties.
- Lightweight and compact design: The thin and flexible nature of FPCBs allows for more compact and lightweight electronic devices.
- Improved signal integrity: Flexible PCBs can reduce signal loss and interference by allowing shorter and more direct signal paths.
- Enhanced reliability: The absence of connectors and the reduced number of solder joints in flexible PCBs contribute to higher reliability and fewer points of failure.
- Cost-effective: In some cases, flexible PCBs can reduce the overall cost of an electronic device by eliminating the need for multiple rigid PCBs and connectors.
Flexible PCB Manufacturing Process
The manufacturing process for flexible PCBs is similar to that of rigid PCBs, but with some key differences to accommodate the unique properties of flexible materials. The following steps outline the typical flexible PCB manufacturing process:
1. Design and Layout
The first step in flexible PCB manufacturing is designing the circuit layout using specialized PCB design software. The designer must consider the specific requirements of the application, such as the desired flexibility, thickness, and electrical properties. They must also ensure that the design adheres to the manufacturing capabilities and constraints of the chosen fabrication process.
2. Material Selection
Once the design is finalized, the appropriate flexible substrate material is selected based on the application’s requirements. The most common materials used for flexible PCBs are:
- Polyimide (PI): Known for its excellent thermal stability, chemical resistance, and mechanical strength, polyimide is the most widely used material for flexible PCBs.
- Polyester (PET): Polyester is a cost-effective alternative to polyimide, suitable for less demanding applications that require moderate flexibility and durability.
- PEEK (Polyetheretherketone): PEEK is a high-performance thermoplastic that offers superior mechanical and chemical properties, making it ideal for harsh environments and high-temperature applications.
The conductive traces on flexible PCBs are typically made from copper, which is laminated onto the flexible substrate using an adhesive layer.
3. Lamination
The flexible substrate material is laminated with a thin layer of copper foil using heat and pressure. The copper foil is typically pre-treated with a roughening process to improve adhesion to the substrate. The lamination process creates a strong bond between the copper and the substrate, ensuring the integrity of the flexible PCB.
4. Patterning
After lamination, the copper layer is patterned to create the desired circuit layout. This is typically done using a photolithography process, which involves the following steps:
- Photoresist application: A light-sensitive polymer (photoresist) is applied to the copper surface.
- Exposure: The photoresist is exposed to UV light through a photomask, which contains the circuit pattern.
- Development: The exposed photoresist is removed using a chemical developer, leaving behind the desired circuit pattern.
- Etching: The exposed copper is etched away using a chemical solution, leaving only the copper traces that form the circuit pattern.
- Stripping: The remaining photoresist is removed, revealing the final copper circuit pattern.
5. Coverlay Application
After patterning, a coverlay (also known as a covercoat or solder mask) is applied to the flexible PCB to protect the copper traces and provide electrical insulation. The coverlay is typically made from a flexible polymeric material, such as polyimide or polyester, and is applied using a lamination process similar to the one used for the copper foil.
6. Drilling and Cutting
Holes are drilled through the flexible PCB to accommodate through-hole components or to create vias for interconnecting different layers in multi-layer designs. The drilling process for flexible PCBs requires special considerations to avoid damaging the delicate substrate material.
After drilling, the flexible PCB is cut to its final shape using a die-cutting or laser-cutting process. The cutting process must be precise to ensure the correct dimensions and to avoid damaging the delicate circuit traces.
7. Surface Finishing
To protect the exposed copper traces and improve solderability, a surface finish is applied to the flexible PCB. Common surface finishes for flexible PCBs include:
- ENIG (Electroless Nickel Immersion Gold): A layer of nickel is deposited on the copper, followed by a thin layer of gold. ENIG provides excellent solderability and durability.
- OSP (Organic Solderability Preservative): A thin, organic coating is applied to the copper to prevent oxidation and enhance solderability. OSP is a cost-effective option for less demanding applications.
