What is PCB population?
PCB population, also known as PCB assembly or PCB stuffing, is the process of attaching electronic components to a printed circuit board (PCB). This process is crucial in the manufacturing of electronic devices, as it involves placing and soldering various components, such as resistors, capacitors, integrated circuits (ICs), and connectors, onto the PCB. The populated PCB then forms the foundation of the electronic device, enabling it to function as intended.
Methods of PCB population
There are two primary methods of PCB population:
- Through-hole technology (THT)
- Surface mount technology (SMT)
Through-hole technology (THT)
Through-hole technology is the traditional method of PCB population, where component leads are inserted through drilled holes in the PCB and soldered onto the opposite side. This method is known for its strong mechanical bonds and is often used for larger components or in applications that require high reliability, such as military or aerospace electronics.
Advantages of THT:
– Strong mechanical bonds
– Suitable for larger components
– High reliability
Disadvantages of THT:
– Slower assembly process
– Larger PCB size due to the need for drilled holes
– Limited component density
Surface mount technology (SMT)
Surface mount technology is a more modern approach to PCB population, where components are placed directly onto the surface of the PCB and soldered in place. SMT allows for smaller components and higher component density, resulting in more compact and efficient electronic devices.
Advantages of SMT:
– Smaller PCB size
– Higher component density
– Faster assembly process
– Lower cost for high-volume production
Disadvantages of SMT:
– Requires specialized equipment and skills
– More susceptible to thermal stress and vibration
– Difficult to repair or replace individual components
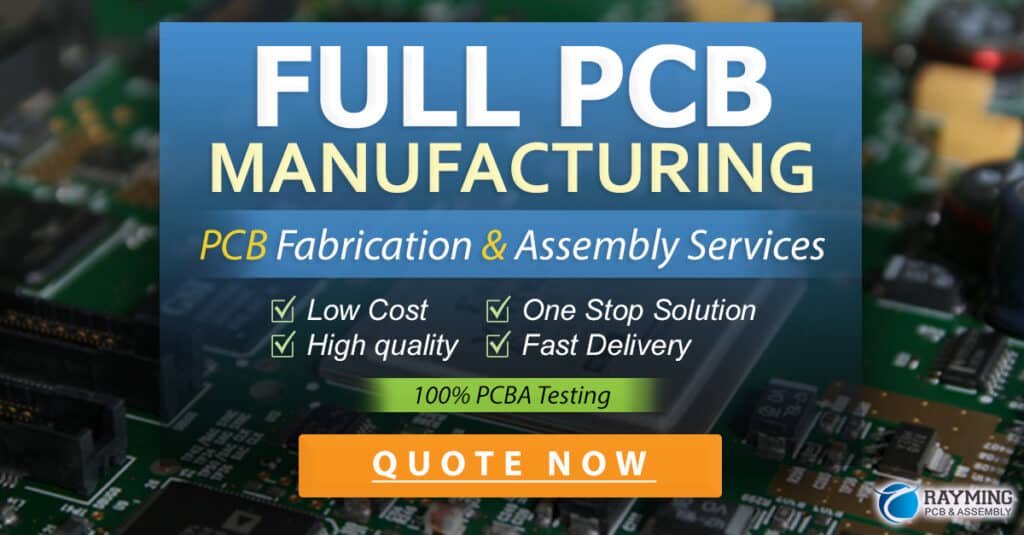
PCB population process
The PCB population process typically involves the following steps:
- Solder paste application
- Component placement
- Reflow soldering
- Inspection and testing
Solder paste application
Solder paste, a mixture of tiny solder spheres and flux, is applied to the PCB pads using a stencil or screen printing process. The stencil ensures that the solder paste is applied accurately and consistently, allowing for proper component attachment during the soldering process.
Component placement
Components are placed onto the PCB using automated pick-and-place machines or by manual placement for low-volume production or prototyping. Automated machines use computer-aided design (CAD) files to determine the precise location of each component and place them accurately on the PCB at high speeds.
