Introduction to Immersion Tin PCB
Immersion tin (IT) is a surface finish commonly used in the manufacturing of printed circuit boards (PCBs). This process involves depositing a thin layer of tin onto the exposed copper surfaces of the PCB through an electroless plating method. Immersion tin PCB offers several advantages, including excellent solderability, improved shelf life, and compatibility with various assembly processes.
In this article, we will explore the process of immersion tin on PCB, its benefits, and its applications in the electronics industry.
The Importance of Surface Finishes in PCB Manufacturing
Surface finishes play a crucial role in PCB manufacturing by providing protection to the exposed copper surfaces and enhancing the solderability of the board. Some common surface finishes include:
- Hot Air Solder Leveling (HASL)
- Electroless Nickel Immersion Gold (ENIG)
- Organic Solderability Preservative (OSP)
- Immersion Silver (IAg)
- Immersion Tin (IT)
Each surface finish has its own advantages and disadvantages, and the choice of finish depends on factors such as the intended application, cost, and manufacturing requirements.
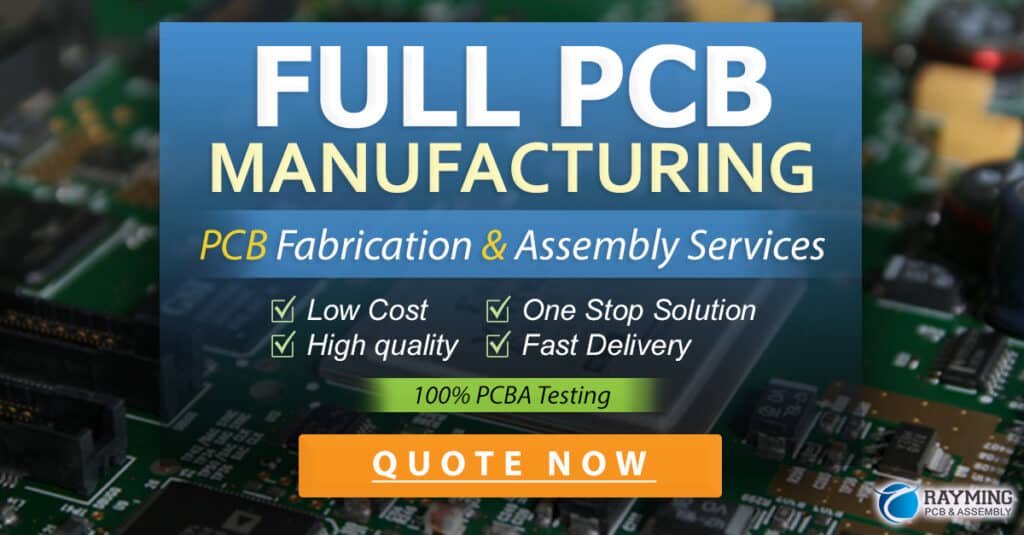
The Immersion Tin Process
The immersion tin process involves several steps to ensure a uniform and adherent tin layer on the PCB surface. The following table outlines the typical steps in the immersion tin process:
Step | Description |
---|---|
1. Cleaning | The PCB is cleaned to remove any contaminants or oxides from the copper surface. |
2. Microetching | A mild etching solution is used to roughen the copper surface, promoting better adhesion of the tin layer. |
3. Pre-dip | The PCB is immersed in a pre-dip solution to prevent oxidation and prepare the surface for tin deposition. |
4. Immersion Tin | The board is immersed in the immersion tin solution, where tin ions replace copper ions on the surface through a displacement reaction. |
5. Rinsing | The PCB is rinsed with deionized water to remove any excess chemicals. |
6. Drying | The board is dried using hot air or an oven to remove any residual moisture. |
Factors Affecting Immersion Tin Performance
Several factors can influence the quality and performance of the immersion tin finish on a PCB:
- Solution composition and pH
- Immersion time and temperature
- Copper surface preparation
- Bath contamination and maintenance
Proper control and monitoring of these factors are essential to achieve a consistent and reliable immersion tin finish.
Benefits of Immersion Tin PCB
Immersion tin PCB offers several advantages over other surface finishes:
-
Excellent solderability: Immersion tin provides a solderable surface that is compatible with various soldering processes, including reflow and wave soldering.
-
Long shelf life: Tin is less prone to oxidation compared to bare copper, resulting in a longer shelf life for PCBs with immersion tin finish.
-
Flat and uniform surface: The immersion tin process produces a flat and uniform surface, which is essential for fine-pitch components and high-density PCB designs.
-
Cost-effective: Compared to other surface finishes like ENIG, immersion tin is a more cost-effective option for many applications.
-
RoHS compliance: Immersion tin is a lead-free and RoHS-compliant surface finish, making it suitable for environmentally friendly electronics manufacturing.
Applications of Immersion Tin PCB
Immersion tin PCBs are used in a wide range of electronics applications, including:
- Consumer electronics
- Automotive electronics
- Telecommunications equipment
- Industrial control systems
- Medical devices
The choice of immersion tin as a surface finish depends on the specific requirements of the application, such as solderability, shelf life, and cost.
Challenges and Limitations of Immersion Tin
While immersion tin offers many benefits, there are some challenges and limitations associated with this surface finish:
-
Tin whiskers: Under certain conditions, tin can form whiskers, which are thin, conductive filaments that can cause short circuits and reliability issues in electronic devices. Proper process control and the use of tin alloys can help mitigate this risk.