- Immersion Silver: A thin layer of silver is deposited on the copper, providing good solderability and a lower cost alternative to ENIG.
8. Assembly and Testing
Finally, the flexible PCB is populated with components using standard SMT (Surface Mount Technology) or through-hole assembly processes. Special care must be taken during the assembly process to avoid damaging the flexible substrate or components.
After assembly, the flexible PCB undergoes thorough testing to ensure its functionality, reliability, and adherence to the specified requirements. This may include electrical testing, mechanical testing, and environmental testing, depending on the application.
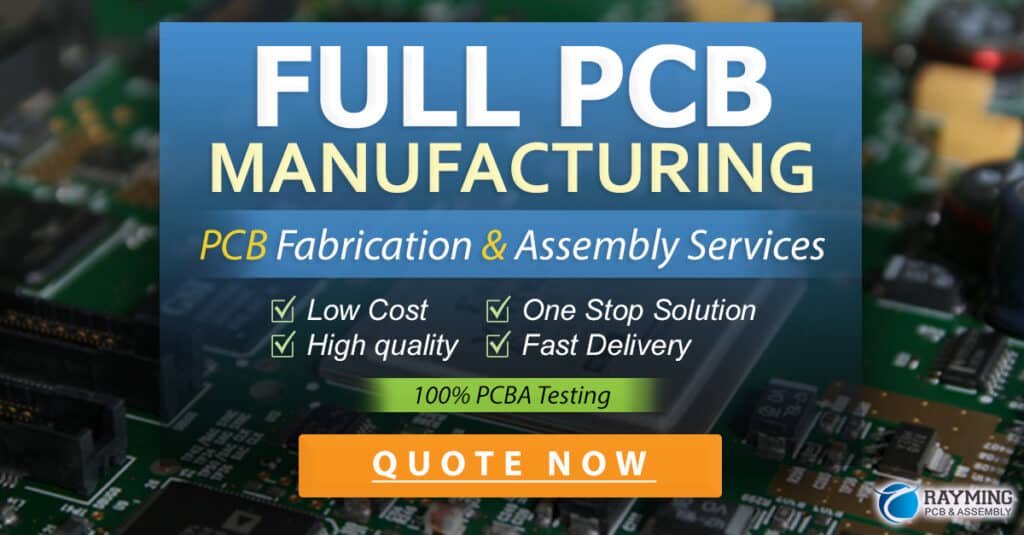
Types of Flexible PCBs
Flexible PCBs come in various types, each with its own unique characteristics and applications. The most common types of flexible PCBs are:
1. Single-Sided Flexible PCBs
Single-sided flexible PCBs have conductive traces on only one side of the flexible substrate. They are the simplest and most cost-effective type of flexible PCB, suitable for applications with low component density and simple circuit layouts.
2. Double-Sided Flexible PCBs
Double-sided flexible PCBs have conductive traces on both sides of the flexible substrate, allowing for higher component density and more complex circuit layouts. The two layers are interconnected using through-hole vias or plated through-holes (PTHs).
3. Multi-Layer Flexible PCBs
Multi-layer flexible PCBs consist of three or more conductive layers separated by flexible insulating layers. They offer the highest component density and the most complex circuit layouts, making them ideal for advanced applications that require high functionality in a compact space.
4. Rigid-Flex PCBs
Rigid-flex PCBs combine the benefits of both rigid and flexible PCBs by integrating rigid and flexible sections into a single circuit board. The rigid sections provide structural support and accommodate high-density components, while the flexible sections allow for bending and folding to fit the device’s form factor.
