Introduction to medical pcb Assembly
Printed Circuit Boards (PCBs) are essential components in modern medical devices. They are used in a wide range of applications, from simple monitoring equipment to complex diagnostic and treatment systems. Medical PCB assembly refers to the process of designing, manufacturing, and assembling PCBs specifically for use in medical devices.
Importance of PCBs in Medical Devices
PCBs play a crucial role in the functioning of medical devices. They provide a reliable and efficient means of interconnecting electronic components, enabling the device to perform its intended function. Some of the key benefits of using PCBs in medical devices include:
- Miniaturization: PCBs allow for the creation of compact and lightweight devices, which is particularly important in portable and wearable medical equipment.
- Reliability: Well-designed and manufactured PCBs ensure the consistent performance and longevity of medical devices, even under demanding conditions.
- Customization: PCBs can be tailored to meet the specific requirements of different medical devices, allowing for optimal functionality and performance.
Designing Medical PCBs
Considerations for Medical PCB Design
Designing PCBs for medical devices requires careful consideration of several factors to ensure the safety, reliability, and effectiveness of the final product. Some of the key considerations include:
- Regulatory compliance: Medical PCBs must adhere to strict regulations and standards, such as the IEC 60601 series for medical electrical equipment.
- Signal integrity: Ensuring the integrity of electrical signals is crucial in medical devices, as any interference or distortion can lead to inaccurate readings or malfunctions.
- Electromagnetic compatibility (EMC): Medical PCBs must be designed to minimize electromagnetic interference (EMI) and ensure compatibility with other electronic devices in the healthcare environment.
- Thermal management: Proper thermal management is essential to prevent overheating and ensure the longevity of the PCB and its components.
- Moisture protection: Medical PCBs may be exposed to various liquids, such as bodily fluids or cleaning agents, making moisture protection a critical consideration in the design process.
Medical PCB Design Software and Tools
Designing medical PCBs requires specialized software and tools to ensure accuracy, efficiency, and compliance with relevant standards. Some popular PCB design software packages used in the medical industry include:
- Altium Designer
- Cadence OrCAD
- Mentor Graphics PADS
- Zuken CR-8000
These software tools offer features such as schematic capture, PCB layout, signal integrity analysis, and design rule checking (DRC) to help designers create high-quality, reliable medical PCBs.
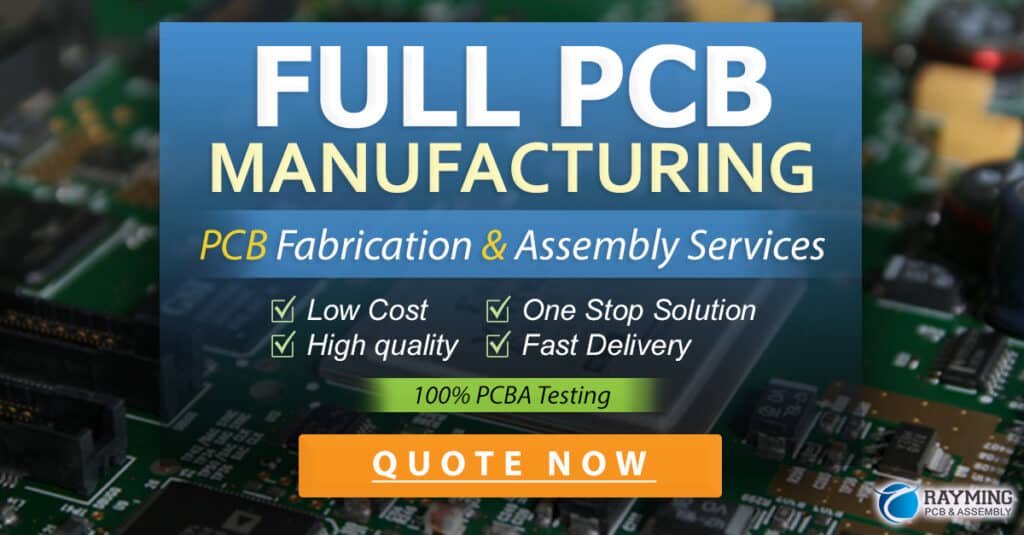
Manufacturing Medical PCBs
Choosing the Right PCB Manufacturer
Selecting a suitable PCB manufacturer is crucial for ensuring the quality and reliability of medical PCBs. When choosing a manufacturer, consider the following factors:
- Experience in medical PCB manufacturing
- Certification and compliance with relevant standards (e.g., ISO 13485, IPC Class 3)
- Quality control processes and testing capabilities
- Ability to handle complex designs and high-mix, low-volume production
- Turnaround time and customer support
Medical PCB Manufacturing Process
The manufacturing process for medical PCBs typically involves the following steps:
- PCB fabrication: The PCB substrate is created, and copper layers are etched according to the design.
