Introduction
Printed Circuit Boards (PCBs) are the backbone of modern electronics, serving as the foundation for connecting and supporting electronic components. As technology advances, the demand for more complex and compact PCBs has grown, leading to the widespread adoption of multilayer PCB designs. One of the most critical yet often overlooked aspects of PCB design is the annular ring. The annular ring plays a vital role in ensuring the reliability and functionality of a PCB, particularly in multilayer designs where precision and tolerances are paramount.
This article explores the concept of annular rings, their significance in multilayer PCB design, and the importance of staying within tolerances to ensure optimal performance. We will delve into the technical aspects of annular rings, the challenges associated with multilayer PCB design, and best practices for maintaining design integrity.
What Are Annular Rings?
Definition and Purpose
An annular ring is the area of copper pad that surrounds a drilled hole on a PCB. It is the conductive material that remains after a hole is drilled and plated, forming a ring-shaped connection point. Annular rings are essential for creating reliable electrical connections between layers in a multilayer PCB and for mounting through-hole components.
The primary purpose of an annular ring is to ensure a robust mechanical and electrical connection. It provides a surface for soldering components and acts as a conductive pathway for signals or power between layers. Without sufficient annular ring width, the connection may become weak or fail entirely, leading to PCB malfunctions.
Key Parameters of Annular Rings
- Annular Ring Width: The width of the annular ring is the distance from the edge of the drilled hole to the edge of the copper pad. A wider annular ring provides more tolerance for drilling inaccuracies and thermal stress during soldering.
- Drill Size: The size of the drilled hole directly affects the annular ring width. Larger holes reduce the available copper area, while smaller holes require precise drilling to maintain annular ring integrity.
- Copper Thickness: The thickness of the copper layer influences the annular ring’s durability. Thicker copper layers provide stronger connections but increase the overall cost and weight of the PCB.
- Plating Quality: The plating process, which involves depositing a conductive material (usually copper) onto the walls of the drilled hole, is critical for ensuring a reliable annular ring. Poor plating can lead to weak connections or voids in the annular ring.
The Role of Annular Rings in Multilayer PCB Design
Multilayer PCB Overview
Multilayer PCBs consist of multiple layers of conductive material separated by insulating layers. These layers are interconnected using vias, which are plated holes that allow electrical signals to pass between layers. Multilayer PCBs are commonly used in complex electronic devices, such as smartphones, computers, and automotive systems, where high component density and signal integrity are required.
Challenges in Multilayer PCB Design
Designing multilayer PCBs presents several challenges, particularly when it comes to annular rings:
- Layer Alignment: In multilayer PCBs, precise alignment of layers is critical to ensure that vias and annular rings are properly aligned across all layers. Misalignment can lead to incomplete connections or signal integrity issues.
- Thermal Stress: During the soldering process, the PCB is subjected to thermal stress, which can cause the annular ring to crack or delaminate if it is not sufficiently robust.
- Signal Integrity: As the number of layers increases, maintaining signal integrity becomes more challenging. Proper annular ring design is essential to minimize impedance mismatches and signal losses.
- Manufacturing Tolerances: Multilayer PCBs require tight manufacturing tolerances to ensure that all layers and vias are accurately produced. Any deviation from these tolerances can compromise the annular ring’s integrity.
Types of Vias and Their Impact on Annular Rings
Vias are conductive pathways that connect different layers of a multilayer PCB. The type of via used can significantly impact the annular ring’s design and integrity.
1. Through-Hole Vias
Through-hole vias extend through the entire thickness of the PCB, connecting all layers. They are the most common type of via and provide robust connections. However, they require careful annular ring design to ensure reliability, especially in high-density designs.
2. Blind Vias
Blind vias connect an outer layer to one or more inner layers but do not extend through the entire PCB. They allow for higher component density but require precise drilling and plating to maintain annular ring integrity.
3. Buried Vias
Buried vias connect inner layers without reaching the outer layers. They are used in complex designs to save space but are more challenging to manufacture and inspect.
4. Microvias
Microvias are small-diameter vias used in high-density interconnect (HDI) PCBs. They enable finer pitch components and higher routing density but require advanced manufacturing techniques to ensure reliable annular rings.
