Understanding PCB Mouse Bite
Definition and Characteristics
Mouse bite, also known as “PCB nibbling” or “PCB breakout,” is a common manufacturing defect that occurs during the production of printed circuit boards (PCBs). It is characterized by small, irregular, and unintended notches or indentations along the edges of the PCB. These imperfections resemble the bite marks of a mouse, hence the term “mouse bite.”
Mouse bites are typically caused by issues in the PCB routing or depaneling process, where individual boards are separated from a larger panel. The defects can vary in size, shape, and depth, depending on the severity of the manufacturing issue.
Impact on PCB Functionality and Reliability
PCB mouse bites can have a significant impact on the functionality and reliability of the circuit board. Some of the potential consequences include:
-
Structural weakness: Mouse bites can compromise the structural integrity of the PCB, making it more susceptible to damage during handling, assembly, or operation. The notches can act as stress concentration points, leading to cracks or complete breakage of the board.
-
Electrical issues: Depending on the location and depth of the mouse bites, they may damage or expose copper traces, solder pads, or other conductive elements on the PCB. This can result in short circuits, open circuits, or signal integrity problems, affecting the overall performance of the electronic device.
-
Contamination risks: Mouse bites can create small cavities or crevices that trap moisture, dust, or other contaminants. Over time, these contaminants can lead to corrosion, dendrite growth, or insulation degradation, compromising the long-term reliability of the PCB.
-
Aesthetic concerns: While not directly impacting functionality, mouse bites can detract from the visual appeal and professionalism of the final product. In applications where aesthetics are important, such as consumer electronics or high-end devices, mouse bites may be considered unacceptable.
Causes of PCB Mouse Bite
PCB Routing and Panelization Design
One of the primary causes of PCB mouse bite is improper PCB routing and panelization design. When designing a PCB, engineers must consider how the individual boards will be separated from the larger manufacturing panel. Poor design choices can contribute to the formation of mouse bites:
-
Inadequate clearance: If the spacing between the edge of the PCB and the routing path is too small, there may not be enough material to support clean breakout during depaneling. This can result in tearing or biting of the PCB edge.
-
Weak or narrow PCB borders: Designing PCBs with excessively thin or weak borders around the perimeter can make them more prone to mouse bites during separation. Ensuring adequate border width and using reinforced materials can help mitigate this issue.
-
Incorrect panelization layout: Suboptimal placement of the individual PCBs within the larger panel can lead to uneven stress distribution during depaneling. This can cause mouse bites, especially in areas where multiple boards intersect or where there are sharp corners.
PCB Depaneling Techniques
The choice of PCB depaneling technique and its execution can also contribute to the occurrence of mouse bites. Some common depaneling methods and their associated risks include:
-
V-scoring: V-scoring involves creating shallow grooves along the intended breakout lines of the panel. If the scoring depth is not well-controlled or if the PCB material is brittle, mouse bites can occur during separation.
-
Tab routing: Tab routing uses small tabs to connect individual PCBs to the panel frame. If the tabs are too small or improperly placed, they may cause tearing or biting of the PCB edge during breakout.
-
Punch and die cutting: In this method, a custom-shaped die is used to punch out the individual PCBs from the panel. Misalignment, wear, or damage to the punching tools can lead to inaccurate cuts and mouse bites.
-
Laser cutting: Laser cutting offers high precision and minimal stress on the PCB, but improper settings or focusing issues can still cause mouse bites along the cut edges.
Manufacturing Process Variables
Various factors within the PCB manufacturing process can influence the likelihood of mouse bites:
-
Material selection: The choice of PCB substrate material and its properties, such as brittleness or elasticity, can affect the ease and cleanliness of depaneling. Some materials are more prone to tearing or chipping than others.
-
Copper weight and distribution: The thickness and distribution of copper traces on the PCB can impact the depaneling process. Heavy copper or uneven distribution can create stress points that lead to mouse bites.
-
Lamination and curing: Proper lamination and curing of the pcb layers are essential for maintaining structural integrity. Inadequate bonding or curing can weaken the board and increase the risk of mouse bites during depaneling.
-
Handling and storage: Rough handling, improper storage, or exposure to extreme temperatures and humidity can degrade the PCB material and make it more susceptible to damage, including mouse bites.
