Understanding Through-Hole PCB Assembly
The Process of Through-Hole PCB Assembly
The through-hole PCB assembly process involves several steps:
- PCB Design and Fabrication
- The PCB layout is designed using specialized software, considering component placement and routing.
- Holes are drilled into the PCB substrate to accommodate the through-hole components.
-
Copper traces are etched onto the PCB to create electrical connections between components.
-
Component Insertion
- Through-hole components, such as resistors, capacitors, and connectors, are inserted into the drilled holes on the PCB.
-
The component leads are bent to secure them in place temporarily.
-
Soldering
- The PCB is placed on a conveyor belt that carries it through a wave soldering machine.
-
The bottom side of the PCB comes into contact with a molten solder wave, which fills the holes and creates a strong electrical and mechanical connection between the component leads and the PCB.
-
Inspection and Testing
- After soldering, the PCB undergoes visual inspection to ensure proper component placement and soldering quality.
- Automated optical inspection (AOI) systems may be used to detect any defects or irregularities.
- Functional testing is performed to verify that the assembled PCB operates as intended.
Advantages of Through-Hole PCB Assembly
Through-hole PCB assembly offers several advantages:
- Mechanical Stability
- Through-hole components provide a stronger mechanical connection to the PCB compared to surface-mount components.
-
This stability is particularly beneficial for applications that require high durability or are subject to vibrations and shocks.
-
Ease of Manual Assembly
- Through-hole components are easier to handle and manually insert into the PCB compared to tiny surface-mount components.
-
This makes through-hole assembly more suitable for low-volume production or prototyping where manual assembly is preferred.
-
Simplified Rework and Repair
- Through-hole components can be easily removed and replaced using soldering tools, making rework and repair processes more straightforward.
-
This is especially useful for troubleshooting and maintenance purposes.
-
Higher Power Handling Capability
- Through-hole components often have higher power handling capabilities compared to their surface-mount counterparts.
- This makes through-hole assembly a good choice for power electronics and high-current applications.
Limitations of Through-Hole PCB Assembly
Despite its advantages, through-hole PCB assembly has some limitations:
- Lower Component Density
- Through-hole components occupy more space on the PCB due to their leads and the need for drilled holes.
-
This limits the achievable component density compared to surface-mount assembly, where components are placed directly on the PCB surface.
-
Increased PCB Size and Weight
- The use of through-hole components often results in larger and heavier PCBs compared to those with surface-mount components.
-
This can be a disadvantage in applications where space and weight are critical factors, such as portable devices and aerospace systems.
-
Higher Manufacturing Costs
- Through-hole PCB assembly typically requires more manual labor compared to automated surface-mount assembly processes.
-
The drilling of holes and the need for wave soldering also contribute to higher manufacturing costs, especially for high-volume production.
-
Limited Compatibility with High-Frequency Circuits
- Through-hole components have longer leads, which can introduce parasitic inductance and capacitance.
- This can be problematic for high-frequency and high-speed circuits, where signal integrity is crucial.
Applications of Through-Hole PCB Assembly
Through-hole PCB assembly finds applications in various industries and products:
- Industrial Electronics
- Industrial control systems, sensors, and actuators often utilize through-hole components for their robustness and reliability.
-
Examples include motor drives, power supplies, and automation controllers.
-
Automotive Electronics
- Through-hole assembly is commonly used in automotive electronics due to its ability to withstand harsh environmental conditions and vibrations.
-
Applications include engine control units, infotainment systems, and safety-critical components.
-
Power Electronics
- High-power applications, such as power converters, inverters, and motor controllers, often employ through-hole components.
-
The higher power handling capability and mechanical stability of through-hole components make them suitable for these applications.
-
Aerospace and Military Electronics
- Aerospace and military applications demand high reliability and durability, making through-hole assembly a preferred choice.
-
Examples include avionics systems, radar equipment, and communication devices.
-
Medical Devices
- Some medical devices, such as patient monitors and diagnostic equipment, use through-hole components for their reliability and ease of maintenance.
- However, surface-mount technology is increasingly being adopted in medical devices for miniaturization and improved performance.