- Solder mask application: A protective layer is applied to the PCB to prevent short circuits and improve durability.
- Silkscreen printing: Component labels and other markings are printed on the PCB for easy identification and assembly.
- Surface finish application: A surface finish, such as ENIG (Electroless Nickel Immersion Gold) or HASL (Hot Air Solder Leveling), is applied to protect the copper and improve solderability.
- Electrical testing: The PCB is tested for continuity, short circuits, and other electrical characteristics to ensure proper functionality.
Throughout the manufacturing process, strict quality control measures are implemented to ensure that the medical PCBs meet the required specifications and standards.
Assembling Medical PCBs
Component Selection for Medical PCBs
Selecting the right components for medical PCBs is essential for ensuring the device’s performance, reliability, and safety. When choosing components, consider the following factors:
- Compliance with medical standards and regulations
- Temperature range and thermal stability
- Moisture and corrosion resistance
- Electromagnetic compatibility (EMC)
- Long-term availability and obsolescence management
Medical PCB Assembly Techniques
There are two primary techniques for assembling medical PCBs:
-
Through-hole technology (THT): Components with wire leads are inserted through holes in the PCB and soldered on the opposite side. THT is often used for larger components or when mechanical strength is a priority.
-
Surface mount technology (SMT): Components are mounted directly onto the surface of the PCB and soldered using a reflow process. SMT allows for smaller components and higher circuit density, making it the preferred choice for most modern medical devices.
Automated assembly processes, such as pick-and-place machines and reflow soldering ovens, are commonly used to ensure consistent quality and efficiency in medical PCB assembly.
Quality Control and Testing
Rigorous quality control and testing are essential in medical PCB assembly to ensure the safety and reliability of the final device. Some common quality control and testing procedures include:
- Visual inspection: PCBs are visually inspected for defects, such as solder bridges, component misalignment, or damaged components.
- Automated optical inspection (AOI): Machine vision systems are used to automatically detect assembly defects and ensure conformance to design specifications.
- X-ray inspection: X-ray imaging is used to detect hidden defects, such as voids in solder joints or component placement issues.
- In-circuit testing (ICT): Electrical tests are performed on the assembled PCB to verify the correct functioning of individual components and circuits.
- Functional testing: The assembled PCB is tested under simulated operating conditions to ensure proper performance and functionality.
Challenges in Medical PCB Assembly
Regulatory Compliance
Medical PCBs are subject to stringent regulations and standards to ensure patient safety and device effectiveness. Some of the key regulatory requirements include:
- IEC 60601 series for medical electrical equipment
- ISO 13485 for quality management systems in medical device manufacturing
- FDA 21 CFR Part 820 for quality system regulations in the United States
- European Medical Device Regulation (MDR) for devices sold in the European Union
Ensuring compliance with these regulations throughout the design, manufacturing, and assembly processes can be challenging and requires a deep understanding of the applicable standards and requirements.
Supply Chain Management
Managing the supply chain for medical PCB components can be complex, particularly given the long product lifecycles and strict quality requirements of medical devices. Some of the challenges in medical PCB supply chain management include:
- Ensuring the availability of qualified components and materials
- Managing obsolescence and end-of-life (EOL) components
- Maintaining traceability and documentation throughout the supply chain
- Dealing with lead time variability and potential supply disruptions
Effective supply chain management strategies, such as multi-sourcing, long-term supply agreements, and proactive obsolescence management, can help mitigate these challenges.
Cost Considerations
Medical PCB assembly can be more expensive compared to PCBs for other industries due to the stringent quality requirements, regulatory compliance, and specialized components. However, there are several strategies for managing costs in medical PCB assembly, including:
- Design optimization: Simplifying the PCB design, reducing layer count, and using standard components can help reduce manufacturing costs.
- Supply chain optimization: Collaborating with suppliers, negotiating volume discounts, and implementing just-in-time (JIT) inventory management can help control material costs.
- Process automation: Investing in automated assembly equipment and processes can reduce labor costs and improve efficiency.
- Value engineering: Continuously evaluating and refining the PCB design and assembly process to identify cost-saving opportunities without compromising quality or performance.
