The Role of PCB Stencils in SMT Assembly
In SMT assembly, the PCB stencil plays a crucial role in the solder paste application process. The stencil is placed on top of the PCB, aligning the openings with the corresponding pads. Solder paste is then applied onto the stencil using a squeegee or automated paste dispensing machine. As the squeegee moves across the stencil, it forces the solder paste through the openings and onto the PCB pads.
The PCB stencil ensures that the correct amount of solder paste is deposited on each pad, which is essential for forming reliable solder joints during the reflow soldering process. Too much or too little solder paste can lead to defects such as bridging, tombstoning, or insufficient solder joints.
Types of PCB Stencils
There are several types of PCB stencils available, each with its own advantages and suitable applications. The most common types include:
-
Laser-cut stencils: These stencils are made by cutting the openings using a high-precision laser. They offer excellent accuracy and are suitable for fine-pitch components and high-density PCB designs.
-
Electroformed stencils: Electroformed stencils are created by electroplating nickel onto a photoresist-coated master. They provide smooth aperture walls and are ideal for applications requiring high repeatability and fine feature resolution.
-
Chemically-etched stencils: These stencils are made by chemically etching the openings into a thin sheet of stainless steel. They are cost-effective and suitable for less demanding applications or prototyping.
Stencil Thickness and Aperture Design
The thickness of the PCB stencil and the design of the apertures (openings) are critical factors in achieving optimal solder paste deposition. The stencil thickness is typically chosen based on the size and pitch of the components being assembled. Common stencil thicknesses range from 0.100mm to 0.150mm (4 to 6 mils) for standard SMT assembly, while finer-pitch components may require thinner stencils.
The aperture design of the PCB stencil involves determining the size, shape, and orientation of the openings. The aperture size is usually slightly larger than the corresponding PCB pad to allow for proper solder paste release. The shape of the aperture can be rectangular, circular, or custom-designed to accommodate specific component requirements. The orientation of the apertures is also important, especially for components with fine-pitch leads, to ensure proper alignment and prevent solder bridging.
Stencil Material and Durability
PCB stencils are typically made from stainless steel due to its durability, stability, and resistance to wear and tear. Stainless steel stencils can withstand multiple print cycles and are easy to clean and maintain. Other materials, such as nickel-plated stencils or polyimide film stencils, may be used in specific applications or for prototype runs.
The durability of the PCB stencil is essential for maintaining consistent solder paste deposition over multiple print cycles. Proper handling, storage, and cleaning of the stencil can extend its lifespan and ensure optimal performance.
Stencil Cleaning and Maintenance
Regular cleaning and maintenance of the PCB stencil are crucial for ensuring consistent solder paste deposition and preventing defects. Solder paste residue can accumulate on the stencil over time, clogging the apertures and affecting the print quality. Therefore, it is important to clean the stencil after each use or at regular intervals, depending on the production volume.
Stencil cleaning can be performed using various methods, such as:
-
Manual cleaning: This involves using a lint-free cloth or wipe and a suitable cleaning solution to remove solder paste residue from the stencil surface and apertures.
-
Ultrasonic cleaning: Ultrasonic cleaners use high-frequency sound waves to agitate a cleaning solution, effectively removing solder paste residue from the stencil.
-
Automated stencil cleaning: Automated stencil cleaning systems are designed to clean the stencil efficiently and consistently, minimizing manual intervention and ensuring thorough cleaning of the apertures.
In addition to cleaning, regular inspection of the PCB stencil is necessary to identify any damage, wear, or clogging of the apertures. Damaged or worn stencils should be repaired or replaced to maintain optimal print quality.
Advantages of Using PCB Stencils
Using PCB stencils in SMT assembly offers several advantages, including:
-
Consistency: PCB stencils ensure consistent solder paste deposition across multiple PCBs, reducing the risk of defects and improving overall assembly quality.
-
Efficiency: Stencil printing is a fast and efficient method of applying solder paste, enabling high-volume production and reducing assembly time.
-
Accuracy: PCB stencils provide accurate solder paste deposition, even for fine-pitch components and high-density PCB designs.
-
Cost-effectiveness: Using PCB stencils is a cost-effective solution for applying solder paste, especially in high-volume production, as it minimizes solder paste waste and reduces the need for manual rework.
Challenges and Considerations
While PCB stencils offer numerous benefits, there are also some challenges and considerations to keep in mind:
-
Stencil design: Designing the stencil apertures correctly is crucial for achieving optimal solder paste deposition. Factors such as aperture size, shape, and orientation must be carefully considered to ensure proper solder paste release and prevent defects.
-
Stencil alignment: Accurate alignment of the stencil to the PCB is essential for ensuring proper solder paste deposition on the pads. Misalignment can lead to solder paste offsets, bridging, or insufficient solder joints.
-
Stencil maintenance: Regular cleaning and maintenance of the PCB stencil are necessary to ensure consistent performance and prevent defects. Neglecting stencil maintenance can result in clogged apertures, uneven solder paste deposition, and reduced print quality.