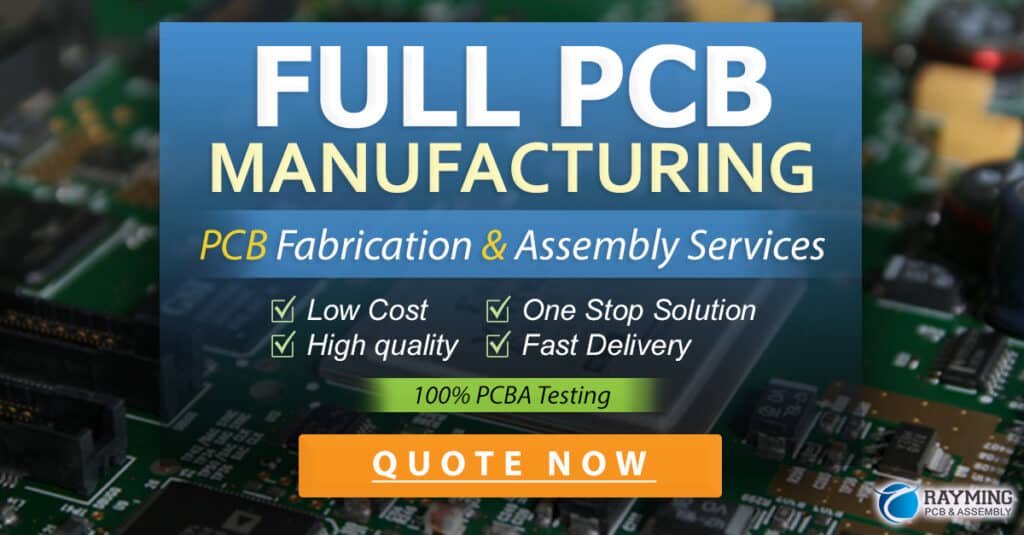
Comparison with Surface-Mount Technology (SMT)
Surface-mount technology (SMT) has gained significant popularity in recent years and has become the dominant assembly method in many industries. Here’s a comparison between through-hole and surface-mount PCB assembly:
Aspect | Through-Hole Assembly | Surface-Mount Assembly |
---|---|---|
Component Placement | Inserted into holes | Placed on PCB surface |
Component Density | Lower | Higher |
PCB Size and Weight | Larger and heavier | Smaller and lighter |
Manufacturing Costs | Higher | Lower |
Automation Capability | Limited | Highly automated |
Mechanical Stability | Stronger | Weaker |
High-Frequency Compatibility | Limited | Better |
Rework and Repair | Easier | More challenging |
Despite the advantages of surface-mount technology, through-hole PCB assembly remains relevant in certain applications where mechanical stability, power handling, and ease of manual assembly are prioritized.
Future Trends and Developments
While surface-mount technology continues to dominate the electronics industry, through-hole PCB assembly is expected to maintain its presence in specific applications. However, there are ongoing efforts to improve the efficiency and capabilities of through-hole assembly:
- Automated Through-Hole Assembly
- Advancements in automation technologies are enabling more efficient and precise through-hole component insertion and soldering processes.
-
Automated through-hole assembly systems can reduce manual labor and improve productivity.
-
Mixed Assembly Techniques
- Many PCB designs now incorporate both through-hole and surface-mount components, leveraging the strengths of each technology.
-
Mixed assembly techniques allow for the integration of components with different package types and requirements on the same PCB.
-
Advanced Soldering Methods
- Innovations in soldering methods, such as selective soldering and pin-in-paste reflow soldering, are improving the efficiency and reliability of through-hole assembly.
-
These methods offer more precise control over the soldering process and can accommodate a wider range of component types.
-
Miniaturization of Through-Hole Components
- Manufacturers are developing smaller and more compact through-hole components to address the demand for miniaturization.
- Smaller through-hole components enable higher component density and help reduce the size and weight of PCBs.
As technology continues to evolve, through-hole PCB assembly will likely adapt and find its place in specific applications where its unique advantages are most valuable.
Frequently Asked Questions (FAQ)
- What is the difference between through-hole and surface-mount PCB assembly?
-
Through-hole assembly involves inserting components into drilled holes on the PCB and soldering them on the opposite side, while surface-mount assembly places components directly on the PCB surface and solders them in place.
-
When is through-hole PCB assembly preferred over surface-mount assembly?
-
Through-hole assembly is preferred when mechanical stability, power handling, ease of manual assembly, and simplified rework and repair are prioritized. It is commonly used in industrial electronics, automotive systems, and high-power applications.
-
Can through-hole and surface-mount components be used together on the same PCB?
-
Yes, mixed assembly techniques allow for the integration of both through-hole and surface-mount components on the same PCB. This approach leverages the strengths of each technology and accommodates components with different package types and requirements.
-
Is through-hole PCB assembly becoming obsolete?
-
While surface-mount technology has become the dominant assembly method in many industries, through-hole assembly remains relevant in specific applications where its advantages are most valuable. It is expected to continue evolving and finding its place in the electronics industry.
-
What are the limitations of through-hole PCB assembly compared to surface-mount assembly?
- Through-hole assembly has lower component density, larger PCB size and weight, higher manufacturing costs, and limited compatibility with high-frequency circuits compared to surface-mount assembly.
Conclusion
Through-hole PCB assembly is a well-established and reliable method for assembling printed circuit boards. Despite the growing popularity of surface-mount technology, through-hole assembly continues to play a significant role in various industries and applications where mechanical stability, power handling, and ease of manual assembly are prioritized.
While surface-mount technology offers advantages such as higher component density, smaller PCB size, and lower manufacturing costs, through-hole assembly remains the preferred choice for applications that demand robustness, durability, and simplified rework and repair processes.
As technology advances, through-hole PCB assembly is expected to evolve and adapt to meet the changing requirements of the electronics industry. Advancements in automation, mixed assembly techniques, and miniaturization of through-hole components will contribute to the continued relevance and effectiveness of this assembly method.
Ultimately, the choice between through-hole and surface-mount PCB assembly depends on the specific requirements and constraints of the application. By understanding the strengths and limitations of each technology, designers and manufacturers can make informed decisions to optimize the performance, reliability, and cost-effectiveness of their electronic products.