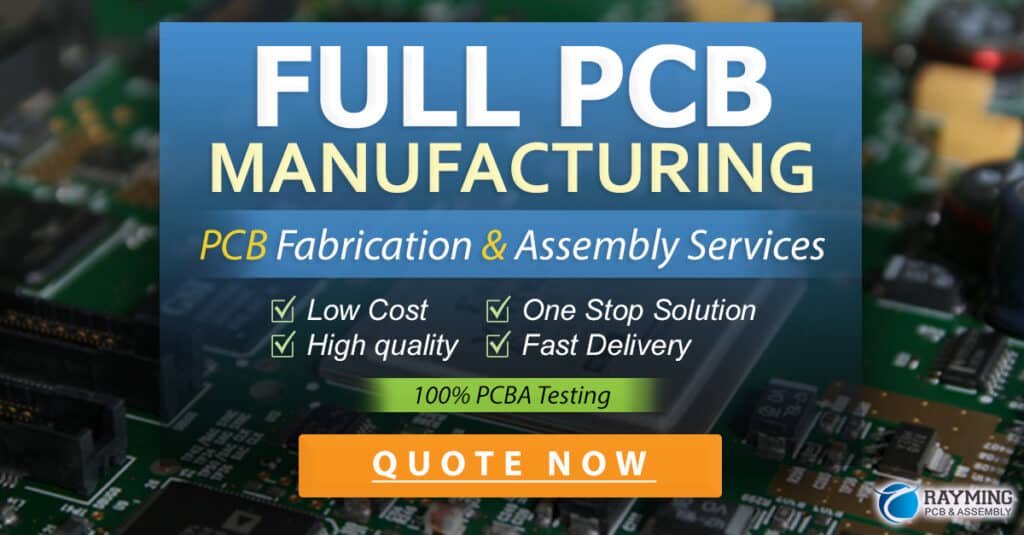
Prevention and Mitigation Strategies
Design Considerations
To minimize the occurrence of PCB mouse bites, designers can implement several strategies in the PCB layout and panelization process:
-
Adequate clearance: Ensure sufficient spacing between the PCB edge and the routed path to provide structural support during depaneling. Follow the manufacturer’s guidelines for minimum clearance requirements.
-
Reinforced borders: Design PCBs with robust borders that can withstand the stresses of depaneling. Consider using thicker material or adding support structures along the perimeter.
-
Optimized panelization: Carefully plan the placement of individual PCBs within the panel to distribute stress evenly and avoid weak points. Use rounded corners and avoid sharp angles where possible.
-
Breakaway tabs: Incorporate breakaway tabs or mousebites into the PCB design to facilitate clean separation. These intentional weak points can help control the breakout process and minimize unintended mouse bites.
Manufacturing Process Improvements
PCB manufacturers can take several steps to reduce the occurrence of mouse bites:
-
Precise depaneling equipment: Invest in high-quality, well-maintained depaneling equipment that offers precise control and minimal stress on the PCB. Regular calibration and maintenance can help ensure optimal performance.
-
Process parameter optimization: Fine-tune the parameters of the depaneling process, such as cutting speed, depth, and pressure, to minimize the risk of mouse bites. Conduct thorough testing and adjust settings as needed.
-
Material selection: Choose PCB substrate materials that are well-suited for the specific application and depaneling method. Consider factors such as flexibility, durability, and compatibility with the manufacturing process.
-
Quality control and inspection: Implement strict quality control measures and perform regular inspections to identify and address mouse bites early in the manufacturing process. Use visual inspection, automated optical inspection (AOI), or other methods to detect and quantify mouse bites.
Post-Processing and Repair
In cases where mouse bites are detected after the depaneling process, there are several post-processing and repair techniques that can be employed:
-
Sanding and smoothing: Minor mouse bites can be manually sanded or smoothed using fine-grit abrasives to remove rough edges and improve the appearance of the PCB.
-
Epoxy filling: For more severe mouse bites that do not impact functionality, epoxy or other filling materials can be used to fill the gaps and reinforce the PCB edge.
-
Rework and repair: If mouse bites have damaged critical traces or components, skilled technicians can perform micro-soldering or other repair techniques to restore functionality. However, this can be time-consuming and costly.