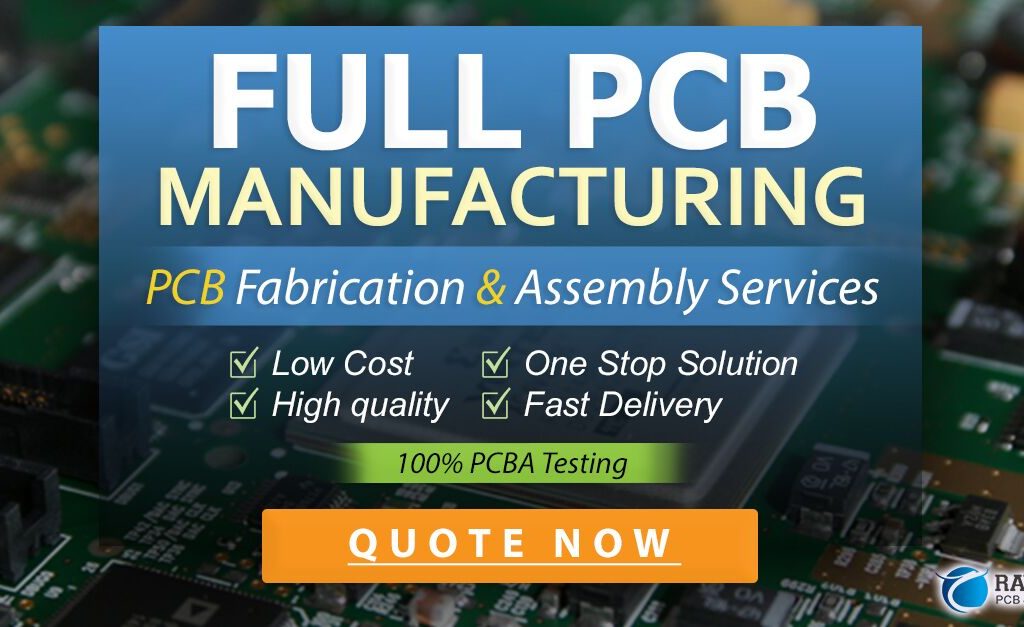
Design for Manufacturability (DFM) and Annular Rings
Design for Manufacturability (DFM) is a critical consideration in multilayer PCB design. DFM involves designing the PCB in a way that facilitates efficient and reliable manufacturing. Key DFM considerations related to annular rings include:
1. Minimum Annular Ring Width
Ensuring that the annular ring width meets the manufacturer’s minimum requirements is essential for reliable connections. A wider annular ring provides more tolerance for drilling inaccuracies and thermal stress.
2. Drill-to-Copper Clearance
Maintaining adequate clearance between the drilled hole and the surrounding copper ensures that the annular ring is not compromised during the drilling process.
3. Aspect Ratio
The aspect ratio, defined as the ratio of the PCB thickness to the diameter of the drilled hole, affects the plating quality and annular ring integrity. A higher aspect ratio makes plating more challenging and can lead to weaker annular rings.
4. Thermal Management
Proper thermal management during the soldering process is crucial to prevent annular ring cracking or delamination. This includes controlling the soldering temperature and duration and using appropriate solder mask materials.
Staying Within Tolerances
Importance of Tolerances in PCB Design
Tolerances in PCB design refer to the allowable deviations from the specified dimensions and properties. Staying within tolerances is crucial for ensuring the PCB’s functionality, reliability, and manufacturability. Key tolerances related to annular rings and multilayer PCB design include:
- Drilling Tolerances: The accuracy of the drilling process directly impacts the annular ring’s width. Staying within the specified drilling tolerances ensures that the annular ring is not compromised.
- Copper Thickness Tolerances: Variations in copper thickness can affect the annular ring’s durability and the PCB’s electrical properties. Adhering to copper thickness tolerances ensures consistent performance.
- Plating Thickness Tolerances: The thickness of the plating material affects the annular ring’s conductivity and mechanical strength. Maintaining plating thickness within tolerances is essential for reliable connections.
- Layer Alignment Tolerances: In multilayer PCBs, the alignment of different layers is critical for signal integrity and power distribution. Staying within layer alignment tolerances ensures that vias and annular rings are properly aligned across layers.
Best Practices for Annular Ring Design in Multilayer PCBs
- Collaborate with Manufacturers: Work closely with PCB manufacturers to understand their capabilities and tolerances. This ensures that your design is feasible and can be produced reliably.
- Use Advanced Design Tools: Utilize PCB design software with built-in DFM checks to identify potential issues early in the design process.
- Optimize Layer Stackup: Carefully plan the layer stackup to minimize signal integrity issues and ensure proper power distribution.
- Conduct Regular Testing: Perform thorough testing and inspection during and after manufacturing to verify that the annular rings meet design specifications.
Conclusion
Annular rings are a critical yet often overlooked aspect of multilayer PCB design. Their role in ensuring reliable electrical connections and mechanical stability cannot be overstated. By understanding the factors that affect annular ring integrity and adhering to design and manufacturing tolerances, engineers can produce high-quality, reliable PCBs that meet the demands of modern electronics.
As technology continues to evolve, the importance of annular rings and multilayer PCB design will only grow. Staying informed about best practices and collaborating closely with manufacturers will be essential for success in this ever-changing field. By prioritizing annular ring design and staying within tolerances, engineers can ensure the longevity and performance of their PCBs in even the most demanding applications.