What is a PCB Core?
A PCB core, also known as a substrate or base material, is the foundation of a printed circuit board. It is a rigid, insulating layer that provides mechanical support and stability to the PCB. The core is typically made from a glass-reinforced epoxy laminate, such as FR-4, which offers excellent electrical insulation properties and mechanical strength.
The core serves several important functions in a PCB:
- Mechanical support: The core provides a stable base for the copper traces, components, and other layers of the PCB.
- Electrical insulation: The glass-reinforced epoxy material of the core ensures that the conductive traces and components are electrically isolated from each other, preventing short circuits and signal interference.
- Thermal stability: The core helps to dissipate heat generated by the components and maintain the overall thermal stability of the PCB.
PCB cores come in various thicknesses, typically ranging from 0.2mm to 3.2mm, depending on the specific requirements of the application. The choice of core thickness depends on factors such as the desired rigidity, the number of layers in the PCB, and the components used.
Types of PCB Cores
There are several types of PCB cores available, each with its own unique properties and applications:
-
FR-4: This is the most common type of PCB core material, consisting of a woven fiberglass fabric impregnated with an epoxy resin. FR-4 offers good electrical insulation, mechanical strength, and heat resistance, making it suitable for a wide range of applications.
-
High Tg FR-4: This variant of FR-4 has a higher glass transition temperature (Tg), which makes it more resistant to heat and suitable for applications that require lead-free soldering or higher operating temperatures.
-
Polyimide: Polyimide cores are known for their exceptional thermal stability and mechanical strength, making them ideal for high-reliability applications in aerospace, military, and medical industries.
-
Aluminum: Aluminum cores are used in metal core PCBs (MCPCBs) to enhance heat dissipation and thermal management. These cores are particularly useful for high-power applications, such as LED lighting and power electronics.
What is PCB Prepreg?
Prepreg, short for pre-impregnated, is a type of dielectric material used in the construction of multi-layer PCBs. It consists of a glass fabric that is pre-impregnated with a partially cured epoxy resin. The prepreg is placed between the PCB cores and copper foil layers during the lamination process to bond them together and provide electrical insulation.
The primary functions of prepreg in a PCB are:
-
Bonding: The partially cured epoxy resin in the prepreg melts and flows during the lamination process, bonding the cores, copper layers, and other prepreg layers together to form a solid, cohesive PCB stack-up.
-
Electrical insulation: The glass fabric and epoxy resin in the prepreg provide electrical insulation between the conductive layers of the PCB, preventing short circuits and signal interference.
-
Filling voids: The prepreg helps to fill any gaps or voids between the cores and copper layers, ensuring a uniform and consistent PCB structure.
Prepregs come in various grades and thicknesses, typically ranging from 0.05mm to 0.2mm, depending on the specific requirements of the PCB design. The choice of prepreg thickness and grade depends on factors such as the desired dielectric constant, the spacing between copper layers, and the signal integrity requirements of the application.
Types of PCB Prepregs
There are several types of PCB prepregs available, each with its own unique properties and applications:
-
Standard FR-4 Prepreg: This is the most common type of prepreg, consisting of a woven fiberglass fabric impregnated with an epoxy resin. Standard FR-4 prepreg offers good electrical insulation, mechanical strength, and thermal stability for general-purpose PCB applications.
-
Low Dk/Df Prepreg: These prepregs have a lower dielectric constant (Dk) and dissipation factor (Df), which makes them suitable for high-speed digital applications that require low signal loss and distortion.
-
Halogen-Free Prepreg: These prepregs are made without halogenated flame retardants, making them more environmentally friendly and compliant with various green initiatives and regulations.
-
High Tg Prepreg: Similar to high Tg FR-4 cores, high Tg prepregs have a higher glass transition temperature, making them more resistant to heat and suitable for lead-free soldering processes and high-temperature applications.
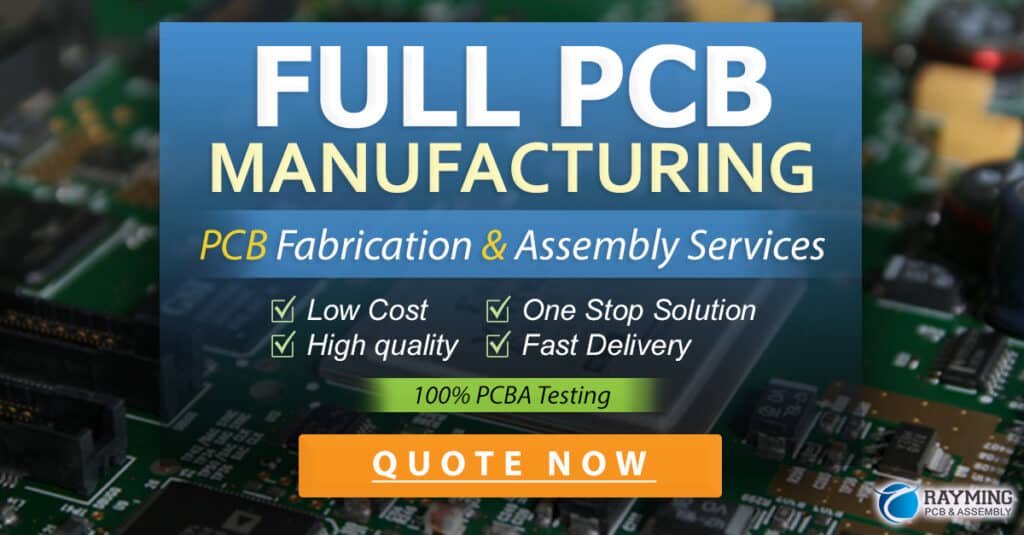
The Role of Prepreg and Core in PCB Plating
PCB plating is an essential process in the manufacturing of printed circuit boards, as it involves the deposition of a thin layer of metal, typically copper, onto the surface of the PCB to create conductive traces, pads, and vias. The choice of prepreg and core materials can have a significant impact on the quality and reliability of the plating process.
