Table of Contents
- Introduction to pcb panelization
- Benefits of PCB Panelization
- PCB Panelization Techniques
- Tab Routing
- V-Scoring
- Mouse Bites
- Considerations for PCB Panelization
- Panel Size and Material
- PCB Orientation and Spacing
- Tooling and Fiducial Marks
- Depaneling Methods
- PCB Panelization Design Guidelines
- PCB Panelization and Assembly
- Challenges in PCB Panelization
- Future of PCB Panelization
- Frequently Asked Questions (FAQ)
- Conclusion
Introduction to PCB Panelization
PCB panelization is the process of arranging multiple individual PCB designs on a larger panel for manufacturing purposes. This technique is widely used in the electronics industry to optimize production efficiency and reduce costs. By grouping several PCBs on a single panel, manufacturers can process them simultaneously, minimizing handling time and material waste.
The panelization process involves careful planning and design to ensure that the individual PCBs can be easily separated from the panel after fabrication. Various techniques are employed to achieve this, such as tab routing, V-scoring, and mouse bites, which will be discussed in detail later in this article.
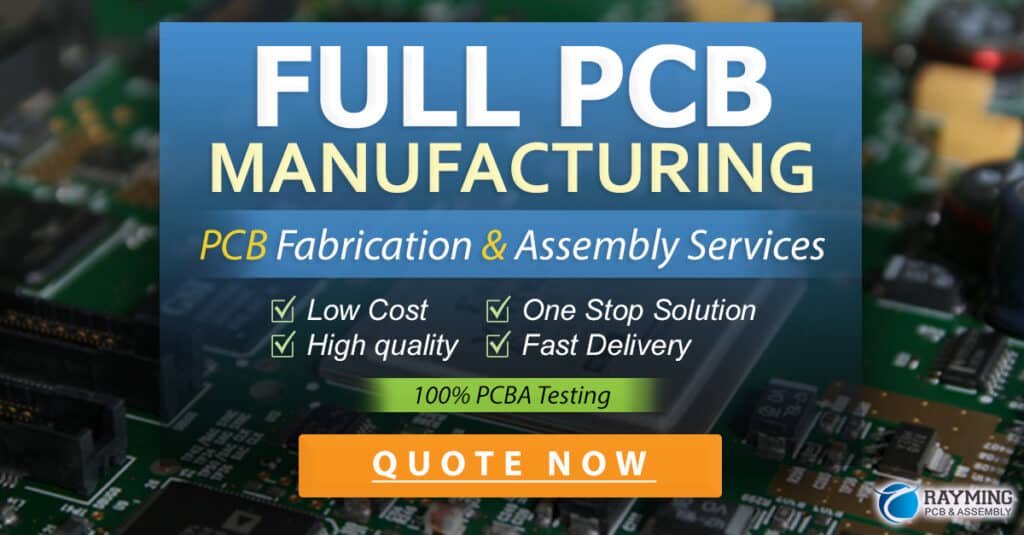
Benefits of PCB Panelization
PCB panelization offers several advantages to both manufacturers and customers:
-
Cost reduction: By processing multiple PCBs on a single panel, manufacturers can reduce material waste, setup time, and handling costs, resulting in lower overall production costs.
-
Increased efficiency: Panelization allows for the simultaneous fabrication of several PCBs, significantly reducing the time required for production and increasing throughput.
-
Improved consistency: When multiple PCBs are manufactured on the same panel, they are subjected to the same production conditions, ensuring greater consistency in quality and performance across the batch.
-
Easier handling: Panelized PCBs are more convenient to handle during the assembly process, as they can be loaded into pick-and-place machines and other equipment more efficiently.
-
Reduced lead times: With increased production efficiency, manufacturers can deliver finished PCBs to customers more quickly, reducing overall lead times.
PCB Panelization Techniques
There are several techniques used in PCB panelization, each with its own advantages and considerations. The choice of technique depends on factors such as the size and shape of the individual PCBs, the required panel strength, and the depaneling method to be used.
Tab Routing
Tab routing involves creating small tabs that connect the individual PCBs to the panel frame. These tabs are milled or routed out during the depaneling process, separating the PCBs from the panel. Tab routing is a popular choice for its simplicity and ease of depaneling.