Applications of Flexible PCBs
Flexible PCBs find applications in a wide range of industries and products, including:
- Consumer electronics: Smartphones, tablets, laptops, and wearable devices
- Medical devices: Implantable devices, diagnostic equipment, and patient monitoring systems
- Automotive electronics: In-vehicle infotainment systems, sensors, and control modules
- Aerospace and defense: Avionics, satellites, and military communication systems
- Industrial automation: Robotics, sensors, and control systems
The unique properties of flexible PCBs make them ideal for applications that require:
- Compact and lightweight design
- High reliability and durability
- Resistance to vibration and shock
- Conformity to complex shapes and geometries
Challenges in Flexible PCB Manufacturing
Despite the many advantages of flexible PCBs, their manufacturing process presents several challenges that must be addressed to ensure reliable and high-quality products. Some of the key challenges include:
1. Material handling
The thin and flexible nature of the substrate materials used in flexible PCBs makes them more difficult to handle and process compared to rigid PCBs. Special handling techniques and equipment are required to avoid damaging the delicate materials during manufacturing.
2. Dimensional stability
Flexible substrates are more susceptible to dimensional changes during processing, especially when exposed to heat and moisture. Careful control of processing conditions and the use of appropriate adhesives and coverlay materials are essential to maintain the dimensional stability of the flexible PCB.
3. Adhesion
Ensuring proper adhesion between the copper traces, flexible substrate, and coverlay is crucial for the reliability and durability of the flexible PCB. Poor adhesion can lead to delamination and other failures, particularly in applications that involve repeated bending and flexing.
4. Interconnection reliability
Creating reliable interconnections between layers in multi-layer flexible PCBs and between rigid and flexible sections in rigid-flex PCBs can be challenging. Special attention must be paid to the design and manufacturing of vias and other interconnection structures to ensure reliable electrical performance and mechanical integrity.
5. Assembly and testing
Assembling components onto flexible PCBs requires specialized equipment and techniques to avoid damaging the delicate substrate and components. Testing flexible PCBs can also be more challenging, as they may require unique fixtures and procedures to simulate the expected bending and flexing in the final application.
Future Trends in Flexible PCB Manufacturing
As the demand for flexible PCBs continues to grow, driven by the increasing adoption of wearable devices, IoT applications, and advanced electronic systems, several trends are expected to shape the future of flexible PCB manufacturing:
- Advanced materials: The development of new substrate materials with improved thermal, mechanical, and electrical properties will enable the creation of flexible PCBs for even more demanding applications.
- 3D printing: The use of 3D printing technologies for flexible PCB manufacturing may enable faster prototyping, more complex designs, and reduced waste.
- Miniaturization: As electronic devices continue to shrink, flexible PCBs will need to accommodate ever-smaller components and higher circuit densities.
- Sustainability: There will be a growing emphasis on sustainable and eco-friendly materials and processes in flexible PCB manufacturing to reduce environmental impact and comply with increasingly stringent regulations.
- Integration with other technologies: The integration of flexible PCBs with other advanced technologies, such as printed electronics, stretchable circuits, and embedded sensors, will open up new possibilities for innovative and multifunctional electronic devices.
Frequently Asked Questions (FAQ)
-
What is the difference between a flexible PCB and a rigid PCB?
A flexible PCB is made from a thin, flexible substrate material that allows the circuit board to bend and conform to various shapes, while a rigid PCB is made from a solid, non-flexible substrate material that maintains a fixed shape. -
What are the most common materials used for flexible PCBs?
The most common materials used for flexible PCBs are polyimide (PI), polyester (PET), and PEEK (polyetheretherketone). These materials offer excellent thermal stability, chemical resistance, and mechanical strength. -
What are the advantages of using flexible PCBs?
Flexible PCBs offer several advantages, including increased flexibility and durability, lightweight and compact design, improved signal integrity, enhanced reliability, and potential cost savings compared to rigid PCBs. -
What are some common applications for flexible PCBs?
Flexible PCBs are used in a wide range of applications, including consumer electronics (smartphones, wearables), medical devices (implantables, diagnostic equipment), automotive electronics (infotainment systems, sensors), aerospace and defense systems, and industrial automation (robotics, control systems). -
What are the key challenges in manufacturing flexible PCBs?