-
Scrap and rework: In some cases, particularly when mouse bites are extensive or impact critical areas, the affected PCBs may need to be scrapped and reworked from scratch.
PCB Mouse Bite Testing and Inspection
Visual Inspection
Visual inspection is the most basic and commonly used method for detecting and assessing PCB mouse bites. Trained operators use magnification tools, such as magnifying glasses or microscopes, to manually examine the edges of the PCB for any signs of biting or irregularities.
Advantages | Disadvantages |
---|---|
Quick and simple to perform | Subjective and prone to human error |
Low cost and readily available | Time-consuming for large batches |
Can identify other surface defects | Limited to visible defects only |
Automated Optical Inspection (AOI)
AOI systems use high-resolution cameras and advanced image processing algorithms to automatically scan and analyze PCBs for various defects, including mouse bites. These systems can quickly and accurately detect even minor irregularities along the PCB edges.
Advantages | Disadvantages |
---|---|
High-speed inspection of large batches | Higher initial investment cost |
Objective and repeatable results | Requires specialized equipment and software |
Automated reporting and data logging | May require operator training and setup |
3D Scanning and Profilometry
3D scanning and profilometry techniques use laser or optical sensors to create detailed 3D models of the PCB surface, including the edges. These methods can provide precise measurements of the depth, width, and shape of mouse bites, enabling quantitative assessment of the defects.
Advantages | Disadvantages |
---|---|
Highly accurate and quantitative | Expensive equipment and software |
Non-contact and non-destructive | Slower than AOI for large batches |
Provides detailed 3D data for analysis | Requires specialized expertise for operation and interpretation |
Microsectioning and Cross-Sectional Analysis
For more in-depth analysis, microsectioning involves cutting the PCB along the affected area and examining the cross-section under a microscope. This destructive method allows for detailed visualization of the internal structure and any damage caused by the mouse bite.
Advantages | Disadvantages |
---|---|
Reveals internal damage and structure | Destructive technique that damages the PCB |
Provides high-resolution images | Time-consuming and labor-intensive |
Enables root cause analysis | Requires specialized equipment and skills |
FAQ
1. Are PCB mouse bites always a critical defect?
Not always. The severity of a mouse bite depends on its size, location, and the specific application of the PCB. Minor mouse bites that do not impact functionality or structural integrity may be acceptable in some cases, while larger or more numerous mouse bites can be critical defects that require rework or scrapping.
2. Can PCB mouse bites be repaired?
In some cases, yes. Minor mouse bites can be sanded or smoothed to remove rough edges, or filled with epoxy for reinforcement. However, if the mouse bites have damaged critical traces or components, the repair process can be complex and may require skilled technicians to perform micro-soldering or other techniques.
3. How can I identify PCB mouse bites during incoming inspection?
PCB mouse bites can be identified through various inspection methods, including visual inspection with magnification tools, automated optical inspection (AOI) systems, 3D scanning and profilometry, or destructive methods like microsectioning. The choice of inspection method depends on factors such as the required accuracy, speed, and available resources.
4. What are the long-term effects of PCB mouse bites on product reliability?
PCB mouse bites can have several long-term effects on product reliability, such as:
– Weakening the structural integrity of the PCB, making it more susceptible to damage or failure over time.
– Creating entry points for moisture, dust, or other contaminants that can lead to corrosion or insulation issues.
– Causing intermittent or permanent electrical faults if the mouse bites damage critical traces or components.
These effects can potentially lead to premature product failure or reduced performance in the field.
5. How can I work with my PCB manufacturer to minimize the occurrence of mouse bites?
To minimize the occurrence of PCB mouse bites, it is important to have open communication and collaboration with your PCB manufacturer. Some key steps include:
– Clearly communicating your design requirements, including any specific guidelines for clearance, border width, or panelization.
– Reviewing and discussing the proposed manufacturing process, depaneling methods, and quality control measures with the manufacturer.
– Establishing acceptable quality limits (AQL) for mouse bites and other defects, and agreeing on inspection and testing procedures.
– Regularly monitoring and reviewing the quality of the delivered PCBs and providing feedback to the manufacturer for continuous improvement.
By working closely with your PCB manufacturer and addressing potential issues proactively, you can significantly reduce the risk of mouse bites and ensure a more reliable and consistent PCB supply chain.