Plating Adhesion
The surface properties of the prepreg and core materials can affect the adhesion of the plated copper to the PCB. A rough or textured surface can provide better mechanical anchoring for the plated copper, improving its adhesion to the substrate. Some prepregs and cores are specifically designed with a roughened surface to enhance plating adhesion.
Thermal Stability
During the plating process, the PCB is exposed to various chemicals and elevated temperatures. The thermal stability of the prepreg and core materials is crucial to ensure that the PCB maintains its structural integrity and does not delaminate or warp. High Tg prepregs and cores are particularly suitable for plating processes that involve higher temperatures, such as lead-free soldering.
Chemical Resistance
The prepreg and core materials must also be resistant to the chemicals used in the plating process, such as acids, bases, and oxidizing agents. Any chemical degradation of these materials can lead to poor plating quality, delamination, or even complete failure of the PCB. Choosing prepregs and cores with good chemical resistance is essential for ensuring a reliable and high-quality plating process.
Comparing Prepreg and Core
While both prepreg and core are essential components in the construction of a PCB, they serve different purposes and have distinct characteristics. Here’s a comparison of prepreg and core:
Property | Prepreg | Core |
---|---|---|
Function | Bonds layers together and provides insulation | Provides mechanical support and stability |
Material | Glass fabric pre-impregnated with partially cured epoxy resin | Glass-reinforced epoxy laminate |
Thickness | Typically 0.05mm to 0.2mm | Typically 0.2mm to 3.2mm |
Curing State | Partially cured | Fully cured |
Dielectric Constant | Varies depending on the grade (3.0 to 4.5) | Typically around 4.5 for FR-4 |
Thermal Stability | Depends on the glass transition temperature (Tg) | Generally stable, high Tg versions available |
Chemical Resistance | Varies depending on the resin system | Generally good, but can be affected by high temperatures and harsh chemicals |
Frequently Asked Questions (FAQ)
-
Q: Can I use prepreg as a standalone insulation layer in a PCB?
A: No, prepreg is not designed to be used as a standalone insulation layer. It is meant to be used in conjunction with PCB cores to bond the layers together and provide insulation between them. -
Q: What happens to prepreg during the PCB lamination process?
A: During the lamination process, the partially cured epoxy resin in the prepreg melts and flows, bonding the PCB layers together. The heat and pressure applied during lamination cause the resin to fully cure, creating a solid and cohesive PCB stack-up. -
Q: Can I mix different types of prepregs and cores in the same PCB?
A: Yes, it is possible to use different types of prepregs and cores in the same PCB, depending on the specific requirements of the application. For example, you may use a high Tg core for the outer layers and a low Dk/Df prepreg for the inner layers in a high-speed digital PCB. -
Q: How does the choice of prepreg and core affect PCB plating?
A: The surface properties, thermal stability, and chemical resistance of the prepreg and core materials can impact the quality and reliability of PCB plating. Choosing materials with good plating adhesion, high thermal stability, and excellent chemical resistance is crucial for ensuring a successful plating process. -
Q: What are the most common types of prepreg and core materials used in PCBs?
A: The most common types of prepreg and core materials used in PCBs are FR-4 (flame retardant-4) and its variants, such as high Tg FR-4 and low Dk/Df FR-4. These materials offer a good balance of electrical, mechanical, and thermal properties for a wide range of PCB applications.
In conclusion, understanding the difference between prepreg and core in PCBs is crucial for designing and manufacturing reliable and high-quality printed circuit boards. While the core provides mechanical support and stability, the prepreg bonds the layers together and offers electrical insulation. The choice of prepreg and core materials can significantly impact the PCB plating process, affecting factors such as plating adhesion, thermal stability, and chemical resistance.
By carefully selecting the appropriate prepreg and core materials based on the specific requirements of the application, PCB designers and manufacturers can ensure optimal performance, reliability, and manufacturability of their printed circuit boards.