Advantages of Aluminum PCBs
Before delving into the specific applications of aluminum PCBs, it is essential to understand the key advantages they offer:
- Enhanced thermal management
- Improved mechanical stability
- Reduced weight
- Cost-effectiveness
- Increased durability
Enhanced thermal management
One of the primary advantages of aluminum PCBs is their excellent thermal management capabilities. The aluminum substrate acts as a heat sink, efficiently dissipating heat away from the electronic components. This is particularly important in high-power applications where heat generation can be significant. By effectively managing the heat, aluminum PCBs can prevent component failure and extend the lifespan of the device.
Improved mechanical stability
Aluminum PCBs offer superior mechanical stability compared to traditional FR-4 PCBs. The aluminum substrate provides a rigid and sturdy base for the components, reducing the risk of physical damage due to vibrations or mechanical stress. This makes aluminum PCBs suitable for applications that are subject to harsh environments or require reliable performance under challenging conditions.
Reduced weight
Compared to other metal core PCBs, such as those made with copper, aluminum PCBs are significantly lighter in weight. This is because aluminum has a lower density than copper. The reduced weight is particularly advantageous in applications where weight is a critical factor, such as in aerospace and automotive industries.
Cost-effectiveness
While aluminum PCBs may have a higher initial cost compared to FR-4 PCBs, they can be more cost-effective in the long run. The enhanced thermal management and improved durability of aluminum PCBs can lead to reduced maintenance and replacement costs. Additionally, the efficient heat dissipation can allow for the use of lower-cost components, as they are less likely to suffer from heat-related failures.
Increased durability
Aluminum PCBs are known for their increased durability and resistance to environmental factors. The aluminum substrate is less prone to moisture absorption compared to FR-4 materials, making them suitable for use in humid or damp environments. Furthermore, aluminum PCBs can withstand higher temperatures and are less likely to suffer from thermal expansion issues, which can cause component failure in traditional PCBs.
Applications of Aluminum PCBs
Now that we have explored the advantages of aluminum PCBs, let’s take a look at some of the key applications where they are commonly used:
- LED lighting
- Power electronics
- Automotive industry
- Aerospace and defense
- High-performance computing
- Industrial automation and control systems
- Medical devices
- Telecommunications
LED lighting
Aluminum PCBs are widely used in LED lighting applications due to their excellent thermal management properties. LEDs generate a significant amount of heat, and if not properly dissipated, this heat can lead to reduced light output, color shifting, and premature failure. By using aluminum PCBs, the heat generated by the LEDs can be efficiently conducted away from the components and dissipated into the surrounding environment. This ensures stable performance, consistent color rendering, and extended lifespan of the LED lighting system.
Application | Benefits of Aluminum PCBs |
---|---|
Indoor lighting | Compact design, improved heat dissipation |
Outdoor lighting | Resistance to moisture and temperature fluctuations |
Automotive lighting | Vibration resistance, extended lifespan |
Industrial lighting | Durability in harsh environments |
Power electronics
Power electronics involve the control and conversion of electrical power using semiconductor devices. These devices, such as MOSFETs, IGBTs, and diodes, generate significant amounts of heat during operation. Aluminum PCBs are commonly used in power electronics to ensure efficient heat dissipation and prevent component failure.
Examples of power electronic applications that benefit from aluminum PCBs include:
– Switch-mode power supplies (SMPS)
– Motor drives
– Inverters
– Rectifiers
– Battery management systems
The use of aluminum PCBs in power electronics allows for higher power densities, improved reliability, and compact designs.
Automotive industry
The automotive industry is another sector where aluminum PCBs find extensive use. Modern vehicles are equipped with a wide range of electronic systems, including engine control units (ECUs), infotainment systems, advanced driver assistance systems (ADAS), and lighting controls. Aluminum PCBs are used in these applications due to their ability to withstand harsh environmental conditions, such as high temperatures, vibrations, and moisture.
Some specific automotive applications where aluminum PCBs are used include:
– Engine control modules
– Power steering control units
– LED headlights and taillights
– Electric vehicle battery management systems
– Automotive infotainment systems
The use of aluminum PCBs in the automotive industry ensures reliable performance, extended product lifespan, and compliance with stringent automotive standards.
Aerospace and defense
Aluminum PCBs are also used in the aerospace and defense industries, where reliability and performance under extreme conditions are paramount. These industries require electronic systems that can withstand high altitudes, extreme temperatures, vibrations, and shock.
Examples of aerospace and defense applications that utilize aluminum PCBs include:
– Avionics systems
– Radar and surveillance equipment
– Satellite communication systems
– Military-grade power supplies
– Missile guidance systems
The lightweight nature of aluminum PCBs is particularly advantageous in aerospace applications, where weight reduction is crucial for fuel efficiency and payload capacity.
High-performance computing
High-performance computing (HPC) systems, such as servers, workstations, and data centers, generate significant amounts of heat due to the high processing power and density of components. Aluminum PCBs are used in HPC applications to ensure efficient heat dissipation and maintain optimal performance.
Examples of HPC applications that benefit from aluminum PCBs include:
– Server motherboards
– Graphics processing units (GPUs)
– High-speed network switches
– Solid-state drives (SSDs)
– Blade servers
The use of aluminum PCBs in HPC systems prevents thermal throttling, ensures stable performance, and extends the lifespan of the components.
Industrial automation and control systems
Industrial automation and control systems often operate in harsh environments, where they are exposed to high temperatures, dust, vibrations, and electromagnetic interference (EMI). Aluminum PCBs are used in these systems to provide reliable performance and protection against environmental factors.