Future Trends in Medical PCB Assembly
Miniaturization and Wearable Devices
The trend towards miniaturization and wearable medical devices is driving innovation in medical PCB assembly. Some of the key developments in this area include:
- Flexible and stretchable PCBs: These enable the creation of conformable and wearable devices that can adapt to the body’s shape and movement.
- High-density interconnect (HDI) PCBs: HDI technology allows for smaller vias, finer pitch components, and higher circuit density, enabling the creation of more compact and feature-rich medical devices.
- Embedded components: Integrating passive components, such as resistors and capacitors, directly into the PCB substrate can further reduce the size and improve the performance of medical devices.
Internet of Medical Things (IoMT)
The Internet of Medical Things (IoMT) refers to the growing network of connected medical devices and sensors that can collect, analyze, and transmit health data. IoMT devices rely heavily on PCBs for their functionality and connectivity. Some of the implications of IoMT for medical PCB assembly include:
- Increased demand for wireless connectivity: PCBs for IoMT devices must incorporate wireless communication technologies, such as Bluetooth, Wi-Fi, or cellular, to enable seamless data transfer.
- Enhanced security requirements: As IoMT devices handle sensitive patient data, medical PCBs must incorporate robust security features, such as encryption and secure boot, to protect against unauthorized access or tampering.
- Low-power design: Many IoMT devices are battery-powered, requiring medical PCBs to be designed for low power consumption and energy efficiency.
Additive Manufacturing and 3D Printing
Additive manufacturing and 3D printing technologies are increasingly being explored for medical PCB fabrication and assembly. Some of the potential benefits of these technologies include:
- Rapid prototyping: 3D printing enables faster and more cost-effective prototyping of medical PCBs, allowing for iterative design improvements and shorter development cycles.
- Customization: Additive manufacturing techniques can enable the creation of patient-specific PCBs and devices, tailored to individual anatomy or treatment requirements.
- Complex geometries: 3D printing can produce PCBs with complex shapes and structures that are difficult or impossible to achieve with traditional manufacturing methods.
While additive manufacturing and 3D printing are still in the early stages of adoption for medical PCB assembly, they hold significant potential for revolutionizing the industry in the coming years.
Frequently Asked Questions (FAQ)
- What are the key standards and regulations for medical PCBs?
- IEC 60601 series for medical electrical equipment
- ISO 13485 for quality management systems in medical device manufacturing
- FDA 21 CFR Part 820 for quality system regulations in the United States
-
European Medical Device Regulation (MDR) for devices sold in the European Union
-
What are the main challenges in medical PCB assembly?
- Ensuring regulatory compliance with applicable standards and requirements
- Managing the supply chain for qualified components and materials
- Dealing with obsolescence and end-of-life (EOL) components
-
Balancing cost considerations with stringent quality and performance requirements
-
What are some of the future trends in medical PCB assembly?
- Miniaturization and the development of wearable devices
- Integration of wireless connectivity and security features for Internet of Medical Things (IoMT) devices
-
Adoption of additive manufacturing and 3D printing technologies for rapid prototyping and customization
-
How can I ensure the quality and reliability of my medical PCBs?
- Choose an experienced and certified PCB manufacturer that adheres to relevant standards and regulations
- Implement robust quality control processes, such as visual inspection, automated optical inspection (AOI), and functional testing
-
Conduct thorough component selection and qualification, considering factors such as compliance, temperature range, and moisture resistance
-
What are some strategies for managing costs in medical PCB assembly?
- Optimize the PCB design to simplify manufacturing and reduce layer count
- Collaborate with suppliers and negotiate volume discounts for components and materials
- Invest in process automation to reduce labor costs and improve efficiency
- Continuously evaluate and refine the PCB design and assembly process through value engineering
Conclusion
Medical PCB assembly is a critical aspect of medical device development, ensuring the safety, reliability, and effectiveness of these life-saving technologies. By understanding the key considerations in medical PCB design, manufacturing, and assembly, as well as staying informed about emerging trends and challenges, medical device manufacturers can create innovative and high-quality products that improve patient outcomes and advance the field of healthcare.
As the demand for medical devices continues to grow, driven by factors such as an aging population and the increasing prevalence of chronic diseases, the importance of medical PCB assembly will only continue to rise. By embracing new technologies, such as miniaturization, IoMT, and additive manufacturing, while maintaining a steadfast commitment to quality and regulatory compliance, the medical PCB industry will be well-positioned to meet the evolving needs of patients and healthcare providers in the years to come.