PCB Routing Basics
At its core, PCB routing involves creating copper traces on the board layers to link component pins according to the schematic design. The router must navigate the limited space available while adhering to design rules that govern factors like trace width, spacing, via sizing, and more.
Types of PCB Routing
There are two main types of PCB routing:
Routing Type | Description |
---|---|
Manual Routing | The PCB designer manually draws each trace between pads and through vias. Allows fine control but is time-consuming, especially for complex boards. |
Autorouting | PCB design software automatically routes traces based on preset design rules and algorithms. Much faster but may not be as neat or optimized as manual routing. |
Most PCB designs use a combination of manual and automated routing. Critical or tricky routes are done by hand while simpler connections are autorouted.
pcb layer Stack-up
Modern PCBs often have multiple copper layers to accommodate more complex circuits in a smaller space. The number of layers depends on the design requirements. Here are some common layer configurations:
Layer Count | Typical Uses |
---|---|
1 | Very simple circuits |
2 | Double-sided boards, lower cost |
4 | Good for most designs, allows dedicated power/ground planes |
6-8 | High-density boards, fast signal speeds |
10+ | Very complex boards like motherboards, FPGAs, etc. |
The outer layers are typically used for component placement and routing. The inner layers are used for power planes, ground planes, and additional signal routing.
PCB Routing Rules and Guidelines
To ensure a successful PCB design, there are many routing rules and best practices to follow. These help optimize the electrical characteristics, manufacturability, and reliability of the board.
Trace Width and Spacing
One of the most important routing rules governs the minimum width of traces and the spacing between them. These are determined by the electrical requirements (current carrying capacity) and manufacturing capabilities.
Typical minimum trace widths are:
Copper Weight (oz) | Minimum Trace Width (mils) |
---|---|
0.5 | 4 |
1 | 5 |
2 | 6 |
The spacing between traces is also important to prevent short circuits and crosstalk. A common rule is to maintain a spacing at least equal to the trace width.
Via Sizing and Drill Holes
Vias are used to route traces between different layers of the board. The via size and drill hole diameter are important design considerations.
Standard via sizes are:
Via Type | Drill Diameter (mils) | Finished Hole Size (mils) |
---|---|---|
Through hole | 20-35 | 40-60 |
Blind/buried | 6-10 | 10-20 |
Microvias | 4-6 | 8-10 |
The pad diameter should be at least 20 mils larger than the drill size. Vias should be placed at least 25 mils away from the edge of the board and other holes.
Routing Angles
While 90-degree trace corners are allowed, it’s generally better to use 45-degree angles or arcs for cleaner routing. 90-degree turns can cause acid traps during manufacturing.
Signal Integrity
For high-speed designs, maintaining signal integrity is crucial. This involves impedance control, length matching, and reducing crosstalk.
Some signal integrity guidelines include:
- Route critical traces first
- Keep high-speed traces as short and straight as possible
- Avoid routing high-speed traces near board edges
- Maintain consistent trace widths and spacing
- Use ground planes and good grounding practices
Power Routing
Proper power routing is important for minimizing noise and ensuring adequate current flow. Some rules of thumb:
- Use thick traces or copper pours for power nets
