Introduction
Flexible printed circuit boards (PCBs), also known as flex circuits, are a vital component in many of today’s electronics. As devices get smaller and more complex, flexible circuits allow for connections and circuitry in tight spaces. When you need custom flexible PCBs designed and manufactured, getting quotes from potential suppliers is the first step. In this guide, we’ll look at tips for getting accurate flexible PCB quotes that meet your requirements.
Overview of Flex Circuits and Their Advantages
A flexible PCB uses a thin, bendable material base rather than a rigid fiberglass FR-4 board. The most common base material is polyimide (Kapton), although other films like polyester and PEN are also used. Flex circuits have conductive traces etched or printed on the flexible base to create the circuit wiring. Components can be directly attached or connected using various methods.
Flex circuits provide many advantages over rigid PCBs:
- Tight space connections – Can fold and bend to fit small spaces
- Motion tolerance – Dynamic flexing without damage
- Lightweight – Thin material with no rigid base
- Reliability – Proven technology for complex circuits
- Design freedom – Curved, 3D, rolled, and irregular shapes
- Heat resistance – Withstands higher temps than standard PCBs
- Chemical resistance – Polyimide base resists many harsh chemicals
- Low cost prototyping – Short runs viable with flexible materials
With these benefits, it’s no wonder flex circuits are used in products from mobile devices to industrial equipment, automotive, aerospace, medical devices, and more.
Key Specifications for Your Flexible PCB Quote
When requesting quotes for flexible PCB production, you’ll need to provide suppliers with the key details of your design requirements. This allows them to accurately estimate the costs and lead times for manufacturing your flex boards. Here are some of the important specifications to have ready:
Board Dimensions
- Length and width of the overall circuit outline
- Any unusual shapes or cutouts required
Layer Count
- Single sided, double sided or multilayer construction
- For multilayer, the number of conductive layers needed
Dielectric Material
- Polyimide, polyester, PEN or other base material
- Thickness of the flexible dielectric
Conductors
- Copper thickness (1/2 oz, 1 oz, 2 oz typical)
- Minimum trace/space width
Stiffener Requirements
- Areas needing stiffeners for component mounting
- Stiffener material (acrylic, aluminum, FR4)
Coatings and Coverlayers
- Coverlay openings for solder pads, components, buttons
- Protective coatings like solder mask, cover coat
Adhesives
- Types of adhesive for layer bonding, component attachment
Text Legends
- Identify text required for markings, labels, etc.
Solder Pads
- Number and location of pads for component termination
Other Components
- Any mounted parts, connectors, etc. to be assembled
Finished Panel Size
- If multiple circuits on a panel for better handling
Quantity Required
- Number of finished boards needed
The more details you can provide, the more accurate the quote will be. Expect to go through some iteration to finalize the specifications.
Getting Flexible PCB Quotes
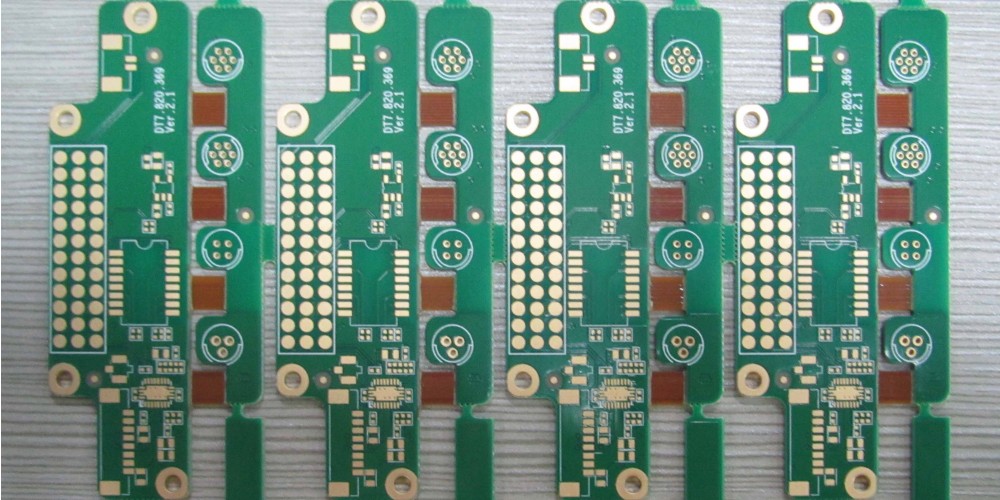
With your design specifications in hand, it’s time to request quotes. Here are some tips on obtaining and comparing flexible PCB quotes:
Choose Reputable Manufacturers
- Stick with established, reliable flexible PCB companies. Check reviews and examples of their work.
- Ask about their specific experience with flex board fabrication.
- Make sure they can meet your lead time needs.
Get Quotes From Multiple Sources
- Get 3-5 quotes to compare options. But don’t overload suppliers with excessive requests.
- Mix quotes from domestic and overseas manufacturers to compare pricing.
