Introduction
A flex PCB (flexible printed circuit board) is a technology that allows circuits to be created on flexible substrates like polyimide or polyester. The flex PCB itself consists of thin layers of copper conductive traces on a polymer base. Flex PCBs provide many advantages over rigid PCBs including:
- Ability to bend and flex without damage
- Lightweight and thin profile
- Can be folded or wrapped into tight spaces
- Dynamic flexing motions possible
- Often cost effective in lower quantities
Finding the right flex PCB supplier is important to get a high quality and reliable flex circuit board for your application. This article provides a comprehensive guide on what to look for in a flex PCB supplier and the key factors to consider in your decision process.
Flex PCB Supplier Capabilities
Flex Circuit Materials
The flex circuit material used is a major driver of quality and reliability. Common materials include:
- Polyimide (Kapton) – Most popular flexible material, high heat resistance and strength.
- Polyester (PET) – More economical but lower heat resistance.
- PEN – Modified PET with improved thermal properties.
- PI Composite – Polyimide films bonded with adhesive.
- LCP – Liquid Crystal Polymer, for high frequency applications.
The supplier should have experience working with different flex circuit materials needed for your application and performance requirements.
Layer Count
The number of conductive copper layers in the flex PCB stackup is an important consideration. A supplier should be able to produce:
- Single layer flex – One layer of conductors, typically under 2 mils thick.
- Two layer flex – Two conductive layers bonded together.
- Multilayer flex – Flex circuits with 3 or more conductive layers.
Higher layer counts allow increased circuit complexity but require specialized processes.
Dense Interconnects
Fine line traces and spaces down to 2/2 mil allow dense interconnections. The latest laser drilling technology enables high density vias.
Flex-Rigid Capability
Many designs require rigid sections connected by flex cables. Choose a supplier with proven flex-rigid fabrication capabilities.
Secondary Operations
Many flex circuits require additional fabrication steps:
- Creep relief – Mechanical reinforcement at interface regions.
- Stiffeners – Rigid sections for strength and mounting.
- Overmolding – Plastic molding over flex circuitry.
- Assembly – Component attachment and soldering.
Seek suppliers experienced in specialized secondary operations needed for your product.
Quality and Certifications
A reputable flex PCB supplier will have quality management certifications like ISO 9001, and cleanroom facilities for flex PCB fabrication. They should be willing to provide samples for design verification and testing.
Benefits of a Strong Flex Supplier Relationship
Design for Manufacturing
A good supplier will work with you on your design to optimize it for flex PCB manufacturing and reliability – this can avoid costly mistakes!
Supply Chain Management
Leverage the flex supplier’s experience in global sourcing of materials, operations management and qualifying special processes.
Reduced Risk
An established flex supplier with a track record of success helps minimize risk and avoid potential issues in a new product introduction.
Cost Savings
Suppliers adept at designing for cost can help reduce expenses through design refinement and leveraging supplier relationships.
Innovation
Flex circuit technology continues advancing rapidly. An innovative supplier can bring new ideas and solutions to challenging applications.
Key Considerations in Choosing a Flex Supplier
Research and Qualify
Thoroughly investigate suppliers under consideration through:
- Technical capability assessment – Review expertise, certifications, equipment.
- Reference checks – Speak to current customers on quality and service.
- Sampling – Test initial prototypes to verify capabilities.
Geographic Location
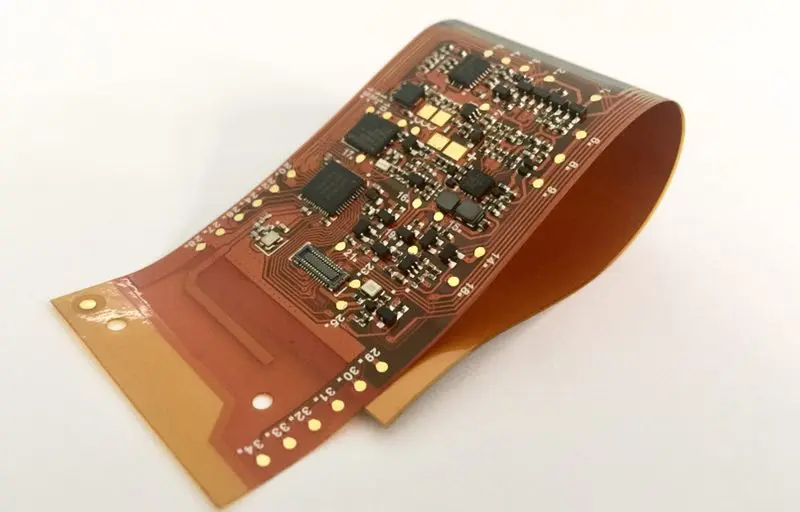
Proximity to manufacturing operations can be beneficial for collaboration and communication. However, geographic diversity also provides stability.
Company Stability
Choose an established company with solid financials. Avoid suppliers with high turnover rates.
Responsiveness
See how quickly the supplier responds to inquiries and how easy they are reach. Rate of communications is telling.
Service Level
Evaluate the commitment to customer service starting right from the quote stage. Purchase price shouldn’t be the only priority.
Questions and Answers
Q: What are some key specs to provide a flex supplier for a quote?
A: Important details in a flex PCB quote request include: circuit material type, number of layers, estimated board size, line width/space, minimum bend radius, stiffener requirements, special processes like overmolding, and production volumes.
Q: Are there certain applications flex PCBs are best suited for?
A: Flex circuits excel in applications where dynamic flexing is required like wearables, medical devices, robotics. Also useful where space constraints require thin, foldable connections.
Q: What are some red flags to watch out for in choosing a flex PCB supplier?
A: Red flags include inability to provide certifications or references, lack of experienced engineering support, poor responsiveness, and inability to provide test samples.
Q: What is the typical lead time for fabrication of a new flex design?
A: For an initial prototype, lead time can range from 2-4 weeks depending on complexity. For higher volume production, the cycle time averages 4-6 weeks but depends on order quantity.
Q: How long do flex PCB designs typically stay in production?
A: Flex circuits tend to support longer product life cycles than rigid boards. Designs often stay in production 5-10+ years. So establishing a supplier relationship is a long term choice.
Conclusion
Choosing the right flex PCB supplier requires careful vetting and analysis of their capabilities, services, and stability. By selecting a strong partner, companies can enable innovative flex circuit designs, ensure high quality components, and reduce time-to-market for products. Consider the guidelines in this article when making this critical decision and establishing supply chain relationships. With an experienced flex circuit provider supporting product development and manufacturing, the possibilities for new and improved products are endless.