Advantages:
– Simple and cost-effective
– Suitable for a wide range of PCB sizes and shapes
– Easy to depanel using manual methods or automated equipment
Considerations:
– Tabs can leave behind small protrusions on the PCB edges, which may require additional processing
– The number and size of tabs must be carefully designed to ensure panel strength and easy depaneling
V-Scoring
V-scoring involves creating V-shaped grooves along the edges of the individual PCBs. These grooves weaken the panel material, allowing the PCBs to be easily snapped out of the panel. V-scoring is often used for smaller PCBs and those with irregular shapes.
Advantages:
– Produces clean, smooth edges on the depaneled PCBs
– Suitable for smaller PCBs and irregular shapes
– Allows for easy manual depaneling
Considerations:
– V-scored panels may be more prone to warping or bending during handling
– The depth and angle of the V-grooves must be carefully controlled to ensure easy depaneling without compromising panel strength
Mouse Bites
Mouse bites, also known as perforations, are small, closely spaced holes drilled along the edges of the individual PCBs. These holes weaken the panel material, allowing the PCBs to be easily snapped out. Mouse bites are often used in combination with tab routing or V-scoring.
Advantages:
– Provides additional weakening of the panel material for easier depaneling
– Can be used in combination with other panelization techniques
– Suitable for a wide range of PCB sizes and shapes
Considerations:
– The size, spacing, and number of mouse bites must be carefully designed to ensure easy depaneling without compromising panel strength
– Mouse bites may leave behind small rough edges on the depaneled PCBs, which may require additional processing
Considerations for PCB Panelization
When designing a panelized PCB, several factors must be taken into account to ensure optimal results.
Panel Size and Material
The size of the panel is determined by the dimensions of the individual PCBs and the number of PCBs to be included on the panel. Standard panel sizes are typically used to maximize material usage and compatibility with manufacturing equipment.
The choice of panel material depends on the requirements of the final application, such as the desired electrical properties, thermal stability, and mechanical strength. Common panel materials include FR-4, aluminum-backed PCBs, and flexible substrates.
PCB Orientation and Spacing
The orientation and spacing of the individual PCBs on the panel should be carefully considered to maximize material usage and minimize waste. PCBs can be arranged in various patterns, such as in a grid or a staggered layout, depending on their size and shape.
Adequate spacing between the PCBs is necessary to ensure panel strength and to accommodate any panelization features, such as tabs or V-grooves. The spacing should also take into account the depaneling method to be used, as some methods may require additional clearance.
Tooling and Fiducial Marks
Tooling holes and fiducial marks are essential features in PCB panelization. Tooling holes are used to align and secure the panel during the manufacturing process, ensuring accurate registration of the layers and consistent results.
Fiducial marks are precise reference points used by automated assembly equipment to accurately place components on the PCBs. These marks should be clearly visible and properly positioned to ensure accurate alignment during assembly.
Depaneling Methods
The choice of depaneling method is an important consideration in PCB panelization. The most common methods include:
-
Manual depaneling: Suitable for low-volume production and prototyping, manual depaneling involves using hand tools to break the PCBs out of the panel along the panelization features.
-
Machine depaneling: Automated depaneling equipment, such as routers or punches, can be used for higher-volume production. These machines offer greater precision and consistency compared to manual methods.
-
Laser depaneling: Laser cutting technology can be used to cut the PCBs out of the panel with high precision and minimal stress on the components. This method is suitable for high-density designs and sensitive components.
The depaneling method should be selected based on the panelization technique used, the volume of production, and the requirements of the final application.
PCB Panelization Design Guidelines
To ensure successful PCB panelization, designers should follow best practices and guidelines:
-
Keep panelization in mind from the start: Consider panelization requirements early in the PCB design process to avoid potential issues later on.
-
Use standard panel sizes: Whenever possible, design your PCBs to fit within standard panel sizes to maximize material usage and compatibility with manufacturing equipment.
-
Provide adequate spacing: Ensure sufficient spacing between the individual PCBs on the panel to accommodate panelization features and allow for easy depaneling.
-
Use appropriate panelization techniques: Select the panelization technique that best suits your PCB size, shape, and depaneling requirements.
-
Include tooling holes and fiducial marks: Incorporate properly sized and positioned tooling holes and fiducial marks to ensure accurate registration and alignment during manufacturing and assembly.
