Rigid flex PCBs (also known as rigid-flexible printed circuit boards) combine rigid and flexible circuit board technologies into a single structure. They contain sections of flexible circuitry to accommodate dynamic flexing requirements, along with rigid sections that provide stability. Rigid flex PCBs enable three-dimensional circuitry design, durability, and miniaturization for advanced electronics and devices. Choosing the right rigid flex PCB manufacturer is crucial for successfully implementing and mass producing these complex boards. This guide examines leading rigid flex PCB manufacturers supporting the needs of various industries worldwide.
Overview of Rigid Flex PCBs
Rigid flex PCBs integrate rigid and flexible PCB technologies into a single board solution. Key characteristics include:
- Rigid sections – Made of typical rigid PCB laminates like FR-4, provide structural stability and leverage dense circuitry.
- Flexible sections – Made of flexible PCB materials like polyimide, enable dynamic flexing and three-dimensional design.
- Folding/bending – Flexible portions allow rigid sections to fold or bend, minimizing electronics size.
- Layer stacking – Rigid flex PCBs support multilayer designs, embedding components.
- High-performance – Superior electrical performance and signal integrity versus discrete rigid and flex PCBs.
- Reliability – Withstand vibration, flexing, thermal extremes, and harsh environments.
- Design freedom – Facilitate innovative, space-saving, lightweight circuit geometries.
With their inherent advantages, rigid flex PCBs are increasingly deployed in applications like:
- Aerospace and defense electronics
- Medical and wearable devices
- Automotive electronics
- Consumer electronics and IoT products
- Industrial equipment
Choosing a capable, experienced rigid flex PCB manufacturer is essential to reliably produce and assemble these complex boards needed for leading-edge products.
Leading Global Rigid Flex PCB Manufacturers
Many PCB manufacturers provide rigid flex PCB services. However, relatively few offer the full spectrum of technical capabilities needed for high complexity and mission-critical applications. Below are 10 of the most renowned global providers of rigid flex PCBs:
TTM Technologies
TTM Technologies is one of the world’s largest PCB manufacturers, with over $2 billion in annual revenue and operations in Asia, Europe, and North America. Their rigid flex PCB capabilities span short runs to high volume production, multilayer designs, and advanced HDI technology supporting component densities up to 20 mil line and space. TTM leverages digital design automation and advanced processes for quick-turn prototypes and ramp-up to mass production. They serve major OEMs in data center, aerospace and defense, automotive, and medical markets.
AT&S
AT&S is Europe’s largest PCB manufacturer and a leading global provider of advanced IC substrates and rigid flex PCBs. Headquartered in Austria, they operate large-scale manufacturing plants in India, China, Korea, and Germany. AT&S rigid flex capabilities include multilayer flex-rigid-flex designs with blind and buried vias, laser drilling, and sequential lamination. They also offer rigid-flex-rigid PCBs using pneumatic pressing to embed components. AT&S serves major European and Asian OEMs in consumer, automotive, and industrial electronics.
Compass Circuits
Compass Circuits specializes in high-reliability, high complexity rigid flex PCBs for defense, aerospace, and medical applications. Based in the US with manufacturing in Asia, they produce prototypes to mid-volume production runs. Compass Circuits leverages processes like laminated sandwiched flex construction for multilayer rigid flex PCBs. They also provide full turnkey design, assembly, and testing services.
Flexium Interconnect
Headquartered in Taiwan with manufacturing throughout Asia, Flexium provides a range of advanced PCBs, including multilayer rigid flex solutions. Flexium’s rigid flex capabilities span short runs to high volume production, blind and buried vias, and stacked microvia structures. They offer design support and one-stop manufacturing for rigid flex PCBs and assemblies. Flexium serves major consumer, automotive, industrial, and networking OEMs.
DSBJ
DSBJ is a high-reliability PCB manufacturer based in China, specializing in rigid flex PCBs for aerospace, defense, telecom infrastructure, and other demanding applications. DSBJ’s rigid flex capabilities include multilayer rigid, multilayer flex, and combination rigid flex designs with laser microvias. They leverage processes like vacuum lamination, cavity PCBs, and embedded components assembly. DSBJ also supports quick-turn engineering prototypes.
Advantages of Rigid Flex PCBs for Product Developers
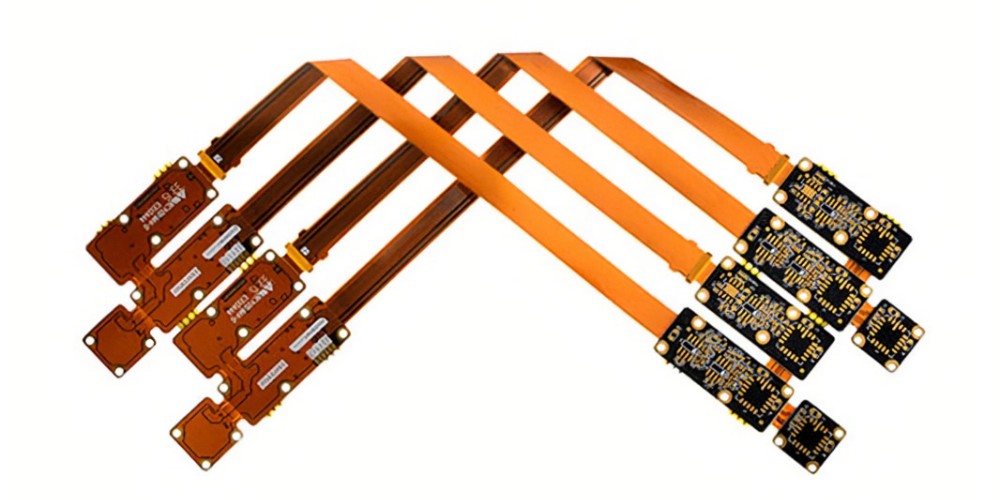
Engineers select rigid flex PCB technology versus discrete rigid boards and flexible circuits for key advantages that benefit product performance, reliability, size, and design flexibility.