Reflow soldering
After component placement, the PCB undergoes reflow soldering, where it is heated in a controlled environment to melt the solder paste and create a strong electrical and mechanical connection between the components and the PCB. The reflow soldering process typically involves the following stages:
- Preheat: The PCB is gradually heated to activate the flux and remove any moisture.
- Soak: The temperature is maintained to allow the components and PCB to reach a uniform temperature.
- Reflow: The temperature is raised above the melting point of the solder, causing the solder to melt and form a connection between the components and PCB pads.
- Cooling: The PCB is cooled down, allowing the solder to solidify and create a strong bond.
Inspection and testing
After the soldering process, the populated PCB undergoes various inspection and testing procedures to ensure the quality and functionality of the assembled board. These procedures may include:
- Visual inspection: Checking for proper component placement, solder joint quality, and any visible defects.
- Automated optical inspection (AOI): Using computer vision systems to detect assembly defects, such as missing or misaligned components, solder bridges, or insufficient solder.
- X-ray inspection: Examining the internal structure of the PCB and solder joints for hidden defects, such as voids or cracks.
- In-circuit testing (ICT): Verifying the functionality of individual components and their interconnections using a bed-of-nails fixture.
- Functional testing: Testing the overall performance of the populated PCB to ensure it meets the desired specifications and requirements.
Factors affecting PCB population quality
Several factors can impact the quality of PCB population:
-
PCB design: A well-designed PCB layout, considering factors such as component placement, trace routing, and thermal management, can facilitate the assembly process and improve the overall quality of the populated board.
-
Component selection: Choosing components with the appropriate package type, size, and thermal characteristics is essential for successful PCB population and long-term reliability.
-
Solder paste quality: Using high-quality solder paste with the correct composition and particle size ensures proper solder joint formation and minimizes defects.
-
Stencil design: A well-designed stencil with optimal aperture sizes and shapes ensures accurate solder paste deposition, reducing the risk of solder bridges or insufficient solder.
-
Pick-and-place accuracy: Accurate component placement is crucial for ensuring proper solder joint formation and preventing assembly defects.
-
Reflow soldering profile: An optimized reflow soldering profile, considering factors such as temperature ramp rates, soak times, and peak temperatures, is essential for achieving high-quality solder joints and minimizing thermal stress on components.
-
Cleanliness: Maintaining a clean environment during the PCB population process, including the use of clean rooms and proper handling procedures, reduces the risk of contamination and improves the overall quality of the assembled board.
Advancements in PCB population technology
PCB population technology has continuously evolved to meet the demands of increasingly complex and miniaturized electronic devices. Some of the recent advancements in PCB population include:
-
3D printing: The use of 3D printing technology in PCB population allows for the creation of complex, three-dimensional PCB structures and the integration of components within the PCB itself, enabling more compact and efficient designs.
-
Flexible and stretchable electronics: The development of flexible and stretchable PCB materials and assembly techniques has enabled the creation of wearable and implantable electronic devices that can conform to the shape of the human body.
-
Embedded components: The integration of passive components, such as resistors and capacitors, within the PCB substrate itself, reduces the number of surface-mounted components and enables more compact and efficient designs.
-
High-density interconnect (HDI) PCBs: HDI PCBs feature finer trace widths, smaller via sizes, and higher layer counts, allowing for the assembly of highly miniaturized and complex electronic devices.
-
Automated optical inspection (AOI) with artificial intelligence (AI): The integration of AI algorithms into AOI systems improves the accuracy and efficiency of defect detection during the inspection process, reducing the risk of assembly errors and improving overall quality control.
PCB population challenges and solutions
Despite advancements in PCB population technology, several challenges remain:
-
Miniaturization: As electronic devices continue to shrink in size, PCB population must adapt to handle increasingly smaller components and tighter spacing requirements. Solutions include the use of high-precision pick-and-place machines, advanced vision systems, and the development of new packaging technologies.
-
High-mix, low-volume production: The trend towards customization and shorter product life cycles has led to an increase in high-mix, low-volume production runs. Flexible and reconfigurable assembly lines, along with rapid changeover capabilities, are essential for meeting these demands.
