Introduction
Ball Grid Array (BGA) packages have become a cornerstone in modern electronics design due to their high pin density, compact size, and superior electrical performance. However, routing signals from a BGA package to the rest of the PCB presents unique challenges, particularly when it comes to fanout routing. Fanout routing is the process of connecting the BGA pins to the PCB’s routing layers, ensuring that all signals are properly routed without causing signal integrity issues or manufacturing difficulties. This article delves into the best practices and techniques for BGA fanout routing, providing a comprehensive guide for engineers and designers.
Understanding BGA Packages
What is a BGA Package?
A BGA package is a type of surface-mount packaging used for integrated circuits. It utilizes an array of solder balls on the bottom of the package to connect to the PCB, offering several advantages over traditional packages:
- High Pin Density: BGAs can accommodate a large number of pins in a small area.
- Improved Electrical Performance: Shorter connections reduce inductance and improve signal integrity.
- Better Thermal Performance: The solder balls provide a low-resistance thermal path for heat dissipation.
Types of BGA Packages
- Standard BGA: Uniform array of solder balls.
- Micro BGA: Smaller pitch and ball size for even higher density.
- CSP (Chip Scale Package): Nearly the same size as the die, offering the highest density.
Key Considerations in BGA Fanout Routing
1. Pad and Via Size
The size of the pads and vias used in fanout routing is critical for ensuring reliable connections and manufacturability.
- Pad Size: The pad size should match the BGA ball size, typically with a slight margin to accommodate misalignment during assembly.
- Via Size: Vias should be as small as possible to minimize the impact on routing density but large enough to ensure reliable plating and soldering.
2. Via Types
Different via types can be used in BGA fanout routing, each with its own advantages and limitations.
- Through-Hole Vias: Traditional vias that go through the entire PCB. They are reliable but can consume significant routing space.
- Blind Vias: Connect an outer layer to an inner layer without going through the entire board, saving space.
- Buried Vias: Connect inner layers without reaching the outer layers, further optimizing space but increasing cost and complexity.
- Microvias: Small vias typically used in high-density interconnect (HDI) designs, offering the highest density but requiring advanced manufacturing techniques.
3. Escape Routing
Escape routing refers to the process of routing signals from the BGA pads to the outer edges of the BGA array, where they can be routed to other parts of the PCB.
- Layer Usage: Utilize multiple layers for escape routing to distribute the routing density and avoid congestion.
- Routing Channels: Plan the routing channels carefully to ensure that all signals can escape without crossing or interfering with each other.
4. Signal Integrity
Maintaining signal integrity is crucial in BGA fanout routing, especially for high-speed signals.
- Impedance Matching: Ensure that the traces maintain consistent impedance to prevent reflections and signal degradation.
- Crosstalk: Minimize crosstalk by maintaining adequate spacing between traces and using ground planes effectively.
- Length Matching: Match the lengths of differential pairs and critical signals to ensure synchronous arrival and reduce skew.
5. Power and Ground Distribution
Proper distribution of power and ground is essential for the reliable operation of the BGA package.
- Power Planes: Use dedicated power planes to distribute power evenly and reduce voltage drops.
- Decoupling Capacitors: Place decoupling capacitors close to the BGA pins to filter noise and stabilize the power supply.
- Ground Vias: Use multiple ground vias to provide a low-impedance return path and improve thermal performance.
Best Practices for BGA Fanout Routing
1. Plan the Fanout Strategy Early
Developing a comprehensive fanout strategy early in the design process can prevent routing congestion and signal integrity issues.
- Pin Assignment: Optimize the pin assignment to group related signals and minimize crossing.
- Layer Stack-Up: Plan the layer stack-up to allocate sufficient layers for escape routing and signal integrity.
- Routing Priority: Prioritize critical signals, such as high-speed and differential pairs, in the fanout strategy.
2. Use a Staggered Via Pattern
A staggered via pattern can help distribute the routing density and improve manufacturability.
- Alternating Rows: Place vias in alternating rows to create more space for routing channels.
- Diagonal Placement: Consider diagonal placement of vias to further optimize space and reduce congestion.
3. Implement HDI Techniques
High-density interconnect (HDI) techniques can significantly enhance the fanout routing of dense BGA packages.
- Microvias: Use microvias to connect adjacent layers, reducing the need for through-hole vias and saving space.
- Sequential Lamination: Employ sequential lamination to build up the PCB layer by layer, allowing for more complex routing and higher density.
4. Optimize Trace Width and Spacing
Careful optimization of trace width and spacing is essential for maintaining signal integrity and manufacturability.
- Width Calculation: Calculate the trace width based on the current carrying capacity and impedance requirements.
- Spacing Rules: Adhere to spacing rules to prevent crosstalk and ensure reliable manufacturing.
5. Utilize Autorouters Wisely
Autorouters can be a valuable tool for BGA fanout routing, but they should be used judiciously.
- Custom Rules: Define custom routing rules to guide the autorouter and ensure compliance with design requirements.
- Manual Adjustments: Review and manually adjust the autorouter’s results to optimize critical signals and address any issues.
6. Conduct Signal Integrity Analysis
Signal integrity analysis is crucial for identifying and addressing potential issues in BGA fanout routing.