Space and Size Efficiencies
Rigid flex PCBs facilitate space and size efficiencies by:
- Eliminating interboard connectors
- Enabling dense 3D circuit geometries
- Supporting ultra-thin, flexible folds and bends
- Embedding discrete components
This enables miniaturization, slimmer profiles, and more compact product industrial designs for applications like wearables and handheld electronics.
Space and Size Benefits | Details |
---|---|
Eliminates Connectors | Rigid flex PCBs integrate both rigid and flexible circuits into one board solution, avoiding the need for connectors between separate rigid and flex boards. |
3D Geometries | Dynamic flexing regions permit more efficient 3-dimensional arrangement of rigid circuitry. |
Folding/Bending | Thin flexible sections allow rigid portions of the PCB to fold or bend within the product. |
Embedded Components | Rigid portions enable embedding and surface mounting of components, reducing product thickness. |
Improved Reliability
Since rigid flex PCBs eliminate interboard connectors and discrete interfaces between rigid and flex sections, they avoid related reliability risks associated with:
- Interfacial misalignment
- Contact fatigue
- Vibration failure
- Intermittent electrical connections
The continuous design also minimizes interfaces that can promote thermal stresses. Reliability benefits make rigid flex PCBs well-suited for defense, aerospace, automotive, and other mission-critical applications.
Design Freedom
Rigid flex PCB technology enables design flexibility not achievable with discrete rigid boards and flex circuits:
- Dynamic flexing actuators
- Moving joints and hinges
- Custom 3D topology
- Conformable wearables
- Complex SMT component placement
This facilitates innovations like foldable mobile devices, advanced robotics, shape-adapting medical devices, and other creative circuit designs.
Performance Benefits
Rigid flex PCBs can offer electrical and signal integrity advantages over assemblies using discrete rigid and flexible boards:
- Improved impedance control
- Reduced parasitic capacitance and crosstalk
- Higher frequency operation
- Lower voltage droop
This derives from eliminating interboard connections and closer integration of rigid digital and flexible high-speed analog circuits within a single board solution.
Trends Driving Adoption of Rigid Flex PCBs
Several technology and market trends are increasing global demand for advanced rigid flex PCBs:
- Miniaturization – Ongoing impetus for smaller, thinner, lighter electronics and devices for portability and invisibility.
- Heterogeneous integration – Combining digital, analog, RF, power, and other components on the same board.
- Internet of Things (IoT) – Need for compact, reliable, interconnected electronic modules and sensors.
- Autonomous mobility – Self-driving vehicles integrating many sensors leveraging rigid flex PCBs.
- Wearable technology – Conformable, high-reliability PCB solutions for body-worn devices.
- Flexible displays – Foldable and rollable displays based on flexible electronics.
- High-speed data – Need for improved signal integrity at high frequencies in data center computing and 5G infrastructure.
Increasingly complex rigid flex PCBs will be essential for continuing innovation and advanced functionality across these areas.
Outlook for Rigid Flex PCBs
Rigid flex PCBs represent an increasingly important technology for next-generation electronics and devices. Continued growth will be fueled by:
- Increasing rigid flex PCB design expertise – More engineers mastering design techniques and CAD tools optimized for rigid flex boards.
- Maturing industry standards – Improving specifications and guidelines for rigid flex materials, design, and manufacturing.
- Expanding manufacturing capacity – Investments in advanced processes, automation, and quality systems essential for rigid flex PCBs.
- Cost reduction – Economies of scale and technology improvements moderating rigid flex PCB costs over time.
With these positive trends, rigid flex PCBs will gain further adoption across critical commercial and defense applications worldwide. Leading manufacturers will continue advancing their technical capabilities to produce highly complex rigid flex circuit boards vital for product innovation.
Frequently Asked Questions
What are some typical applications using rigid flex PCBs?
Some major applications using rigid flex PCB technology include aerospace avionics, missiles and munitions, drones, medical devices like endoscopes and implants, diagnostic imaging equipment, robots and UAVs, automotive sensors and cameras, mobile devices, laptops, AR/VR headsets, advanced smartphones, and more.
What are some key rigid flex PCB design considerations?
Important design factors include determining the optimum layout of rigid and flexible sections, minimizing static and dynamic stresses on flex areas, managing thermomechanical issues, allowing for motion cycles, implementing robust flexible-to-rigid interconnects, and accounting for electrical performance needs like impedance control and high-speed signals.
What fabrication processes are required for rigid flex PCB manufacturing?
Rigid flex PCB fabrication leverages many sequential lamination and imaging steps, advanced drilling/routing methods like laser direct imaging (LDI), plasma processes, specialty flexible circuit materials, and other complex procedures exceeding typical rigid PCB manufacturing.
How are components assembled on rigid flex PCBs?
Assembly techniques include SMT chip placement and reflow on the rigid portions using standard surface mount equipment. Precision tools and fixtures are required for assembling components on the flexible areas to avoid damaging the thin, delicate circuitry.
How should rigid flex PCBs be handled and protected during assembly and testing?
Special handling fixtures and protective covers are used to avoid damaging flexible regions during PCB fabrication, assembly, inspection, and testing processes. The fragility of flex circuits also impacts standard acceptance testing requirements.