-
Limited thickness: The immersion tin layer is relatively thin (typically 0.5-2.0 µm) compared to other surface finishes like ENIG. This may not provide sufficient protection for some applications that require a thicker finish.
-
Copper diffusion: Over time, copper can diffuse through the tin layer, leading to a decrease in solderability and an increased risk of tin whiskers.
Despite these challenges, immersion tin remains a popular choice for many PCB applications due to its cost-effectiveness and excellent solderability.
Immersion Tin vs. Other Surface Finishes
When choosing a surface finish for a PCB, it is essential to consider the advantages and disadvantages of each option. The following table compares immersion tin with other common surface finishes:
Surface Finish | Advantages | Disadvantages |
---|---|---|
Immersion Tin | – Excellent solderability – Long shelf life – Cost-effective |
– Tin whiskers – Limited thickness |
ENIG | – Excellent solderability – Good wear resistance – Long shelf life |
– Higher cost – Possible “black pad” issue |
OSP | – Low cost – Flat surface |
– Limited shelf life – Sensitive to handling |
Immersion Silver | – Excellent solderability – Flat surface |
– Tarnishing over time – Higher cost than IT |
The choice of surface finish depends on the specific requirements of the application, including cost, solderability, shelf life, and reliability.
Quality Control and Testing of Immersion Tin PCB
To ensure the quality and reliability of immersion tin PCBs, several tests and inspections are performed during the manufacturing process:
-
Visual inspection: The PCB surface is visually inspected for any defects, such as discoloration, uneven tin distribution, or contamination.
-
Thickness measurement: The thickness of the immersion tin layer is measured using X-ray fluorescence (XRF) or cross-sectional analysis to ensure it meets the specified requirements.
-
Solderability testing: The solderability of the immersion tin surface is tested using the wetting balance method or the dip-and-look test to assess the wetting properties and the extent of tin coverage.
-
Whisker growth testing: Accelerated life testing, such as high-temperature storage or temperature cycling, is conducted to evaluate the propensity for tin whisker growth on the PCB surface.
-
Adhesion testing: The adhesion of the immersion tin layer to the underlying copper is tested using the tape test method to ensure adequate bonding strength.
Regular monitoring and control of the immersion tin process parameters, along with thorough testing and inspection, help maintain the quality and reliability of immersion tin PCBs.
Future Trends in Immersion Tin PCB
As the electronics industry continues to evolve, new trends and developments are expected to influence the use of immersion tin in PCB manufacturing:
-
Tin alloys: The use of tin alloys, such as tin-bismuth or tin-silver, may become more common to mitigate the risk of tin whiskers and improve the overall performance of the immersion tin finish.
-
Thinner PCBs: As the demand for miniaturization and lightweight electronics grows, thinner PCBs with immersion tin finish may become more prevalent, requiring advancements in process control and materials.
-
Environmental regulations: Stricter environmental regulations may drive the adoption of more eco-friendly and sustainable immersion tin processes, such as the use of recycled tin or the development of new, less hazardous chemistries.
-
Advanced packaging technologies: The increasing use of advanced packaging technologies, such as 3D packaging and system-in-package (SiP), may require new approaches to immersion tin processing to ensure compatibility and reliability.
As the immersion tin process continues to evolve, collaboration between PCB manufacturers, material suppliers, and end-users will be essential to address the challenges and opportunities in this field.
Frequently Asked Questions (FAQ)
-
Q: What is the typical thickness of an immersion tin layer on a PCB?
A: The typical thickness of an immersion tin layer on a PCB ranges from 0.5 to 2.0 µm. -
Q: How does immersion tin compare to ENIG in terms of cost?
A: Immersion tin is generally more cost-effective than ENIG due to the simpler process and lower material costs. -
Q: Can immersion tin be used for high-frequency PCB applications?
A: Yes, immersion tin can be used for high-frequency PCB applications, as it provides a flat and uniform surface that is suitable for fine-pitch components and high-density designs. -
Q: How long does the immersion tin process typically take?
A: The immersion tin process typically takes 15-30 minutes, depending on the specific process parameters and the size of the PCB panels. -
Q: What are the main factors that contribute to tin whisker growth on immersion tin PCBs?
A: The main factors that contribute to tin whisker growth on immersion tin PCBs include compressive stress, temperature fluctuations, and the presence of impurities or contaminants in the tin layer.
Conclusion
Immersion tin is a widely used surface finish in the PCB industry, offering excellent solderability, long shelf life, and cost-effectiveness. The immersion tin process involves several steps to ensure a uniform and adherent tin layer on the PCB surface, and proper control of the process parameters is essential for achieving a high-quality finish.
While there are some challenges and limitations associated with immersion tin, such as the risk of tin whiskers and limited thickness, these can be mitigated through proper process control and the use of tin alloys. As the electronics industry continues to evolve, new trends and developments in immersion tin PCB manufacturing are expected to emerge, driven by the demand for miniaturization, environmental sustainability, and advanced packaging technologies.
By understanding the process, benefits, and applications of immersion tin PCB, electronics manufacturers can make informed decisions when selecting surface finishes for their products, ensuring optimal performance, reliability, and cost-effectiveness.