The Role of PCB Factories in the Electronics Industry
PCB factories are responsible for the design, fabrication, assembly, and testing of printed circuit boards. They work closely with electronics manufacturers to ensure that the PCBs meet the required specifications and quality standards. The success of many electronic products relies heavily on the quality and reliability of the PCBs produced by these factories.
Types of PCB Factories
There are several types of PCB factories, each focusing on different aspects of the manufacturing process:
-
PCB Fabrication Factories: These factories specialize in the fabrication of bare PCBs. They take the PCB design files and convert them into physical boards using various processes, such as etching, drilling, and plating.
-
PCB Assembly Factories: These factories focus on assembling components onto the bare PCBs. They use techniques like surface mount technology (SMT) and through-hole mounting to attach components to the board.
-
Full-Service PCB Factories: These factories offer both PCB fabrication and assembly services. They can take a project from the design stage through to the finished, assembled PCB.
-
Specialized PCB Factories: Some factories specialize in producing specific types of PCBs, such as high-density interconnect (HDI) boards, flexible PCBs, or rigid-flex PCBs.
The PCB Manufacturing Process
The PCB manufacturing process involves several key steps:
-
PCB Design: The process begins with the creation of a PCB design using specialized software. The design includes the layout of the circuit, the placement of components, and the routing of traces.
-
PCB Fabrication: Once the design is finalized, it is sent to the PCB fabrication factory. The fabrication process involves the following steps:
- Printing the circuit pattern onto a copper-clad board using photoresist and exposure to UV light.
- Etching away the unwanted copper to leave the desired circuit pattern.
- Drilling holes for through-hole components and vias.
- Applying a solder mask to protect the copper traces and prevent short circuits.
-
Adding a silkscreen layer for component labels and other markings.
-
PCB Assembly: After fabrication, the bare PCB is sent to the assembly factory. The assembly process involves:
- Applying a solder paste to the pads where components will be placed.
- Placing the components onto the board using pick-and-place machines.
- Soldering the components to the board using reflow ovens or wave soldering machines.
-
Inspecting the assembled board for defects and performing necessary repairs.
-
PCB Testing: The assembled PCBs undergo rigorous testing to ensure they function as intended. This may include:
- In-circuit testing (ICT) to verify the presence and correct placement of components.
- Functional testing to ensure the board performs as designed.
- Boundary scan testing to check for manufacturing defects.
- Environmental testing to ensure the board can withstand the intended operating conditions.
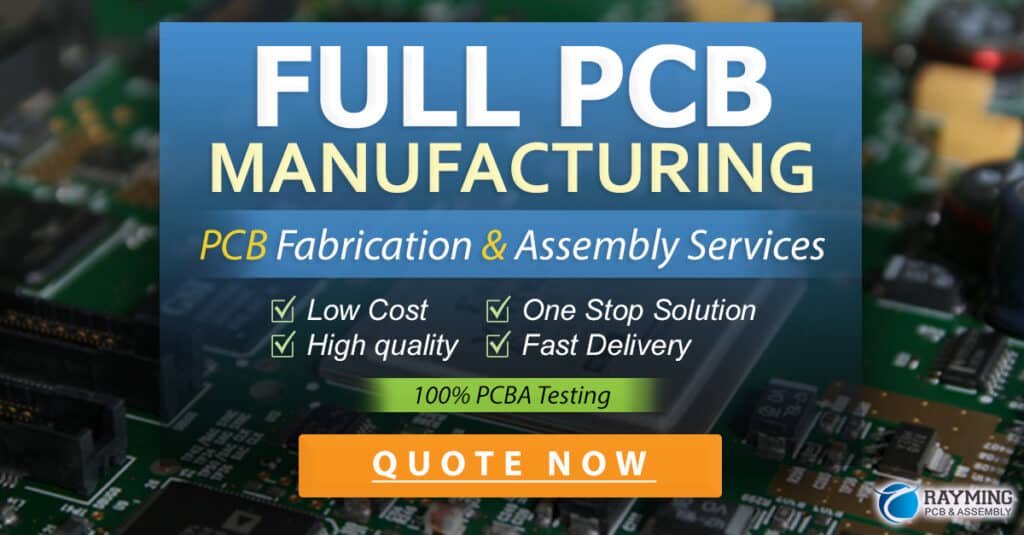
Advantages of Working with a PCB Factory
Working with a professional PCB factory offers several advantages for electronics manufacturers:
-
Expertise: PCB factories have experienced staff and specialized equipment to handle the complex PCB manufacturing process.
