Introduction to IPC Standards for PCB
In the electronics industry, the IPC (Association Connecting Electronics Industries) is a global trade association that develops and publishes standards for the design, manufacture, and assembly of printed circuit boards (PCBs). These standards ensure consistency, reliability, and quality in the production of PCBs, which are essential components in a wide range of electronic devices.
What are IPC Standards?
IPC standards are a set of guidelines and specifications that define the requirements for various aspects of PCB design, fabrication, and assembly. They cover topics such as material selection, board layout, component placement, soldering, testing, and quality control. By adhering to these standards, manufacturers can produce PCBs that meet the necessary performance and reliability criteria for their intended applications.
Why are IPC Standards Important for PCBs?
IPC standards play a crucial role in the PCB industry for several reasons:
-
Consistency: IPC standards ensure that PCBs are designed and manufactured consistently across different facilities and regions, making it easier for companies to source components and collaborate with various suppliers.
-
Reliability: By following IPC guidelines, manufacturers can produce PCBs that are more reliable and less prone to defects or failures, which is essential for mission-critical applications in industries such as aerospace, defense, and medical devices.
-
Quality control: IPC standards provide a framework for quality control and testing procedures, helping manufacturers identify and address issues early in the production process, reducing waste and improving overall product quality.
-
Communication: IPC standards serve as a common language for PCB designers, manufacturers, and customers, facilitating clear communication and understanding of requirements and expectations.
Key IPC Standards for PCBs
There are several IPC standards that are widely used in the PCB industry. Some of the most important ones include:
IPC-A-600: Acceptability of Printed Boards
IPC-A-600 is a visual inspection standard that defines the acceptable criteria for the cosmetic and functional attributes of PCBs. It covers aspects such as board thickness, hole size, copper plating, solder mask, and marking. This standard helps manufacturers and customers agree on the quality requirements for PCBs and provides a consistent method for evaluating the acceptability of finished boards.
IPC-6012: Qualification and Performance Specification for Rigid Printed Boards
IPC-6012 is a performance specification that defines the requirements for the electrical, mechanical, and environmental properties of rigid PCBs. It covers aspects such as conductor width and spacing, hole size and placement, dielectric materials, and surface finishes. This standard ensures that PCBs meet the necessary performance criteria for their intended applications and provides a basis for qualifying and comparing different PCB manufacturers.
IPC-2221: Generic Standard on Printed Board Design
IPC-2221 is a design standard that provides guidelines for the layout and design of PCBs. It covers topics such as component placement, signal integrity, thermal management, and manufacturability. This standard helps designers create PCBs that are optimized for performance, reliability, and ease of manufacture, reducing the risk of design-related issues and ensuring a smooth transition from design to production.
IPC-7711/7721: Rework, Modification and Repair of Electronic Assemblies
IPC-7711/7721 is a repair and rework standard that provides guidelines for the modification, repair, and rework of electronic assemblies, including PCBs. It covers topics such as component removal and replacement, conductor repair, and laminate repair. This standard helps technicians perform repairs and modifications in a consistent and reliable manner, minimizing the risk of further damage to the PCB or components.
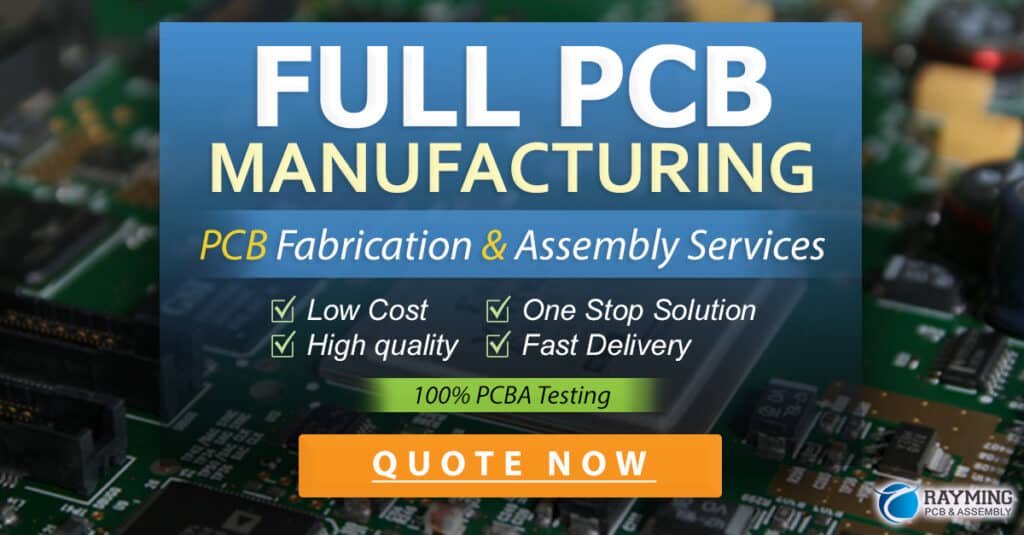
Implementing IPC Standards in PCB Manufacturing
To ensure compliance with IPC standards, PCB manufacturers need to implement a comprehensive quality management system that encompasses all aspects of the production process, from design and material selection to final inspection and testing.
Quality Management System
A quality management system (QMS) is a set of policies, processes, and procedures that an organization uses to ensure that its products and services meet customer requirements and applicable standards. In the context of PCB manufacturing, a QMS should be based on the requirements of IPC standards and should cover all stages of the production process, including:
- Design review and verification
- Material selection and qualification
- Process control and monitoring
- Inspection and testing
- Corrective and preventive actions
- Documentation and record-keeping
By implementing a robust QMS, PCB manufacturers can demonstrate their commitment to quality and compliance with IPC standards, and can continuously improve their processes and products.