Examples of industrial automation and control applications that utilize aluminum PCBs include:
– Programmable logic controllers (PLCs)
– Motor drives and servo controllers
– Industrial sensors and transducers
– Power supplies for industrial equipment
– Human-machine interfaces (HMIs)
The ruggedness and thermal management capabilities of aluminum PCBs make them suitable for use in industrial settings, ensuring long-term reliability and minimizing downtime.
Medical devices
Medical devices require high reliability, precision, and safety. Aluminum PCBs are used in various medical applications due to their ability to provide stable performance and resist environmental factors such as moisture and chemicals.
Examples of medical devices that utilize aluminum PCBs include:
– Imaging equipment (e.g., MRI, CT scanners)
– Patient monitoring systems
– Surgical instruments
– Diagnostic devices
– Medical power supplies
The use of aluminum PCBs in medical devices ensures accurate measurements, reliable operation, and compliance with strict medical standards and regulations.
Telecommunications
Telecommunications equipment, such as base stations, routers, and switches, require efficient heat dissipation to maintain optimal performance and prevent component failure. Aluminum PCBs are used in telecommunications applications to manage the heat generated by high-speed processing and data transmission.
Examples of telecommunications applications that benefit from aluminum PCBs include:
– 5G base stations
– Fiber-optic communication systems
– Wireless routers and access points
– Network switches and gateways
– Satellite communication equipment
The use of aluminum PCBs in telecommunications ensures reliable data transmission, high bandwidth, and extended equipment lifespan.
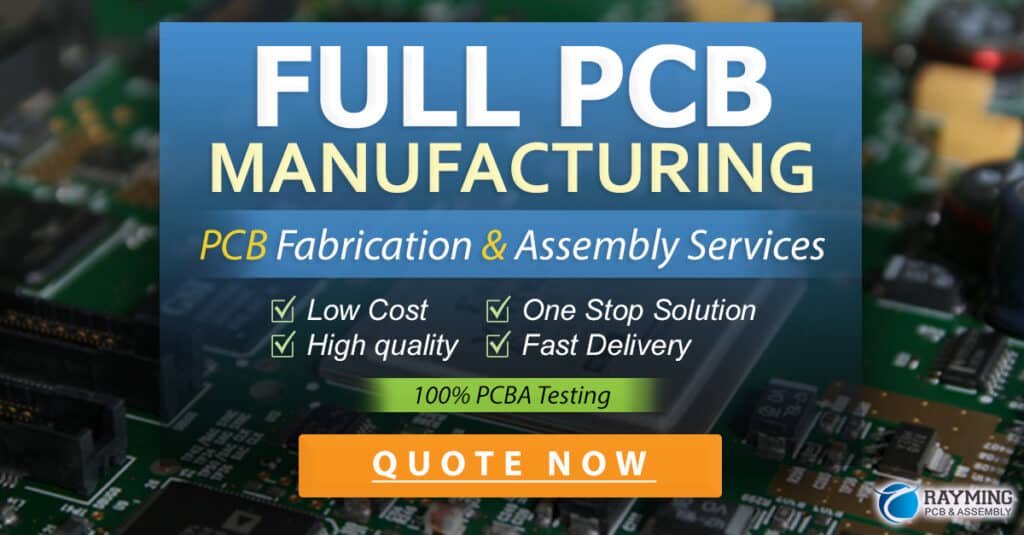
FAQ
-
Q: What is the difference between aluminum PCBs and traditional FR-4 PCBs?
A: Aluminum PCBs use an aluminum substrate instead of the FR-4 material used in traditional PCBs. This provides better thermal management, improved mechanical stability, and increased durability. -
Q: Can aluminum PCBs be used in high-frequency applications?
A: Yes, aluminum PCBs can be used in high-frequency applications. However, the design considerations may differ compared to FR-4 PCBs, and proper impedance matching and signal integrity measures should be implemented. -
Q: Are aluminum PCBs more expensive than traditional PCBs?
A: The initial cost of aluminum PCBs may be higher than traditional FR-4 PCBs. However, they can be more cost-effective in the long run due to their enhanced thermal management, improved durability, and reduced maintenance and replacement costs. -
Q: Can aluminum PCBs be used in flexible applications?
A: No, aluminum PCBs are not suitable for flexible applications due to the rigid nature of the aluminum substrate. For flexible applications, other types of PCBs, such as polyimide or polyester-based flexible PCBs, should be used. -
Q: How are components mounted on aluminum PCBs?
A: Components can be mounted on aluminum PCBs using various methods, including surface mount technology (SMT), through-hole mounting, or a combination of both. The choice of mounting method depends on the specific requirements of the application and the types of components used.
Conclusion
Aluminum PCBs offer several advantages over traditional FR-4 PCBs, including enhanced thermal management, improved mechanical stability, reduced weight, cost-effectiveness, and increased durability. These advantages make them suitable for a wide range of applications across various industries, such as LED lighting, power electronics, automotive, aerospace and defense, high-performance computing, industrial automation, medical devices, and telecommunications.
When considering the use of aluminum PCBs, it is essential to evaluate the specific requirements of the application, such as thermal management needs, environmental conditions, and mechanical constraints. Proper design considerations, including thermal interface materials, dielectric layers, and layout optimization, should be implemented to ensure optimal performance and reliability.
As technology continues to advance and the demand for high-performance, reliable electronic systems grows, the use of aluminum PCBs is expected to increase. Their unique properties and advantages make them a valuable solution for applications that require efficient heat dissipation, robustness, and long-term reliability.
In conclusion, aluminum PCBs are a versatile and effective choice for a wide range of industries and applications. By understanding their advantages and proper implementation, designers and engineers can leverage the benefits of aluminum PCBs to create high-performance, reliable, and cost-effective electronic systems.