Introduction
Electrostatic Discharge (ESD) is a common phenomenon that can cause significant damage to electronic components and Printed Circuit Boards (PCBs). ESD occurs when a sudden flow of electricity between two electrically charged objects, often caused by contact, electrical shorting, or dielectric breakdown. In the context of PCBs, ESD can lead to the failure of sensitive components, data corruption, and even permanent damage to the board itself. Therefore, designing effective ESD protection circuits is crucial for ensuring the reliability and longevity of electronic devices.
This guide aims to provide beginners with a comprehensive understanding of ESD protection circuit design for PCBs. We will cover the basics of ESD, the importance of ESD protection, key components used in ESD protection circuits, and step-by-step guidelines for designing and implementing these circuits on your PCBs.
Understanding ESD and Its Impact on PCBs
What is ESD?
Electrostatic Discharge (ESD) is the sudden flow of electricity between two electrically charged objects caused by contact, an electrical short, or dielectric breakdown. This discharge can occur when two objects at different potentials come into close proximity or direct contact, resulting in a rapid transfer of charge.
How ESD Affects PCBs
ESD can have several detrimental effects on PCBs and their components:
- Component Damage: Sensitive components, such as integrated circuits (ICs), transistors, and diodes, can be damaged or destroyed by the high voltage and current associated with ESD events.
- Data Corruption: In digital circuits, ESD can cause data corruption or loss, leading to malfunction or failure of the device.
- Latent Defects: ESD can cause latent defects that may not be immediately apparent but can lead to premature failure of the component or PCB over time.
- Operational Disruption: ESD events can disrupt the normal operation of electronic devices, causing temporary or permanent malfunction.
Common Sources of ESD
ESD can originate from various sources, including:
- Human Body: The human body can accumulate static charge through friction and discharge it when touching electronic components.
- Equipment: Improperly grounded equipment can generate and discharge static electricity.
- Environment: Dry environments, low humidity, and certain materials (e.g., plastics) can increase the likelihood of ESD events.
Importance of ESD Protection in PCB Design
Why ESD Protection is Crucial
- Component Reliability: ESD protection ensures the reliability and longevity of sensitive components by preventing damage from static discharge.
- Device Performance: Effective ESD protection maintains the performance and functionality of electronic devices.
- Cost Savings: Preventing ESD-related failures reduces the need for costly repairs, replacements, and recalls.
- Compliance: Many industry standards and regulations require ESD protection in electronic devices to ensure safety and reliability.
ESD Protection Standards
Several standards and guidelines govern ESD protection in electronic design, including:
- IEC 61000-4-2: This standard specifies the immunity requirements and test methods for electronic equipment against ESD.
- ANSI/ESD S20.20: This standard provides guidelines for establishing an ESD control program to protect electronic components from ESD damage.
- JEDEC JESD22-A114: This standard defines the ESD sensitivity testing for integrated circuits.
Key Components for ESD Protection Circuits
1. TVS Diodes (Transient Voltage Suppression Diodes)
TVS diodes are one of the most common components used for ESD protection. They are designed to clamp transient voltages to a safe level, diverting the excess energy away from sensitive components.
- Operation: TVS diodes operate by rapidly conducting when the voltage exceeds a certain threshold, effectively shunting the excess energy to ground.
- Selection Criteria: When selecting a TVS diode, consider parameters such as breakdown voltage, clamping voltage, peak pulse current, and response time.
2. ESD Suppressors
ESD suppressors are specialized components designed to protect against ESD events. They are typically placed at the input/output (I/O) ports of a PCB.
- Operation: ESD suppressors absorb and dissipate the energy from ESD events, preventing it from reaching sensitive components.
- Types: Common types of ESD suppressors include polymer-based suppressors, ceramic suppressors, and silicon-based suppressors.
3. Varistors
Varistors are voltage-dependent resistors that provide ESD protection by clamping transient voltages.
- Operation: Varistors exhibit a high resistance at normal operating voltages but rapidly decrease their resistance when the voltage exceeds a certain threshold, diverting the excess energy.
- Selection Criteria: Key parameters for varistors include clamping voltage, energy absorption capability, and response time.
4. Capacitors
Capacitors can be used in ESD protection circuits to filter out high-frequency noise and transient voltages.
- Operation: Capacitors absorb and store energy from transient voltages, releasing it slowly to prevent damage to sensitive components.
- Selection Criteria: Consider capacitance value, voltage rating, and equivalent series resistance (ESR) when selecting capacitors for ESD protection.
5. Resistors
Resistors can be used in series with signal lines to limit the current flow during an ESD event.
- Operation: Resistors reduce the current flowing through sensitive components, minimizing the risk of damage.
- Selection Criteria: Key parameters include resistance value, power rating, and tolerance.