-
Lead-free soldering: The transition to lead-free soldering, driven by environmental and health concerns, has presented challenges in terms of higher processing temperatures and the need for new solder alloys. Optimizing reflow soldering profiles and using compatible components and PCB finishes are crucial for successful lead-free PCB population.
-
Thermal management: As electronic devices become more powerful and compact, thermal management during PCB population becomes increasingly important. Solutions include the use of thermally-enhanced PCB materials, optimized component placement, and the integration of heat sinks or other cooling mechanisms.
-
Electrostatic discharge (ESD) protection: Electronic components are susceptible to damage from ESD during the PCB population process. Implementing ESD protection measures, such as grounded workstations, ESD-safe packaging, and proper handling procedures, is essential for minimizing the risk of ESD-related defects.
Frequently Asked Questions (FAQ)
-
What is the difference between through-hole and surface mount technology?
Through-hole technology involves inserting component leads through drilled holes in the PCB and soldering them on the opposite side, while surface mount technology places components directly onto the surface of the PCB and solders them in place. SMT allows for smaller components and higher component density compared to THT. -
What is solder paste, and how is it applied to the PCB?
Solder paste is a mixture of tiny solder spheres and flux that is applied to the PCB pads using a stencil or screen printing process. The stencil ensures accurate and consistent application of the solder paste, allowing for proper component attachment during the soldering process. -
What is reflow soldering, and what are the stages involved?
Reflow soldering is the process of heating the PCB in a controlled environment to melt the solder paste and create a strong electrical and mechanical connection between the components and the PCB. The stages involved in reflow soldering are preheat, soak, reflow, and cooling. -
What inspection and testing procedures are used to ensure the quality of populated PCBs?
Inspection and testing procedures for populated PCBs include visual inspection, automated optical inspection (AOI), X-ray inspection, in-circuit testing (ICT), and functional testing. These procedures help identify defects, verify component functionality, and ensure the overall performance of the assembled board. -
What are some of the challenges faced in PCB population, and how can they be addressed?
Some of the challenges faced in PCB population include miniaturization, high-mix low-volume production, lead-free soldering, thermal management, and electrostatic discharge (ESD) protection. These challenges can be addressed through the use of advanced technologies, optimized processes, and proper handling procedures, such as high-precision pick-and-place machines, flexible assembly lines, optimized reflow soldering profiles, thermally-enhanced PCB materials, and ESD protection measures.
PCB Population Method | Advantages | Disadvantages |
---|---|---|
Through-hole technology (THT) | Strong mechanical bonds, suitable for larger components, high reliability | Slower assembly process, larger PCB size, limited component density |
Surface mount technology (SMT) | Smaller PCB size, higher component density, faster assembly process, lower cost for high-volume production | Requires specialized equipment and skills, more susceptible to thermal stress and vibration, difficult to repair or replace individual components |
PCB Population Process | Description |
---|---|
Solder paste application | Solder paste is applied to the PCB pads using a stencil or screen printing process |
Component placement | Components are placed onto the PCB using automated pick-and-place machines or by manual placement |
Reflow soldering | The PCB is heated in a controlled environment to melt the solder paste and create a strong connection between the components and the PCB |
Inspection and testing | The populated PCB undergoes various inspection and testing procedures to ensure quality and functionality |
In conclusion, PCB population is a crucial process in the manufacturing of electronic devices, involving the attachment of electronic components to a printed circuit board using either through-hole or surface mount technology. The process typically involves solder paste application, component placement, reflow soldering, and inspection and testing. Various factors, such as PCB design, component selection, and solder paste quality, can affect the quality of PCB population. As electronic devices continue to advance, PCB population technology must adapt to meet the challenges of miniaturization, high-mix low-volume production, lead-free soldering, thermal management, and ESD protection. By understanding the fundamentals of PCB population and staying informed about the latest advancements and best practices, manufacturers can ensure the production of high-quality, reliable electronic devices that meet the ever-evolving demands of the market.