- Use dedicated power and ground planes when possible
- Keep power traces short and use multiple vias for high current paths
- Add decoupling capacitors close to ICs
- Avoid daisy-chaining power between components
Electromagnetic Compatibility (EMC)
PCBs can both emit and be susceptible to electromagnetic interference (EMI). Good routing practices help mitigate EMI issues:
- Separate high-speed digital and sensitive analog sections
- Avoid routing traces under crystals or clock generators
- Keep high-frequency traces away from board edges
- Use guard rings or shielding for sensitive components
- Filter inputs and outputs as needed
Manufacturing Considerations
To ensure the PCB can be reliably and cost-effectively manufactured, these guidelines help:
- Adhere to the fabrication house’s design rules and tolerances
- Provide proper trace width, spacing, and hole size
- Avoid acid traps and extreme trace angles
- Allow adequate space for solder mask between pads
- Define the board outline and add tooling holes
- Generate proper Gerber and drill files
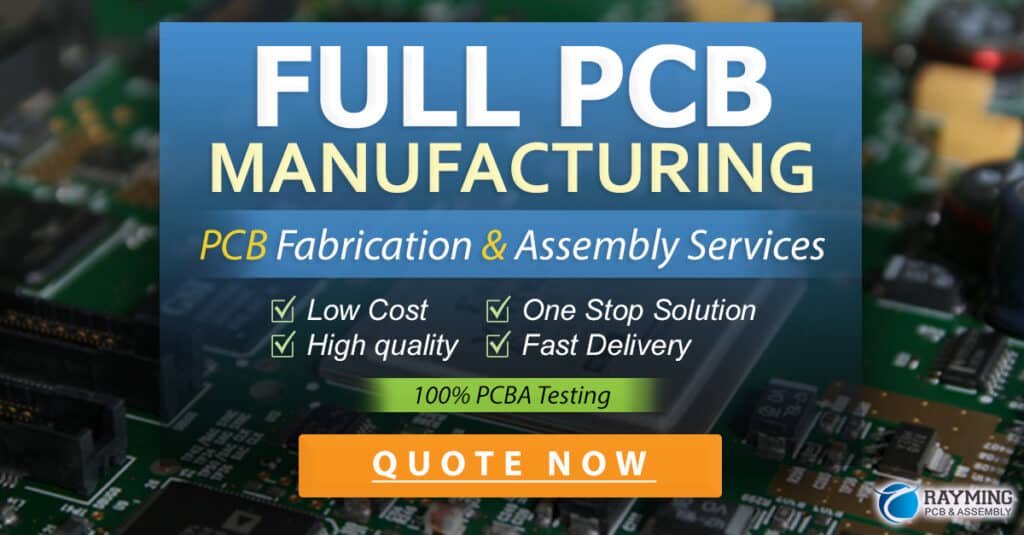
PCB Routing Workflow
With the above rules in mind, a typical PCB routing workflow involves:
- Define the schematic and component placement
- Configure design rules and constraints in the PCB layout software
- Route critical signals like clocks and high-speed paths first
- Use autorouting to connect less critical nets
- Manually route remaining traces and clean up the routing
- Perform design rule checks (DRC) to verify all rules are met
- Generate manufacturing files like Gerbers and drill drawings
Frequently Asked Questions
What is the difference between a trace and a via?
A trace is a flat conductive path on a single layer of the PCB that routes signals between components. A via is a hole that is drilled and plated with copper to connect traces on different layers of the board.
How do I determine the right trace width for my design?
The minimum trace width is determined by the current it needs to carry and the manufacturing capabilities. Online trace width calculators are available, and your PCB fabrication house can provide guidance on their minimum tolerances.
What is the advantage of using multiple copper layers?
Using multiple copper layers allows for more complex routing in a smaller space. It also enables the use of dedicated power and ground planes for better power distribution and signal integrity.
What is the difference between blind, buried, and through vias?
Through vias go through all layers of the PCB and are exposed on both outer layers. Blind vias start on an outer layer and stop at an inner layer. Buried vias connect two or more inner layers without being exposed on the outer layers. Blind and buried vias allow for higher wiring density but are more expensive to manufacture.
How can I reduce electromagnetic interference in my PCB?
Some ways to reduce EMI include separating digital and analog sections, keeping high-frequency traces away from edges, using ground planes and guards, filtering I/Os, and adhering to good routing and grounding practices. Pre-compliance EMI testing can also identify potential issues to address.
In conclusion, proper PCB routing is a complex task that requires balancing many design rules and tradeoffs. By understanding the fundamental guidelines for trace widths, via sizing, signal integrity, power delivery, EMC, and manufacturability, PCB designers can create reliable and high-performing boards. While PCB design software provides autorouting and rule checking features, having a solid grasp of routing best practices is invaluable for optimizing designs.