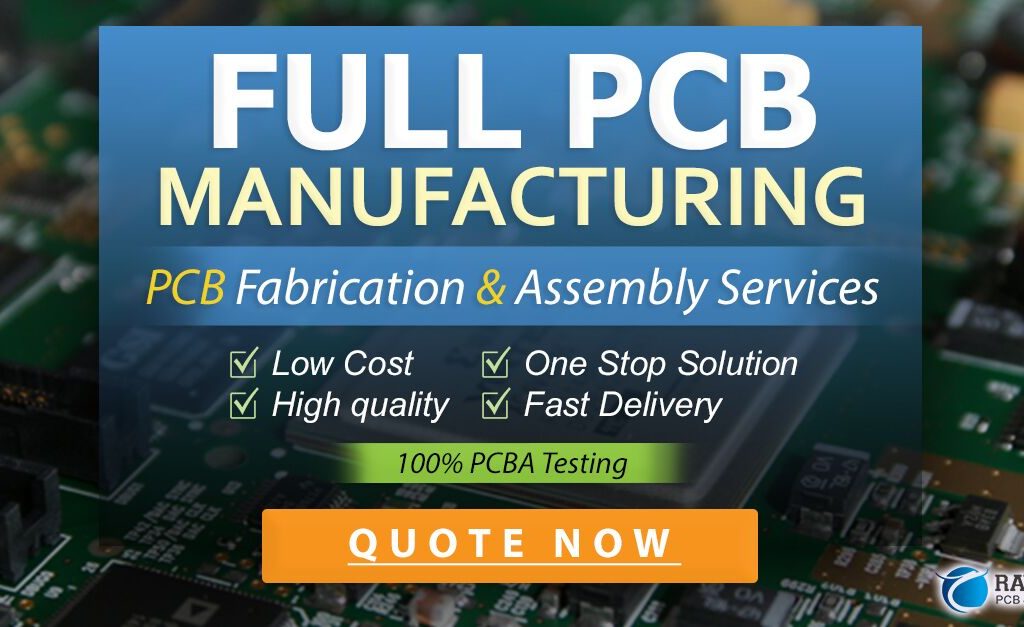
Designing ESD Protection Circuits for PCBs
Step 1: Identify ESD-Sensitive Components and Interfaces
The first step in designing ESD protection circuits is to identify the components and interfaces that are most susceptible to ESD damage. These typically include:
- I/O Ports: USB, HDMI, Ethernet, and other connectors that interface with external devices.
- Sensitive Components: ICs, transistors, diodes, and other components that are vulnerable to ESD.
- Power Supply Lines: Power input and output lines that can carry ESD transients.
Step 2: Select Appropriate ESD Protection Components
Based on the identified ESD-sensitive areas, select the appropriate ESD protection components. Consider the following factors:
- Voltage and Current Ratings: Ensure the components can handle the expected voltage and current levels.
- Response Time: Choose components with fast response times to effectively clamp transient voltages.
- Package Size: Select components that fit within the available space on the PCB.
Step 3: Place ESD Protection Components Strategically
Proper placement of ESD protection components is crucial for effective protection. Follow these guidelines:
- Close to the Source: Place ESD protection components as close as possible to the ESD entry points (e.g., connectors, I/O ports).
- Minimize Trace Length: Keep the traces between the ESD protection components and the sensitive components as short as possible to reduce inductance and improve effectiveness.
- Grounding: Ensure a low-impedance ground path for the ESD protection components to divert the excess energy effectively.
Step 4: Design the PCB Layout for ESD Protection
The PCB layout plays a significant role in ESD protection. Follow these best practices:
- Ground Plane: Use a solid ground plane to provide a low-impedance path for ESD currents.
- Signal Routing: Route sensitive signals away from potential ESD sources and avoid long, parallel traces that can act as antennas for ESD-induced noise.
- Shielding: Use shielding techniques, such as grounded metal enclosures or conductive coatings, to protect sensitive areas from ESD.
Step 5: Simulate and Test the ESD Protection Circuit
Before finalizing the design, simulate and test the ESD protection circuit to ensure its effectiveness.
- Simulation: Use simulation tools to model ESD events and analyze the performance of the protection circuit.
- Testing: Perform ESD testing according to industry standards (e.g., IEC 61000-4-2) to verify the circuit’s ability to withstand ESD events.
Step 6: Implement ESD Control Measures in the Manufacturing Process
In addition to designing ESD protection circuits, implement ESD control measures during the manufacturing process to prevent ESD damage during assembly and handling.
- ESD-Safe Workstations: Use ESD-safe workstations with grounded mats and wrist straps.
- ESD-Safe Packaging: Store and transport components in ESD-safe packaging.
- Training: Train personnel on ESD awareness and proper handling procedures.
Common Mistakes to Avoid in ESD Protection Circuit Design
1. Inadequate Component Selection
Choosing components with insufficient voltage or current ratings can lead to ineffective ESD protection. Ensure that the selected components can handle the expected ESD events.
2. Poor Placement of ESD Protection Components
Placing ESD protection components too far from the ESD entry points can reduce their effectiveness. Always place these components as close as possible to the connectors or I/O ports.
3. Neglecting Grounding
A poor ground connection can render ESD protection components ineffective. Ensure a low-impedance ground path and use a solid ground plane.
4. Overlooking PCB Layout Considerations
Ignoring PCB layout best practices, such as signal routing and shielding, can compromise ESD protection. Pay attention to the layout to minimize ESD risks.
5. Skipping Simulation and Testing
Failing to simulate and test the ESD protection circuit can lead to unexpected failures. Always validate the design through simulation and testing.
Conclusion
Designing effective ESD protection circuits for PCBs is essential for ensuring the reliability and longevity of electronic devices. By understanding the basics of ESD, selecting appropriate protection components, and following best practices in PCB design, you can create robust ESD protection circuits that safeguard your components from static discharge. Remember to simulate and test your designs, and implement ESD control measures during the manufacturing process to further enhance protection. With this beginner’s guide, you are well on your way to mastering ESD protection circuit design and creating reliable, high-performance PCBs.