Printed Circuit Board (PCB) design is a meticulous process that requires attention to detail at every stage. One of the most critical aspects of PCB design is specifying hole size tolerances. Holes in PCBs serve various purposes, including mounting components, creating vias for electrical connections, and facilitating mechanical assembly. The accuracy of these holes is vital for ensuring the proper fit of components, reliable electrical connections, and overall functionality of the board.
Specifying hole size tolerances is not just a technical detail—it has significant implications for manufacturability, cost, and performance. Incorrect or overly tight tolerances can lead to manufacturing challenges, increased costs, and potential failures in the field. On the other hand, overly loose tolerances can result in poor component fit and unreliable connections.
In this article, we will explore five essential tips for specifying PCB hole size tolerance. These tips will help you strike the right balance between precision and practicality, ensuring that your PCB designs are both manufacturable and reliable.
1. Understand the Purpose of the Hole
The first step in specifying hole size tolerance is understanding the purpose of the hole. Different types of holes have different requirements, and the tolerance specifications will vary accordingly.
Types of Holes in PCBs:
- Component Holes: These holes are used for mounting through-hole components, such as resistors, capacitors, and connectors. The size and tolerance of these holes must accommodate the leads of the components while ensuring a secure fit.
- Vias: Vias are used to create electrical connections between different layers of the PCB. They can be through-hole vias, blind vias, or buried vias. The tolerance for vias is critical for ensuring reliable electrical connections.
- Mounting Holes: These holes are used for mechanically mounting the PCB to an enclosure or other structure. The tolerance for mounting holes must ensure a proper fit with screws or other fasteners.
- Tooling Holes: Tooling holes are used for alignment during the manufacturing process. The tolerance for these holes must be tight enough to ensure accurate alignment but not so tight as to make manufacturing difficult.
Considerations:
- Component Leads: For component holes, consider the diameter of the component leads and the required clearance. The hole should be slightly larger than the lead to allow for easy insertion while ensuring a secure fit.
- Via Size: For vias, consider the current-carrying capacity and the required electrical performance. The hole size and tolerance must ensure reliable electrical connections without compromising the integrity of the PCB.
- Mechanical Fit: For mounting holes, consider the size of the screws or fasteners and the required mechanical strength. The hole should provide a secure fit without causing stress on the PCB.
Why This Matters: Understanding the purpose of the hole helps you specify the appropriate tolerance, ensuring that the hole meets its intended function without causing manufacturing challenges.
2. Consider Manufacturing Capabilities and Constraints
The capabilities and constraints of your PCB manufacturer play a significant role in determining the appropriate hole size tolerance. Different manufacturers have different capabilities, and specifying tolerances that are too tight can lead to increased costs and production delays.
Key Factors to Consider:
- Drilling Precision: The precision of the drilling process varies between manufacturers. High-precision drilling can achieve tighter tolerances but may come at a higher cost.
- Material Properties: The type of PCB material (e.g., FR-4, high-frequency laminates) can affect the drilling process. Some materials are more challenging to drill accurately, requiring looser tolerances.
- Plating Requirements: For plated through-holes, the plating process adds a thin layer of metal to the hole walls. This must be accounted for when specifying the hole size and tolerance.
- Manufacturer Guidelines: Most PCB manufacturers provide guidelines for hole size tolerances based on their capabilities. Adhering to these guidelines ensures manufacturability and reduces the risk of production issues.
Common Manufacturing Tolerances:
- Standard Tolerances: For most applications, a standard tolerance of ±0.10 mm (±0.004 inches) is sufficient.
- Tight Tolerances: For high-precision applications, tighter tolerances of ±0.05 mm (±0.002 inches) may be required, but this can increase costs and lead times.
- Loose Tolerances: For less critical applications, looser tolerances of ±0.15 mm (±0.006 inches) may be acceptable, reducing manufacturing complexity and cost.
Why This Matters: Aligning your tolerance specifications with your manufacturer’s capabilities ensures that your design can be produced efficiently and cost-effectively.
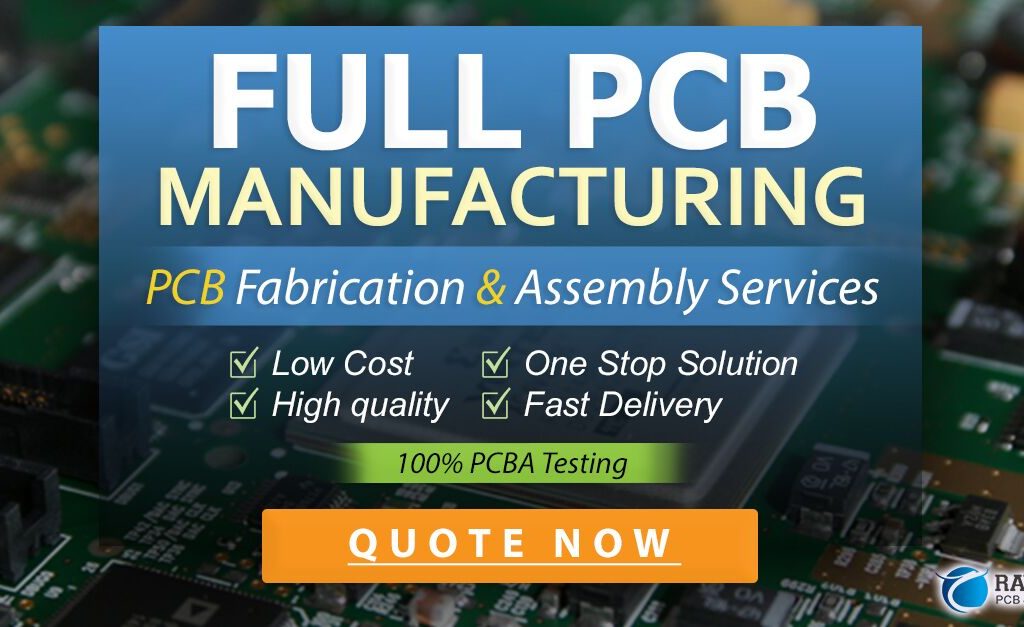
3. Account for Plating and Finish Requirements
Plating and finish requirements have a significant impact on hole size tolerance. Plated through-holes (PTH) and non-plated through-holes (NPTH) have different considerations, and the plating process itself can affect the final hole size.