The key challenges in manufacturing flexible PCBs include material handling, dimensional stability, adhesion, interconnection reliability, and assembly and testing. These challenges arise from the unique properties of flexible substrates and the need for specialized equipment and techniques to process them reliably.
Conclusion
Flexible PCBs have become an essential component in the rapidly evolving world of electronics, enabling the creation of innovative, compact, and reliable devices across various industries. The unique properties of flexible PCBs, such as their ability to bend, fold, and conform to complex shapes, have opened up new design possibilities and improved the functionality of electronic systems.
However, the manufacturing of flexible PCBs presents its own set of challenges, requiring specialized materials, processes, and techniques to ensure the highest quality and reliability. As the demand for flexible PCBs continues to grow, manufacturers must stay at the forefront of technological advancements, embracing new materials, processes, and design strategies to meet the ever-increasing performance and sustainability requirements.
By understanding the intricacies of flexible PCB manufacturing, designers and engineers can leverage the full potential of these versatile circuit boards to create the next generation of electronic devices that are smarter, more compact, and more reliable than ever before.
Key Takeaways
- Flexible PCBs are made from thin, flexible substrate materials that allow the circuit board to bend and conform to various shapes.
- The manufacturing process for flexible PCBs involves several key steps, including design and layout, material selection, lamination, patterning, coverlay application, drilling and cutting, surface finishing, and assembly and testing.
- Flexible PCBs offer numerous advantages, such as increased flexibility and durability, lightweight and compact design, improved signal integrity, and enhanced reliability.
- Flexible PCBs find applications in a wide range of industries, including consumer electronics, medical devices, automotive electronics, aerospace and defense, and industrial automation.
- Manufacturers must address several challenges in flexible PCB manufacturing, such as material handling, dimensional stability, adhesion, interconnection reliability, and assembly and testing, to ensure high-quality and reliable products.
As flexible PCBs continue to shape the future of electronics, staying informed about the latest advancements and best practices in flexible PCB manufacturing will be crucial for designers, engineers, and manufacturers alike. By embracing innovation and collaborating across industries, we can unlock the full potential of flexible PCBs and create electronic devices that are more functional, sustainable, and adaptable than ever before.
Aspect | Flexible PCBs | Rigid PCBs |
---|---|---|
Substrate Material | Thin, flexible materials (e.g., polyimide, polyester, PEEK) | Solid, non-flexible materials (e.g., FR-4, CEM-1, CEM-3) |
Flexibility | Can bend, fold, and conform to various shapes | Maintains a fixed, rigid shape |
Durability | Can withstand repeated bending and flexing | More susceptible to damage from bending or physical stress |
Weight and Size | Lightweight and compact, enabling space-saving designs | Generally heavier and bulkier than flexible PCBs |
Signal Integrity | Improved signal integrity due to shorter, more direct paths | Signal integrity may be affected by longer, more complex paths |
Reliability | Enhanced reliability due to fewer connectors and solder joints | Reliability dependent on the quality of connectors and joints |
Cost | Can be cost-effective by reducing connectors and rigid PCBs | Generally less expensive than flexible PCBs for simple designs |
Applications | Wearables, medical devices, automotive, aerospace, automation | Consumer electronics, industrial control, power electronics |
Table: Comparison of key aspects between flexible PCBs and rigid PCBs
Industry | Applications of Flexible PCBs |
---|---|
Consumer Electronics | Smartphones, tablets, laptops, wearable devices, digital cameras, gaming devices |
Medical Devices | Implantable devices, diagnostic equipment, patient monitoring systems, wearables |
Automotive | In-vehicle infotainment systems, sensors, control modules, LED lighting |
Aerospace & Defense | Avionics, satellites, military communication systems, portable devices |
Industrial Automation | Robotics, sensors, control systems, machine vision, portable devices |
Table: Common applications of flexible PCBs in various industries