Introduction
Electroless Nickel and Immersion Gold (ENIG) is a widely used surface finish in the electronics industry, known for its excellent solderability, flat surface, and corrosion resistance. However, despite its many advantages, ENIG is not without its challenges. One of the most significant issues associated with ENIG is the phenomenon known as “Black Pad.” This article provides a comprehensive analysis of Black Pad and ENIG, exploring the causes, effects, and mitigation strategies for this critical issue. By understanding the intricacies of ENIG and the factors contributing to Black Pad, manufacturers can improve the reliability and performance of their PCB assemblies.
Understanding ENIG
What is ENIG?
ENIG is a two-layer metallic coating applied to the surface of PCBs. It consists of an electroless nickel layer followed by an immersion gold layer. The nickel layer provides a barrier to prevent copper diffusion and offers a hard, wear-resistant surface. The gold layer protects the nickel from oxidation and provides a solderable surface.
Advantages of ENIG
- Solderability: ENIG provides an excellent surface for soldering, ensuring strong and reliable solder joints.
- Flat Surface: The flat surface of ENIG is ideal for fine-pitch components and surface-mount technology (SMT).
- Corrosion Resistance: The gold layer protects the underlying nickel and copper from oxidation and corrosion.
- Wire Bonding: ENIG is suitable for wire bonding applications, making it versatile for various assembly processes.
Disadvantages of ENIG
- Cost: ENIG is more expensive than other surface finishes like HASL (Hot Air Solder Leveling).
- Complexity: The ENIG process is more complex and requires precise control of chemical baths and process parameters.
- Black Pad: The risk of Black Pad, a defect that can lead to solder joint failures, is a significant concern.
The Black Pad Phenomenon
What is Black Pad?
Black Pad is a defect that occurs in ENIG surface finishes, characterized by a dark, brittle layer between the nickel and gold layers. This layer can lead to weak solder joints, resulting in poor electrical connections and potential failures in the field.
Causes of Black Pad
- Over-Aggressive Gold Bath
- Description: An over-aggressive gold bath can lead to excessive gold deposition, causing the underlying nickel to corrode.
- Effect: The corroded nickel forms a brittle, dark layer that weakens the solder joint.
- Improper Nickel Phosphorus Composition
- Description: The nickel layer in ENIG typically contains phosphorus. An improper phosphorus composition can make the nickel more susceptible to corrosion.
- Effect: Corrosion of the nickel layer leads to the formation of Black Pad.
- Inadequate Rinsing
- Description: Inadequate rinsing between the nickel and gold baths can leave residual chemicals on the surface.
- Effect: Residual chemicals can react with the nickel, leading to corrosion and Black Pad formation.
- Contamination
- Description: Contamination from oils, dust, or other foreign materials can interfere with the ENIG process.
- Effect: Contamination can lead to uneven deposition and corrosion, contributing to Black Pad.
Effects of Black Pad
- Weak Solder Joints: Black Pad can lead to weak solder joints, resulting in poor electrical connections and potential failures.
- Intermittent Failures: The brittle layer can cause intermittent failures, making it difficult to diagnose and repair.
- Reduced Reliability: Black Pad reduces the overall reliability of the PCB assembly, leading to higher failure rates in the field.