-
Solder paste selection: Choosing the appropriate solder paste for the specific application and components is important. The solder paste’s rheological properties, such as viscosity and tackiness, must be compatible with the stencil aperture design and the PCB’s surface finish.
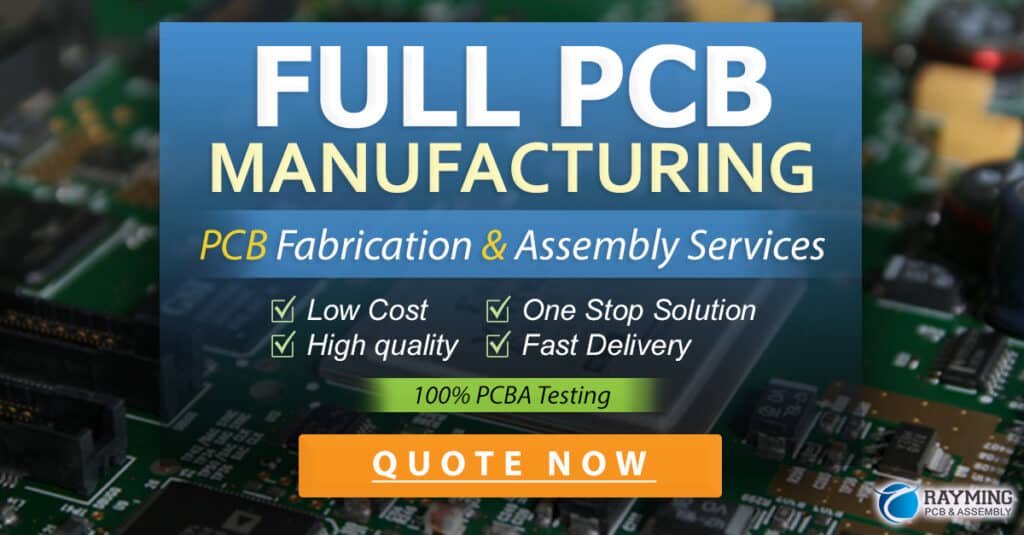
Conclusion
PCB stencils are an essential tool in SMT assembly, enabling accurate and consistent solder paste deposition on PCB pads. They play a critical role in ensuring reliable solder joint formation and overall assembly quality. By understanding the types of PCB stencils, their design considerations, and maintenance requirements, manufacturers can optimize their SMT assembly processes and achieve high-quality results.
As PCB designs continue to evolve with smaller component sizes and higher densities, the importance of PCB stencils will only increase. Investing in high-quality stencils, proper stencil design, and regular maintenance will help manufacturers stay competitive and meet the demands of the ever-advancing electronics industry.
Frequently Asked Questions (FAQ)
-
What is the difference between a PCB stencil and a solder paste screen?
A PCB stencil and a solder paste screen are essentially the same things. Both terms refer to a thin, flat sheet with openings used to apply solder paste onto PCB pads. The term “stencil” is more commonly used in the industry. -
How often should I clean my PCB stencil?
The frequency of cleaning your PCB stencil depends on factors such as the type of solder paste used, the production volume, and the environmental conditions. As a general rule, it is recommended to clean the stencil after every use or at regular intervals (e.g., every 4-8 hours of continuous use) to prevent solder paste buildup and ensure consistent print quality. -
Can I reuse a damaged or worn PCB stencil?
It is not recommended to reuse a damaged or worn PCB stencil as it can lead to poor solder paste deposition, inconsistent print quality, and defects in the assembled PCBs. If a stencil is damaged or worn, it should be repaired or replaced to maintain optimal performance. -
How do I choose the right solder paste for my PCB stencil?
When selecting solder paste for your PCB stencil, consider factors such as the paste’s particle size, viscosity, and flux activity. The paste should be compatible with the stencil aperture design, the PCB’s surface finish, and the reflow profile. Consult with your solder paste supplier or stencil manufacturer for recommendations based on your specific application. -
What factors influence the choice of stencil thickness?
The choice of stencil thickness depends on several factors, including the size and pitch of the components being assembled, the solder paste’s viscosity, and the PCB’s surface finish. As a general guideline, thicker stencils (e.g., 0.15mm or 6 mils) are used for larger components and higher-viscosity solder pastes, while thinner stencils (e.g., 0.10mm or 4 mils) are used for smaller components and lower-viscosity pastes. It is important to select the appropriate stencil thickness to ensure optimal solder paste deposition and prevent defects such as insufficient solder joints or bridging.
Stencil Thickness | Typical Application |
---|---|
0.100mm (4 mils) | Fine-pitch components, low-viscosity solder paste |
0.125mm (5 mils) | Standard SMT components, medium-viscosity solder paste |
0.150mm (6 mils) | Larger SMT components, high-viscosity solder paste |
0.175mm (7 mils) | Extra-large components, very high-viscosity solder paste |
0.200mm (8 mils) | Specialized applications, extremely high-viscosity solder paste |