- Simulation Tools: Use simulation tools to analyze signal integrity, including impedance, crosstalk, and timing.
- Iterative Refinement: Iteratively refine the design based on simulation results to achieve optimal performance.
7. Collaborate with Manufacturers
Collaborating with PCB manufacturers can help ensure that the fanout routing design is manufacturable and reliable.
- DFM Guidelines: Follow the manufacturer’s design for manufacturability (DFM) guidelines to avoid common pitfalls.
- Prototyping: Build prototypes to validate the design and identify any manufacturing issues early.
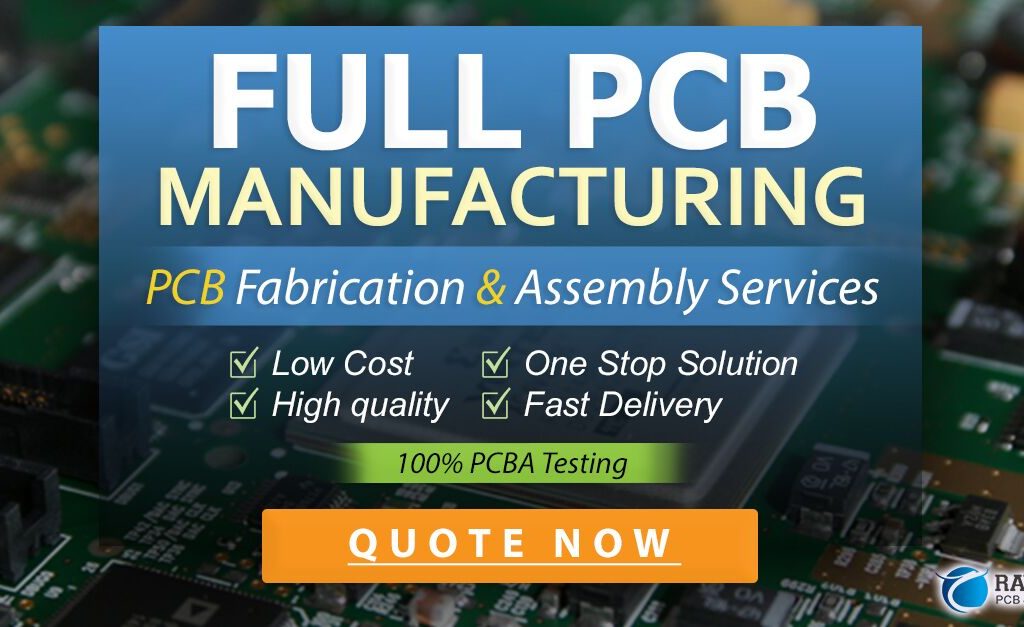
Common Pitfalls and Lessons Learned
1. Insufficient Layer Allocation
Failing to allocate sufficient layers for fanout routing can lead to congestion and signal integrity issues.
- Lesson Learned: Plan the layer stack-up carefully, ensuring enough layers are available for escape routing and signal integrity.
2. Ignoring Thermal Management
Neglecting thermal management in BGA fanout routing can result in overheating and reliability issues.
- Lesson Learned: Incorporate thermal vias and consider the thermal performance of the PCB materials and layout.
3. Overlooking Manufacturing Constraints
Ignoring manufacturing constraints can lead to costly redesigns and delays.
- Lesson Learned: Collaborate with manufacturers early and adhere to their DFM guidelines to ensure a smooth production process.
4. Inadequate Signal Integrity Analysis
Skipping signal integrity analysis can result in performance issues and failed prototypes.
- Lesson Learned: Conduct thorough signal integrity analysis and iterative refinement to achieve optimal performance.
Case Studies
Case Study 1: High-Density BGA Fanout in a Networking Device
A networking device manufacturer faced challenges with fanout routing for a high-density BGA package. By implementing HDI techniques, including microvias and sequential lamination, they were able to achieve the necessary routing density and signal integrity. Collaboration with the PCB manufacturer ensured that the design was manufacturable, resulting in a successful product launch.
Case Study 2: Signal Integrity Optimization in a Consumer Electronics Product
A consumer electronics company designed a product with a high-speed BGA package. Initial prototypes suffered from signal integrity issues due to inadequate fanout routing. By conducting detailed signal integrity analysis and optimizing trace width and spacing, they resolved the issues and achieved reliable performance.
Case Study 3: Thermal Management in an Automotive Control Unit
An automotive control unit required robust thermal management for its BGA package. The design team incorporated thermal vias and optimized the power and ground distribution, ensuring reliable operation under high-temperature conditions. Prototyping and collaboration with the manufacturer validated the design, leading to a successful implementation.
Conclusion
BGA fanout routing is a critical aspect of modern PCB design, requiring careful planning and execution to ensure reliable performance and manufacturability. By following best practices such as early planning, staggered via patterns, HDI techniques, and thorough signal integrity analysis, engineers can overcome the challenges of BGA fanout routing. Learning from common pitfalls and real-world case studies further enhances the ability to create high-performance, reliable designs. Ultimately, mastering BGA fanout routing enables the development of advanced electronic devices that leverage the full potential of BGA packages.