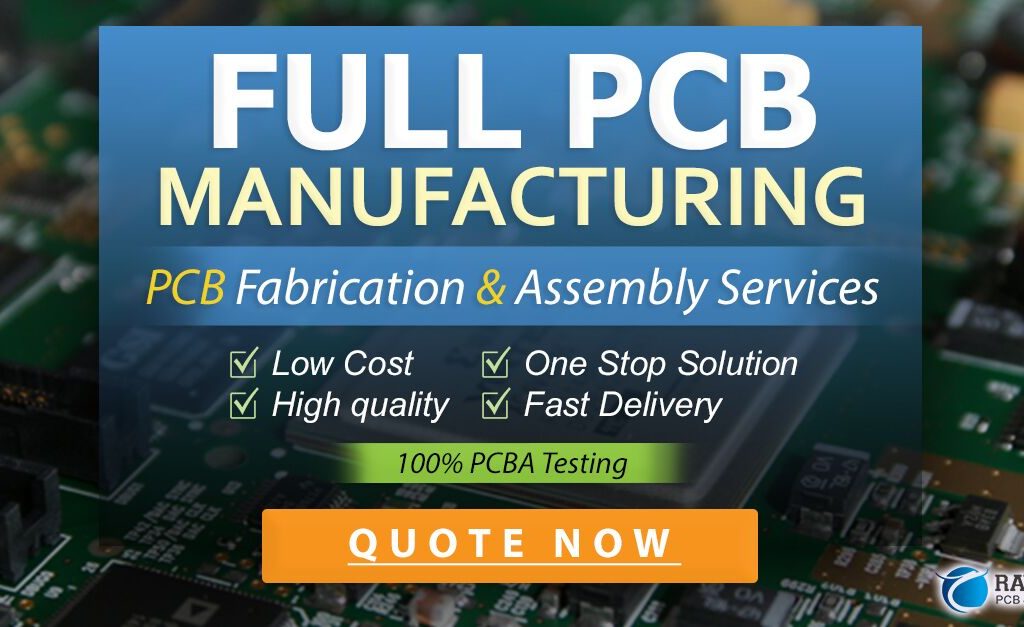
Mitigation Strategies for Black Pad
1. Control Gold Bath Parameters
Proper control of the gold bath parameters is crucial to prevent over-aggressive gold deposition.
- Gold Concentration: Maintain the gold concentration within the recommended range to avoid excessive deposition.
- pH Level: Monitor and control the pH level of the gold bath to ensure optimal conditions.
- Temperature: Maintain the gold bath temperature within the specified range to prevent over-deposition.
2. Optimize Nickel Phosphorus Composition
Ensuring the correct phosphorus composition in the nickel layer can reduce the risk of corrosion.
- Phosphorus Content: Maintain the phosphorus content within the recommended range (typically 7-11%).
- Uniform Deposition: Ensure uniform deposition of the nickel layer to avoid areas with varying phosphorus content.
3. Ensure Proper Rinsing
Adequate rinsing between the nickel and gold baths is essential to remove residual chemicals.
- Rinse Time: Ensure sufficient rinse time between baths to remove all residual chemicals.
- Rinse Quality: Use high-quality deionized water for rinsing to prevent contamination.
4. Prevent Contamination
Preventing contamination is critical to ensuring a clean and uniform ENIG surface.
- Cleanroom Environment: Perform the ENIG process in a cleanroom environment to minimize contamination.
- Regular Maintenance: Regularly clean and maintain the chemical baths and equipment to prevent contamination.
5. Implement Quality Control Measures
Implementing robust quality control measures can help detect and prevent Black Pad.
- Inspection: Regularly inspect the ENIG surface for signs of Black Pad using techniques like cross-sectional analysis and SEM (Scanning Electron Microscopy).
- Testing: Conduct solderability tests to ensure the integrity of the solder joints.
- Process Monitoring: Continuously monitor the ENIG process parameters to ensure they remain within the specified ranges.
Case Studies
Case Study 1: Addressing Black Pad in a Consumer Electronics Company
A consumer electronics company experienced intermittent failures in their PCB assemblies due to Black Pad. By optimizing the gold bath parameters and ensuring proper rinsing, they were able to reduce the incidence of Black Pad and improve the reliability of their products.
Case Study 2: Improving Nickel Phosphorus Composition in an Automotive Electronics Company
An automotive electronics company faced issues with Black Pad due to improper nickel phosphorus composition. By adjusting the phosphorus content and ensuring uniform deposition, they were able to mitigate the risk of Black Pad and enhance the durability of their PCB assemblies.
Case Study 3: Preventing Contamination in an Industrial Equipment Manufacturer
An industrial equipment manufacturer encountered Black Pad issues caused by contamination. By implementing a cleanroom environment and regular maintenance of the ENIG process, they were able to prevent contamination and eliminate Black Pad defects.
Conclusion
ENIG is a highly effective surface finish for PCBs, offering excellent solderability, flat surfaces, and corrosion resistance. However, the risk of Black Pad poses a significant challenge that can compromise the reliability and performance of PCB assemblies. By understanding the causes of Black Pad and implementing mitigation strategies such as controlling gold bath parameters, optimizing nickel phosphorus composition, ensuring proper rinsing, preventing contamination, and implementing robust quality control measures, manufacturers can reduce the incidence of Black Pad and enhance the reliability of their products. Through careful process control and continuous improvement, the electronics industry can continue to leverage the benefits of ENIG while minimizing its associated risks.