- Consider both small and large producers. Small shops may provide more customization.
Share Complete Design Files
- Provide full details of your flex board design requirements.
- If available, share actual CAD/CAM files so suppliers understand the design.
Request a Design Review
- Ask suppliers to review your design for potential issues or improvements.
- Consider their suggestions, but don’t let them dictate your design without reason.
Clarify Scope Upfront
- Make sure the quote includes everything required for a finished, tested board.
- Define who handles board assembly if needed. Get assembly quotes separately.
- Understand shipping responsibilities and costs.
Confirm Production Capabilities
- Ensure the PCB producer can fabricate your board design as specified.
- Ask about their experience with fine features, HDI, thick copper, hybrid rigidflex, etc. if needed.
Review All Cost Factors
- Prices for short prototype runs will differ from production volume pricing.
- Make sure tooling, masks, and NRE costs are identified if applicable.
- Understand additional charges like packaging, testing, insurance, tariffs, etc.
- Get an itemized breakdown of all costs rather than just a bottom line total.
By following these tips, you should be able to get accurate flexible PCB quotes from suppliers that meet your needs and budget.
Comparing Flexible PCB Quotes
Once you’ve received quotes from multiple manufacturers, you’ll need to compare the options to choose your supplier. Here are key factors to consider:
- Total pricing – Consider both short run and production volume costs. Look for deals on assembly or other value-added services.
- Quality – Evaluate process capabilities, certifications, reviews, and product samples.
- Lead time – Choose a supplier that can deliver when needed, but don’t sacrifice too much on cost for faster turns.
- Communication – How responsive and helpful is the sales staff? Good communication indicates an easier production process.
- Engineering support – Will the supplier review your design and provide engineering feedback to improve the product?
- Proximity – Domestic suppliers allow for easier communication and rapid shipping. Overseas can offer significant cost savings if managed properly.
- NRE costs – One-time mold, tooling and mask charges can often be negotiated with the supplier.
- Volume flexibility – Some shops have minimum order quantities. Others can accommodate prototype to mid-volume production.
- Certifications – Look for quality management system certification like ISO 9001 or AS9100 as applicable. Some industries require compliance with IATF16949 automotive or Nadcap aerospace standards.
By balancing these criteria, you can select the flexible PCB manufacturing partner that best fits your specific product needs. Don’t automatically choose the cheapest quote, but the best value based on the factors above.
Tips for Getting the Most from Your Selected Manufacturer
Once you’ve chosen your flexible circuit board supplier, here are some tips for working with them throughout the process:
- Maintain clear, timely communication and set expectations upfront. Make sure you understand the production schedule and key milestones.
- Provide thorough documentation of your design, bill of materials, assembly instructions, testing requirements, etc. Don’t assume anything – document every detail required.
- Work collaboratively with engineers to conduct design reviews and resolve any issues early before they become costly problems in manufacturing.
- Understand the inspection criteria and confirm with your supplier. Make sure quality control points match your needs.
- Plan for potential delays and give the supplier reasonable lead time. Trying to rush production typically backfires.
- Once your prototype boards are delivered, inspect thoroughly and provide feedback to your supplier. Resolve any problems before full production.
- Pay attention to packaging requirements. Electronics must be protected from electrostatic discharge (ESD) and moisture penetration during shipment.
Following these guidelines will help develop a strong working relationship with your chosen flex board manufacturer. By taking the time upfront to optimize the design, documentation, and communication, you’ll achieve a smoother production process and higher quality product.
Frequently Asked Questions
What design tools do I need for designing flex circuits?
Most flex board designers use standard PCB CAD software like Altium, Cadence Allegro, and Mentor Xpedition. These tools allow creating the circuit traces, outlines, cover layers, and documentation for flex boards. Specialized tools for analyzing flex stress and fatigue may also be used.
Can connectors be mounted directly to flex boards?
Yes, connectors and components can be attached directly to flex boards if the material is thick enough. Adhesives or solders are used to bond the connections. Stiffeners may be required in some cases to reinforce the area.
How small can flex circuit traces and spaces be?
Advanced flex PCBs can achieve extremely fine lines and spaces below 100 microns (0.1 mm) using micro-etching manufacturing processes. Typical traces are 200-250 microns for standard consumer products.
How many conductive layers can flex circuits support?
While most flexible boards are 1-2 layers, some specialized constructions support 4-6 layers or more. Full HDI stackups with blind and buried vias are also possible, but increase the cost.
Can rigid sections be combined on the same flex board?
Yes, rigid-flex boards use stiffened sections connected by flexible circuits. The rigid portions provide component mounting stability while the flex segments enable connections.
Summary
Getting quotes from prospective flexible PCB manufacturers is the critical first step in bringing your custom flex circuit design to reality. By providing detailed specifications, evaluating suppliers thoroughly, managing the production process closely, and maintaining open communication, you can obtain quality flexible boards tailored to your exact requirements. Use the tips in this guide to acquire the best value flexible PCB manufacturing services for your next product design.