-
Consider depaneling methods: Design your panelization features with the intended depaneling method in mind, ensuring that the PCBs can be easily and cleanly separated from the panel.
-
Verify your design: Always review your panelization design with your PCB manufacturer to ensure that it meets their requirements and capabilities.
PCB Panelization and Assembly
PCB panelization plays a crucial role in the assembly process, as it allows for the efficient handling and placement of components on the individual PCBs.
Panelized PCBs are typically loaded into pick-and-place machines, which use the fiducial marks to accurately position and orient the panel. The machines then place the components on the individual PCBs according to the assembly data.
After component placement, the panel undergoes additional assembly processes, such as soldering, inspection, and testing. Once the assembly is complete, the individual PCBs are depaneled using the chosen method and prepared for final packaging and shipping.
Challenges in PCB Panelization
Despite its many benefits, PCB panelization also presents some challenges that designers and manufacturers must address:
-
Warping and bowing: Panelized PCBs may be more susceptible to warping and bowing due to the uneven distribution of material and the stresses introduced by the panelization features. Proper panel design and handling can help minimize these issues.
-
Depaneling stress: The depaneling process can introduce stress on the individual PCBs and their components, potentially causing damage or affecting performance. Careful design of the panelization features and the use of appropriate depaneling methods can help mitigate these risks.
-
Material waste: While panelization helps reduce overall material waste, some waste is still inherent in the process due to the spacing between the individual PCBs and the panelization features. Optimal panel design and layout can help minimize this waste.
-
Increased complexity: Panelization adds an extra layer of complexity to the PCB design and manufacturing process, requiring careful planning and coordination between designers, manufacturers, and assemblers.
Future of PCB Panelization
As the electronics industry continues to evolve, PCB panelization techniques and technologies are also advancing to meet new challenges and requirements.
Some of the trends and developments in PCB panelization include:
-
Advanced materials: The use of new, high-performance materials, such as advanced composites and ceramics, may require the development of new panelization techniques and guidelines.
-
Miniaturization: As PCBs become smaller and more densely populated, panelization techniques must adapt to ensure proper handling and depaneling of these miniaturized designs.
-
Automation: Continued advancements in automated manufacturing and assembly equipment, including depaneling machines, will help improve the efficiency and precision of the panelization process.
-
3D printing: The growing use of 3D printing technologies in PCB fabrication may lead to new panelization approaches and considerations.
As these trends continue to shape the electronics industry, PCB panelization will remain an essential aspect of PCB manufacturing, evolving to meet the changing needs of designers and end-users.
Frequently Asked Questions (FAQ)
-
What is the purpose of PCB panelization?
PCB panelization is used to maximize manufacturing efficiency and reduce costs by allowing multiple individual PCBs to be fabricated and assembled simultaneously on a larger panel. -
What are the most common PCB panelization techniques?
The most common PCB panelization techniques are tab routing, V-scoring, and mouse bites. Each technique has its own advantages and considerations, and the choice depends on factors such as PCB size, shape, and depaneling requirements. -
How does PCB panelization affect the assembly process?
Panelized PCBs are easier to handle during the assembly process, as they can be loaded into pick-and-place machines and other equipment more efficiently. The panelization features, such as fiducial marks, help ensure accurate component placement on the individual PCBs. -
What are some challenges associated with PCB panelization?
Some challenges in PCB panelization include warping and bowing of the panels, stress introduced during the depaneling process, material waste, and increased complexity in design and manufacturing. -
How can I ensure successful PCB panelization?
To ensure successful PCB panelization, consider panelization requirements early in the design process, use standard panel sizes, provide adequate spacing between PCBs, use appropriate panelization techniques, include tooling holes and fiducial marks, consider depaneling methods, and verify your design with your PCB manufacturer.
Conclusion
PCB panelization is a critical aspect of PCB manufacturing that enables the efficient and cost-effective production of multiple PCBs simultaneously. By understanding the various panelization techniques, design considerations, and best practices, designers and manufacturers can optimize their panelization processes to achieve the best possible results.
As the electronics industry continues to evolve, PCB panelization will remain an essential tool for meeting the ever-changing demands of pcb fabrication and assembly. By staying informed about the latest trends and technologies in panelization, designers and manufacturers can ensure that they are well-positioned to address the challenges and opportunities of the future.