Plated Through-Holes (PTH):
- Plating Thickness: The plating process adds a thin layer of metal (typically copper) to the hole walls. This reduces the effective diameter of the hole, so the initial hole size must be larger to accommodate the plating.
- Hole Shrinkage: During the plating process, the hole may shrink slightly due to the deposition of metal. This must be accounted for when specifying the hole size and tolerance.
- Aspect Ratio: The aspect ratio (the ratio of hole depth to diameter) affects the uniformity of the plating. Higher aspect ratios can lead to uneven plating, requiring tighter tolerances.
Non-Plated Through-Holes (NPTH):
- No Plating: NPTHs do not require plating, so the hole size remains consistent throughout the manufacturing process. However, the tolerance must still account for drilling precision and material properties.
- Mechanical Fit: NPTHs are often used for mounting holes, so the tolerance must ensure a proper fit with screws or other fasteners.
Surface Finish:
- Finish Thickness: The surface finish (e.g., HASL, ENIG, OSP) adds a thin layer to the PCB surface, including the hole walls. This must be considered when specifying the hole size and tolerance.
- Finish Uniformity: Some finishes are more uniform than others, affecting the consistency of the hole size. For example, ENIG (Electroless Nickel Immersion Gold) provides a more uniform finish compared to HASL (Hot Air Solder Leveling).
Why This Matters: Accounting for plating and finish requirements ensures that the final hole size meets the design specifications and functional requirements.
4. Use Design for Manufacturability (DFM) Principles
Design for Manufacturability (DFM) is a critical consideration when specifying hole size tolerance. DFM principles help ensure that the design can be efficiently and reliably manufactured, reducing the risk of production issues and costly redesigns.
Key DFM Considerations for Hole Size Tolerance:
- Standard Hole Sizes: Using standard hole sizes simplifies the manufacturing process and reduces costs. Avoid specifying custom hole sizes unless absolutely necessary.
- Consistent Tolerances: Applying consistent tolerances across the design simplifies the manufacturing process and reduces the risk of errors.
- Avoiding Overly Tight Tolerances: Overly tight tolerances can increase manufacturing complexity and cost. Specify the tightest tolerance necessary for the application, but no tighter.
- Clear Documentation: Provide clear and comprehensive documentation, including hole size, tolerance, and plating requirements, to ensure that the manufacturer understands the design intent.
Common DFM Mistakes:
- Ignoring Manufacturer Guidelines: Failing to adhere to the manufacturer’s guidelines for hole size tolerance can lead to unmanufacturable designs.
- Overlooking Plating Requirements: Not accounting for plating thickness and hole shrinkage can result in holes that are too small or too large.
- Inconsistent Tolerances: Applying inconsistent tolerances across the design can lead to manufacturing challenges and increased costs.
Why This Matters: Applying DFM principles ensures that your design can be manufactured efficiently and cost-effectively, reducing the risk of production issues and costly redesigns.
5. Validate Tolerances Through Prototyping and Testing
The final step in specifying hole size tolerance is validating the tolerances through prototyping and testing. This ensures that the specified tolerances meet the design requirements and functional needs.
Prototyping:
- Prototype Fabrication: Fabricate a prototype PCB with the specified hole sizes and tolerances to validate the design.
- Component Fit: Test the fit of through-hole components, vias, and mounting hardware to ensure that the holes meet the required specifications.
- Electrical Performance: Test the electrical performance of vias and plated through-holes to ensure reliable connections.
Testing:
- Dimensional Inspection: Use precision measurement tools (e.g., calipers, optical inspection systems) to verify the hole sizes and tolerances.
- Functional Testing: Perform functional testing to ensure that the PCB meets the design requirements and performs as expected.
- Environmental Testing: Conduct environmental testing (e.g., thermal cycling, vibration testing) to ensure that the holes maintain their integrity under real-world conditions.
Iterative Refinement:
- Feedback Loop: Use the results of prototyping and testing to refine the hole size tolerances as needed. This iterative process ensures that the final design meets all requirements.
- Manufacturer Collaboration: Collaborate with the manufacturer to address any issues identified during prototyping and testing, ensuring that the final design is manufacturable.
Why This Matters: Validating tolerances through prototyping and testing ensures that the specified tolerances meet the design requirements and functional needs, reducing the risk of failures in the field.
Conclusion
Specifying PCB hole size tolerance is a critical aspect of PCB design that requires careful consideration of various factors, including the purpose of the hole, manufacturing capabilities, plating requirements, DFM principles, and validation through prototyping and testing. By following the five tips outlined in this article, you can ensure that your PCB designs are both manufacturable and reliable, striking the right balance between precision and practicality.
For your boss, understanding the importance of hole size tolerance and the factors that influence it is essential for making informed decisions, optimizing costs, and ensuring the success of product development. By fostering a deeper understanding of this critical aspect of PCB design, you can help your organization achieve its goals and maintain a competitive edge in the ever-evolving electronics industry.