The Advantages of Polyimide PCB
1. High Temperature Resistance
One of the most significant advantages of polyimide PCB is its ability to withstand high temperatures. Polyimide has a glass transition temperature (Tg) of around 360°C and a continuous operating temperature of up to 260°C. This makes it suitable for applications that require exposure to extreme heat, such as in aerospace and automotive industries.
Material | Glass Transition Temperature (Tg) | Continuous Operating Temperature |
---|---|---|
Polyimide | 360°C | 260°C |
FR-4 | 130°C | 130°C |
Polytetrafluoroethylene (PTFE) | 327°C | 260°C |
2. Excellent Mechanical Properties
Polyimide PCBs exhibit excellent mechanical properties, including high tensile strength, low coefficient of thermal expansion (CTE), and good dimensional stability. These properties make polyimide PCBs resistant to stress, vibration, and shock, ensuring reliable performance in harsh environments.
Property | Polyimide | FR-4 |
---|---|---|
Tensile Strength (MPa) | 231 | 124 |
Coefficient of Thermal Expansion (ppm/°C) | 20 | 15 |
Elongation at Break (%) | 72 | 2.5 |
3. Superior Electrical Insulation
Polyimide is an excellent electrical insulator, with a dielectric constant of 3.5 and a dielectric strength of 280 kV/mm. This ensures minimal signal loss and cross-talk, making polyimide PCBs suitable for high-frequency applications and high-speed data transmission.
Material | Dielectric Constant | Dielectric Strength (kV/mm) |
---|---|---|
Polyimide | 3.5 | 280 |
FR-4 | 4.7 | 20 |
PTFE | 2.1 | 60 |
4. Chemical Resistance
Polyimide PCBs are resistant to a wide range of chemicals, including acids, bases, and organic solvents. This makes them suitable for applications that involve exposure to harsh chemical environments, such as in the chemical processing industry.
5. Lightweight and Thin
Compared to other high-performance PCB materials, polyimide PCBs are lightweight and can be manufactured in thin layers. This makes them ideal for applications that require reduced weight and size, such as in portable electronic devices and aerospace components.
Applications of Polyimide PCB
1. Aerospace Industry
Polyimide PCBs are widely used in the aerospace industry due to their ability to withstand extreme temperatures, vibrations, and radiation. They are used in various aerospace applications, including:
- Satellite systems
- Avionics
- Radar systems
- Space exploration vehicles
2. Automotive Industry
In the automotive industry, polyimide PCBs are used in applications that require high temperature resistance and reliability, such as:
- Engine control units (ECUs)
- Transmission control modules
- Brake systems
- Hybrid and electric vehicle power electronics
3. Electronics Industry
Polyimide PCBs are used in various electronic applications that demand high performance and reliability, including:
- High-frequency communication devices
- Medical electronic equipment
- Industrial control systems
- Military and defense electronics
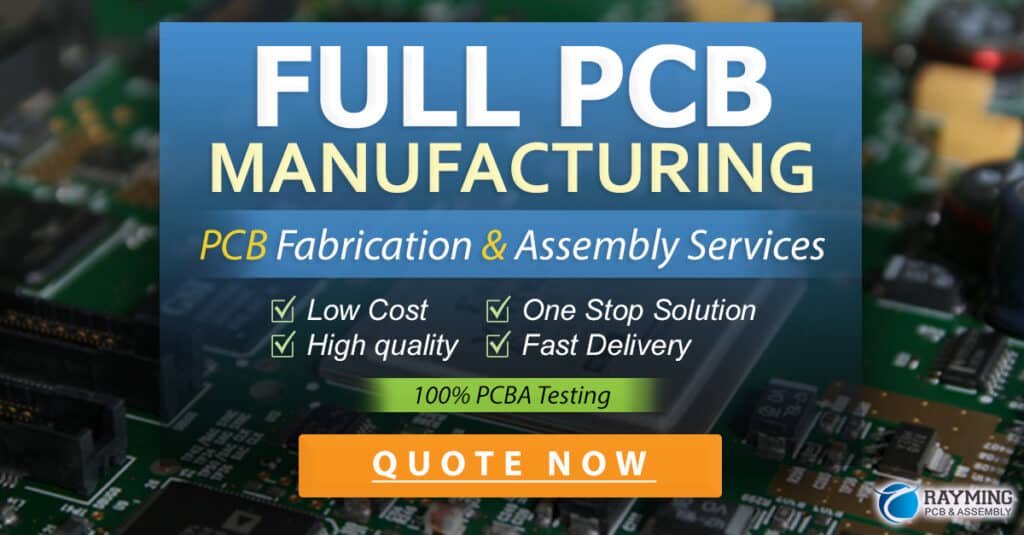
Manufacturing Process of Polyimide PCB
The manufacturing process of polyimide PCB is similar to that of standard PCBs, with a few additional steps to handle the unique properties of polyimide. The process typically involves the following steps:
-
Substrate Preparation: The polyimide film is laminated onto a copper foil using high temperature and pressure.