Training and Certification
To ensure that personnel involved in PCB manufacturing are competent and knowledgeable about IPC standards, it is important to provide regular training and certification programs. IPC offers a range of training and certification courses for various roles in the electronics industry, including:
- IPC-A-600 Certified IPC Specialist (CIS)
- IPC-A-610 Certified IPC Specialist (CIS)
- IPC/WHMA-A-620 Certified IPC Specialist (CIS)
- IPC J-STD-001 Certified IPC Specialist (CIS)
- IPC-7711/7721 Certified IPC Specialist (CIS)
By investing in training and certification, PCB manufacturers can ensure that their personnel have the necessary skills and knowledge to produce high-quality PCBs that meet IPC standards.
Auditing and Certification
To demonstrate compliance with IPC standards, PCB manufacturers can undergo third-party audits and certification programs. IPC offers several certification programs for PCB manufacturers, including:
- IPC-1791 Trusted Electronic Designer, Fabricator and Assembler Requirements
- IPC-1071 Best Industry Practices for Intellectual Property Protection in Printed Board Manufacturing
- IPC-1401 Supply Chain Risk Management Practices for Printed Circuit Boards
By achieving certification to these standards, PCB manufacturers can provide assurance to their customers that they have the necessary processes and controls in place to produce high-quality, reliable PCBs that meet IPC requirements.
Benefits of Adhering to IPC Standards
Adhering to IPC standards offers several benefits for PCB manufacturers and their customers, including:
Improved Quality and Reliability
By following IPC guidelines for design, manufacture, and assembly, PCB manufacturers can produce boards that are more reliable and less prone to defects or failures. This can help reduce warranty claims, field returns, and customer complaints, and can improve overall customer satisfaction.
Increased Efficiency and Productivity
By using standardized processes and procedures based on IPC standards, PCB manufacturers can streamline their operations, reduce variability, and improve efficiency. This can help reduce cycle times, minimize waste, and increase productivity, leading to lower costs and faster time-to-market.
Enhanced Reputation and Competitiveness
By demonstrating compliance with IPC standards through audits and certifications, PCB manufacturers can enhance their reputation as reliable and quality-focused suppliers. This can help them differentiate themselves from competitors, attract new customers, and retain existing ones.
Reduced Risk and Liability
By adhering to IPC standards, PCB manufacturers can reduce the risk of product failures, safety hazards, or legal liabilities associated with non-compliant or defective products. This can help protect the company’s brand, reputation, and financial well-being.
Frequently Asked Questions (FAQ)
1. What is the difference between IPC-A-600 and IPC-6012?
IPC-A-600 is a visual inspection standard that defines the acceptable criteria for the cosmetic and functional attributes of PCBs, while IPC-6012 is a performance specification that defines the requirements for the electrical, mechanical, and environmental properties of rigid PCBs.
2. Are IPC standards mandatory for PCB manufacturers?
While IPC standards are not legally mandatory, they are widely accepted and expected by customers in the electronics industry. Adhering to IPC standards is often a contractual requirement for PCB manufacturers, and is necessary to compete in the global marketplace.
3. How often should PCB manufacturers undergo IPC audits and certifications?
The frequency of IPC audits and certifications depends on the specific standard and the customer requirements. Some certifications, such as IPC-1791, require annual surveillance audits to maintain certification status. PCB manufacturers should work with their customers and certification bodies to determine the appropriate audit and certification schedule.
4. Can PCB manufacturers deviate from IPC standards?
In some cases, PCB manufacturers may need to deviate from IPC standards to meet specific customer requirements or application needs. However, any deviations should be clearly documented, justified, and agreed upon with the customer. PCB manufacturers should also assess the potential risks and impacts of deviating from IPC standards on product quality, reliability, and compliance.
5. How can PCB designers ensure compliance with IPC standards?
PCB designers can ensure compliance with IPC standards by following the guidelines and requirements outlined in the relevant standards, such as IPC-2221 for PCB design. They should also collaborate closely with PCB manufacturers to ensure that the design is optimized for manufacturability and assembly, and to address any potential issues or challenges early in the design process. PCB designers can also benefit from IPC training and certification programs to enhance their knowledge and skills in designing compliant and high-quality PCBs.
Conclusion
IPC standards play a critical role in ensuring the quality, reliability, and consistency of PCBs in the electronics industry. By adhering to these standards, PCB manufacturers can produce boards that meet the necessary performance and safety requirements, while reducing the risk of defects, failures, and liabilities. Implementing a comprehensive quality management system, investing in training and certification, and undergoing regular audits and certifications are key strategies for PCB manufacturers to demonstrate their commitment to IPC standards and to compete successfully in the global marketplace. As the electronics industry continues to evolve and new technologies emerge, IPC standards will remain essential for ensuring the integrity and performance of PCBs in a wide range of applications, from consumer electronics to mission-critical systems.
Standard | Description |
---|---|
IPC-A-600 | Acceptability of Printed Boards |
IPC-6012 | Qualification and Performance Specification for Rigid Printed Boards |
IPC-2221 | Generic Standard on Printed Board Design |
IPC-7711/7721 | Rework, Modification and Repair of Electronic Assemblies |
Table 1: Key IPC Standards for PCBs
Certification | Description |
---|---|
IPC-1791 | Trusted Electronic Designer, Fabricator and Assembler Requirements |
IPC-1071 | Best Industry Practices for Intellectual Property Protection in Printed Board Manufacturing |
IPC-1401 | Supply Chain Risk Management Practices for Printed Circuit Boards |
Table 2: IPC Certification Programs for PCB Manufacturers