-
Quality Control: PCB factories have strict quality control measures in place to ensure that the boards meet the required standards and specifications.
-
Cost-Effectiveness: Outsourcing PCB manufacturing to a factory can be more cost-effective than setting up an in-house production line, especially for small to medium-sized businesses.
-
Scalability: PCB factories can handle large-scale production runs, allowing electronics manufacturers to scale up their production as needed.
-
Access to Advanced Technologies: PCB factories often invest in the latest manufacturing technologies, giving their clients access to advanced capabilities like HDI, embedded components, and more.
Choosing the Right PCB Factory
When selecting a PCB factory to work with, consider the following factors:
-
Capabilities: Ensure that the factory has the necessary capabilities to handle your specific PCB requirements, such as the ability to produce complex designs or use specific materials.
-
Quality Standards: Look for factories that adhere to recognized quality standards, such as ISO 9001, IPC-A-610, and UL.
-
Experience: Choose a factory with a proven track record of producing high-quality PCBs for the electronics industry.
-
Communication: Good communication is essential for a successful partnership. Look for a factory that is responsive, transparent, and easy to work with.
-
Cost: While cost is an important factor, it should not be the only consideration. Strike a balance between cost, quality, and service to ensure the best value for your investment.
The Future of PCB Factories
As the electronics industry continues to evolve, PCB factories must adapt to keep pace with new technologies and demands. Some of the trends shaping the future of PCB manufacturing include:
-
Miniaturization: The demand for smaller, more compact electronic devices is driving the need for smaller, denser PCBs. PCB factories are investing in advanced manufacturing technologies to produce ever-smaller boards with finer features.
-
High-Speed Applications: With the growing demand for high-speed data transmission, PCB factories are developing new materials and techniques to produce boards that can handle high-frequency signals with minimal loss and distortion.
-
Sustainability: There is a growing emphasis on environmentally friendly manufacturing practices. PCB factories are exploring ways to reduce waste, use eco-friendly materials, and improve energy efficiency.
-
Industry 4.0: The adoption of Industry 4.0 technologies, such as automation, robotics, and data analytics, is transforming PCB manufacturing. These technologies enable factories to improve efficiency, quality, and flexibility.
-
Supply Chain Resilience: The COVID-19 pandemic has highlighted the importance of a resilient supply chain. PCB factories are working to diversify their supply sources and improve their risk management strategies to ensure a stable supply of materials and components.
Trend | Impact on PCB Factories |
---|---|
Miniaturization | Investment in advanced manufacturing technologies |
High-Speed Applications | Development of new materials and techniques |
Sustainability | Adoption of eco-friendly practices and materials |
Industry 4.0 | Integration of automation, robotics, and data analytics |
Supply Chain Resilience | Diversification of supply sources and risk management |
Frequently Asked Questions (FAQ)
-
Q: What is the difference between a PCB fabrication factory and a PCB assembly factory?
A: A PCB fabrication factory focuses on producing bare PCBs, while a PCB assembly factory specializes in assembling components onto the bare boards. -
Q: How long does it typically take to manufacture a PCB?
A: The lead time for PCB manufacturing can vary depending on the complexity of the design, the manufacturing processes required, and the factory’s workload. Typical lead times range from a few days to several weeks. -
Q: What quality standards should I look for when choosing a PCB factory?
A: Look for factories that adhere to recognized quality standards, such as ISO 9001 for quality management systems, IPC-A-610 for electronics assembly, and UL for safety. -
Q: Can PCB factories handle both small and large production runs?
A: Yes, most PCB factories are equipped to handle a wide range of production volumes, from small prototype runs to large-scale mass production. -
Q: What should I provide to a PCB factory when placing an order?
A: When placing an order with a PCB factory, you should provide the PCB design files (usually in Gerber format), a bill of materials (BOM) listing the required components, and any special instructions or requirements for the project.
Conclusion
PCB factories play a vital role in the electronics industry, enabling the production of the printed circuit boards that power our modern world. By understanding the PCB manufacturing process, the advantages of working with a professional factory, and the factors to consider when choosing a partner, electronics manufacturers can ensure the success of their projects and bring innovative products to market efficiently and cost-effectively.
As the electronics industry continues to evolve, PCB factories must adapt to new technologies, demands, and challenges. By staying at the forefront of trends like miniaturization, high-speed applications, sustainability, Industry 4.0, and supply chain resilience, PCB factories can remain competitive and continue to support the growth and innovation of the electronics sector.