-
Drilling: Holes are drilled into the laminated polyimide-copper substrate to accommodate components and vias.
-
Plating: The drilled holes are plated with copper to establish electrical connections between layers.
-
Patterning: The desired circuit pattern is transferred onto the copper layer using photolithography and etching processes.
-
Solder Mask Application: A solder mask is applied to the PCB to protect the copper traces and prevent short circuits.
-
Surface Finish: A surface finish, such as ENIG (Electroless Nickel Immersion Gold) or HASL (Hot Air Solder Leveling), is applied to the exposed copper areas to enhance solderability and protect against oxidation.
-
Cutting and Singulation: The manufactured panel is cut into individual PCBs using a routing or punching process.
Challenges in Polyimide PCB Manufacturing
While polyimide PCBs offer numerous advantages, there are some challenges associated with their manufacturing process:
-
High Processing Temperatures: The high glass transition temperature of polyimide requires elevated processing temperatures, which can lead to increased manufacturing costs and potential issues with component compatibility.
-
Dimensional Stability: Although polyimide has a low CTE, ensuring dimensional stability during the manufacturing process can be challenging due to the material’s high processing temperatures.
-
Adhesion Issues: The low surface energy of polyimide can make it difficult to achieve strong adhesion between the polyimide substrate and the copper foil or other materials used in the PCB manufacturing process.
-
Cost: Polyimide PCBs are generally more expensive than standard FR-4 PCBs due to the higher material costs and specialized processing requirements.
Future Trends in Polyimide PCB Technology
As the demand for high-performance electronics continues to grow, polyimide PCB technology is expected to evolve to meet the increasing requirements of various industries. Some of the future trends in polyimide PCB technology include:
-
Thinner and More Flexible PCBs: Advancements in polyimide film technology are enabling the production of thinner and more flexible PCBs, which are essential for wearable electronics and other applications that require conformable devices.
-
Integration with Other Advanced Materials: Researchers are exploring the combination of polyimide with other advanced materials, such as graphene and carbon nanotubes, to enhance the thermal, mechanical, and electrical properties of PCBs.
-
Improved Manufacturing Processes: Efforts are being made to optimize the manufacturing processes for polyimide PCBs, including the development of new lamination techniques and surface treatments to improve adhesion and reduce manufacturing costs.
-
Expansion into New Applications: As the benefits of polyimide PCBs become more widely recognized, their use is expected to expand into new applications, such as 5G communication systems, advanced robotics, and space exploration.
Frequently Asked Questions (FAQ)
-
What is the difference between polyimide PCB and standard FR-4 PCB?
Polyimide PCB uses polyimide as the base material, which offers superior thermal, mechanical, and electrical properties compared to the standard FR-4 material. Polyimide PCBs can withstand higher temperatures, exhibit better mechanical stability, and provide excellent electrical insulation, making them suitable for demanding applications in various industries. -
Can polyimide PCBs be used in high-frequency applications?
Yes, polyimide PCBs are well-suited for high-frequency applications due to their low dielectric constant and high dielectric strength. These properties ensure minimal signal loss and cross-talk, enabling reliable high-speed data transmission. -
Are polyimide PCBs more expensive than standard PCBs?
Yes, polyimide PCBs are generally more expensive than standard FR-4 PCBs due to the higher material costs and specialized processing requirements. However, the superior performance and reliability offered by polyimide PCBs often justify the additional cost in demanding applications. -
How do polyimide PCBs handle extreme temperatures?
Polyimide PCBs have a high glass transition temperature (Tg) of around 360°C and a continuous operating temperature of up to 260°C. This makes them suitable for applications that require exposure to extreme heat, such as in aerospace and automotive industries. -
What are the challenges in manufacturing polyimide PCBs?
The challenges in manufacturing polyimide PCBs include high processing temperatures, ensuring dimensional stability, achieving strong adhesion between the polyimide substrate and other materials, and the higher costs associated with the specialized processing requirements.
In conclusion, polyimide PCB is a high-performance alternative to standard PCB materials, offering exceptional thermal, mechanical, and electrical properties. Its ability to withstand extreme temperatures, resist chemicals, and provide excellent electrical insulation makes it an ideal choice for demanding applications in various industries, including aerospace, automotive, and electronics. As technology continues to advance, polyimide PCB is expected to play an increasingly important role in enabling the development of cutting-edge electronic devices and systems.